The College of Veterinary Medicine at Cornell University in Ithaca, N.Y., has been creating educational opportunities for students, visitors, community members and farmers since 1894. Their Teaching Dairy Barn, home to 150 milking cows and about 20 dry cows and pre-weaned calves, allows the veterinary students to learn about dairy cows, herd health, calf health, mastitis, milk production and more, and is a place to showcase best practices for dairy management.
CHALLENGE
For years, the Teaching Dairy’s manure management practices included land applying the sand-laden manure from the barn to Cornell’s commodity crops, but when the university stopped growing their commodity crops, they no longer needed the manure for fertilizer.
“We needed to implement another approach for managing our manure,” Jennette explained.
The Teaching Dairy Barn considered many options for manure disposal and sand reclamation, including switching to organic bedding material, hauling the manure elsewhere and growing commodity crops themselves. However, since their main mission is to teach veterinarians and demonstrate the best practices for cow health, they decided to stick with sand bedding and find a more sustainable way to dispose of their sand-laden manure. This led them to the McLanahan SMS12 System.
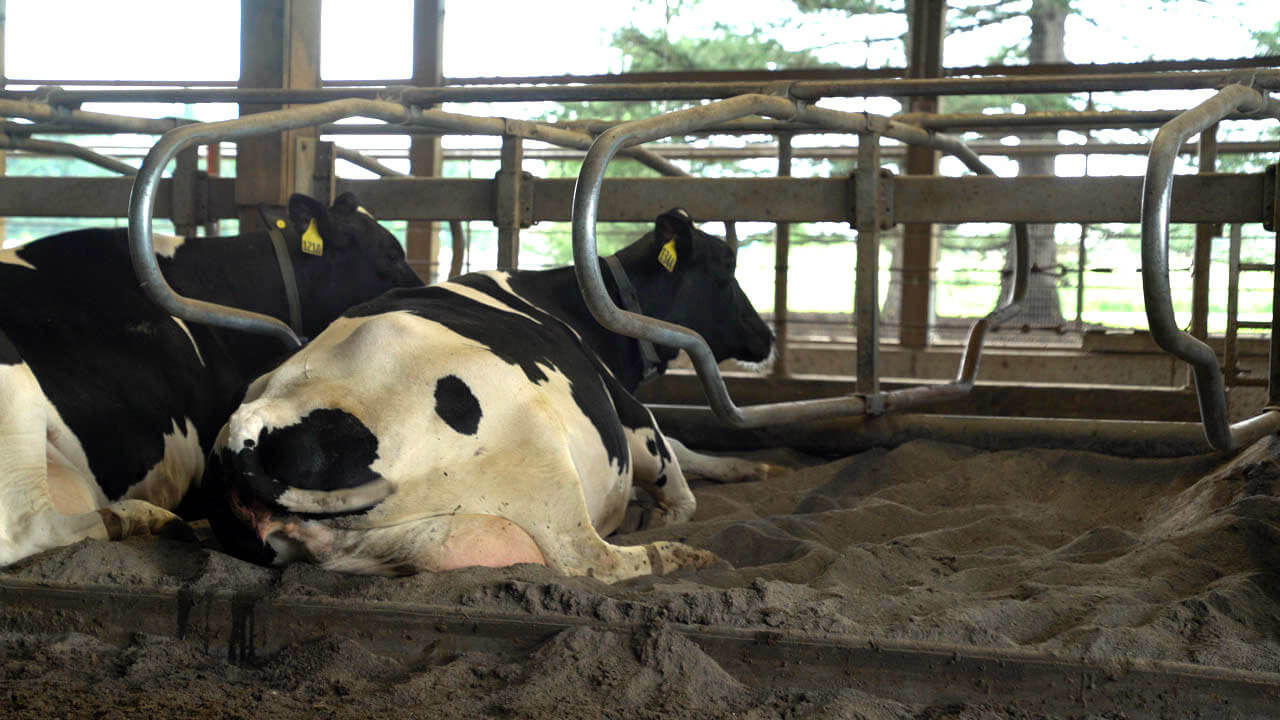
SOLUTION
“When we decided that we were going to manage the manure ourselves at this facility and look at sand separation, we basically went out to the industry and did a quick survey of what farms in the area were doing,” Jennette said. “We found that the farmers in the area had good success with McLanahan.”
The Teaching Dairy contacted McLanahan and explained their need for a sustainable way to separate their sand-laden manure. McLanahan worked with staff in the Teaching Dairy Barn to design the SMS12 sand recycling system, a sand separation system ideally suited for smaller herds like the Teaching Dairy’s.
“I really have appreciated the working relationship we’ve developed with McLanahan over the development of the SMS12 System,” Jennette said. “The people that we’ve interfaced with have all been professional and good folks to work with that, most importantly, have worked with us. They worked with us to adapt their equipment to our needs so that we came up with a system that works really well for us.”
The SMS12 separates the sand from the manure so that it can be recycled. Sand-laden manure from the alleys is scraped into a reception pit, where it is pumped into a conditioning box and diluted. The diluted manure flows into a Rotary Drum, which removes the manure fibers from the liquid and sand and sends them to a storage pit. The liquid and sand are pumped from the Rotary Drum to a Hydrocyclone, which separates the sand from the liquid. The sand exits out the bottom of the Hydrocyclone into a Sand Washer. The sand is rinsed as it travels from the washer box up an auger to discharge onto a Dewatering Screen. The Dewatering Screen removes the excess moisture from the sand and discharges the dewatered, drip-free sand into a storage area.
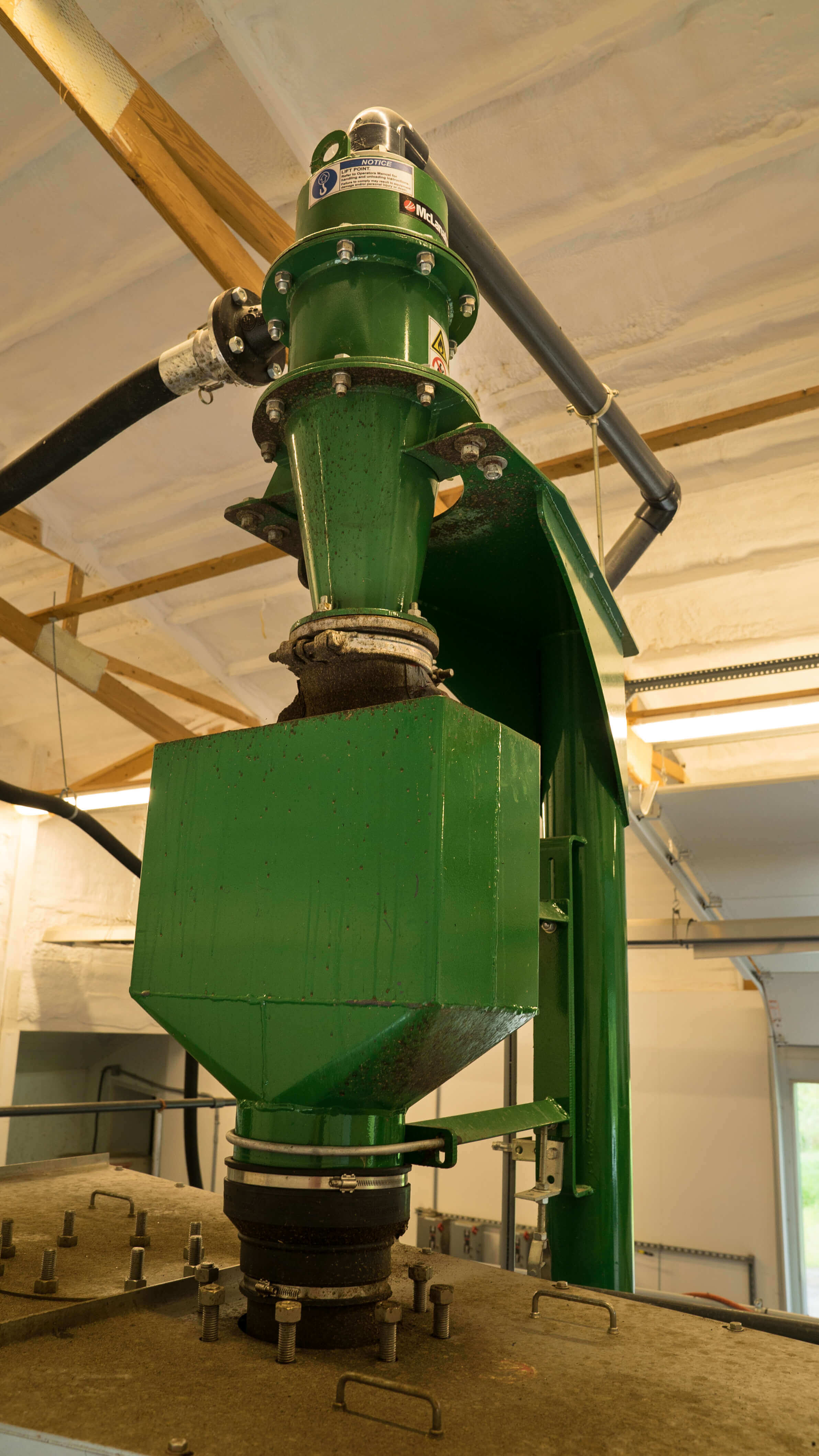
RESULTS
Since implementing the SMS12 System, the Teaching Dairy has exceeded their initial sand separation goals.
“One of the nice surprises we’ve had is how well it does the sand separation for us,” Jennette said. “Our initial estimate was a target goal of a 90% sand separation rate, and our long-term average is now somewhere in the 93% range. We consistently have weeks where we’re looking at 97% plus in terms of sand separation, which is huge.”
They’ve also saved thousands of dollars in purchasing new sand.
“Before we implemented the SMS12, we were trucking about 30 tons a week of sand into this facility,” explained Jennette. “We’re not trucking any sand into this facility anymore.”
Because their sand recovery rate is so high, Jennette said they’ll only have to buy a few tons of sand every now and again.
Besides saving the dairy money, the SMS12 helps the Teaching Dairy Barn and Cornell in sustainability efforts.
“I think one of the benefits of installing the McLanahan SMS12 System for us was that it enables us to do something much more environmentally sustainable, not only in terms of operating the dairy barn and reusing the sand, but also disposing of the manure itself,” said Jennette.
The sand-free manure effluent is hauled to the Ithaca Area Wastewater Treatment Facility, and methane gas generated from the manure in the facility’s anaerobic digester produces electricity and heat.
“The SMS12 is a huge benefit to us on the environmental sustainability side,” Jennette said.
He added that the SMS12 has helped their dairy in multiple ways, but most importantly, it has made them self-sufficient.
“We’re not as dependent anymore on outside entities to take care of the manure in terms of hauling it to somewhere else, spreading it somewhere else,” said Jennette. “We’re taking care of our manure management needs here on-site.”
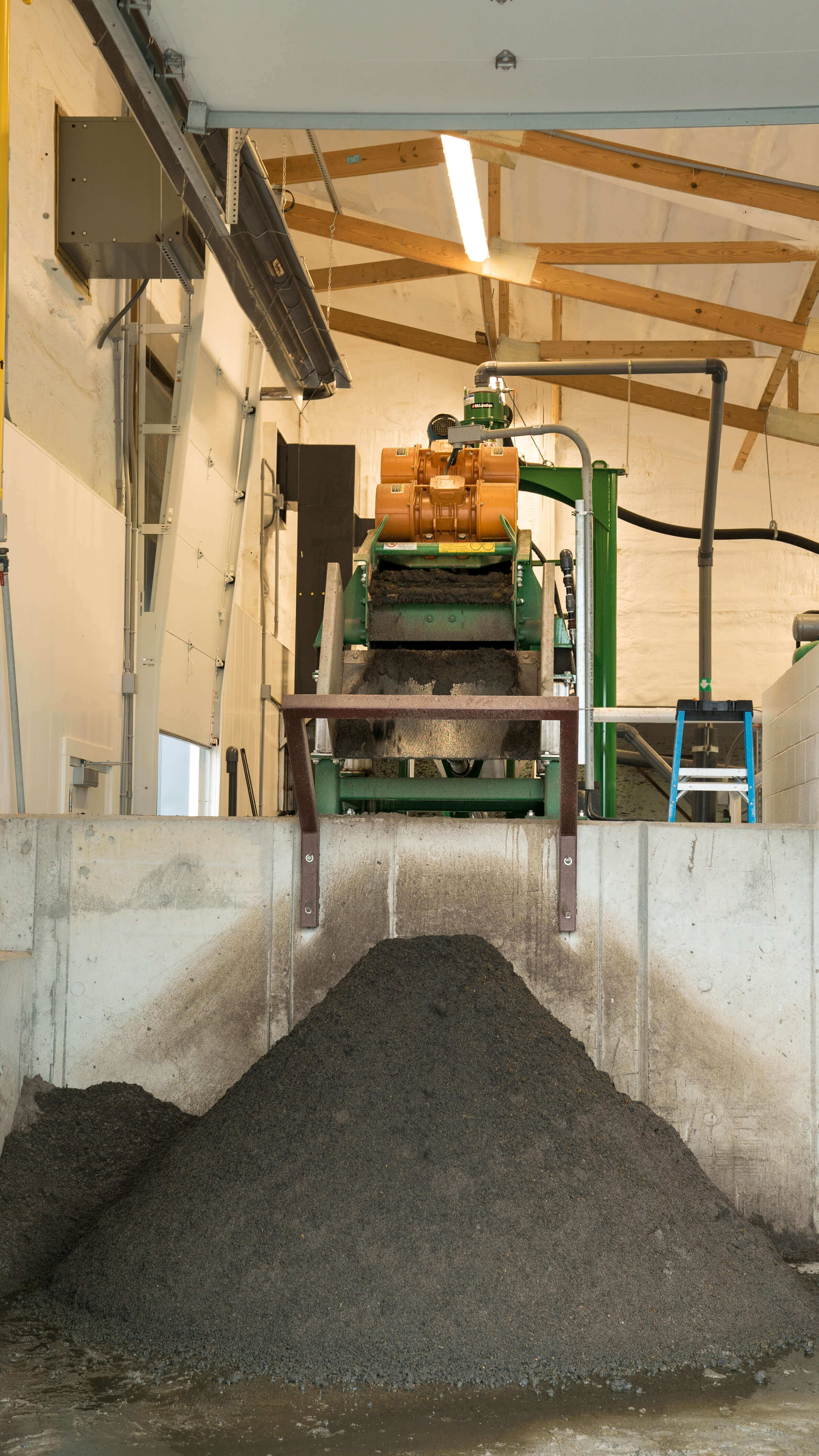