Roll Presses
Often used in series with a primary separator, such as a Rotary Drum or Inclined Screen, Roll Presses further reduce the moisture content of the removed fibers.
Download Brochure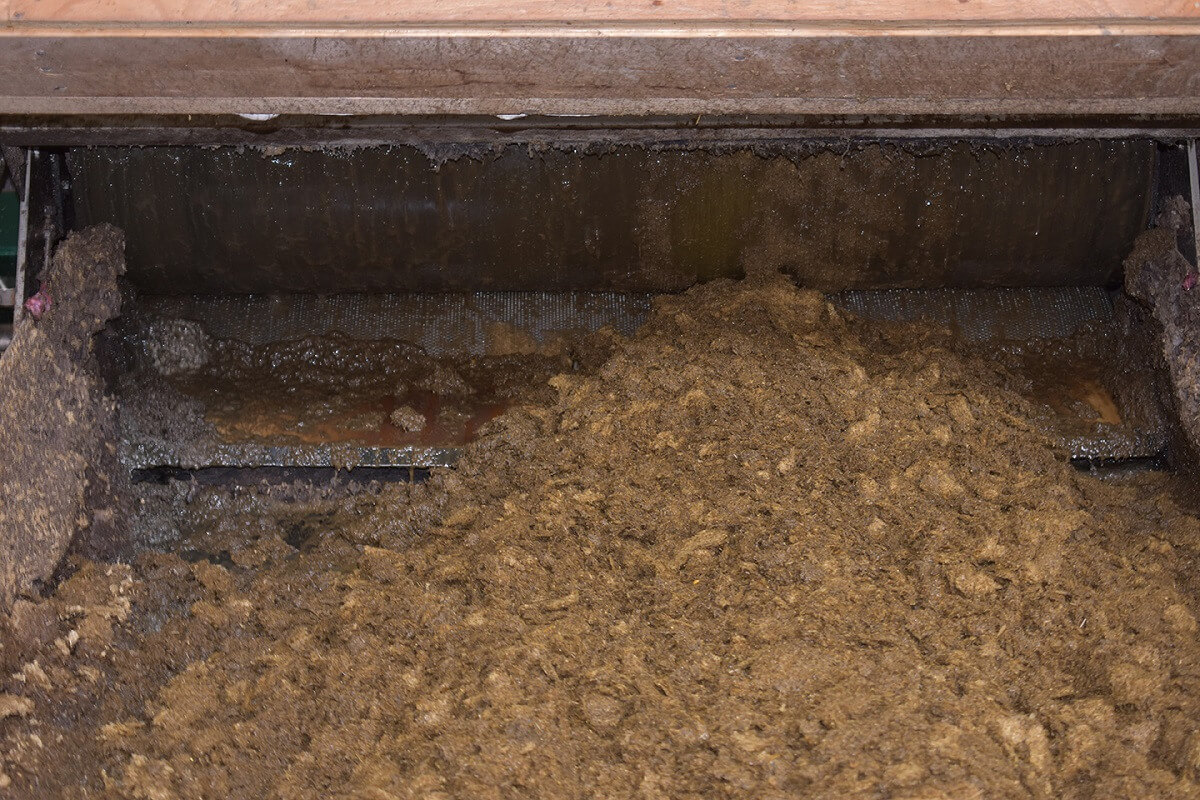
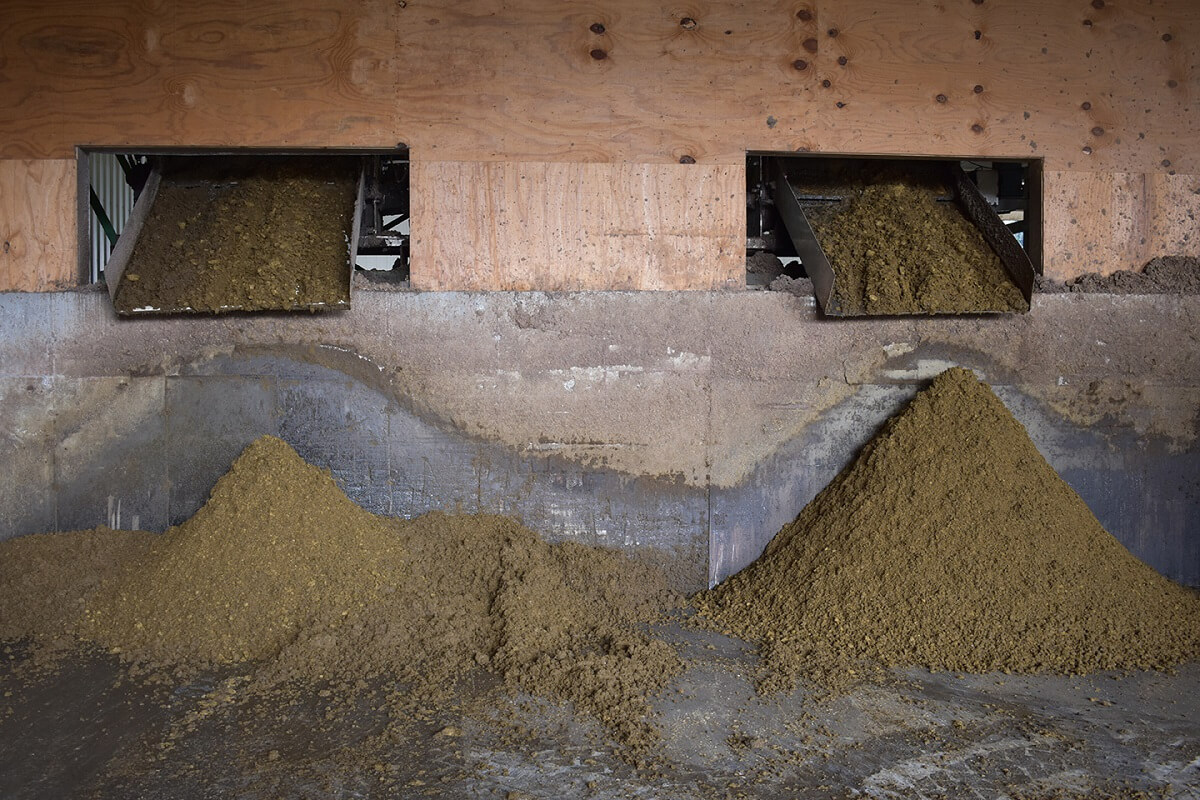
Often used in series with a primary separator, such as a Rotary Drum or Inclined Screen, Roll Presses further reduce the moisture content of the removed fibers.
Download BrochureJump To:
Roll presses are used as a secondary step in the dewatering process due to their small screen area and relatively low capacity. Their slow operation and high pressure points produce a highly dewatered product that is readily stackable and easily transportable. This secondary dewatering device is used in place of Screw Presses where abrasion is a concern, such as dairies that use sand bedding.
Roll Presses are available in multiple widths and press zones. They are sized according to the amount of material that needs processed and the amount of moisture that needs to be removed. They are used in a wide range of industries to dewater organic and non-organic materials. Besides manure fibers, these presses have been used to dewater plastics, organic sludges, paper pulp, fiberglass, wet leaves and nut hulls.
Wet materials are fed into the top of the press, onto the first press zone. The rotational movement of the drive roll pulls the material through the press zone. Extremely high pressure is applied across a very small area called a nip point. High pressure at this nip point squeezes a portion of the liquid out from in and around the fibers and forces it through a screen, while the dewatered fibers continue to rotate with the drum and are mechanically removed by either a scraper or a rotating brush.
McLanahan Roll Presses can be supplied with one, two or three press zones depending on the amount of moisture that needs to be removed. A single zone press will produce a product with about 80% moisture. With the addition of a second zone, that moisture can be reduced to about 75%, and a third zone will reduce it further to about 70%. Two sizes are available, the 36” and the 48”. These sizes are the width of the press and dictate how much material can be processed.
All standard McLanahan presses are built on a heavy, 304 stainless steel frame. They require low horsepower due to their low speed and low friction. They are simple to operate and maintain. To minimize plugging and stalling, a simple clutch system on the top drive pulls tramp material through the drums.
Each roll is supported by bearings that are isolated or shielded from the manure. The bottom roll is supported by an oversized pillow block bearing, which is shielded from the manure by a shaft seal.
Pressure is applied to the top roll by an adjustable air spring system. By using an air spring system, the pressure between the rolls can be quickly and easily adjusted by raising or lowering the air pressure.
For safety, these units are fully enclosed and shielded. A grease bank is located on one side of the machine to allow the bearings and pivot points to be lubricated from one location without removing any guards.
The size of press is determined by what type of materials are being fed into it and how it’s being fed. Most of the current installations involve manure dewatering. Here is a chart showing the different sizes and capacities. For applications other than manure, please contact McLanahan’s agriculture team for sizing and selection.
This depends on the goals of the system. If the goal is simply to dewater the material enough to handle with a payloader and haul to the fields, a single-stage press is usually sufficient. If there are other goals for dewatering, then a double or single press may be a good idea. This chart shows the amount of dewatering that happens at each press stage.
A small tank compressor is all that’s needed. Once the air springs are filled with air, they consume little if any air during operation.
A UHMW scraper is standard. In the case of long, stringy materials like fruit stems or even shredded plastic, which can build up under a scraper, a motorized brush is used.
Both a Roll Press and a Screw Press operate under the principle of applying high pressure to squeeze the moisture from the solid material, but each does so in a slightly different way.
The Roll Press contains two rolls that rotate counter to each other and contact each other at a small area called a nip point. This is the point where pressure is applied between the two rolls. The bottom roll contains drainage holes to allow the water to escape once it is squeezed out. The top roll is solid, and is often constructed or covered with a slightly softer material than plain steel. Many times this material is rubber or urethane. Thickened material is fed into the top of the roll, near the nip point. As the rolls rotate, they pull the material through and the high pressure squeezes water out. There is no sliding abrasion in the high pressure point in a roll press, so they are great to use when sand is used as a bedding material. A roll press isn’t suited to function as a primary separator unless the incoming feed slurry has a high total solids (TS) concentration. With dairy manure, this would need to be about 12% TS or higher.
A Screw Press can handle much lower total solids concentrations and higher incoming flow rates; therefore, it is suitable to be used as either a primary separator or secondary dewaterer. Unlike a Roll Press, which uses two counter rotating rolls to create a nip point, a Screw Press uses a rotating auger contained within a screen. The auger rotates constantly while material floods the interior of the screen. Larger fibers are trapped on the screen while liquid and smaller particles pass through. As the auger rotates, it scrapes the captured fibers from the screen and advances them to the discharge. As the fibers approach the discharge, they begin to form a thick plug of material. Paddles at the front of the machine retard their forward motion and the plug is forced to slow down and pressure begins to form. It’s in this high pressure plug where dewatering occurs. Tight tolerances between the screw and the screen are necessary to ensure the captured fibers are advanced forward into the dewatering zone. Due to these tight tolerances and the sliding abrasion that happens between the screw and the screen, Screw Presses aren’t the best choice for dewatering manure if sand bedding is present.
Roll presses are used in a wide range of industries to dewater organic and non-organic materials.