Kraemer Mining and Materials, Inc. has been supplying quality aggregate products in and around the Twin Cities metropolitan area since 1959. Based in Burnsville, Minn., Kraemer operates a limestone quarry that was opened to develop Interstate 35W decades ago. Today, the company produces approximately 1.5 million tons of aggregates per year for commercial, residential and municipal projects.
CHALLENGE
To maximize production, Kraemer added a McLanahan Two-Stage Ultra Sand Plant to operate alongside their existing wash plant in 2017. The Ultra Sand Plant provided a double wash of the sand material, allowing it to first pass through a Hydrocyclone to remove unwanted material and then through a Separator™ (which is a vacuum assisted cyclone) for an additional wash before being dewatered with a Dewatering Screen for stockpiling.
“One of our biggest customers in the blacktop industry needs a very clean sand product,” explained Quarry Superintendent Mike Hoffman.
Kraemer’s material has a high amount of minus 200 mesh fines, and they needed to remove those fines to achieve the desired product spec.
“The McLanahan Ultra Sand Plant was able to process our material and get us to the numbers that we needed to satisfy our customer, Hoffman said.”
The McLanahan Ultra Sand Plant allowed Kraemer to double their production. However, the boost in production meant an increase in the minus 200 mesh material reporting to their settling ponds. They needed to find a way to reduce the footprint of their pond and to reduce the maintenance involved with the now-more-frequent pond cleanouts.
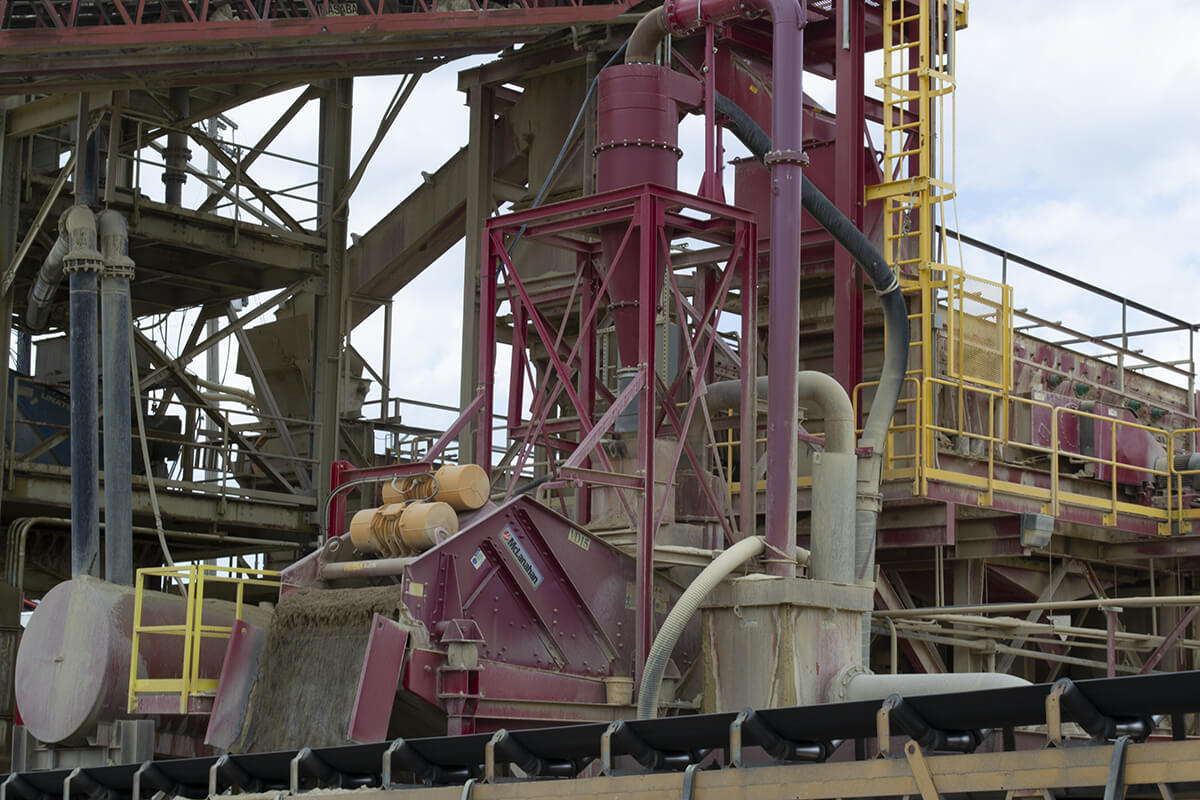
SOLUTION
McLanahan supplied an Ultra Fines Recovery (UFR) System to remove the ultra-fine material from the wash plants’ waste streams ahead of Kraemer’s settling pond. The system consists of a 7,000-gallon Sump, 12x10 Pump with 300 horsepower motor, six 15” Hydrocyclones with 10-degree cones and a Dewatering Screen capable of dewatering the captured material to a drip-free product.
The UFR’s Sump accepts all effluent streams from the plant via three individual slurry lines, which enter the sump and hit a dispersion plate to release any air bubbles. The waste slurry is then pumped up to a bank of Hydrocyclones, which remove the plus 400 mesh material and discharge it onto the Dewatering Screen. The Dewatering Screen removes excess moisture in the material, discharging a drip-free material that is conveyable, stackable and, in Kraemer’s case, saleable; Kraemer is able to sell the recovered material as an agricultural lime or animal bedding.
Fine material that passes through the Dewatering Screen with the water is returned to the Sump to mix with the incoming feed. The overflow from the Hydrocyclones containing the process liquid and minus 400 mesh material gravity flows to the existing tailings pond.
The UFR System package also contained access stairs, walkways, handrails and kickplates for inspection and maintenance activities.
Hoffman said the installation of the UFR was straightforward, as it was “very user-friendly to put together” and that “the team at McLanahan was always there for support”.
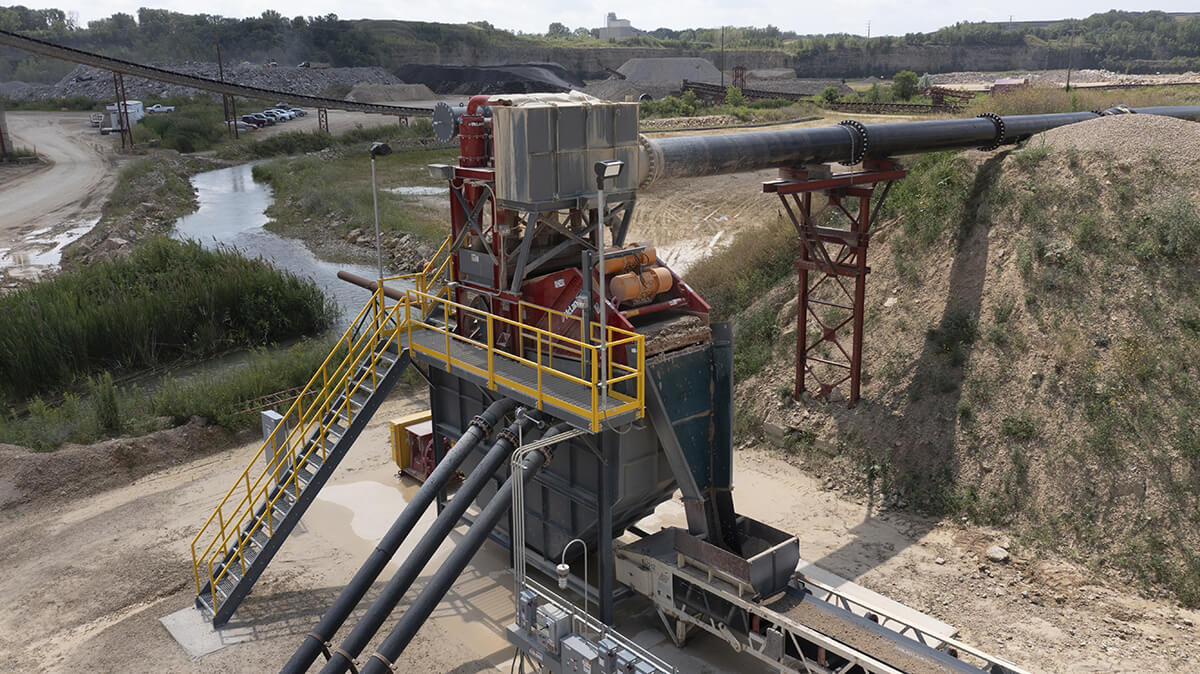
RESULTS
Since installing the McLanahan UFR, Kraemer has indeed reduced the footprint of their settling pond by lessening the amount of solids reporting to the pond.
“The UFR was able to capture material so that our pond did not fill up as frequently as it did in the past, so we don’t have to spend time and money to capture that material back out of it,” said Hoffman.
Kraemer used to recover the material from their settling pond to sell as a byproduct, but it was a lengthy and involved process to do so. With the UFR, it is much simpler to create this agricultural lime material.
“In the past, we would recover the material out of the pond, but we would excavate it, haul it with haul trucks, let it dry, then we would haul it again, then we would screen it, then we would sell it,” Hoffman explained. “Now, we’ve skipped four of those processes.”
The UFR allows Kraemer to recover the material they sell as animal bedding and dewater it for stockpiling – all in one machine.
“Every year, we either had lifts or cleanouts or routine maintenance that was time and cost,” said Hoffman. “We have very minimal pond cleaning now, so it’s a big money-saver for us also. The McLanahan UFR has definitely simplified our waste handling and management.”
In terms of operation and upkeep, Hoffman said the UFR is easy to use and fairly simple to maintain.
“All in all, it’s the Cadillac of the industry,” Hoffman said.