CMB Cone Crushers
A Cone Crusher is a compression type of machine that reduces material by squeezing or compressing the feed material between a moving piece of steel and a stationary piece of steel.
Applications
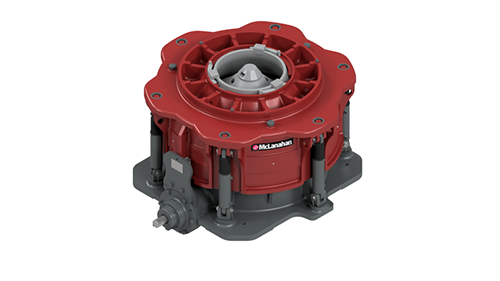
A Cone Crusher is a compression type of machine that reduces material by squeezing or compressing the feed material between a moving piece of steel and a stationary piece of steel.
Applications
Jump To:
Cone Crushers deliver a 4:1 to 6:1 reduction ratio. A Cone Crusher with coarse-style liners would typically have a 6:1 reduction ratio, though reduction ratios of 8:1 may be possible in certain coarse crushing applications. Fine liner configurations typically have reduction ratios of 4:1 to 6:1.
Final sizing and reduction are determined by the closed-side setting or the gap between the two crushing members at the lowest point. As the wedge or eccentric rotates to cause the compression within the chamber, the material gets smaller as it moves down through the wear liners as the opening in the cavity gets tighter. The crushed material is discharged at the bottom of the machine after it passes through the cavity.
The tighter the closed-side setting, the finer the output; however, the volume or throughput capacity will also be reduced. Generally speaking, multiplying the closed-side setting by two is a good guide to the top size of the gradation exiting the machine.
Cone Crushers are ideal for crushing medium to hard materials that are dry or wet but not sticky.
CMB Cone Crushers feature a lower mainframe housing the main shaft, an upper frame supporting a concave bowl assembly and a tapered wedge assembly machined to correspond with the inner tapered surface of the main frame. A drive turns the horizontal countershaft, and a pinion gear on the countershaft rotates the eccentric gear on the main shaft. This causes the wedge assembly to wobble.
Material is choke fed into the top of the bowl assembly to maintain a full crushing chamber. The material is crushed between the wobbling wedge assembly and the concave bowl. Sized material discharges out the bottom of the crusher.
The closed side setting, which determines product size, can be adjusted quickly, easily and while the crusher is in operation. In the event tramp material enters the crushing chamber, a vertical lift raises the upper frame to allow large uncrushable objects to pass freely.
Capacities and product gradations produced by Cone Crushers are affected by the method of feeding, characteristics of the feed material, speed of the machine, power applied and other factors. Hardness, compressive strength, mineral content and other characteristics of the material also affect production capacities and gradations.
Gradations and capacities are most often based on a typical, well-graded choke feed to the crusher. Well-graded feed is considered to be 90-100% passing the closed-side feed opening, 40-60% passing the midpoint of the crushing chamber on the closed side (average of the closed-side feeding opening and the closed-side setting), and 0-10% passing the closed-side setting.
Choke feed is considered to be material located 360 degrees around the crushing head and approximately 6” above the mantle nut. Maximum feed size is the average of the open-side feed opening and the closed-side feed opening.
Minimum closed-side setting may vary depending on crushing conditions, the compressive strength of the material being crushed and stage of reduction.
McLanahan CMB Cone Crushers are modern cast steel, all roller bearing and feature hydraulic adjustment, which enables the operator to rapidly change the discharge setting if required during crusher operation. These machines feature hydraulics that also incorporate a tramp metal release, automatic reset and an unblocking feature, which will clear the crushing chamber in a matter of minutes.
Re-metalling is carried out with the crushing head in situ. The short shaft configuration, which requires no top bearing, enables all major components to be removed from above, and demands minimal head room for installation and maintenance.
The proven all-roller-bearing design provides for lower power consumption, long life, easy spares availability and the need for a more compact lubrication system.
The controls of the CMB Cone Crushers comprise a contactless in-cylinder transducer and an operating console that can be positioned close to the crusher. Quick release, self-sealing couplings are used to connect the twin hydraulic hoses that run between the crusher and console. The console houses the fluid tank, motorized hydraulic pump, valves, PLC instrumentation and push button controls. Remote control operation is available so the crusher can be operated from a control room any reasonable distance away.
Mounted on a modular chassis, the UltraCRUSH is quick to set up and easily moveable from site to site. The UltraCRUSH system features a CMB Cone Crusher, which includes a hydraulic adjustment system that enables producers to rapidly change the discharge setting with little interruption to production. Arriving on site in an almost fully assembled state, the UltraCRUSH system can be up and running in a short amount of time.
For best operating performance, CMB Cone Crushers must be choke fed. Choke feeding ensures the crushing chamber is always full, with material on top of it so the crushing chamber stays full. Crushers that are choke fed produce a more cubical product at higher throughput.
CMB Cone Crusher speed settings are based on the crushing application. Below are suggested speed guidelines for CMB Cone Crushers:
Speed ranges:
To maintain the maximum levels of capacity, gradation and cubical product, a CMB Cone Crusher must be choke fed at all times. The best way to keep a choke feed to the CMB Cone Crusher is with a surge bin or hopper and Feeder that are located prior to the crusher. Choke feeding is almost impossible to achieve without a hopper and Feeder.
There are a number of different criteria to consider when selecting the right chambers for your crushing needs. However, the one that must always be considered is that you have a well-graded feed to the chamber. A well-graded feed is generally though to be 90-100% passing the closed-side feed opening, 40-60% passing the midpoint and 0-10% passing the closed-side setting.
One thing you should never do is place a new concave liner in a crusher with a worn mantle or place a new mantle in a crusher with a concave liner. Why? If you have properly selected the replacement component, you will change the complete profile of the Cone Crusher by mating new and worn components. The receiving opening will tend to close down, restricting the feed from entering the chamber and causing a reduction in tons per hour.
If the liner is wearing evenly throughout the chamber, you should consider changing out the manganese when it has worn down to about 1” (2.5 cm) thick at the bottom. At about ¾” to 5/8” (1.9 cm to 1.6 cm) thick, the manganese will crack, causing the backing material to begin to disintegrate. This, in turn, will cause the liners to break loose. If this should happen, continued operation could destroy the seat on the support bowl or the head of the Cone Crusher.
McLanahan CMB Cone Crushers are ideal for medium to hard materials that are dry or wet.