Since the mid-1960s, this mine in Vernal, Utah has been producing phosphate for agriculture fertilizer. In 2003, the J.R. Simplot Company became sole owner of the property and formed Simplot Phosphates, LLC. The three key ingredients used in the production of this fertilizer are ammonia, sulfur and phosphate ore.
CHALLENGE
Company officials at the site had been struggling with issues regarding their ore crushing system for more than a decade. Their existing crusher crushed slabs of phosphate ore into inconsistently sized pieces that would often trip and cause delays on conveyor belts. Some of the harder ore couldn’t be crushed with the existing machine and had to be set aside. Additionally, as the site’s face moved, haul distances increased, meaning higher fuel usage and greater wear and tear on the trucks.
However, none of this was as time-consuming or frustrating as the daily need to maintain their existing feeder-breaker by replacing picks on the pick roll. Every day, one of the workers had to climb inside and replace whatever picks had been damaged, a process that rarely took less than an hour.
In addition to the time-consuming repairs on the interior pick rolls, the feeder-breaker was inefficient in consistently crushing material to the needed size, resulting in oversized material and causing belt trips along the two-mile conveyor system. Simplot also had power constraints that limited the site to 600 HP for the system.
“The feeder-breaker we had was highly inefficient and high-maintenance,” said Delrie Gale, Simplot Maintenance Supervisor. “The operation would have to slow down, and it was tough to stockpile enough inventory to keep up.”
Simplot officials knew they had to make a change. In early 2011, they called on McLanahan to work with them on a solution. McLanahan Regional Sales Manager Jeff McGovern studied the problem and worked extensively with Simplot officials about changing the crushing system.
“The problem is that feeder-breakers only crush in one dimension and that created some problems on their 42” (106.7 cm) wide conveyance system,” McGovern said. “Our solution would have to address their needs, work within their energy requirements and meet their budget.”
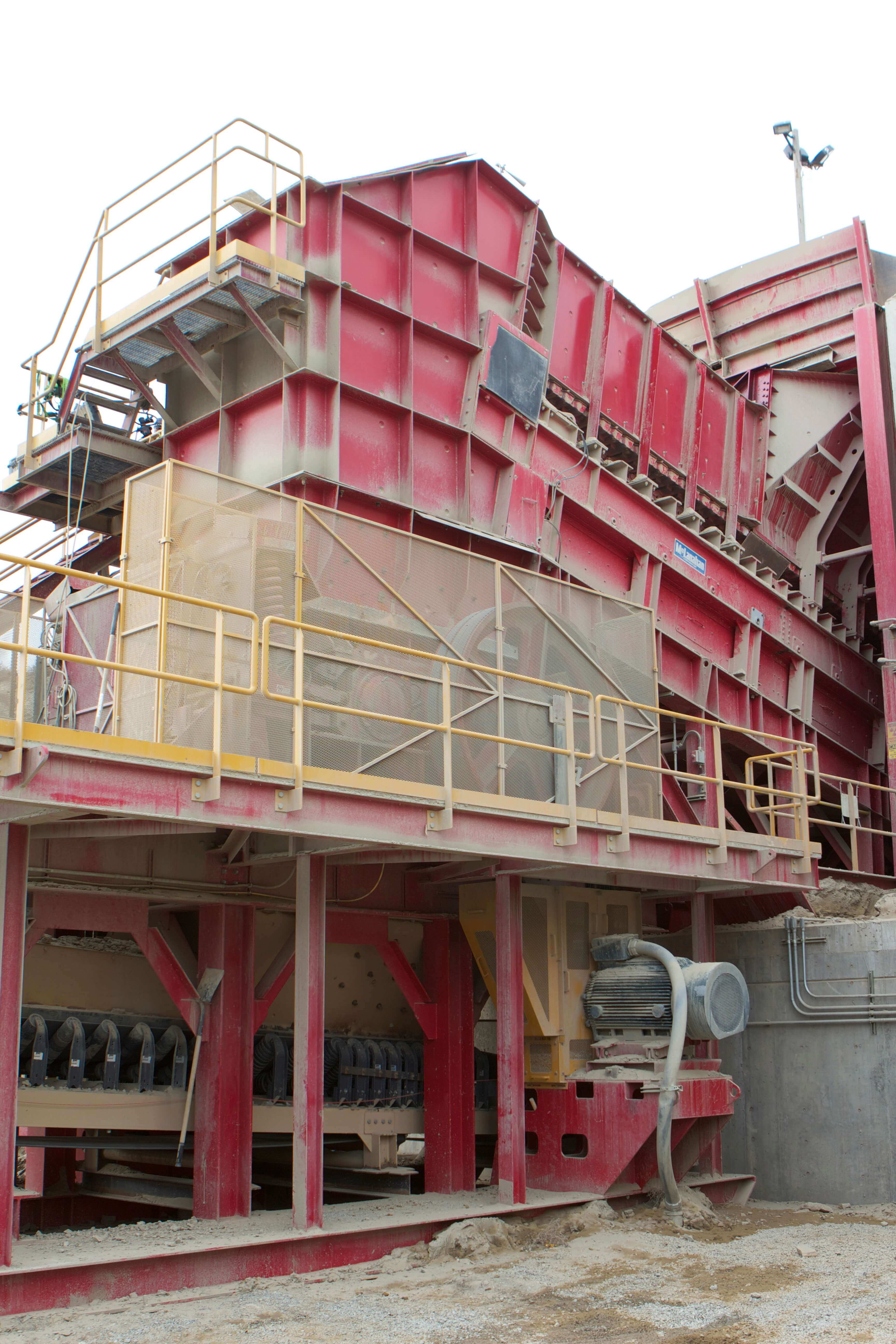
SOLUTION
After research and discussions with Simplot personnel, McLanahan’s proposed a 72” (182.9 cm) wide x 45” (114.3 cm) long Apron Feeder that fed into a hybrid 48” (121.9 cm) diameter x 72” (182.9 cm) long Heavy-Duty Double Roll Crusher.
This custom-engineered system incorporated the design features of a Sizer along with the drive configuration of a Heavy-Duty Double Roll, ultimately saving 465 HP to accommodate the limited power supply.
“We were trying to find a solution that would size the ore better, work with their operation and not trip the system,” McGovern said. “After reviewing the application, we found the right machines to get the job done in the parameters we had to follow.”
The skid-mounted design would also allow the crushing system to move with the face, decreasing haul times and distances. Best of all, the entire system would come in on time and under budget. In the fall of 2011, the system was installed and was commissioned for use in February 2012.
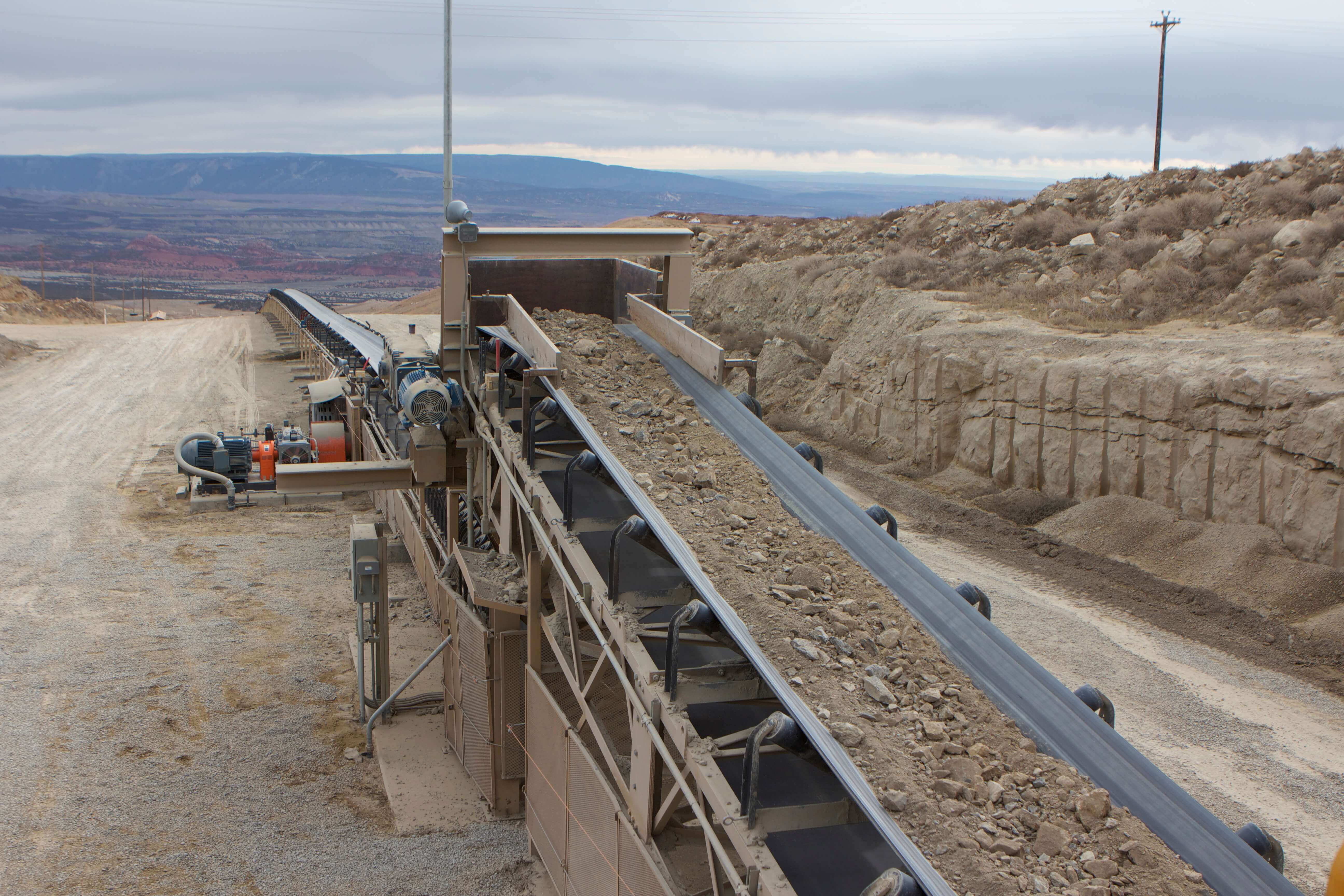
RESULTS
Since its start-up, the crushing station has resulted in savings in energy use and less wear and tear on the machines. The smaller, more consistent product allows Simplot to crush more ore in fewer work days.
The system crushes the phosphate ore into a more cubical-shaped product – a consistent 8” (20.3 cm) in size. This was in contrast to the old system, which had a 10” (25.4 cm) range, but created slabs that got caught in the system, requiring shutdowns. This more consistent feed from the McLanahan crushing station to the conveyor for further processing in a sag mill has cut down on the belt trips and downtime that occurred while the slabs were removed.
“With the help of McLanahan, our problem has been solved,” Gale said. “We get a smoother, even-flow material going down the conveyor belt. The mill gets a smaller material to deal with and it goes through our facility a lot quicker.”
Simplot has also been able to reduce the crushing schedule from 14 days to 12 days with no loss in productivity. The company uses the two days off as energy-saving days – lowering costs, slashing power usage, and saving on wear and tear.
There is also much less maintenance required with the new system, as the system only needs to be checked two or three times a week rather than every day. Gale said Simplot has seen a large decrease in time spent on maintenance.
“As far as man-hours, we changed picks every day, seven days a week,” Gale said. “We had to get down into the crusher every day for sometimes hours at a time. No one misses that.”
Today, Simplot officials are happy with the results of their new system. The operation is maintaining their output goals while running 12 days instead of 14.
Gale said that working with McLanahan on an ongoing basis helps the operation better anticipate and head off any potential challenges that inevitably arise at a mining site.
“With McLanahan’s help, we are continually improving how the system works, making it a better machine, more refined,” Gale said. “More consistent product flows down the conveyor belt and we’re seeing it in our mill”.
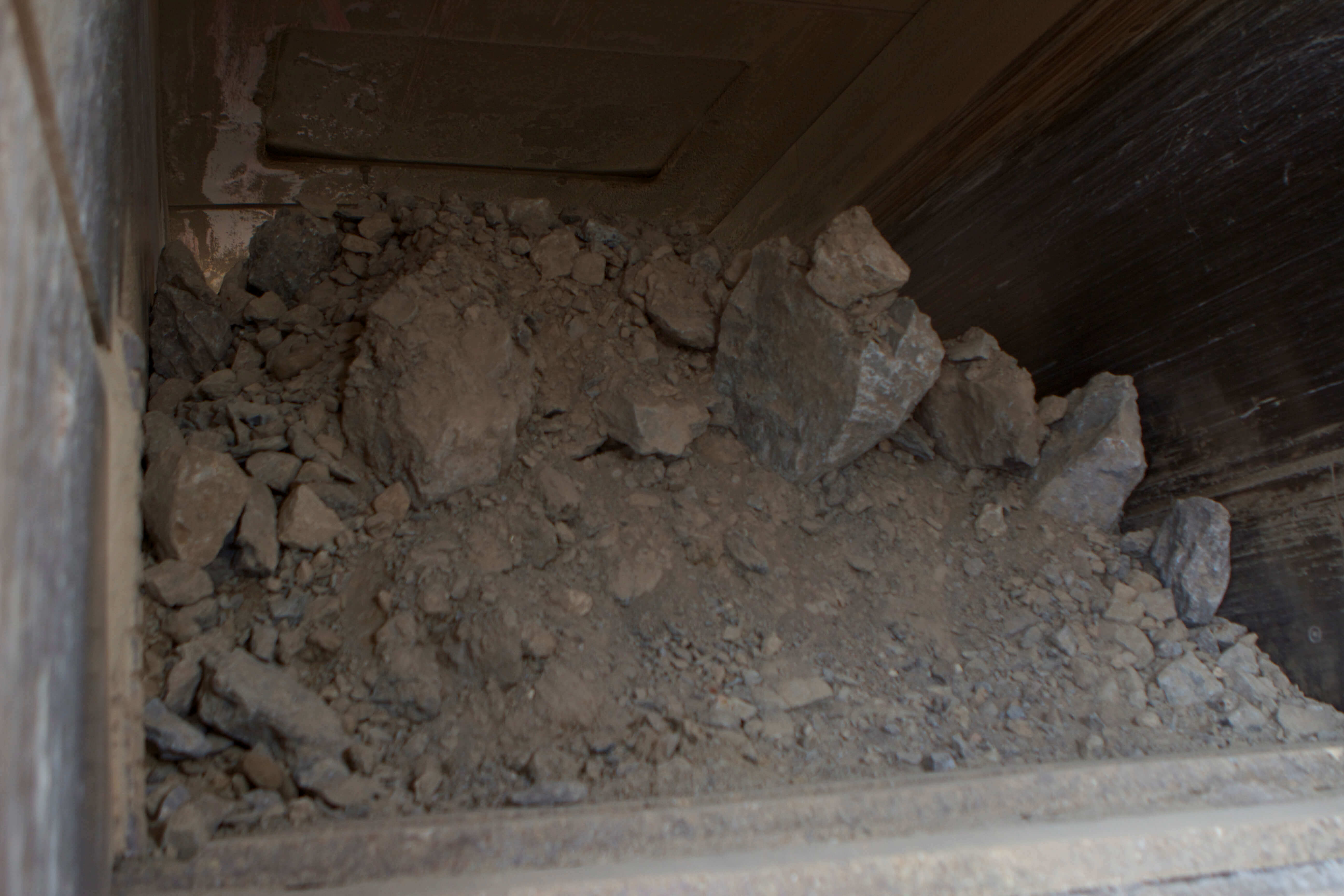