In 2008, Dutch Made Holsteins dairy owner Martin Vanderstappen expanded his operation, adding a new barn and parlor. He now oversees more than 450 cows, each producing about 95 pounds of milk per day on the Lake Geneva, Wis. property.
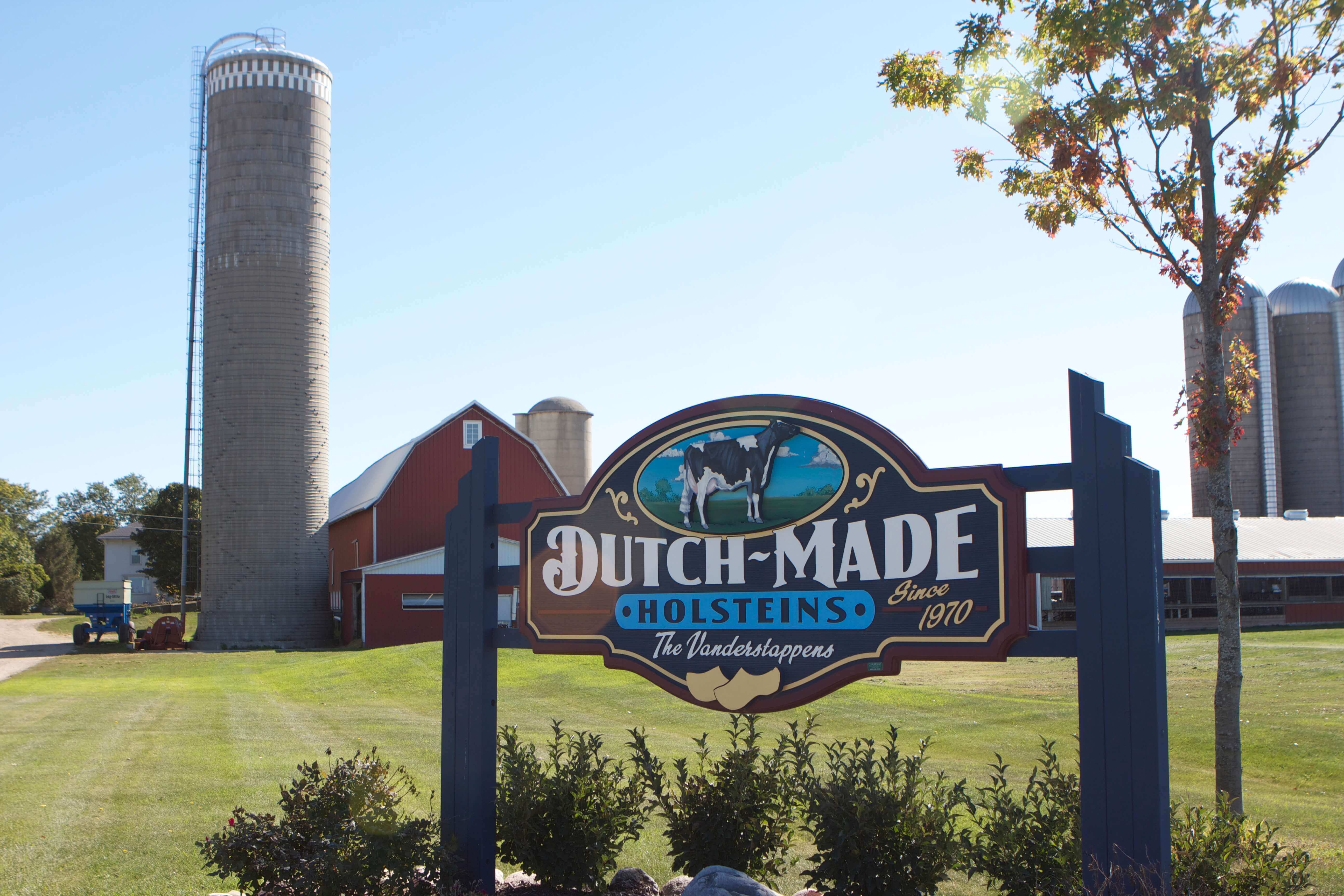
CHALLENGE
With the expansion came more cows – and more manure. Local and federal laws required Dutch Made Holsteins to have a manure management plan in place if it wanted to move forward with the expansion.
This requirement was complicated by Vanderstappen’s decision in 2008 to switch from rubber-mattress cow bedding to sand. “We heard the benefits of sand bedding from the dairy community and our vets,” said Vanderstappen. “Sand has great drainage, reduces slippage, and it’s very comfortable for the cows.”
Unfortunately, sand also caused problems when it came to getting rid of manure. “Moving to sand was a benefit to our facility, but we couldn’t successfully remove the majority of sand from the manure, which created significant wear on our equipment,” he said.
Vanderstappen’s manure-management plan used a low-dilution scrape system to move sand-laden manure from the barn to a waste-management building. Three times a day, a Dutch Made employee scraped the manure from the barn alleys into a transfer channel. The system then scraped the manure into a settling pond where the solids and liquids were separated. The liquids were removed from the pond via pumps and a hydraulic piston pump, while the solids were scooped out with a wheel loader or skid steer.
The process worked well until Vanderstappen learned firsthand the challenges of sand-laden manure. The sand’s abrasiveness caused increased wear on Dutch Made equipment, from hoses to the hammerhead paddles on their manure spreading equipment.
The sand-laden manure also added weight to the tankers and other equipment. This caused a safety issue when transporting manure on or off the property. Vanderstappen estimates the dairy went through two truckloads of new sand a week, as most of the sand was being lost in the fields.
SOLUTION
To combat these problems, Dutch Made turned to McLanahan Corporation and its local dealer, Foxland Harvestore. “We started looking into sand-separation systems in 2010,” Vanderstappen said. “Our requirements for the system were for it to be safe, easy to operate and manage, and for it to have longevity.”
To accomplish these goals, McLanahan and Foxland Harvestore engineered a closed-loop sand separation system for Dutch Made. This system utilizes recycled water produced from a rotary drum separator to provide the necessary dilution water needed for consistent sand separation.
Sand-laden manure is pumped from the reception tank using an existing hydraulic piston pump to a McLanahan Sand-Manure Separator. The Sand-Manure Separator has an inclined auger that turns slowly, along with nozzles to spray water to rinse the manure from the sand.
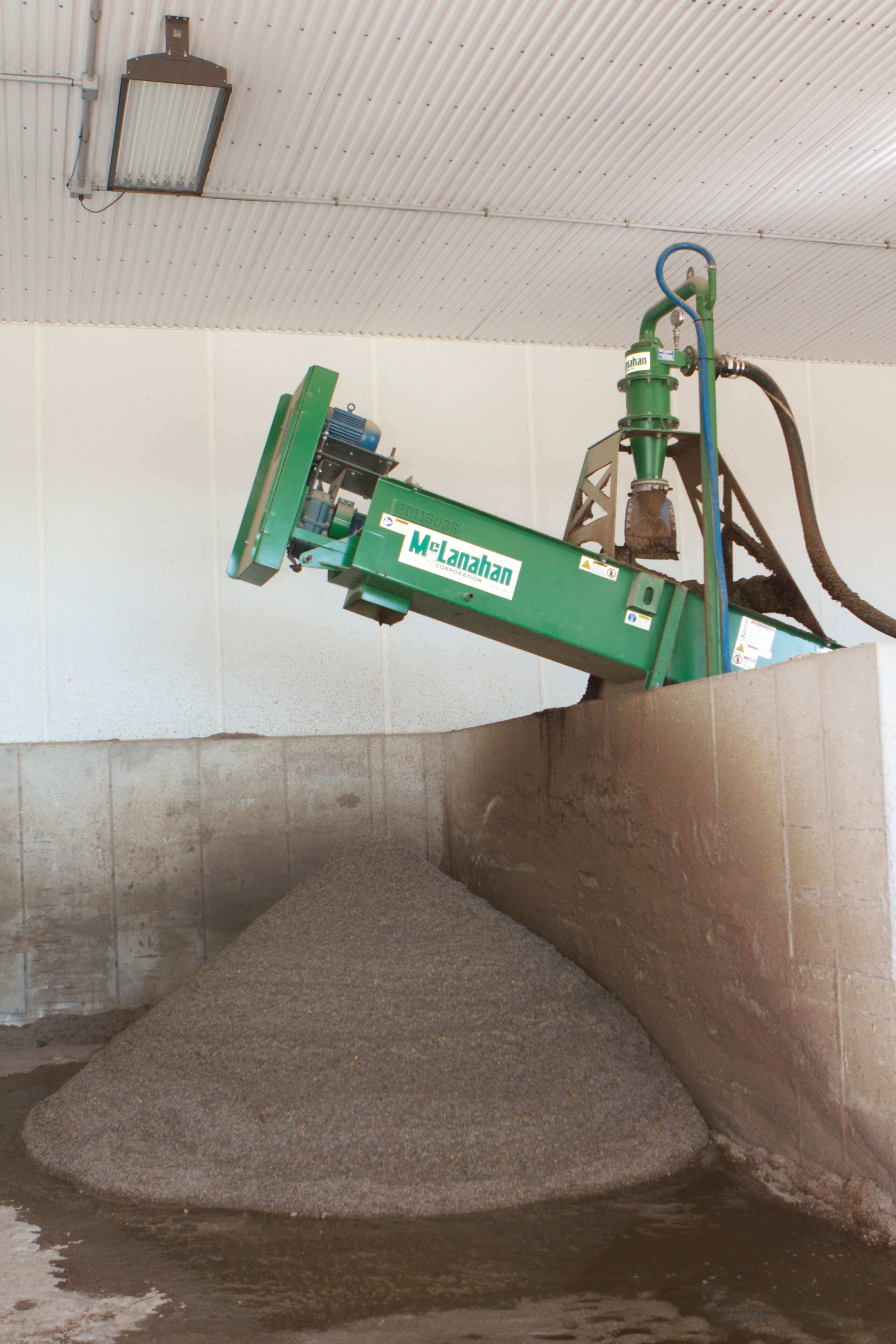
RESULTS
Since the system’s installation, Dutch-Made spends less time managing the sand-laden manure, reducing equipment costs. “We’ve seen a number of benefits since implementing the new system,” said Vanderstappen. “We now recycle up to 95 percent of the sand, reducing the need for new sand. We’re also seeing much less wear and tear on our equipment.”
“The new process is also safer. There’s now less chance of injury because the tankers are not overweight with sand-laden manure, and we’re not struggling with clogged hoses,” he said.
Vanderstappen also likes the cost savings he attributes to the separation system, as they are using less commercial fertilizer.
“With our expansion came a new farm-management plan that included soil testing. We work with the Natural Resources Conservation Service (NRCS) to monitor our soil nitrogen. So far, we’ve seen excellent results applying the processed manure in our fields, which lets us use very little commercial fertilizer.”
Uptime is critical on Vanderstappen’s farm, and the McLanahan system delivers. The system is built with heavy-duty components and engineered with larger tolerances, allowing for less wear during operation and longer up-time. “We’ve had no issues so far, and since the local dealer is about four hours away, we really can’t afford to be down for extended periods,” Vanderstappen said.
With the success of the sand-separation system, Dutch Made is poised to expand further. “Now that we have a reliable and efficient way to manage the manure, we’re planning for our next expansion,” he said.
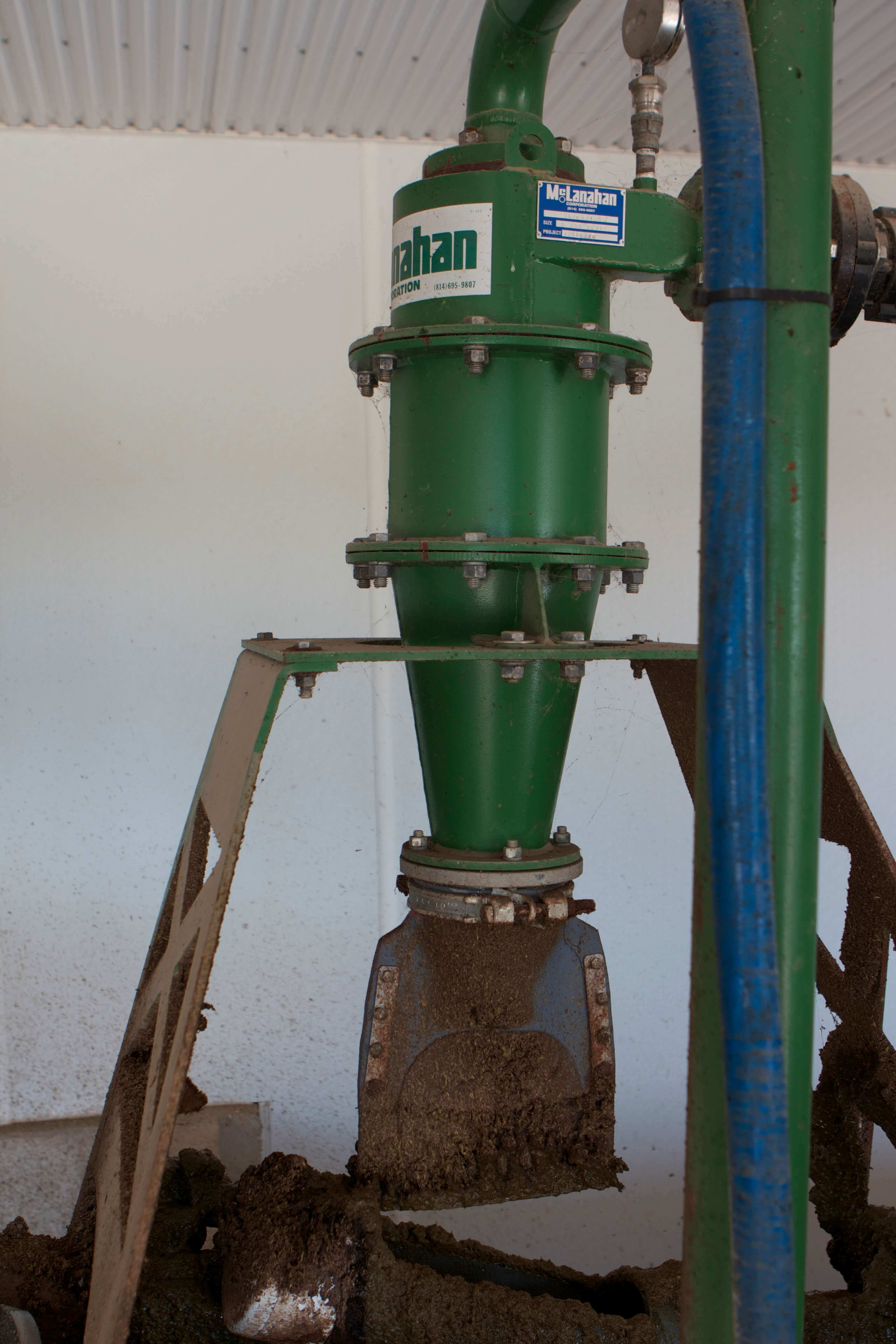