Sizers
McLanahan Sizers provide primary, secondary and tertiary reduction of friable, low silica materials such as coal, salt, gypsum, phosphate, limestone, bauxite, petroleum coke, lignite, trona, carbon anodes, oil sands, clay, shale and more.
Applications
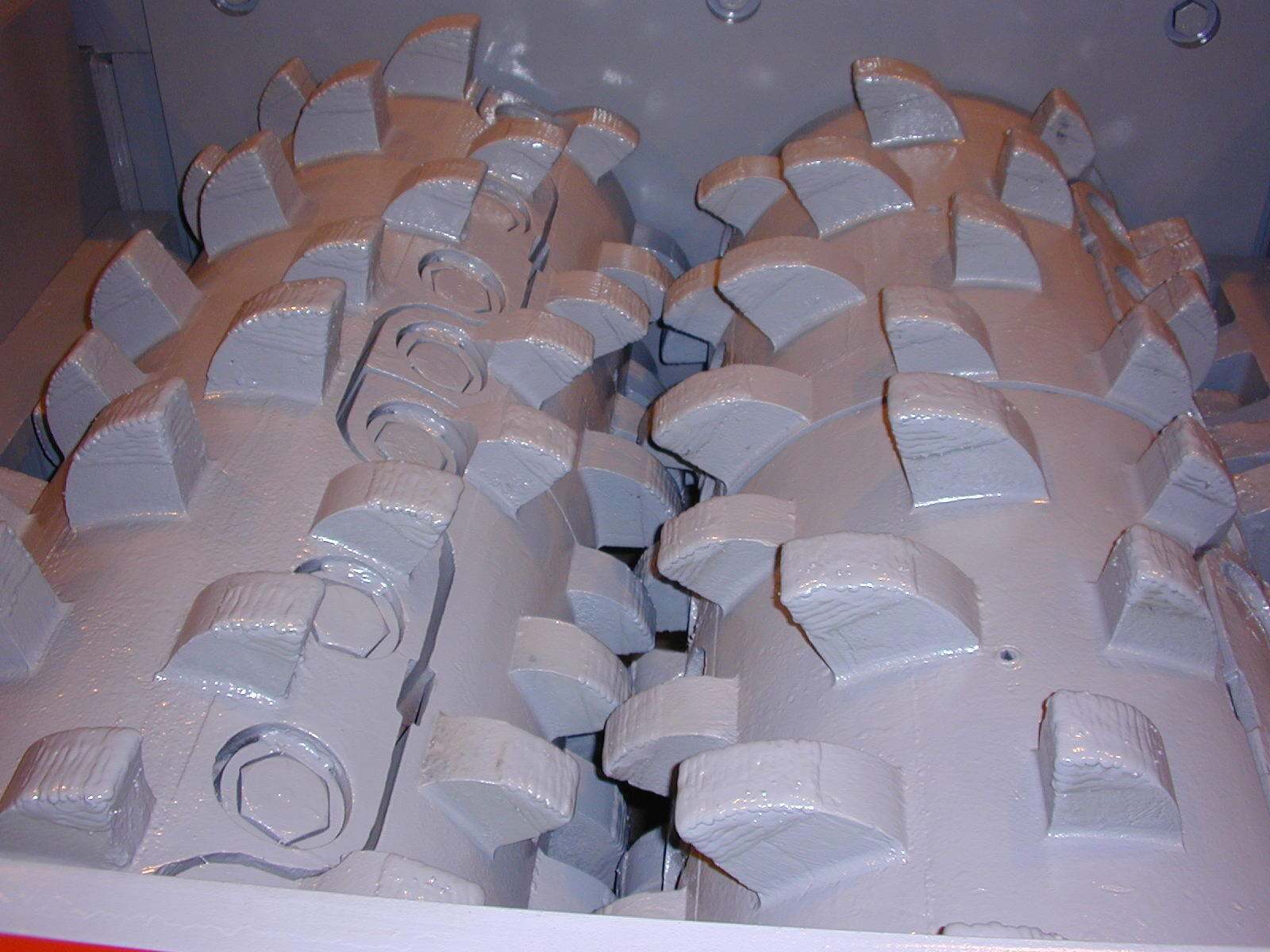
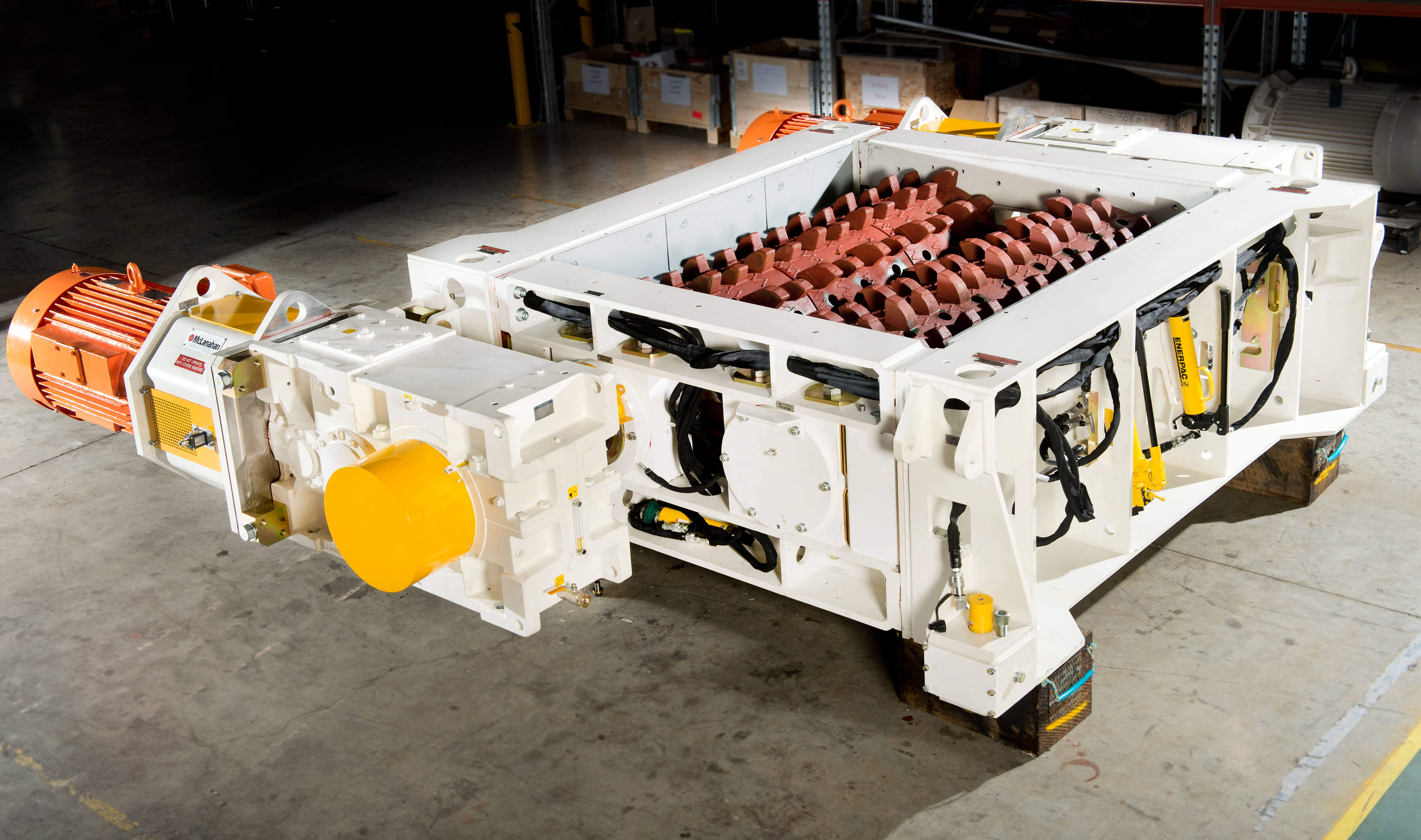
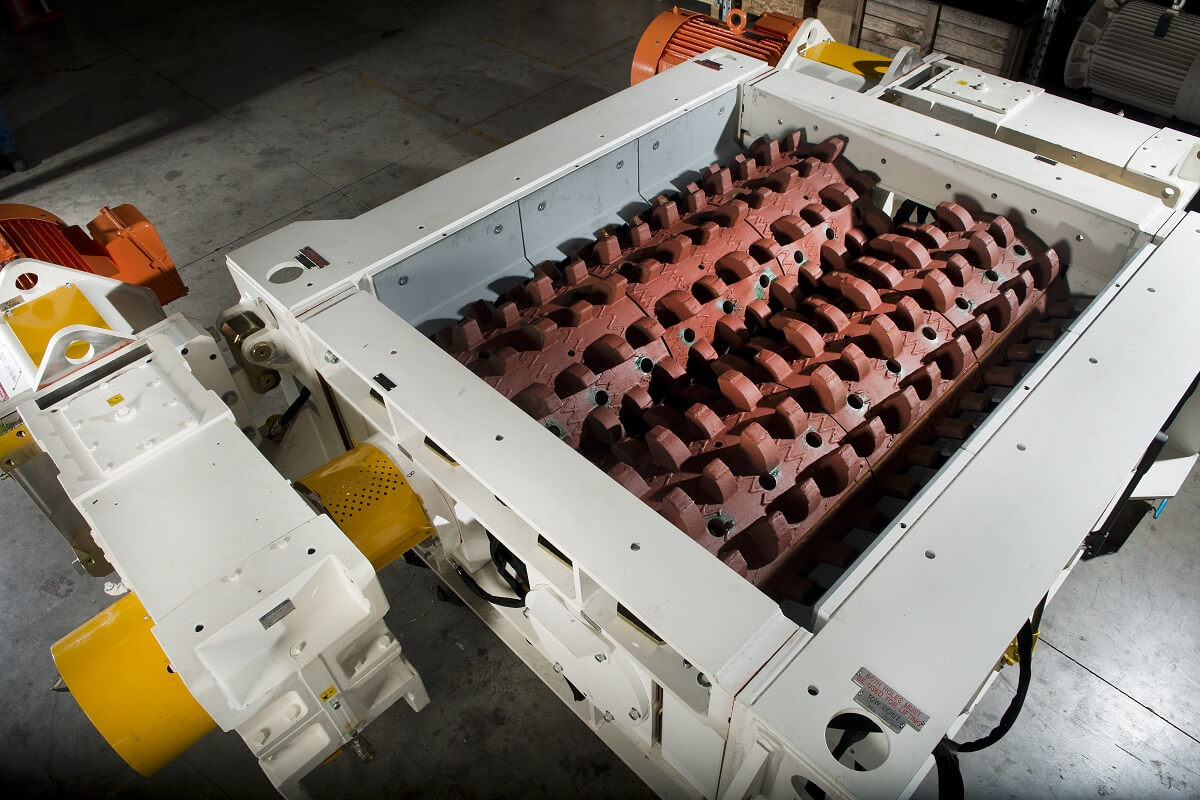
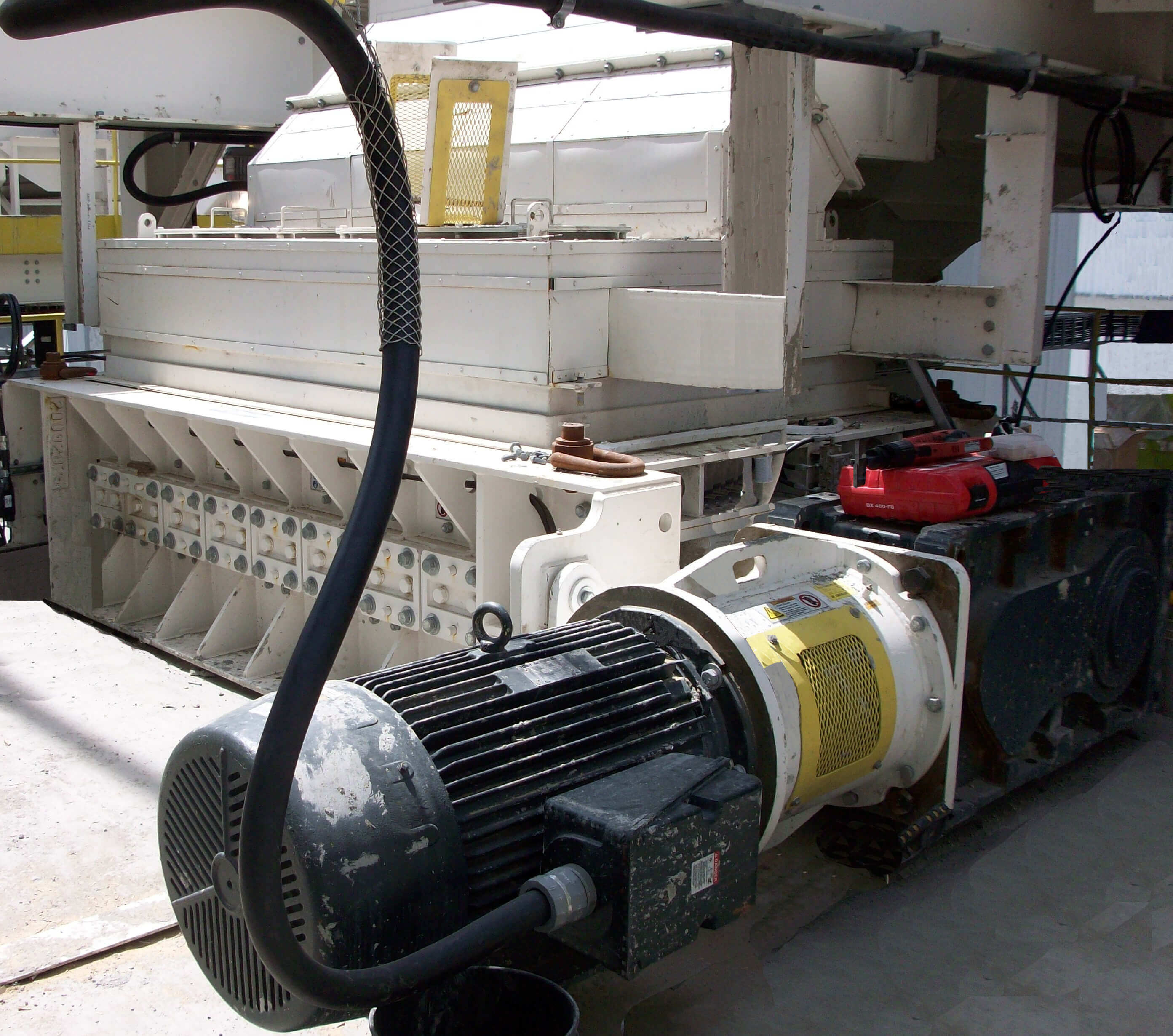
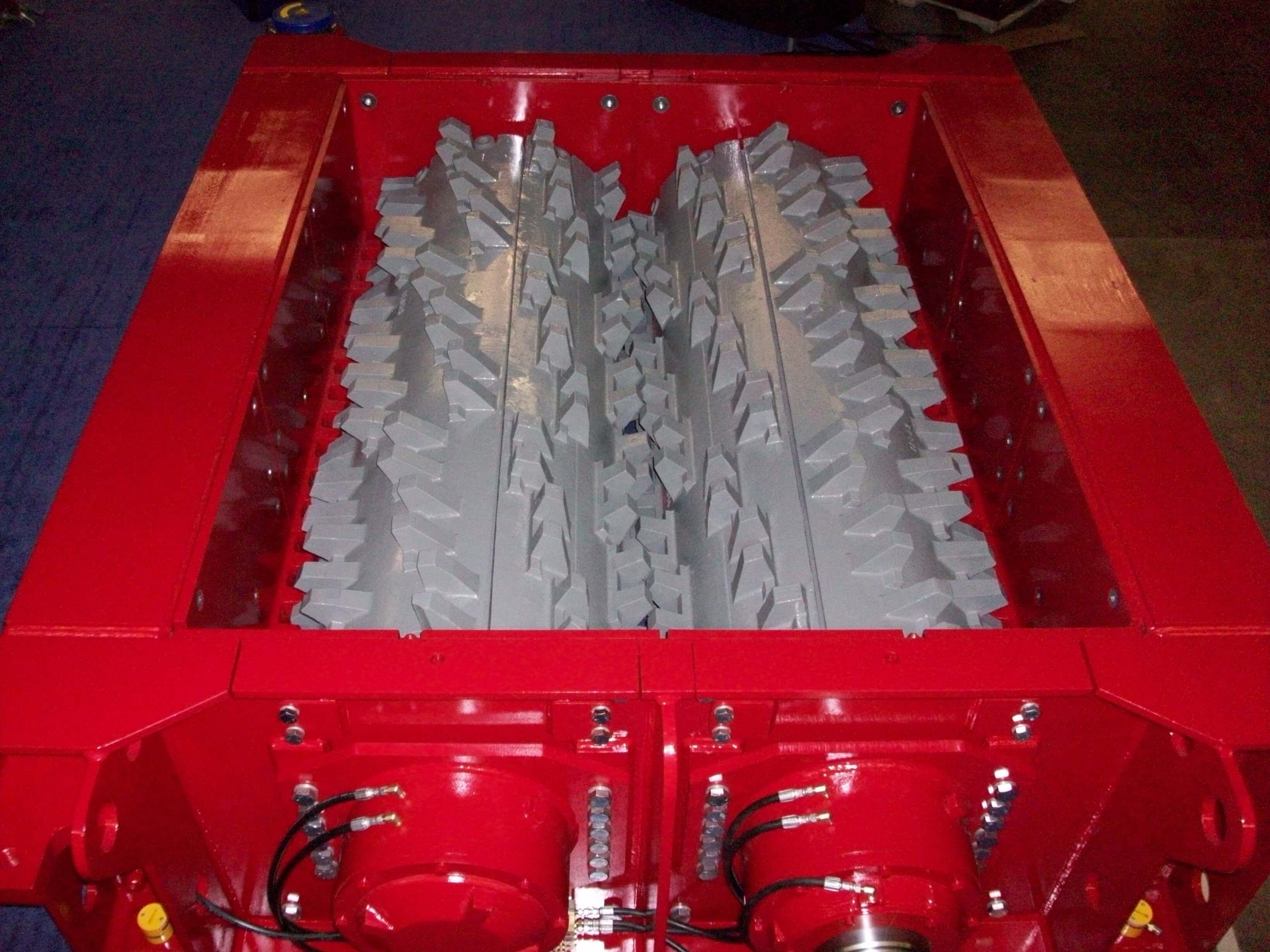
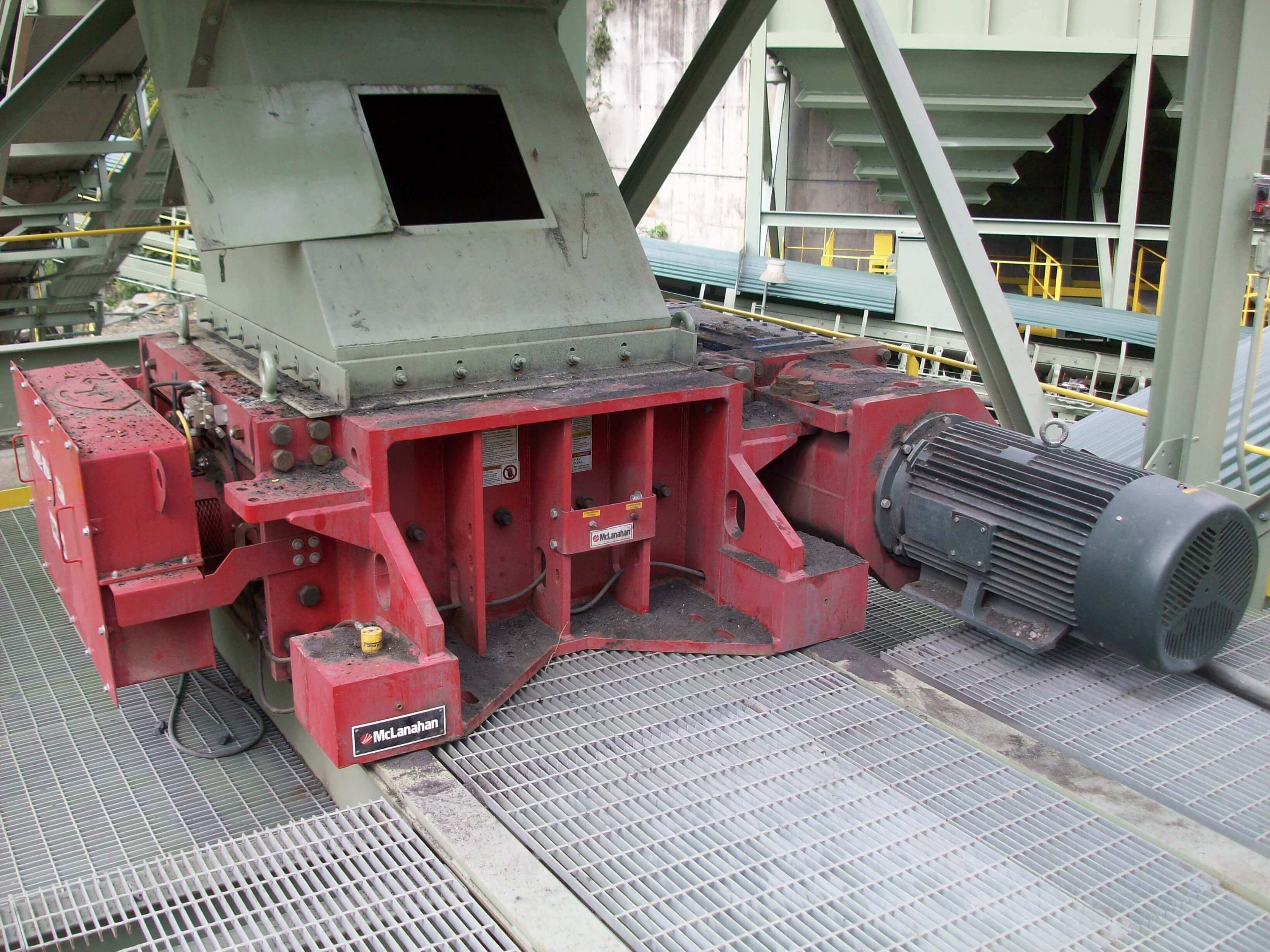