Sampling Systems
Sampling Systems assist in identifying and verifying the quality or composition of a material that is shipped, received or utilized in a process.
Applications
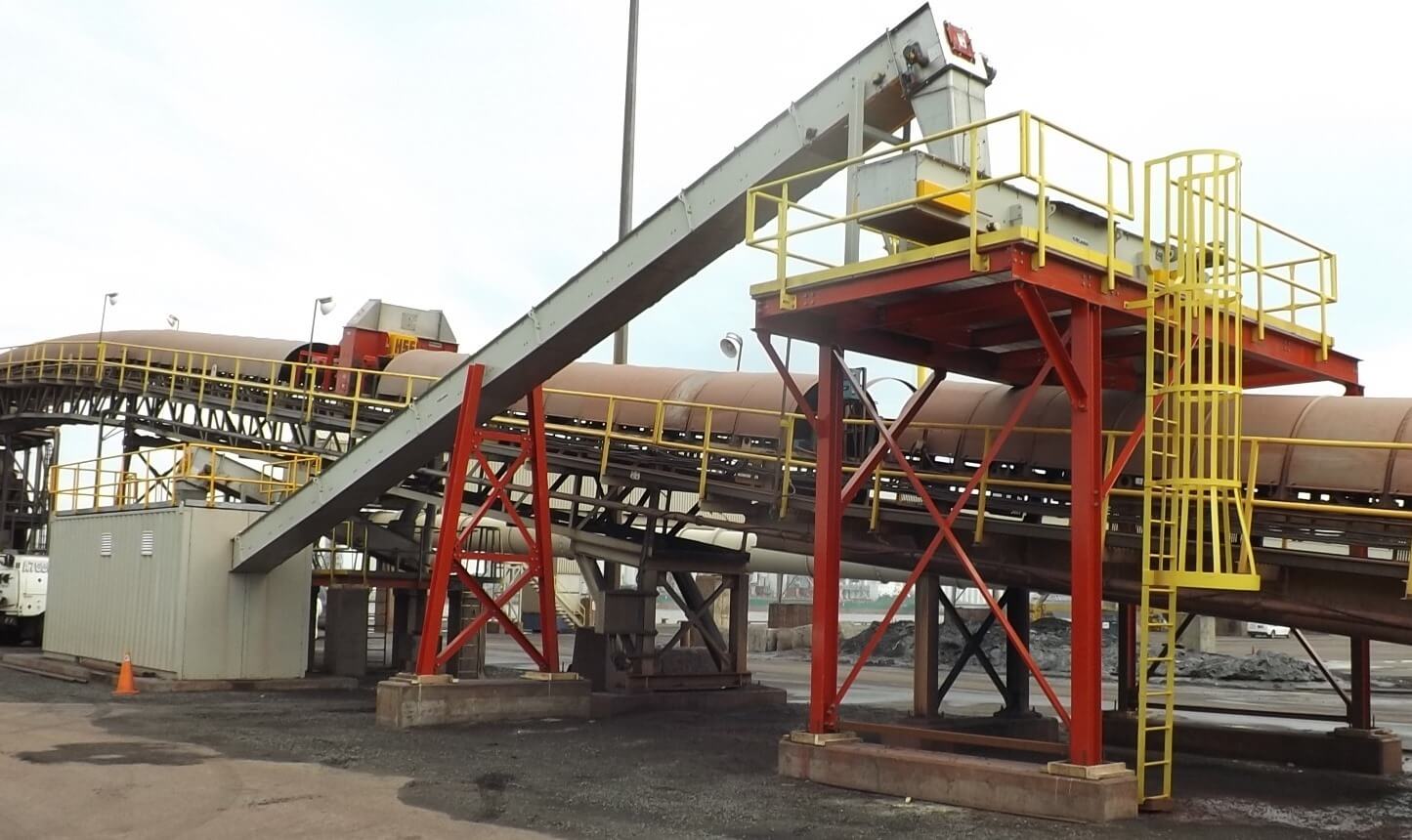
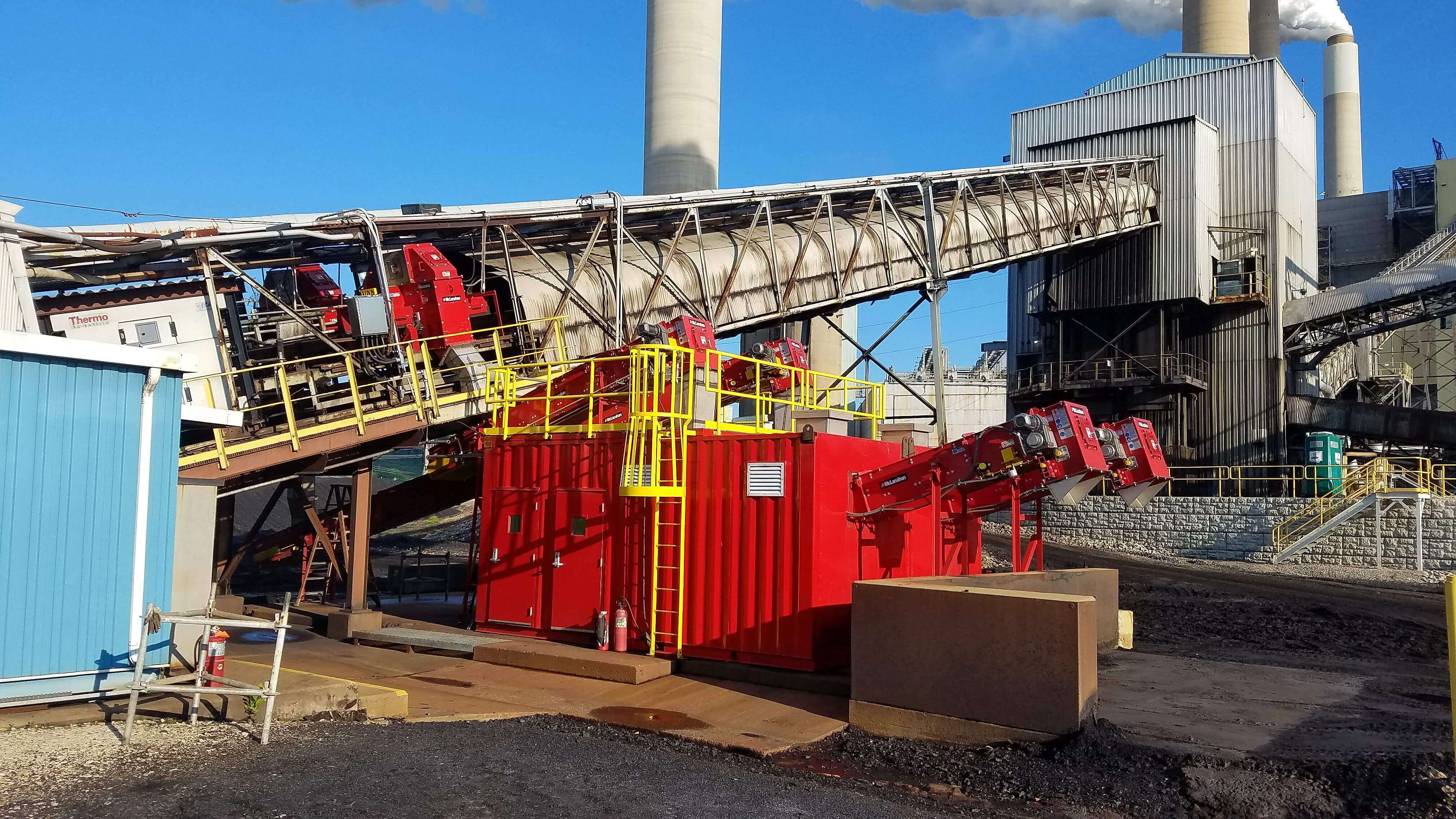
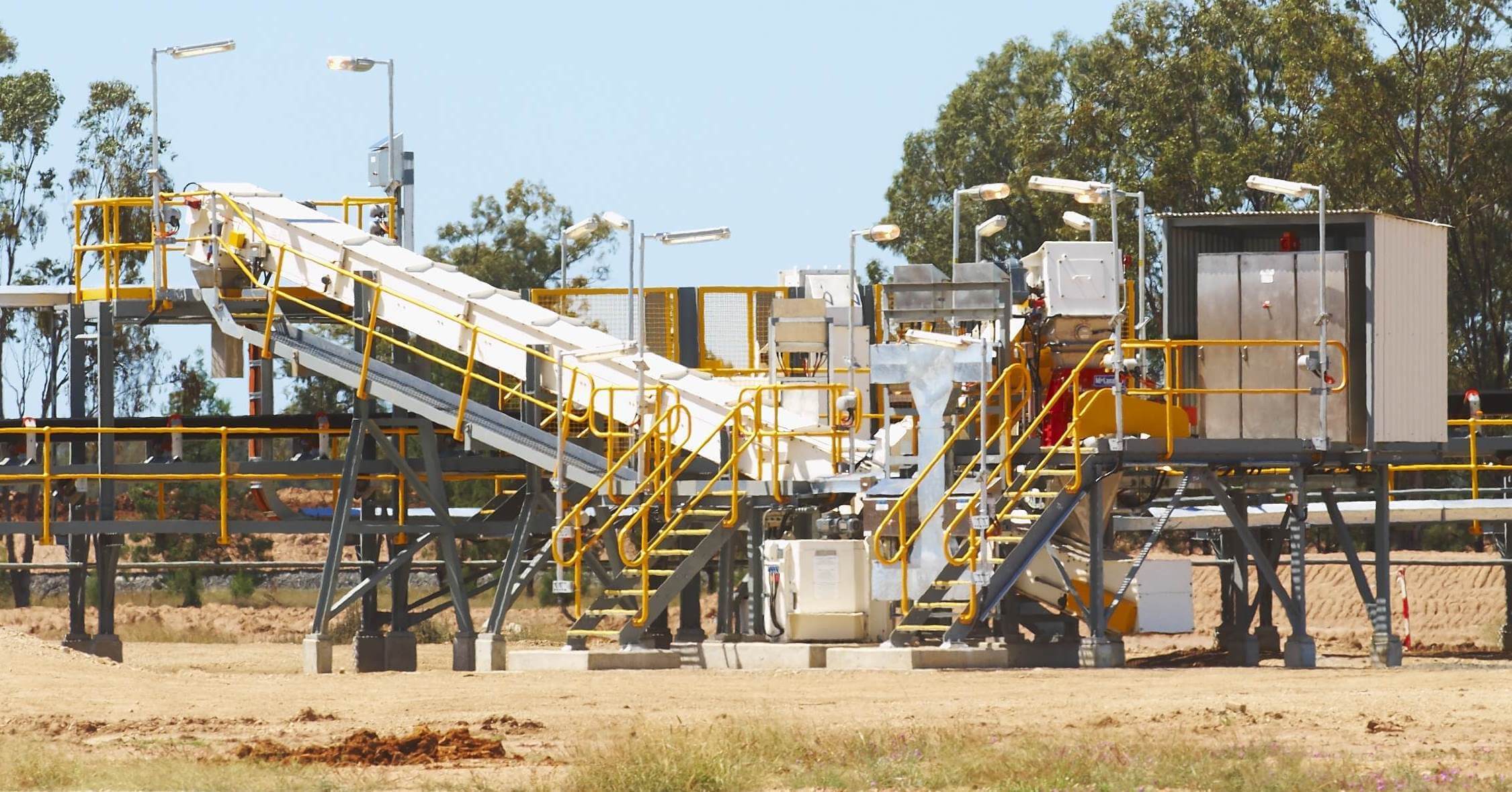
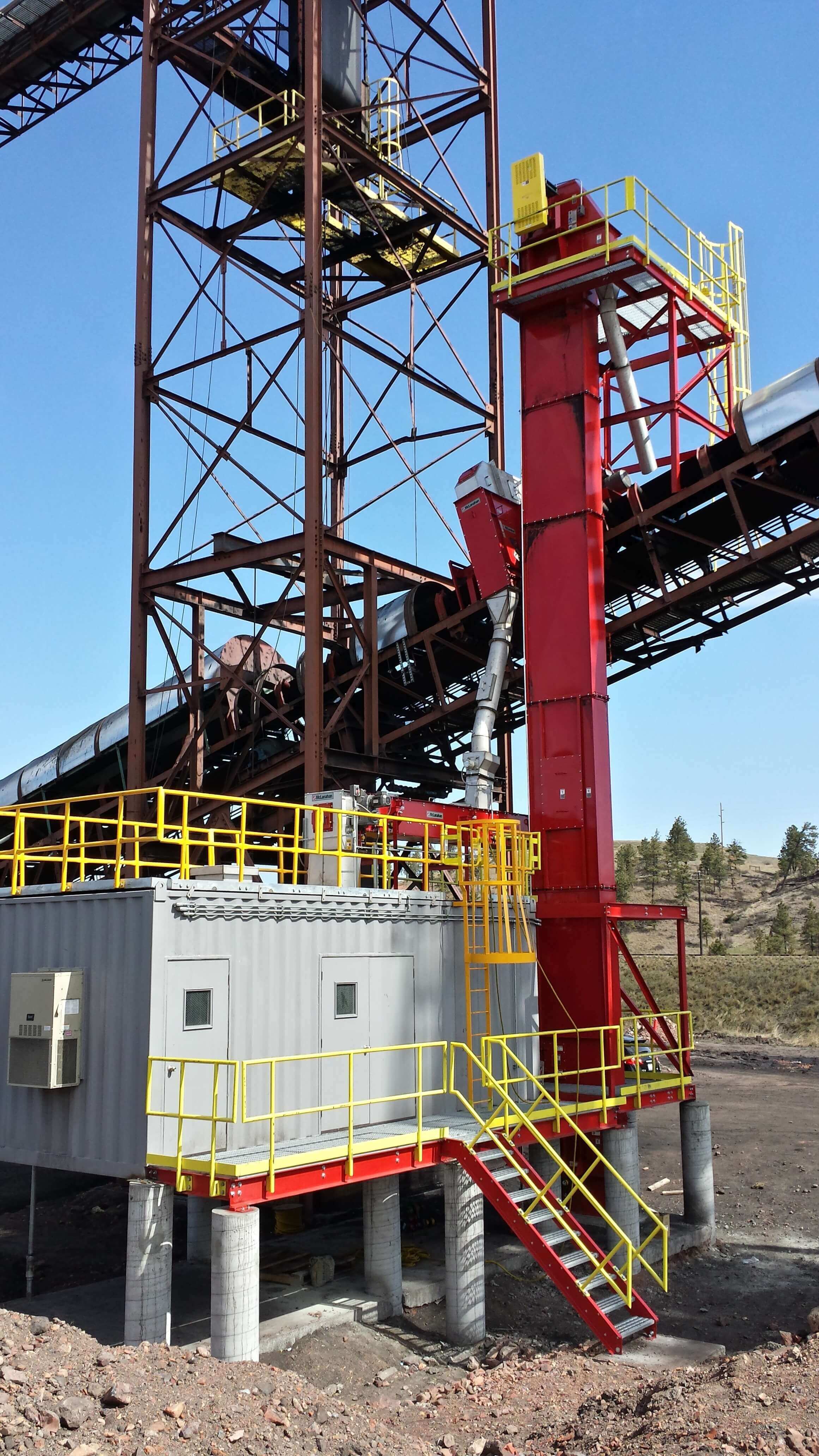
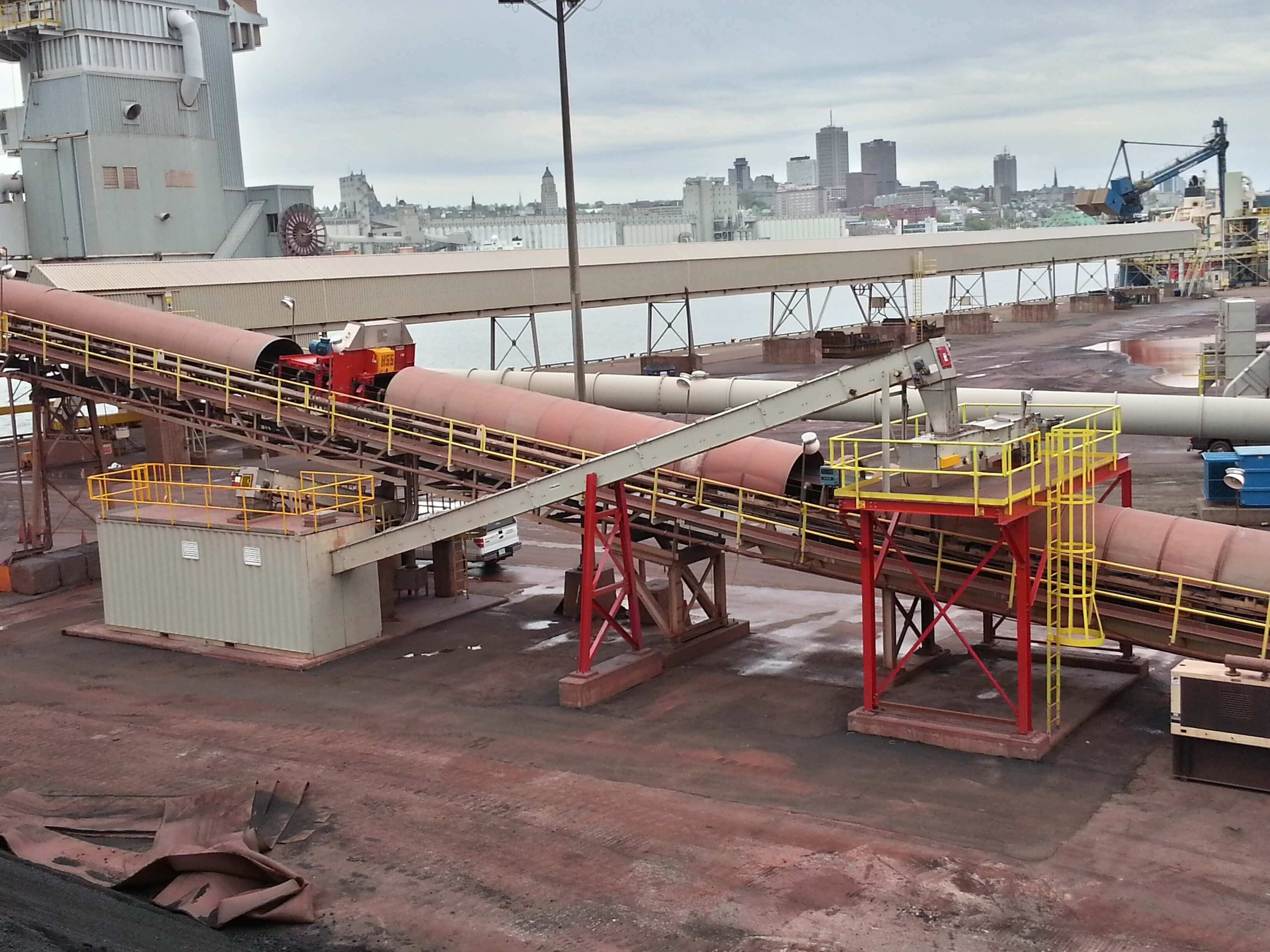
Sampling Systems assist in identifying and verifying the quality or composition of a material that is shipped, received or utilized in a process.
Applications
Jump To:
Many different types of mechanical Sampling Systems are available, each with its own set of features and benefits. These systems can include anything from sampling material from a moving product stream to containerized sampling to sampling slurry material. None of these samplers work and operate in the exact same way, and it is extremely important for any material processing application to work with an experienced manufacturer or consultant to understand everything from the system layout and integration to the long-term site goals.
In general, mechanical Sampling Systems are designed to create an automated process that eliminates the need for manual sample collection. Cross-Belt Sampling Systems are integrated directly onto a conveyor system to collect samples, while Falling Stream Sampling Systems collect material from a moving point. Additionally, McLanahan offers Auger Sampling Systems for applications where material needs to be sampled from a fixed point.
For years, McLanahan’s customized sampling solutions have been successfully implemented into a variety of industries — first as HSS Sampling Systems, and then as McLanahan Sampling Systems when HSS was acquired in the 1990s. Customers looking for long-term success in rugged applications using a Sampling System designed to meet their specific requirements need look no further than McLanahan.
McLanahan understands the importance of collecting correct, representative samples. These samples provide the foundation for testing and evaluation that allows for good decision-making — from valuing a given consignment of material to planning the future of an entire operation. Poor sampling (or no sampling) results in bad data that will very likely have a negative impact on outcomes associated with decisions based on that data, both in short-term operation and in longer-term financial impacts.
This is why McLanahan takes the time to understand your process and offer the best possible solution rooted in sampling standards and experience-driven best practices related to sampling and material handling. The result is a sampling solution that packages the optimum blend of sampling theory and real-world practicality into a cost-effective sampling system fit for your site and application needs. This often means customizing layouts or parts of individual machines to best suit what a client is trying to accomplish. Sampling projects may be similar, but rarely are they exactly the same. McLanahan’s flexibility in design allows us to offer the best options while the competition may offer standard options that are merely good.
Use McLanahan Sampling Systems for collecting correct samples to: determine the appropriate value for a material as-produced or as-shipped, verify the quality or value of an as-received product, determine the composition of an as-fired fuel, monitor plant performance or the performance of specific equipment within the plant, calculate metallurgical mass balances and evaluate the amount of a desirable (or undesirable) component distributed within a bulk material.
McLanahan Sampling Systems are used for collecting correct samples to:
Use McLanahan Sampling Systems in nearly any dry bulk material application. Examples of past projects include coal, concentrates, ores, metallurgical and petroleum coke, sand, stone, gravel, salt, potash, phosphates, bauxite, lignite, wood pellets and other wood products, biomass and others.
The final samples collected should be analyzed and charted on a continuous basis. What analysis is performed and what charting techniques are used will depend on what material is being sampled and the sampling goals of the end user. Periodically, perhaps once or twice per year, the system should be verified, meaning that the overall operation of the system and the operation of individual pieces of equipment are evaluated against historical data and theoretical data to determine if the system is operating at a high level. After verification activities are complete, a system is often bias tested. A bias test is simply a comparison test of samples produced by the mechanical Sampling System to samples collected by another method, usually stopped belt samples.
A wide variety of sampling equipment is available on the market today. This variety can be attributed to a number of reasons, such as industry preference, type of material being sampled, system layout restrictions and so forth. In general, sampling types can be broken down into three main categories: falling stream, cross belt and auger. Falling Stream Sampling Systems are probably the largest category. They intercept sample material either from a free-falling stream of material or from a stream of material moving through its natural trajectory, as when material is discharged from a conveyor. Cross Belt Sampling Systems are installed on belt conveyors and, when activated, swing a cutter assembly across the moving conveyor belt to collect an increment. Auger Sampling Systems are used to collect samples from a stationary lot of material, such as in a truck or railcar. Sometimes augers are used in sampling stockpiles.
Despite only three main categories of samplers, there are many varieties to choose from, and any number of combinations of types of samplers may be used to develop a sampling system as a whole.
McLanahan offers a variety of mechanical Sampling Systems to ensure product specifications are being met.