Attrition Cells/Scrubbers
Attrition Cells/Scrubbers are designed to scrub the surfaces of particulates, liberate deleterious materials and break down pretend particulates associated with durability, such as hard-pan clays.
Applications
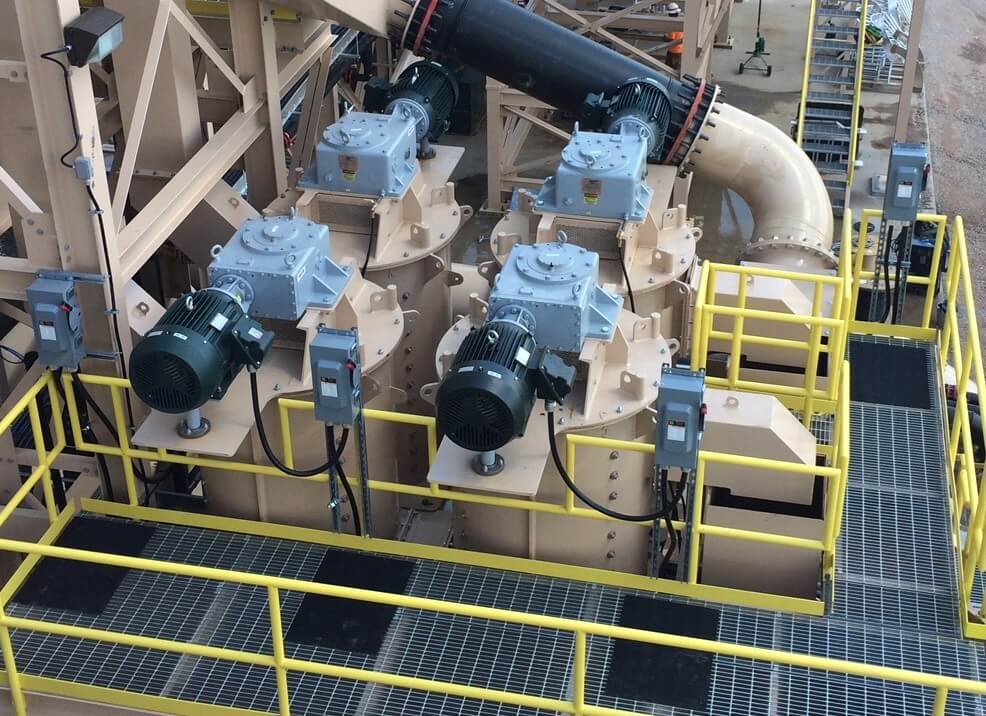
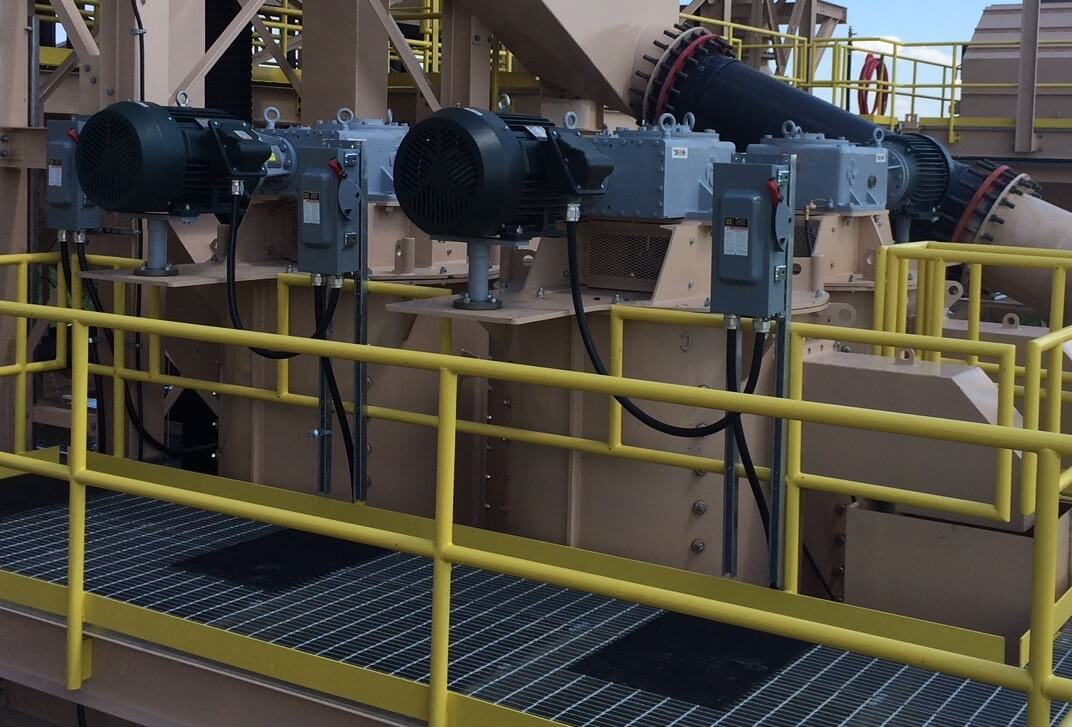
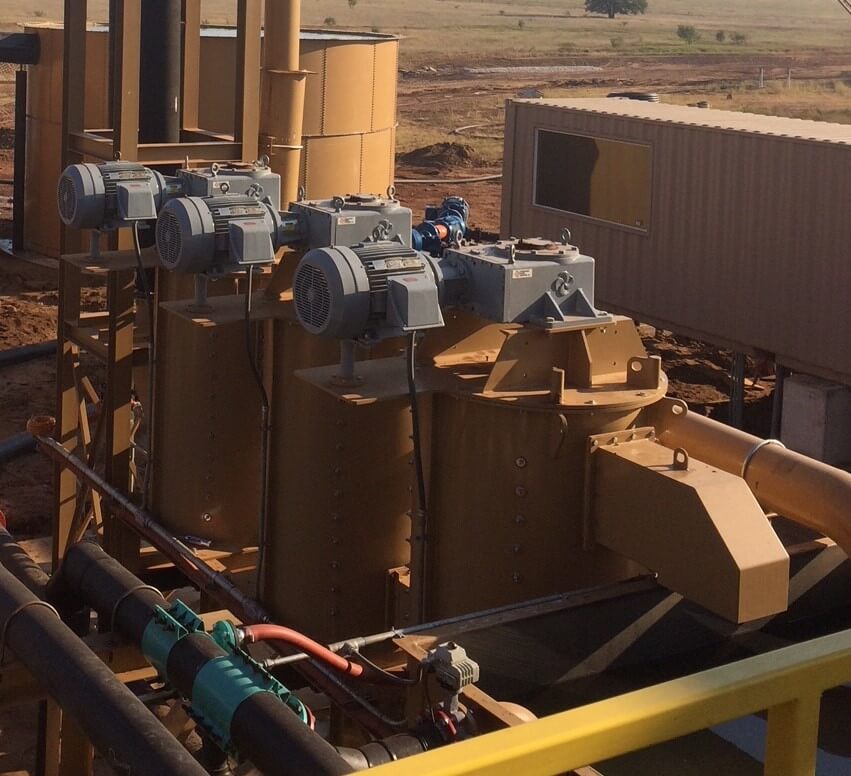
Attrition Cells/Scrubbers are designed to scrub the surfaces of particulates, liberate deleterious materials and break down pretend particulates associated with durability, such as hard-pan clays.
Applications
Jump To:
Attrition Cells/Scrubbers are typically fed by Separators™ to present the material at a high density to achieve the best scrubbing action possible, but also can be fed by Hydrosizers™ or Dewatering Screens. Operating densities vary depending on the application but are typically in the range of 72-75% solids by weight. To maintain correct operating density, dilution water is automatically added at rising power draw. In the event of excessive power draw, the motor shuts off to protect the motor, gearbox and shaft/paddles.
The top size of the feed is typically of up to 1/2” (12 mm). Surface contaminants, such as clays, oxides and chemicals, are removed by particle-on-particle attrition generated by a series of rotating paddles inside the Attrition Cells that have been sized to suit the application.
Attrition Cells/Scrubbers are configured to provide the most efficient performance, producing a high shear environment in which particle-on-particle scrubbing scours the surfaces and liberates deleterious materials. Due to the higher levels of materials passing through the unit too quickly to be fully processed, multiple Attrition Cells/Scrubbers are used in series.
Material enters the Attrition Cell/Scrubber at the bottom and by displacement passes up through the tank, being subject to high velocity axial and radial motion to best provide particle-on-particle scrubbing action. The material overflows the Attrition Cell at the top and passes through to the next cell in the series, where the scrubbing is repeated. A series of weirs is provided to increase or decrease the total volume being processed in an Attrition Cell/Scrubber. Retention time is based on testwork and can vary between one and eight minutes. Greater retention times may end in diminishing returns for the energy consumed and capital investment.
In cases of severe contamination, interstage washing is used. In this type of application, the materials can be diluted and processed through a pump and Separator™ or other methods, and are then directed to the next stage for further attritioning.
The most commonly used Attrition Cell/Scrubber is a 1.7 m3 unit with multiple units in series. These can be round, square or octagonal. Larger Attrition Cells/Scrubbers are available; however, multiple smaller units are preferred due to their efficiency.
Attrition Cells/Scrubbers are ideal for industrial sand (frac sand, glass sand, sports sand, etc.) and mineral sands to meet turbidity and color test requirements. They can be used in the production of iron ore, clay, and sand and gravel, as well as in the preparation of flotation feeds and reagent washing. They also allow more efficient downstream separation, such as in flotation and electrostatic/electromagnetic separation.
McLanahan Attrition Cells/Scrubbers are designed to be robust. They feature heavy-duty direct-drive gearboxes that eliminate the slip often associated with V-belt driven units. They also feature field-replaceable rubber liners, shaft protection and individually replaceable paddles for longer wear life and reduced maintenance downtime.
McLanahan's in-house Applications Research Laboratory performs lab-scale testing of sample material to evaluate the most appropriate process for an application, whether it's surface contamination or durability issues, as well as to determine the effectiveness of that process. This ensures the right size and quantity of Attrition Cells/Scrubbers are selected to achieve the most efficient operating configuration in the field. McLanahan offers multiple configurations of Attrition Cells, including a variety of sizes and shapes, as well as unique adjustable internal geometry to provide maximum scrubbing and increase the quality of the final product.
McLanahan has more than 30 years of experience with Attrition Cells/Scrubbers and many units installed in a variety of applications. Our experienced geological and process engineering staff can assist with your application needs to ensure efficiency and profitable production.
The typical retention time for clay removal using an Attrition Cell/Scrubber is between two and five minutes, but specifications and individual requirements vary. The only way to determine how long the retention time needs to be is to test the materials.
Particle shape, size and mineralogy affect the wear life of Attrition Cells/Scrubbers, and sometimes materials of construction have to vary to suit the application. No manufacturer can guarantee wear life, but advanced knowledge of the materials being processed can help with the selection of wear materials and thicknesses to help maximise wear life.
In certain applications it is necessary to add chemicals to the Attrition Cell/Scrubber feed to improve the performance of the attrition process. Certain materials of construction are adversely affected by different chemistries, so it is important to consult the manufacturer before purchase and/or before the use of additional chemicals.
McLanahan does not employ the use of side access to Attrition Cells/Scrubbers for safety reasons. As work components often have sharp edges, reaching inside the vessel and indexing the shaft rotation can lead to uncontrolled exposure to sharp surfaces and accidental engagement. Extraction of the shaft assembly allows more controlled and more complete access to the assembly to evaluate any wear or damage. This allows the maintenance crew to remove/replace worn components with the greatest level of safety. Inspection of internal surfaces can also be carried out with the shaft assembly removed.
McLanahan Attrition Cells/Scrubbers can handle high plasticity clays in high shear and aggressive scrubbing environments.