Hydrocyclones
Hydrocyclones, or more simply Cyclones, and variations such as McLanahan Separators™ are used in a variety of applications, including classification, desliming, fines recovery, densifying and dewatering.
Applications
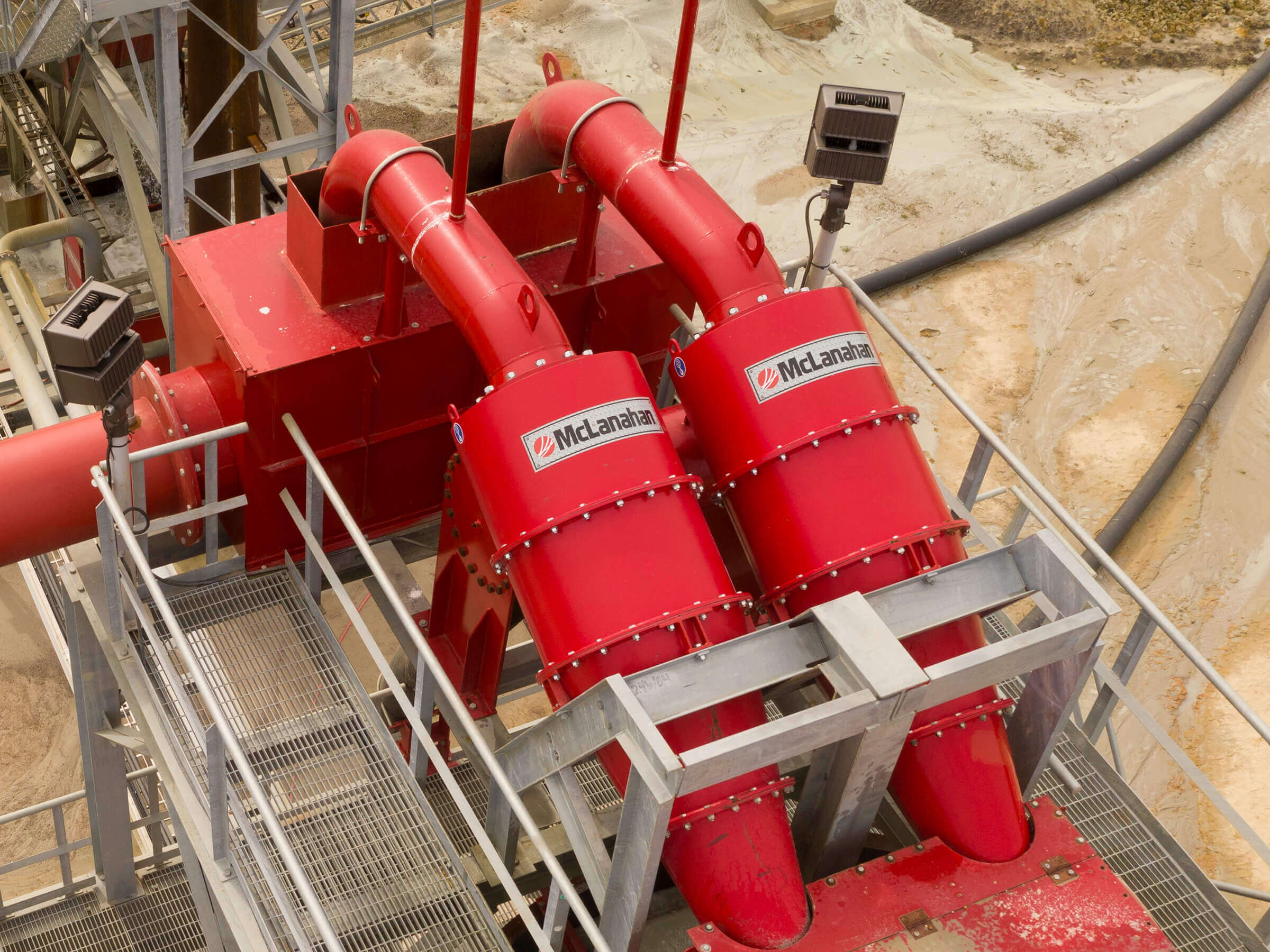
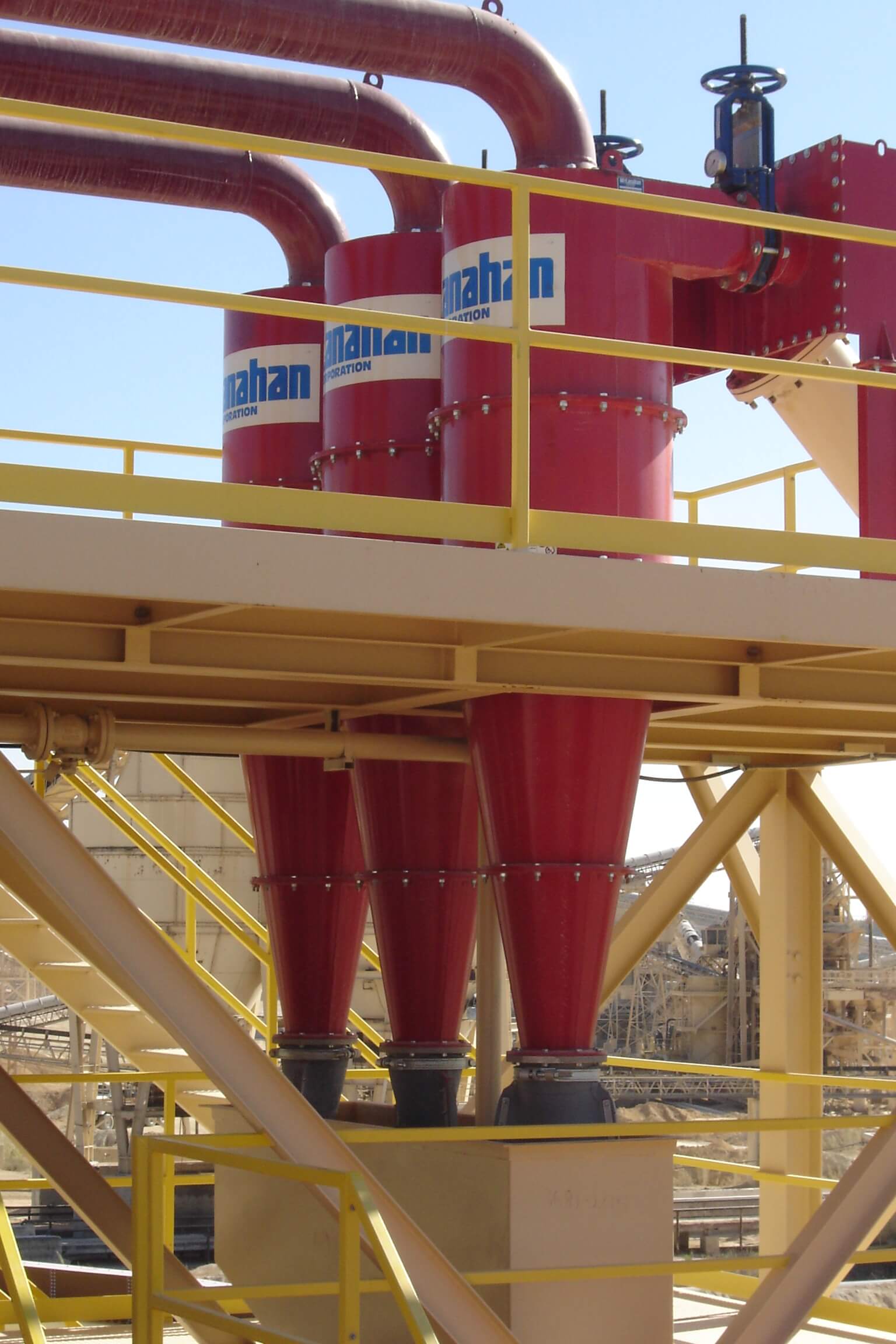
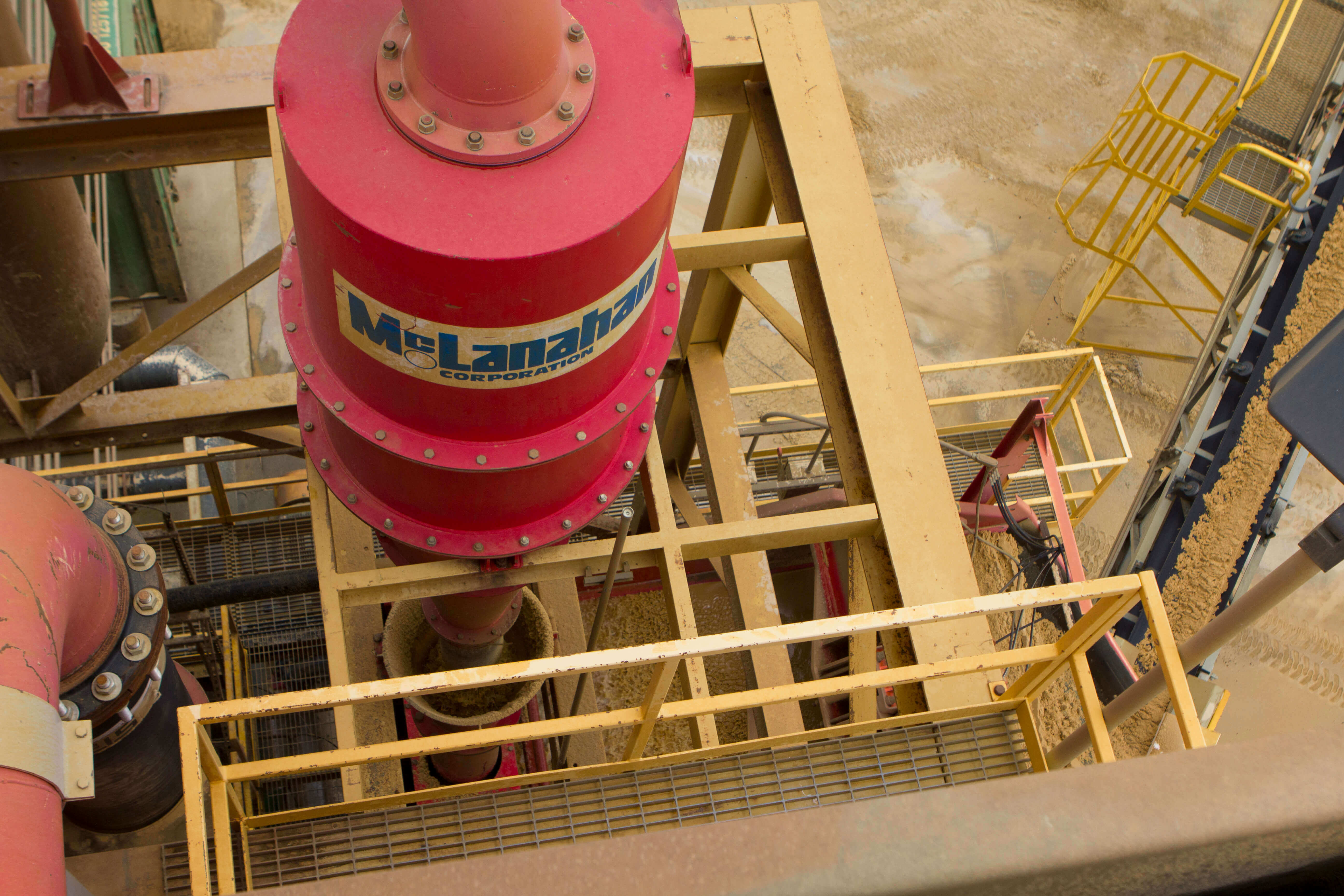
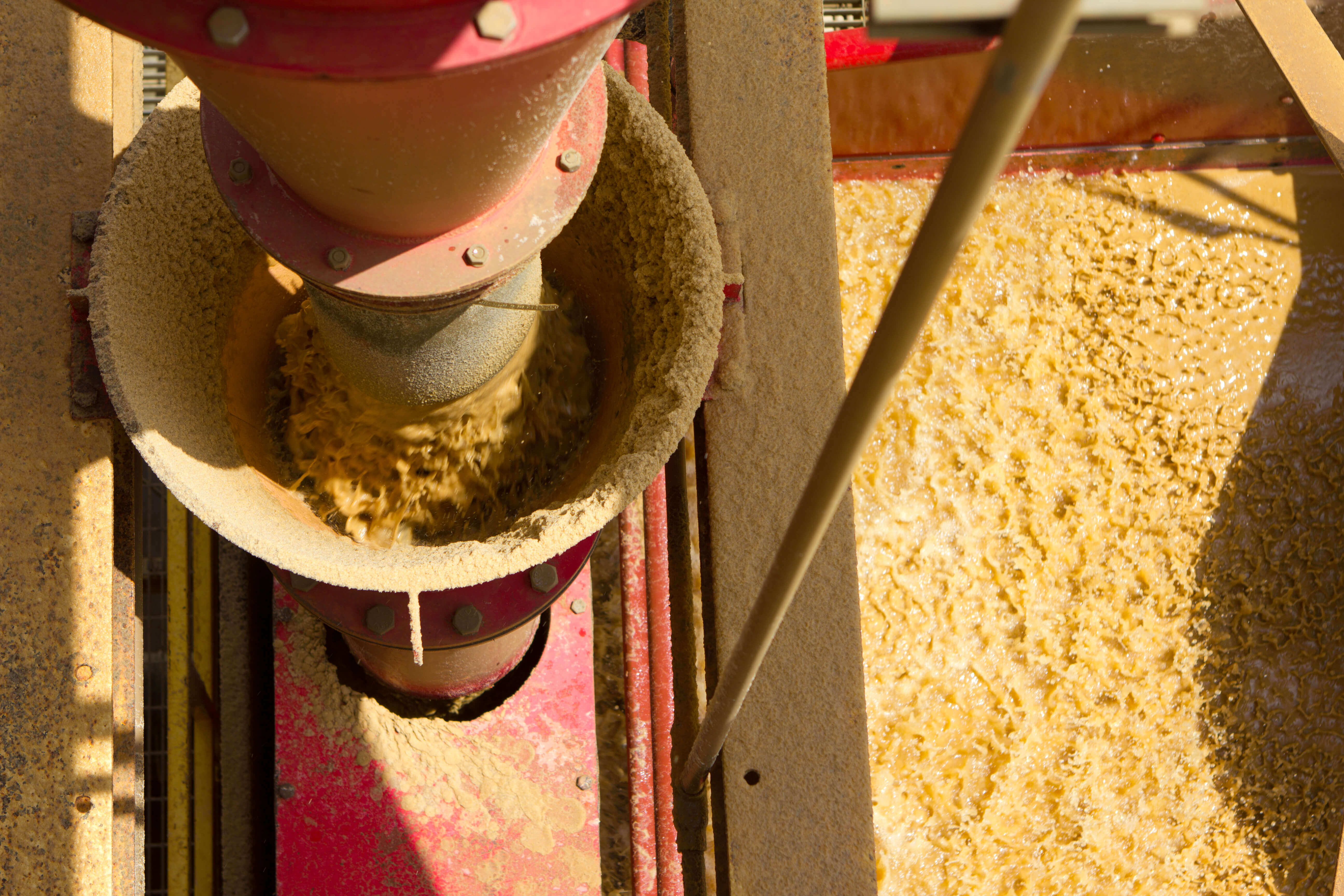
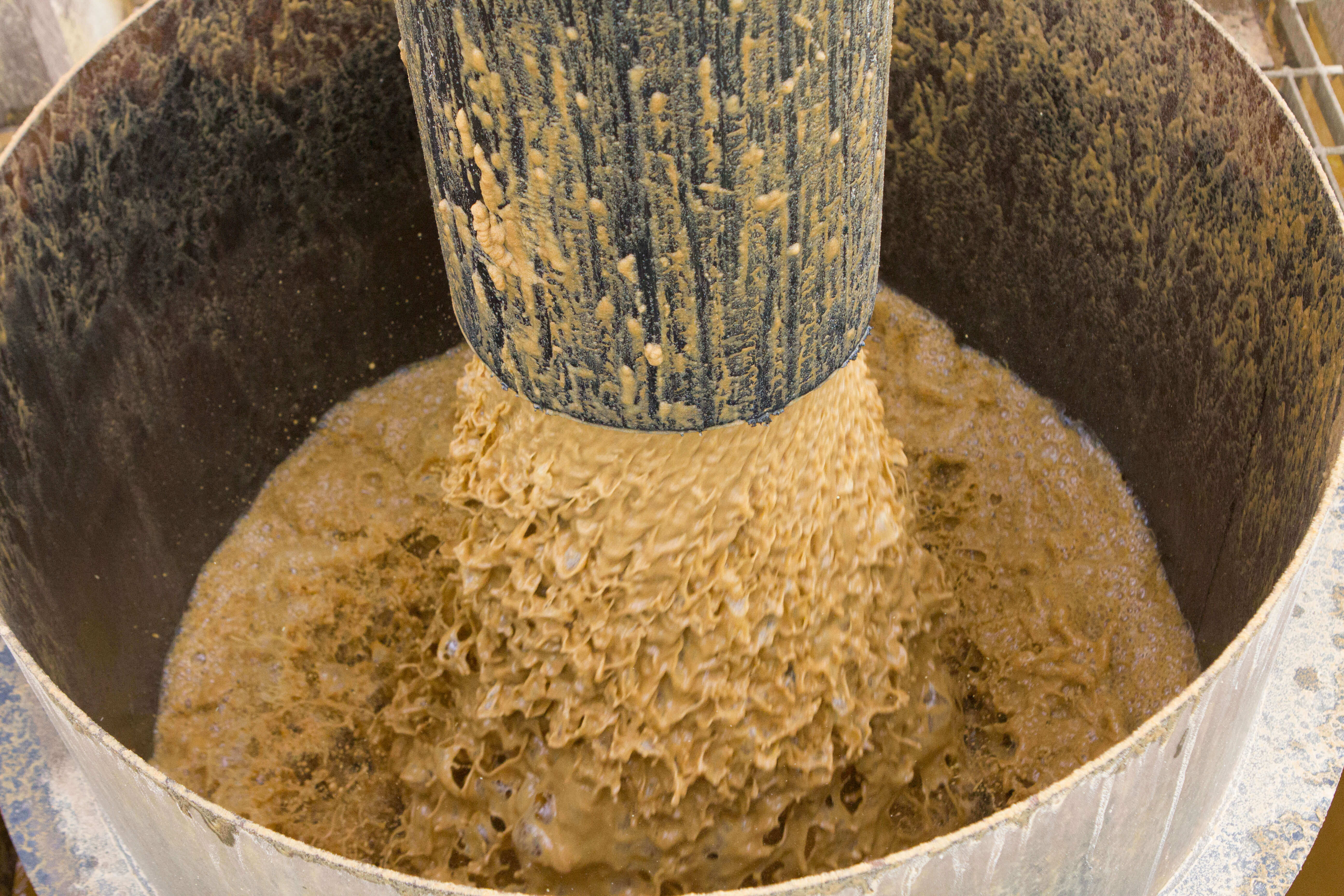
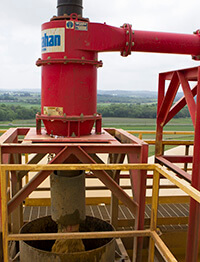
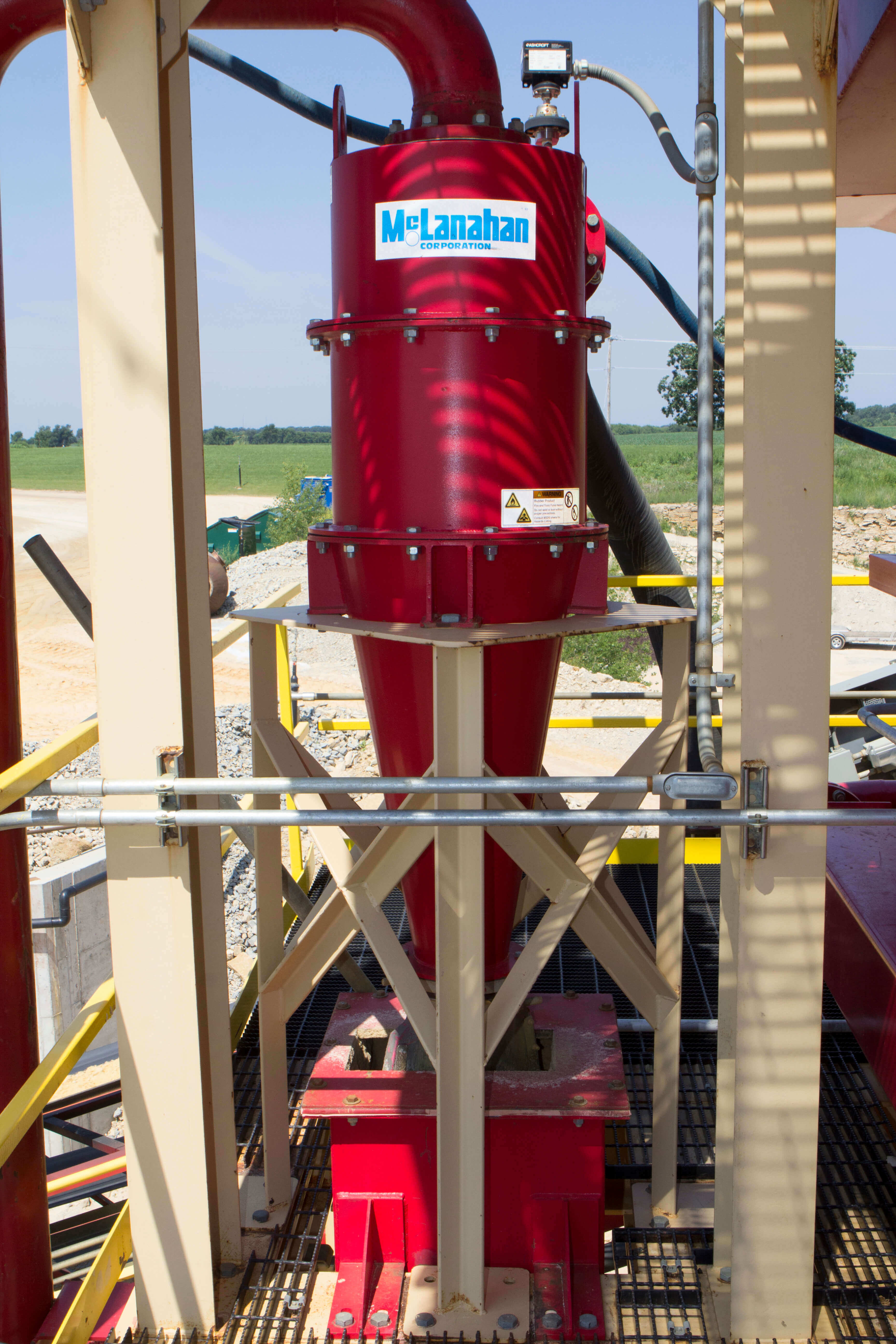
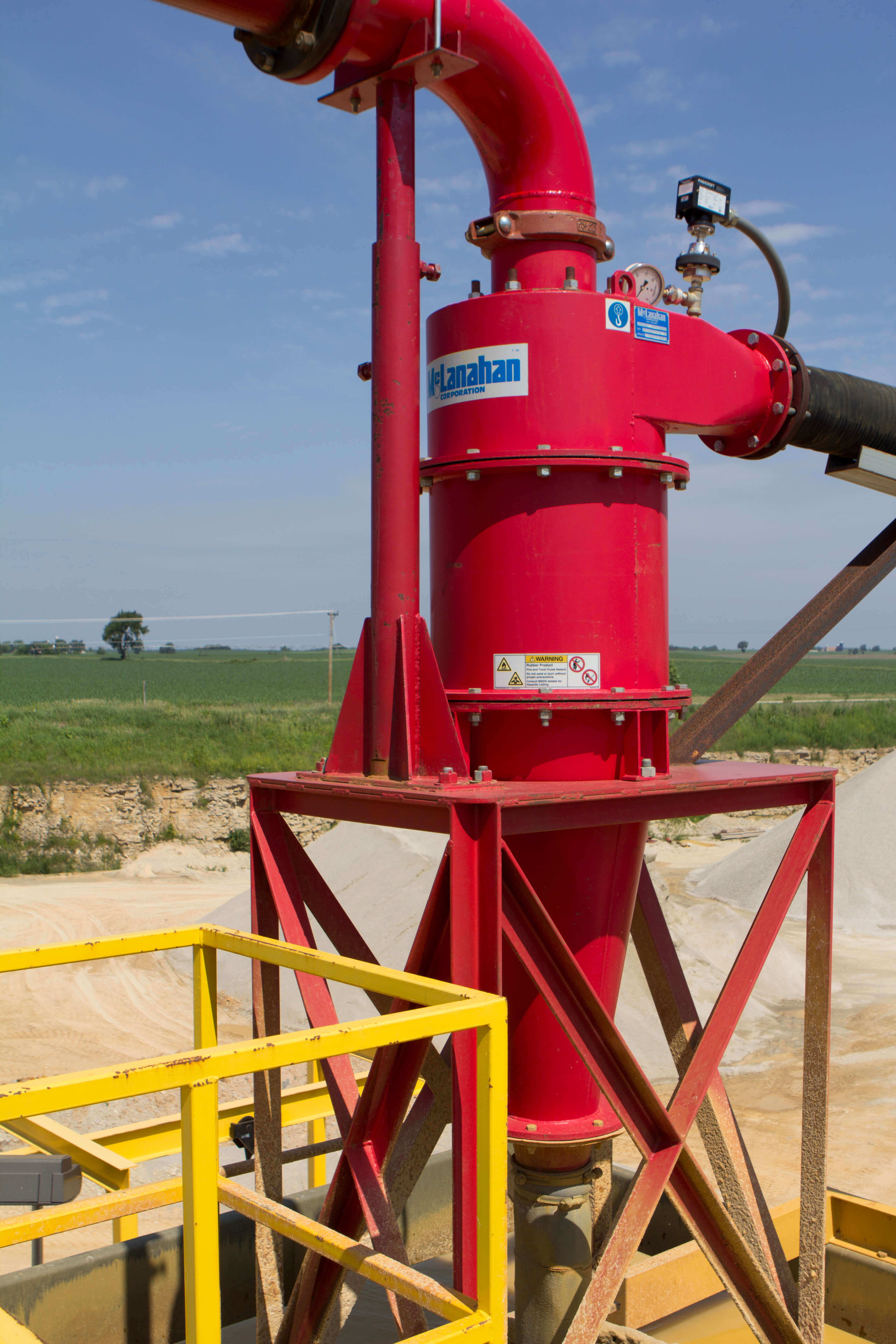
Hydrocyclones, or more simply Cyclones, and variations such as McLanahan Separators™ are used in a variety of applications, including classification, desliming, fines recovery, densifying and dewatering.
Applications
Jump To:
Hydrocyclones were invented in the late 1800s and became widely used in mineral processing because they are relatively inexpensive, process high volumes, take up minimal floor space and have no moving parts.
Hydrocyclones are commonly used for desliming, dewatering and sizing -4mesh (5mm) particles. They can be used in industries such as sand, aggregates, coal, industrial minerals, hard rock mining and more. The use of Hydrocyclones in washing and stockpiling is common in the construction aggregate industry. Desliming prior to Classification Tanks and Screw Washers can significantly improve the performance of these devices in high fines situations. Separators™ provide consistent density feed to Attrition Cells in Frac Sand.
For mineral applications such as in hard rock and precious metals processing, Cyclones are the most common equipment to control what size of materials exit the comminution (ball milling) circuit. In these applications, it is the fine fraction in the overflow that is the product. Different ores have different liberation sizes, so Hydrocyclones are configured in many different ways.
Alternative linings, such as polyurethanes and ceramics, are available for different chemistries (such as where amines are present) and for handling highly abrasive materials. Hydrocyclones can also be made from cast hard metals such as ni-hard and hi-chrome. These designs are often used in processes known as heavy media for coal and iron ore, etc.
Hydrocyclones also find use in pharmaceuticals; agricultural applications, such as sand/manure separation; pulp and paper; potable water and wastewater treatment systems; degritting of spray water; etc.
In Aggregate applications, typical recovery of 2.7 specific gravity particles is +200 mesh (75µm) at 2.7 SG; in typical Fines Recovery applications, Hydrocyclones capture down to 400 mesh (38µm) at 2.7 SG; and in specialty applications, recoveries are possible down to 625 mesh (20µm) at 2.7 SG.
Slurry enters the feed inlet at a designated pressure and volume. Independent of the shape or configuration of the inlet, slurry follows the fall of the upper cylinder in a rotating action. Resultant centrifugal forces send coarser material to the outer wall to travel downward and be further accelerated in the conical sections. These coarser fractions then exit through the apex, or spigot, at the bottom of the Hydrocyclone. Finer fractions remain rotating with the fluid in the inner core and are removed upward by an air core.
The air core is formed at the spigot/apex as air is drawn in to the Hydrocyclone. The vortex finder provides a pathway for the air to exit the body of the Hydrocyclone. As the air flows through the vortex finder, the fluids and finer fractions are dragged along to perform the classification of materials. The air core is important for the proper operation of the cyclone. If the air core is not formed due to excessive solids discharge, called roping, the cyclone will not efficiently classify the slurry. The apex/spigot is sized for the expect range of solids. Significant process changes may require a resizing in the spigot/apex.
McLanahan has collected field data from hundreds of applications, allowing process engineers to make the accurate selection of size and configuration for each application using computer simulations. Performance is influenced by the size of the unit and its operating pressure, as well as the inlet area, vortex finder diameter, underflow and overflow diameters, cylindrical sections and cone angle.
Hydrocyclones are exceptionally simple machines but require process knowledge to be utilized properly. Although there are many configurations, most Hydrocyclones have a cylindrical upper (feed) section, with either a tangential or involute style feed inlet, followed by lower conical sections ending with the apex. Designs that combine rubber-lined, bolt-together sections makes them simple to operate and maintain. Alternative linings, such as polyurethanes and ceramics, are also available.
While Cyclones are simple to operate, a great deal of understanding is needed to apply this technology to any given application. Whether the application is sand-washing or classifying high-end minerals, McLanahan’s process engineers have long experience in successfully applying this product into stand-alone applications and integrated systems. With our in-house developed simulations, we can reliably predict outcomes of different scenarios to evaluate new or existing installations. Using the application predictions and the "been there, done that" experience, McLanahan personnel can develop the best approach to any process requirements.
A modified version of the Hydrocyclone is the Separator™, which features an Automatic Discharge Regulator to improve underflow density. Separators™ are used when the downstream process is moisture sensitive and you want to maintain a specific density, such as feeding Attrition Cells/Scrubbers, or for stockpiling material.
Hydrocyclones are ideal for recovering down to 400 mesh (38µm) particles of 2.7 SG. This is typically done in the form of an Ultra Fines Recovery system comprised of a Sump, Pump, Cyclones and Dewatering Screen, which will have a discharge to waste nominally 90% passing 400 mesh (38µm) and a product discharging the screen in a drip-free, readily conveyable and stackable form. McLanahan uses 9” and 12” Hydrocyclones for this application in place of 4” units. We previously used 4” Hydrocyclones in our systems, but we found them to be plagued with blockages in the apexes of the Hydrocyclones, resulting in significant amounts of unprocessed materials. We have also replaced many clusters of competitive-brand small Cyclones with 9” and 12” units with the benefit of low blockage rates and longer life with very similar performance.
Hydrocyclones are limited in being able to dewater fine solids to a conveyable state. The finer the underflow solids, the more dilute it will be; therefore, Dewatering Screens are used to further dewater Hydrocyclone underflow.
Hydrocyclones and Separators™ are selected based on several parameters, including volume of flow, tons per hour of recoverable material and cut-point required. Larger units process higher volumes; however, the larger the Hydrocyclone, the coarser the cut. Therefore, processing a larger volume of slurry with the need to recover finer fractions would lead to the selection of several smaller units.
McLanahan Hydrocyclones are simple machines with no moving parts.