Single Roll Crushers
The Single Roll Crusher, with its 6:1 ratio of reduction, is ideal for reducing large feed lumps to a medium product size while producing a considerably lower percentage of fines.
Applications
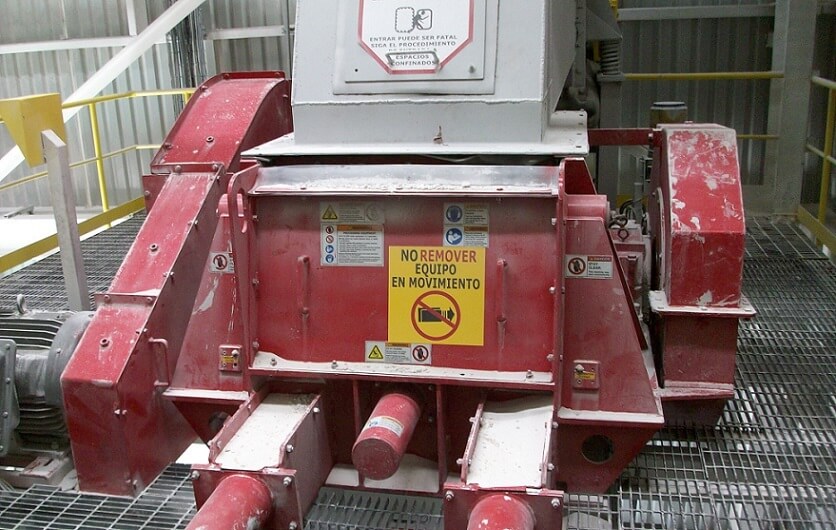
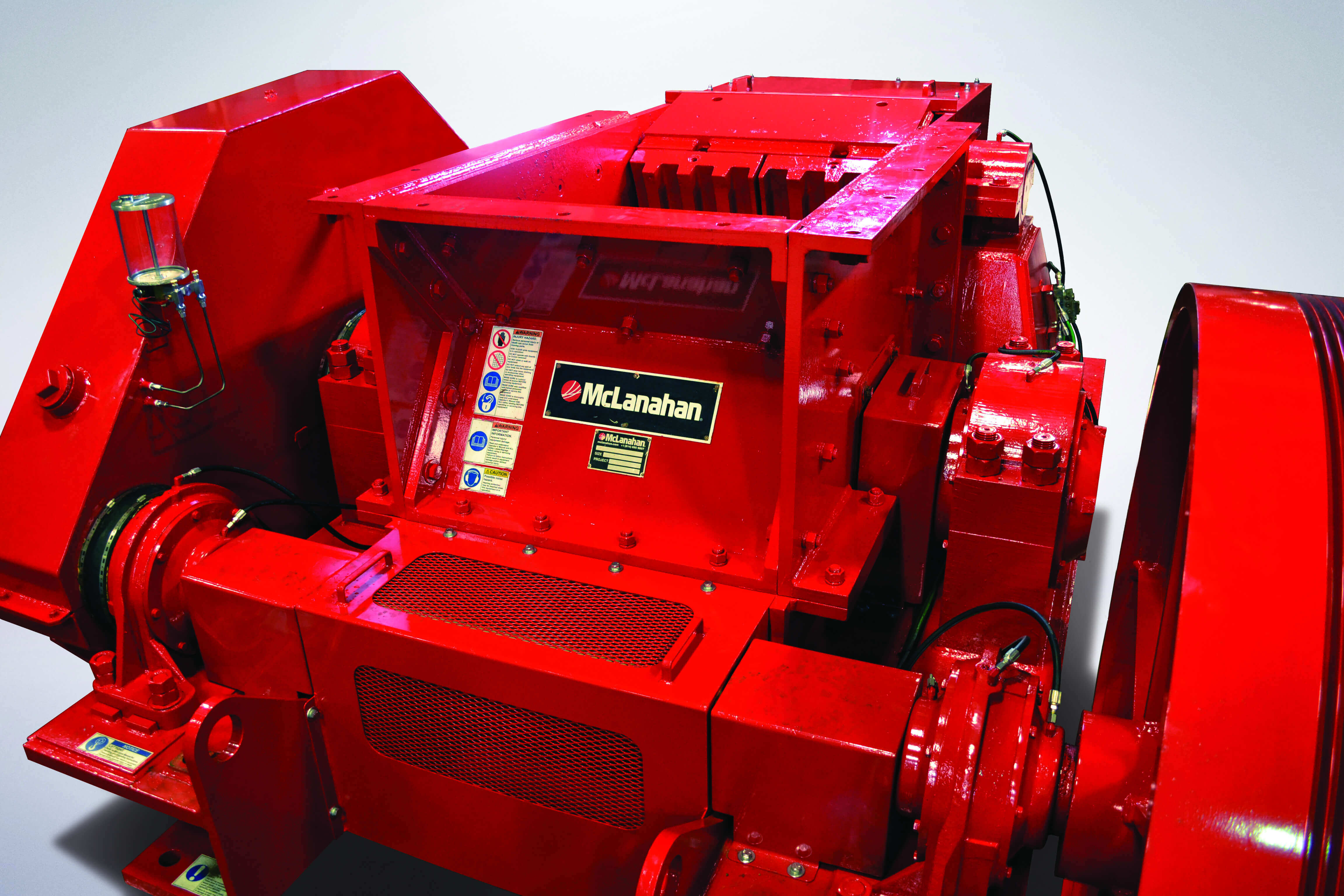
Jump To:
The minimum product sizing of a Single Roll Crusher is generally limited to 2-3”. The crushing is carried out between the full width of the extra-long curved crushing plate and the low-speed crushing roll. The curvature of the crushing plate provides an ample throat opening to capture large irregular feed lumps. The replaceable crushing plate tips or liners are slotted to intermesh with the roll teeth to produce a cubical product and effectively reduce slabbing.
Single Roll Crushers are V-belt driven and employ a large diameter flywheel with a gear and pinion set to reduce roll speed. With the assistance of the inertia generated by the flywheel, this crusher is operated with relatively low horsepower and requires lower headroom in comparison to other crushers used for primary reduction. The roll diameter and width of the crusher will ultimately be dictated by the feed size, product size and capacity.
Single Roll Crushers employ a tramp relief mechanism to allow momentary movement of the crushing plate so the uncrushable object can pass. The mechanism then allows the crusher to return to its original setting and remain in operation.
Single Roll Crushers have long been used in a variety of applications, including ROM feeds, clay, glass and other friable minerals.
A Single Roll Crusher is made up of a toothed roll assembly, which crushes the incoming feed material against a crushing plate. The Single Roll Crusher is designed to reduce larger feed sizes to the desired product size at a 6:1 ratio of reduction while producing a considerably lower percentage of fines. When properly fed in the direction of the roll rotation, the crushing action is carried out along the full width of the curved crushing plate, which ensures maximum throughput capacity. A properly sized roll diameter and tooth configuration grabs the incoming feed and pulls it into the crushing zone without hesitation. The crushing plate has reversible and easily replaceable crushing plate tips, which are designed to produce a cubical product while providing the producer with twice the wear life and simplified maintenance. Single Roll Crushers often require less horsepower and lower headroom in comparison to other crushers used in primary and secondary applications.
These units are designed to make crushing simpler and more effective. McLanahan Single Roll Crushers also feature hydraulic product size adjustment to perform relatively simple changes to the crusher setting if required.
The Single Roll Crusher, which was originally patented by Samuel Calvin McLanahan in 1894, has evolved over the years to include design features to ensure many years of rugged operation. Complete with all safety guards, the Single Roll Crusher features an automatic tramp relief mechanism that allows the crushing plate to hinge open, pass non-crushable tramp material and return to the previous setting for continued operation.
Based on the application data and extensive field experience, McLanahan selects the proper duty class of Single Roll Crusher for each project. A fully-equipped application research laboratory allows for crushing tests to make sure McLanahan can provide the best possible solution.
When an uncrushable object, such as metal, roof bolts/timbers, etc., enters the crusher and the force necessary to crush this material is greater than the crushing forces of the crusher, the crusher allows the crushing plate to open and pass the tramp material. The crusher then returns to its previous setting and remains in operation.
The ratio of reduction is the ratio of the feed size to the desired product size. For example, if the feed size is 12” and the desired product size is 2”, then the ratio of reduction is 6:1.
Depending on the customer’s feed size and product size requirements, consideration can be given to Mineral Sizers or Double Roll Crushers.
Cobra Single Roll Crushers are the lightest duty in the McLanahan line of Single Roll Crushers. They are ideal for wet, sticky feeds and for processing materials such as clean coal, petroleum coke, sulfur, rosin, foundry cores, frozen agglomerates and other friable materials.
Black Diamond Single Roll Crushers are designed to handle medium-hard materials, such as ROM coal with shale and slate, salt, and phosphate rock.
Super Black Diamond Single Roll Crushers are designed to handle hard to medium-hard materials, such as shale, gypsum, ROM coal and phosphate rock.
Shale King Single Roll Crushers produce primary and secondary sized products and are designed specifically to process rock. They are ideal for oil shale and materials of similar hardness.
Rockmaster® Single Roll Crushers are the heaviest-duty model in the McLanahan line of Single Roll Crushers. They are ideal for the most severe crushing applications and reduce extremely hard material and typical mine refuse.
McLanahan invented the Single Roll Crusher in 1894.