Filter Presses
Filter Presses dewater and separate liquids and solids in a slurry by pumping the slurry at high pressure into a series of hydraulically closed recessed plates lined with filter cloths.
Applications
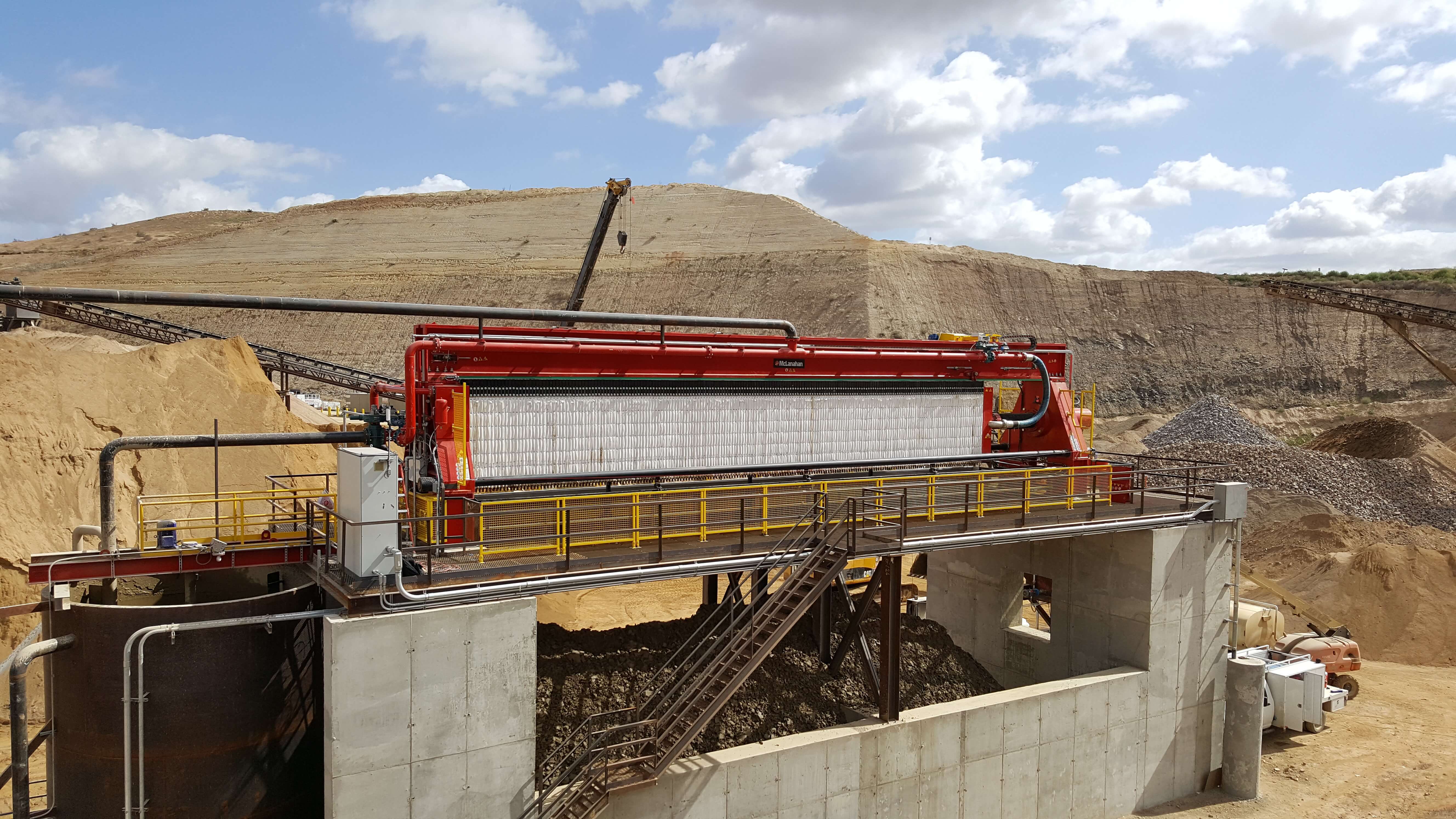
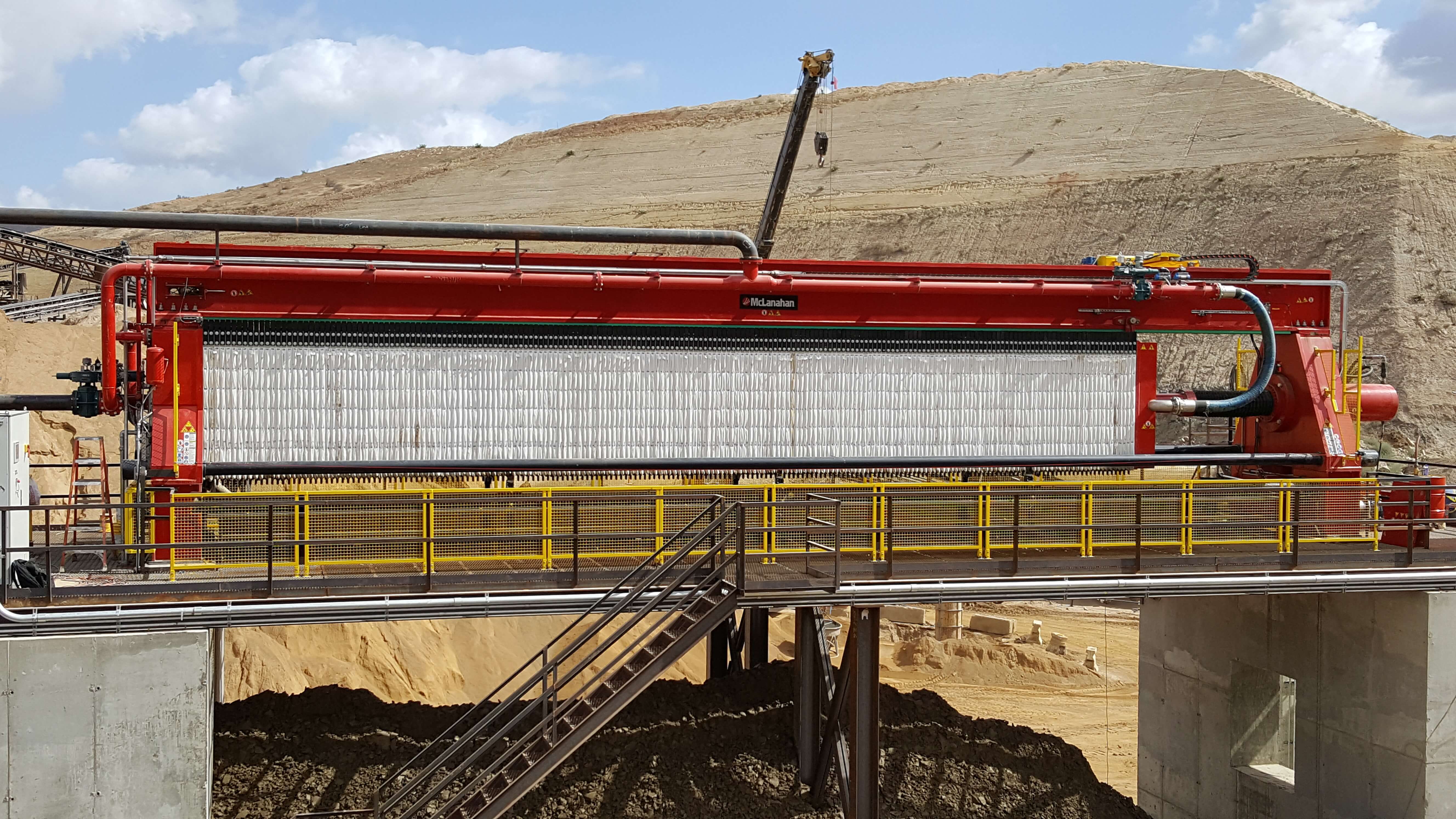
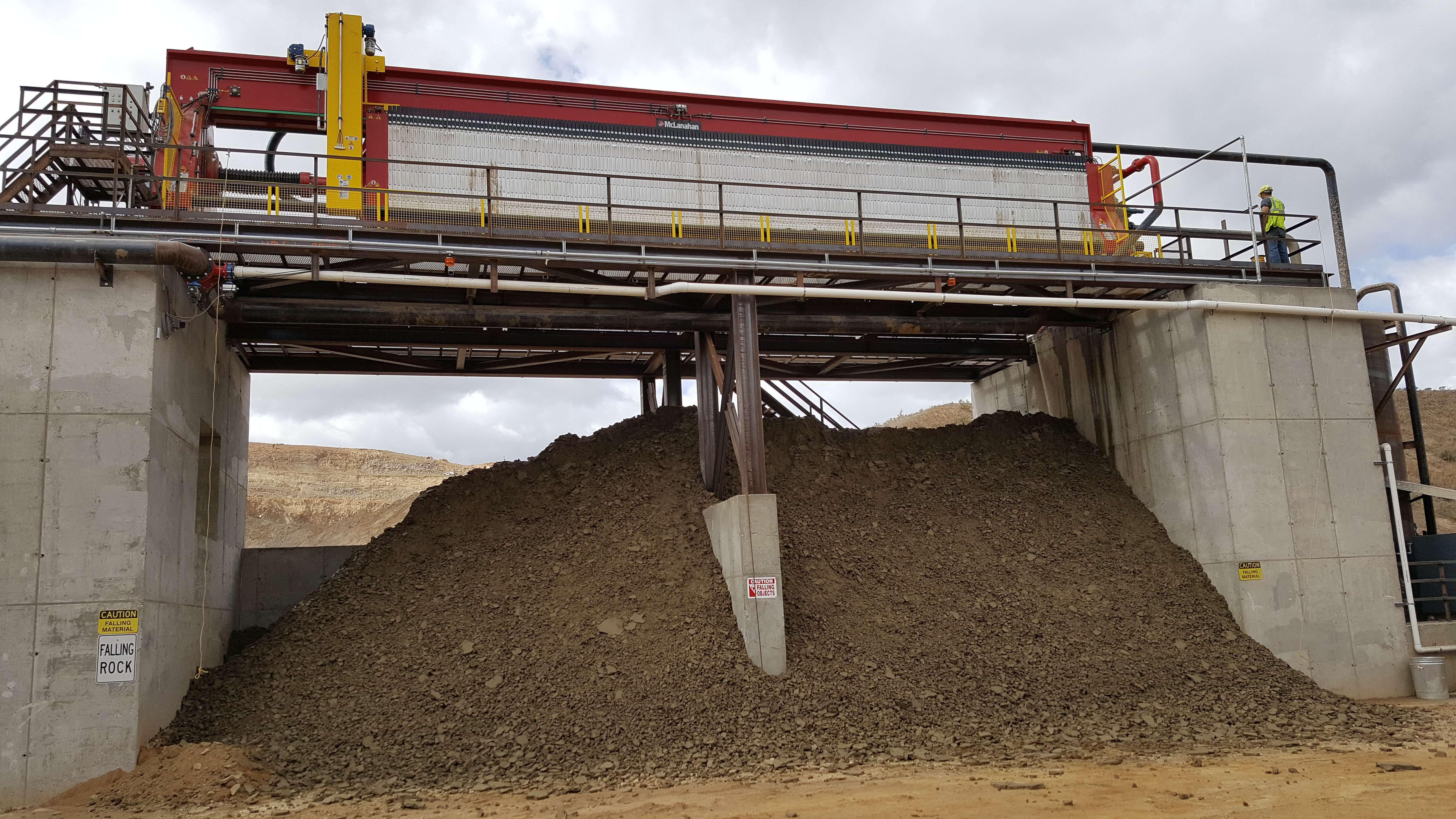
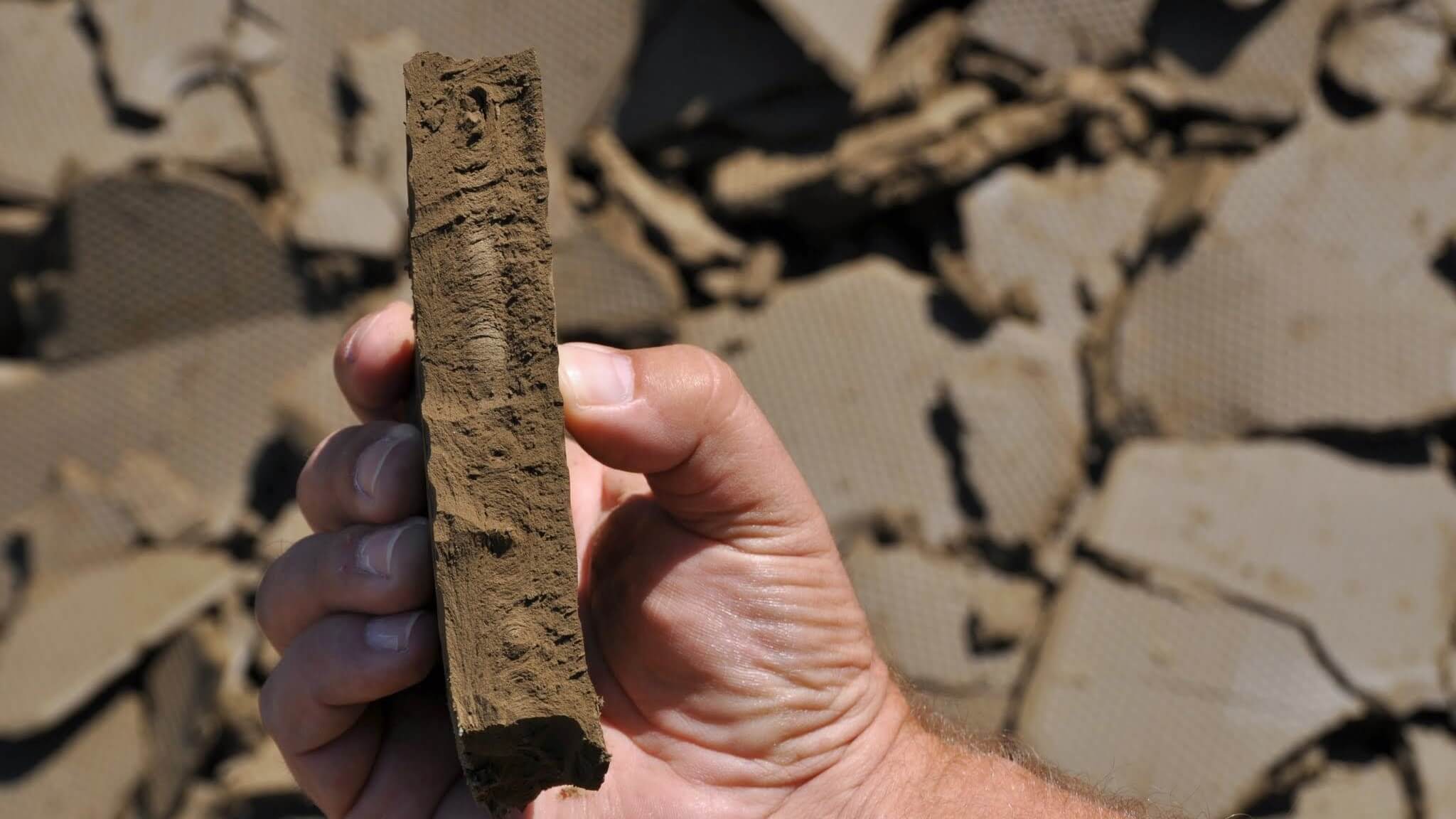
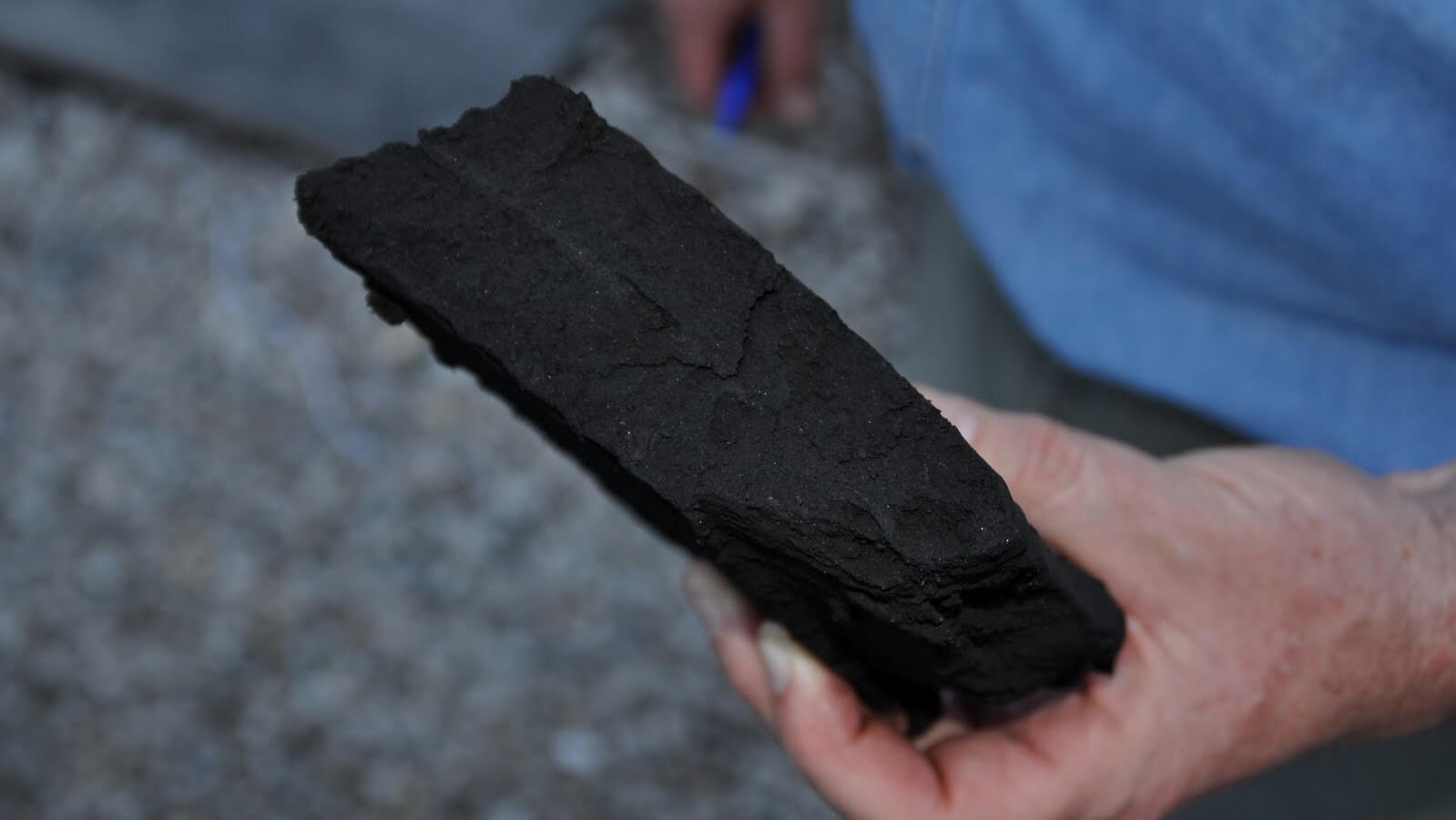
Filter Presses dewater and separate liquids and solids in a slurry by pumping the slurry at high pressure into a series of hydraulically closed recessed plates lined with filter cloths.
Applications
Jump To:
Filter Presses dewater and separate liquids and solids in a wide range of applications. Due to their versatility and reliability, Filter Presses are one of the most widely used pieces of equipment in liquid-solid separation. They dewater material and separate liquids and solids by pumping the slurry into a series of empty chambers that are formed by the plates of the filter press. Each plate is lined with filter media, which determines what particles are dewatered and separated from the liquid.
Applications ideal for Filter Presses include: tailings or effluent from a mine or aggregate wash plant, mineral concentrates and most underflow slurries from industrial, agricultural or mineral processes coming from a Thickener or clarifier process. McLanahan Filter Presses provide customers in many industries with proven technology that is capable of producing a drip-free cake from mining and aggregate tailings, mineral concentrates, and a wide range of waste materials through mechanical dewatering.
A Filter Press is composed of a support structure holding a series of recessed plates lined with filter cloths. Hydraulic pressure is used to hold the recessed plates tightly together, creating a seal around their perimeters and void spaces between the plates. A high-pressure slurry dewatering pump forces slurry into the empty chamber spaces between the plates for dewatering. The slurry solids are captured between the plates, while the clean filtrate water passes through the filter cloth mesh and exits through ports in the filter plates. When the chamber spaces are full of dewatered slurry solids, the slurry feed pump is automatically stopped. The hydraulic pressure holding the plates together is released so the plates can be separated individually, allowing the dewatered solid material cakes to fall by gravity out of the press.
Many people think the filter plates are squeezed together to expel water, but the press never moves during the time of dewatering. The only movements involved occur when the plates separate to expel the dry cakes or close to begin a new process cycle. Plates simply connect to form a seal under hydraulic pressure while the feed pump supplies the necessary pressure to dewater the fine solids.
Filter Presses are designed for simple and limited movement. This design leads to high-levels of automation and reliability. Compared to competing dewatering technologies, higher levels of water removal can be achieved with the Filter Press because the material being dewatered is captured between the recessed plates under the highest possible pump pressures. The Filter Press is also designed for the specific application by selecting the cycle times, cake thickness, feed pressures and plate styles to achieve optimum dewatering efficiencies.
McLanahan Filter Presses are designed to generate easily managed dry product or waste material. The Filter Press also provides the ability to optimize the recovery of clean, reusable water. McLanahan Filter Presses can address many typical issues associated with fine material processing, including full slurry ponds/dams, high material handling equipment repair costs, limited expansion capabilities, environmental permit restrictions, high waste material handling costs and limited water availability.
McLanahan Filter Presses are used by many 24/7 operations that rely on machine performance and excellent support to keep their plants running and profitable.
McLanahan Filter Presses are engineered using a single hydraulic cylinder. This results in robust and reliable automation capabilities with lower horsepower, fewer control valves and less complexity than multi-cylinder designs. McLanahan’s Overhead Beam style results in faster opening and closing for greater production and better cake release in tailings applications. It also provides larger plate openings for better cleaning and maintenance access. McLanahan’s Side Beam style is designed for concentrates and smaller tailings applications while providing fast plate/cloth removal. It is also more transportable for modular or portable applications.
Unlike the traditional plate and frame presses, McLanahan’s Filter Press line features modern recessed plates or membrane plates, both of which create a chamber for dewatering the slurry without trapping the cakes within the frames. This allows the dewatered cakes to discharge more easily than with traditional plate and frame presses.
Due to the variability in permeability and surface area, each site’s material should be tested prior to sizing a Filter Press for a specific customer application. McLanahan offers experienced lab and on-site pilot testing with a wide range of testing capabilities. Other parameters are used for greenfield sites when testing isn’t possible.
McLanahan’s Customer Service Team offers a wide range of fast spare parts sourcing as well as routine and emergency maintenance service support. All McLanahan Filter Presses can have customer remote control access capability for efficient monitoring and troubleshooting.
The main factors impacting Filter Press dewatering efficiency include:
Pump options for Filter Presses include:
Filter Presses and Belt Presses are different in several ways. With Belt Presses, slurry is dewatered between two moving synthetic cloths or belts. Water initially is released by gravity then by squeezing the slurry/belts between rollers. The filtrate water is collected below the press unit in a pit. The dewatered cake material is scraped off the belts as they separate at the discharge end of the press. A dewatering polymer chemical is required to flocculate the slurry particles prior to the slurry entering the press. The chemical also aids in allowing the water to release from the solid material.
A plate Filter Press is composed of a frame holding a series of recessed plates lined with filter cloths. The plates are held tightly together, creating a seal around their perimeters using hydraulic pressure. A high-pressure slurry dewatering pump forces slurry into the chamber spaces between the plates for dewatering. The slurry solids are captured between the plates, while the clean filtrate water passes through the filter cloth mesh and exits through ports in the filter plates. When the chamber spaces are full of dewatered slurry solids, the slurry feed pump is automatically stopped. The hydraulic pressure holding the plates together is released so the plates can be separated individually, allowing the cake to fall by gravity out of the press. Typically, no chemicals are required to aid dewatering on a plate filter press.
Recessed plates are solid plates made of plastic or metal or a combination of metal and plastic. The plates have recessed surfaces, except for the perimeter edge surface that allows the plates to seal against each other when they are clamped together using a hydraulic ram. With the plates held tightly together, all dewatering takes place as a result of the slurry feed pump press.
Membrane plates are similar to recessed plates, having recessed surfaces except for their perimeter edges. The membrane plates are constructed so compressed air or water can be injected inside the plate surface, inflating the plate surfaces. These plates are also held tightly together with a hydraulic ram while the slurry is pumped into the press and dewatered. Once the chambers are filled with dewatered slurry, the feed pump is stopped. With plates still clamped together, the membrane plate surfaces are inflated to compress/squeeze the dewatered cake material. If the material can be compressed, additional water is removed from the solids. The plate surfaces are deflated by relieving the air or water pressure, then the plates are unclamped to allow the plates to be separated and the cakes are discharged by gravity.
Recessed plate Filter Presses require routine filter cloth replacement and slurry feed pump rebuilds. The cloth's life is typically in thousands of press cycles. Pump rebuilds are required due to internal pump wear caused by the slurry material. The rebuild frequency can vary greatly depending on pump materials of construction, slurry material abrasiveness and hours of operation, but in general would occur once to twice per year.
The savings most frequently gained using a Filter Press are:
Filter Presses are often used to create a closed loop process. This eliminates the need for a settling pond or tailings pond, while also recycling process water back for reuse. By eliminating the need for tailings ponds or settling ponds, valuable land reserves can be protected or freed up for mining rather than being covered with tailings.
In many cases, the use of a closed loop process can also reduce regulatory permits while also putting forth an environmentally positive message for investment companies.
Many companies are now waiting years for permits for new settling ponds without assurance that this permit will be approved. Moving to a closed-loop process can eliminate the need for some of these long permitting processes.
Water availability and cost are becoming more of an issue as large population areas continue to grow. These areas also require quarried and mined materials, but lack of water can be restrictive for new plant considerations. Plant feasibility is greatly improved using a closed loop approach to wet processing with a filter press due to the maximum recovery of recyclable water, minimizing the need for new water sourcing.
The most commonly considered options when purchasing a Filter Press are:
The capacity of a Filter Press is determined primarily by the following items:
The number of cycles per hour is dependent on the:
McLanahan Filter Presses produce a drip-free cake and recover immediately reusable process water.