Overhead Beam Filter Presses
Overhead Beam Filter Presses are one style of recessed/membrane plate Filter Presses used to dewater and separate liquids and solids in a wide range of applications.
Applications
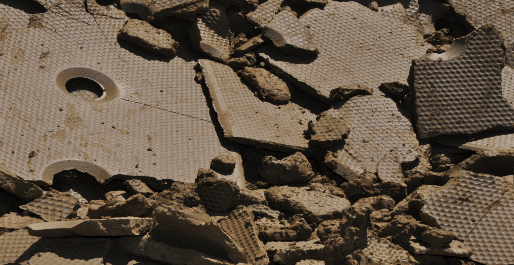
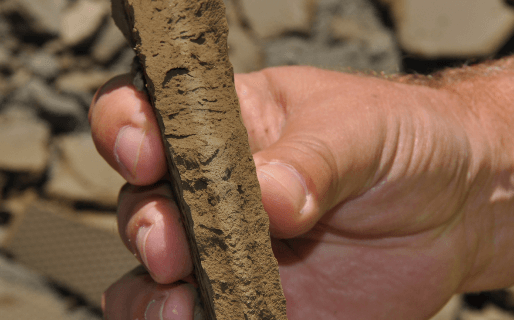
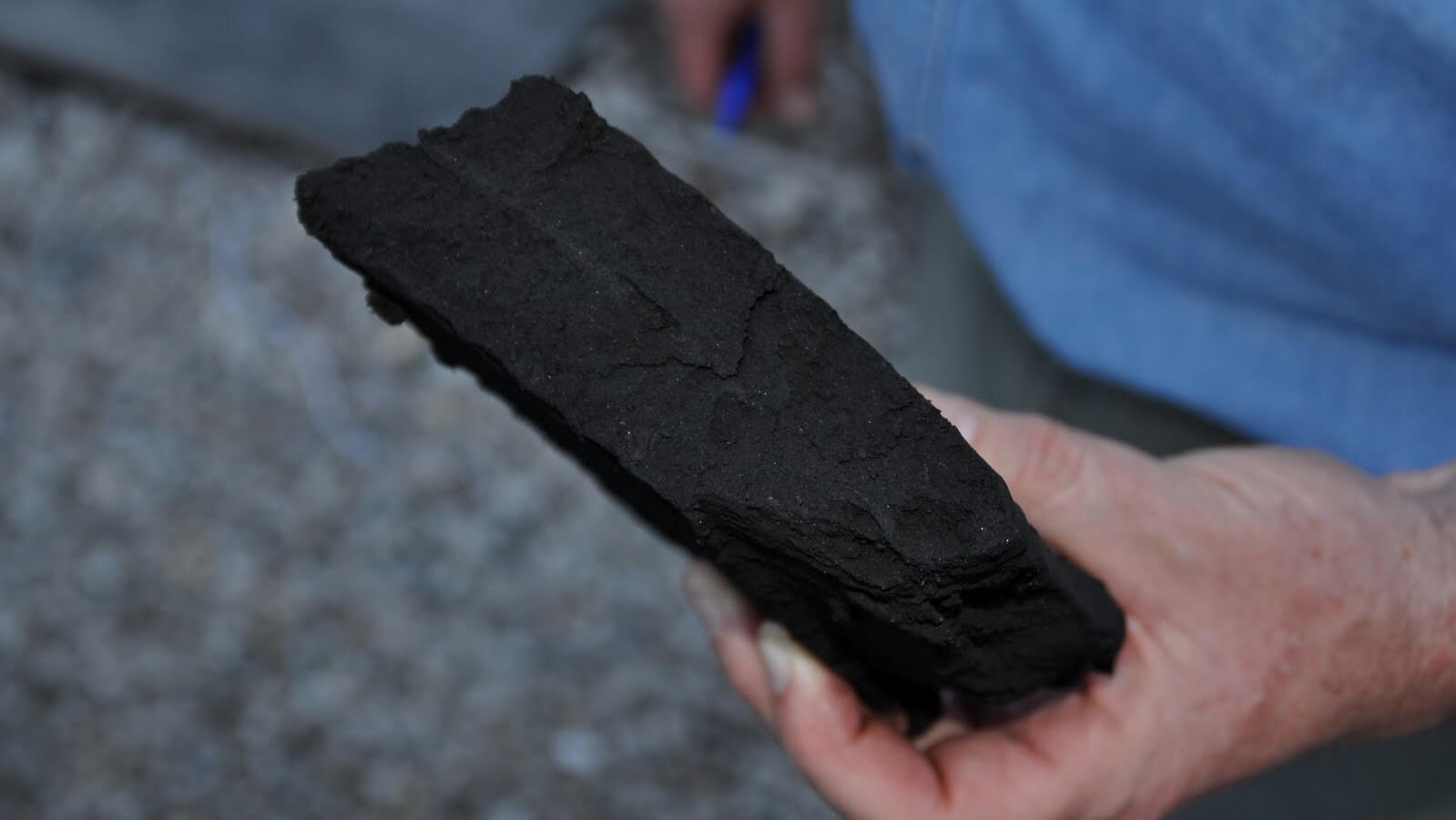
Overhead Beam Filter Presses are one style of recessed/membrane plate Filter Presses used to dewater and separate liquids and solids in a wide range of applications.
Applications
Jump To:
Dewatering occurs when slurry material is pumped into the cavities created between the filter plates when they are hydraulically clamped together. The dewatered cake material accumulates between the filter plates, while the filtrate water passes through the filter cloths mounted on the plate surfaces.
The filter plates are mounted from an I-beam above the filter press, giving very good access to the filter plates and filter cloths. This orientation creates no interference when the dewatered filter cakes discharged and limits any slurry contamination with the plate opening carousel mounted in the I-beam.
Overhead Beam Filter Presses typically are used in applications when larger volumes of materials are being processed. The plate sizes and plate counts can be very large to accommodate the customer’s high processing rates.
The Overhead Beam Filter Press uses the same basic technology as any other plate filter press to dewater slurry material and recover reusable filtrate water. The filter plates are suspended from an I-beam above the filter press. A hydraulic cylinder and tension rods are used to clamp the plates together, while a slurry feed pump forces the slurry between the plates where the slurry solids accumulate, and the filtrate water passes through filter cloths mounted on the plate surfaces. The plates are opened using a chain carousel system mounted on the I-beam designed to separate the filter plates one at a time after the plate stack has been hydraulically unclamped. The bottom and both sides of the filter plates are completely open and unobstructed, preventing any interference with the cake discharge. The overhead beam design also allows the easiest access to the filter plates and filter cloths for cleaning and maintenance.
Overhead Beam Filter Presses are used in a wide range of dewatering applications in many industries. The overhead beam style press is well suited for dewatering material that are difficult to dewater slurries with high clay content, very fine particle size or organic materials. With the plate opening system mounted in the beam above the filter press, most of the moving components are well protected from contamination and wear associated with abrasive and corrosive materials. The overhead beam filter presses can be fully automated for continuous operations without full time operator monitoring.
McLanahan Filter Presses are designed to generate easily managed dry product or waste material. The Filter Press also provides the ability to optimize recovery of clean reusable water. McLanahan Filter Presses can address many typical issues associated with fine material processing, including full slurry ponds/dams, high material handling equipment repair costs, limited expansion capabilities, environmental permit restrictions, high waste material handling costs and limited water availability.
McLanahan Filter Presses are used by many 24/7 operations that rely on Filter Press performance and excellent support to keep their plants running and profitable.
McLanahan Filter Presses are engineered using a single hydraulic cylinder. This results in robust and reliable automation capabilities with lower horsepower, fewer control valves and less complexity than multi-cylinder designs. McLanahan’s Overhead Beam style results in faster opening and closing for greater production and better cake release in tailings applications, while also providing larger plate openings for better cleaning and maintenance access.
Unlike the traditional plate and frame presses, McLanahan’s Filter Press line features modern recessed plates or membrane plates, both of which create a chamber for dewatering the slurry without trapping the cakes within the frames. This allows the dewatered cakes to discharge more easily than with traditional plate and frame presses.
Due to the variability in slurry material percent solids, particle size distribution, particle shape and material makeup, each site’s material should be tested prior to sizing a Filter Press for a specific customer application. McLanahan offers experienced lab and on-site pilot testing with a wide range of testing capabilities. Other parameters are used for green field sites when material testing is not possible.
McLanahan’s Customer Service Team offers a wide range of fast spare part sourcing as well as routine and emergency maintenance service support. All McLanahan Filter Presses can have customer remote control access capability for efficient monitoring and troubleshooting.
Additional equipment to consider for a Filter Press includes: Slurry surge tank, mixer, bridge and level sensor Slurry feed pump with VFD Membrane plate water supply tank and water pump Wide range of nylon, polypropylene or polyester filter cloth materials to matched application requirements Cloth washing system Drip trays doors below the filter plates Stainless steel or other materials of construction for corrosion resistance Compressed air system for core blow/cake dry Synthetic and metal filter plate material options Cake dry capable plates can provide additional water recovery efficiency Cake wash capable plates allow for removal of soluble materials from the cakes
Because plate Filter Presses can vary greatly in size, the cost varies widely also. Equipment cost can range from tens of thousands of dollars to more than one million dollars for a single Filter Press.
Filter Presses are often used in place of: Belt Presses Centrifuges Screw Presses Vacuum Drum Filters The primary reasons people would consider a Filter Press over these alternative technologies are for the reduction in operating costs, drier product, reduced chemical consumption, better solids recovery and the high degree of automation.
McLanahan Overhead Beam Filter Presses can hold larger plate sizes and a larger number of plates, making them more suited with high processing volumes.