Quad Roll Crushers
McLanahan Quad Roll Crushers are ideal for producers who want to accomplish two stages of reduction in one pass.
Applications
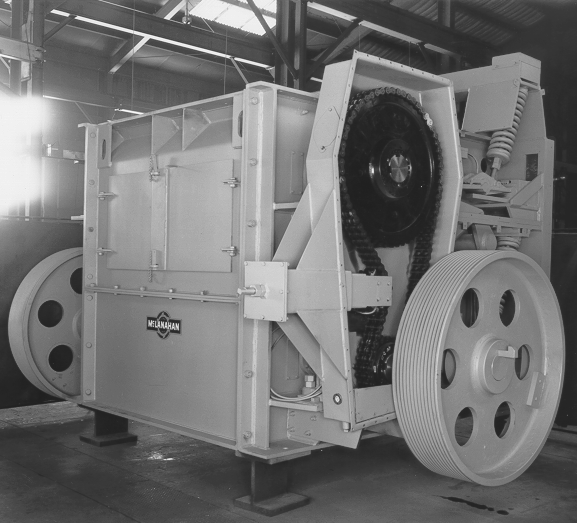
Jump To:
Depending on the duty class, Quad Roll Crushers can be used in ROM applications such as coal, salt, lime, pet coke and potash operations, among others. These crushers are designed as two Double Roll Crushers, with both the primary and secondary stage achieving a 4:1 reduction ratio. The intermeshing tooth design in the McLanahan crusher means that no timing gears are required.
Quad Roll crushers are designed for larger feed sizes and high ratios of reduction at high capacities. The top stage of the Quad Roll crusher is essentially made up of a double roll crusher, which is designed with the appropriate diameter rolls and tooth configuration to readily grab the incoming feed material. This stage is designed to reduce larger feed sizes at a 4:1 ratio before feeding directly to the secondary stage.
The secondary crushing stage consists of another double roll crusher arrangement. The bottom or secondary stage is fed directly from the top stage where the feed material is channeled between the crushing rolls. A combination of compression and shear forces created between the rolls reduce the feed material to the desired product size while producing a cubical product with minimum fines.
McLanahan’s mechanical tramp relief systems employ a spring-and-toggle mechanism that activates whenever an uncrushable object enters the crushing chamber. Once an excessive force is applied to the movable roll assemblies, they toggle or break open to allow the uncrushable item to pass. The tramp relief system then closes, returning both stage movable roll assemblies to the previous setting while allowing the crusher to continue operating uninterrupted.
Optional features include hydraulic product adjustment, roll scrapers, automatic lubrication, wheeled support base and other custom solutions.
By creating one machine to do the work of two, McLanahan has generated a lower overall headroom requirement and a simplified process flow. Quad Roll Crushers also feature hydraulic product size adjustment for both the primary and secondary crushing stages. This allows producers the option of changing size specifications or adjusting for wear if the need arises.
Quad Roll Crushers feature an automatic toggle relief mechanism for both stages. This allows the movable roll in both the primary and secondary stages to open, safely pass uncrushable material and return to its original setting for continued operation. In addition to the tramp protection feature, Quad Roll Crushers also include access doors for inspecting for wear or to facilitate roll maintenance. All V-belt and inter-stage drives are guarded for personal protection.
Depending on the customer’s feed size to product size reduction ratio, two stages of crushing should be considered, such as two Double Roll Crushers, Sizers or a Triple Roll crusher.
It is the ratio of the feed size to the desired product size. As an example, if the feed size is 12” and the desired product size is 3”, then the ratio of reduction is or 4:1. With Quad Roll crushers, you have a 4:1 on the top stage followed by a 4:1 on the bottom stage.
Standard-Duty Quad Roll Crushers are the lightest-duty Quad Roll Crusher and are designed to perform two-stage reduction on soft materials such as clean coal, salt, lime, coke, glass, etc. This model is powered by a single motor and features an inter-stage V-belt drive between the primary and secondary stages of crushing.
Medium-Duty Quad Roll Crushers perform two-stage reduction of materials such as salt, potash, harder coals that contain medium-hard shale and slate, and other minerals, but are not suitable for hard rock and other refuse. The Medium-Duty Quad Roll Crusher uses two motors to drive its four rolls and includes an inter-stage V-belt drive between the primary and secondary rolls.
Super Quad Roll Crushers perform two-stage reduction for ROM coal that contains moderate amounts of medium-hard refuse, as well as other materials of similar compressive strength. It is the heaviest-duty model of Quad Roll Crusher that McLanahan makes, but it is not intended for very hard or abrasive rock. Designed for high-capacity applications, the Super Quad Roll Crusher is capable of throughput up to 4,500 TPH and is available with dual or four motor drives depending on the application.
Abrasive Material Quad Roll Crushers have the ability to perform two-stage reduction of hot, abrasive feeds such as sintered iron ore and coke. This crusher has a number of features that limit the wear caused by abrasive materials and also simplify maintenance. These include abrasion-resistant renewable side and end liners, as well as a flanged shaft design to easily remove the primary rolls through the hopper and the secondary through the end plates. For hot feed options, McLanahan is able to provide water-cooled roll shaft assemblies, with bearings located outboard to dissipate heat and high temperature seals to protect the bearings.
Quadroll Crushers have long been used in a variety of applications, including ROM feeds, coal, trona, salt, glass and other friable minerals.