Since 1919, A.F. Gelhar Co, Inc. in Markesan, Wis., has flourished by providing silica sand to foundries throughout Wisconsin. In 2009, the company realized it was in a prime position to take advantage of the growing demand for silica sand to use in hydraulic fracturing – or fracking – and began looking for a system to help them meet the demands of the frac sand industry.
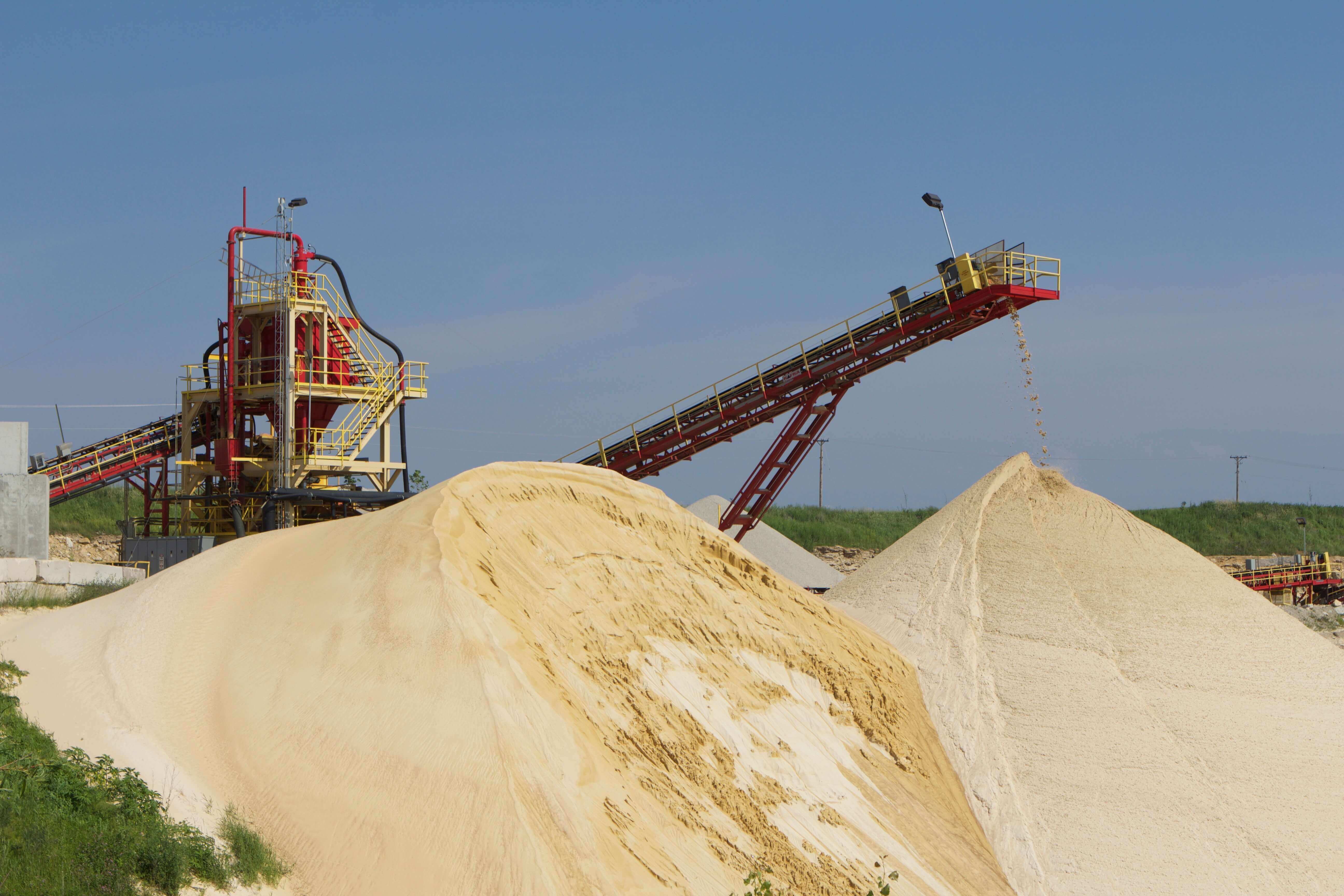
CHALLENGE
A.F. Gelhar had always mined sand for foundries, but found a way to diversify their operation by producing a silica sand blend to meet the needs of frac sand producers. Though it was essentially the same sand, a different sizing process was needed to produce the specific fractions required for frac sand. When producing frac sand or foundry sand, it is important that the sand is free of any contaminants and separated by grain size based on whether it will be used for fracking or in a foundry.
“Foundry sand production and frac sand processing are actually similar processes,” said Kyle Grahn, Vice President of A.F. Gelhar. “What we needed was to find equipment that could meet the capacities required for our production rates. We wanted to improve the way we were operating, while expanding our capacity.”
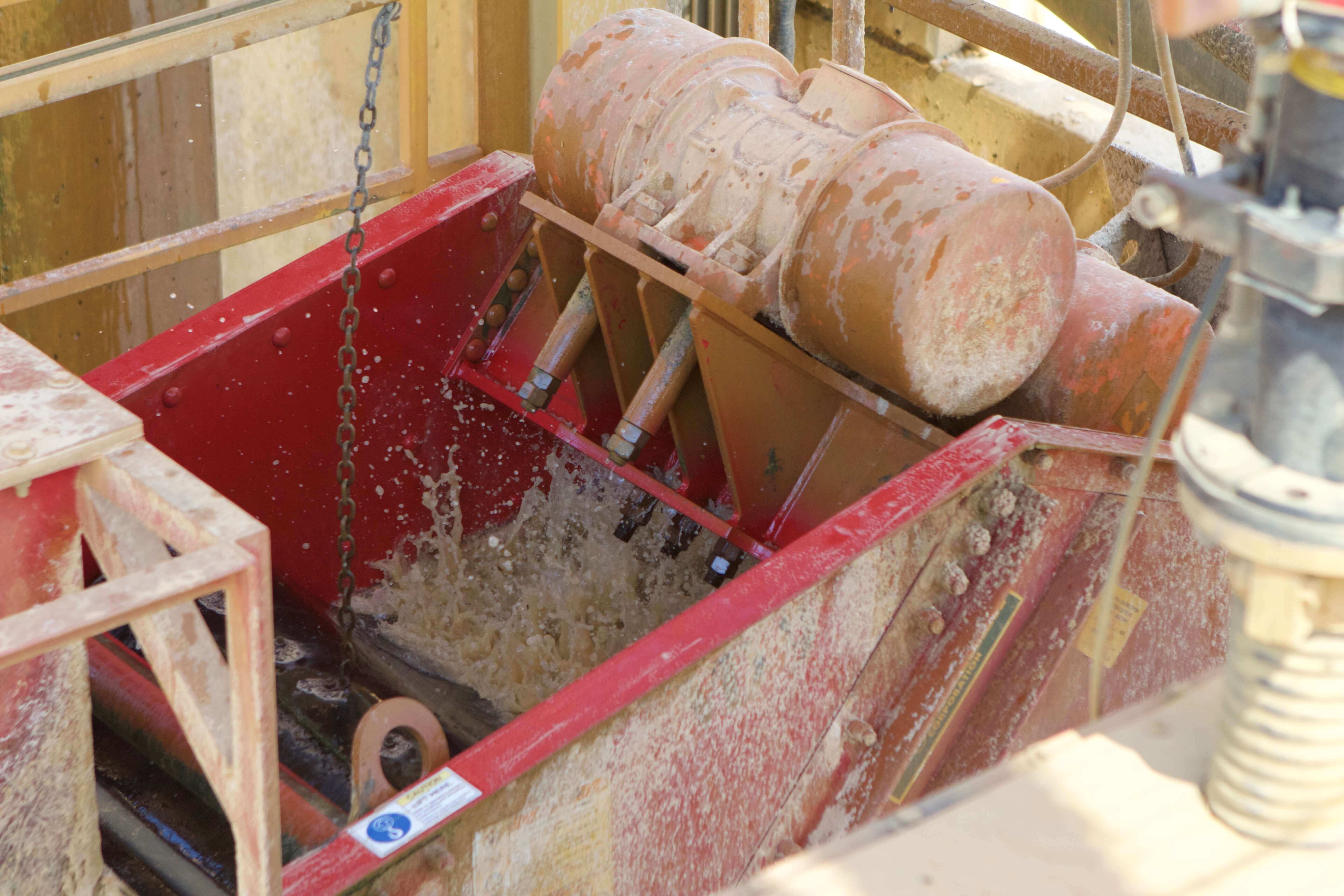
SOLUTION
A.F. Gelhar officials were under time constraints when deciding which system to go with, so instead of reviewing multiple alternatives, Grahn says they based their decision to purchase a new sand processing system from McLanahan Corporation on industry reputation. He also noted that McLanahan came on site and did an analysis that included testing the sand to determine the best solution for A.F. Gelhar’s specific requirements for both fine and coarse sand.
In 2011, McLanahan was able to custom-engineer a system that utilizes Hydrocyclones, a Hydrosizer® (or density separator), Pumps and Dewatering Screens. The system washes and classifies the coarse frac sand, as well as finer sand.
“The system allows us to make two grades of sand, both fine and coarse, which is huge,” Grahn said. “McLanahan designed the system for optimized utilization of the mine’s sand deposit.”
According to Grahn, the system is easy to operate, and he says he enjoys the flexibility the McLanahan system gives the quarry.
After being processed by the McLanahan system, the sand goes through the screening process where the company makes different grades and ships it by rail.
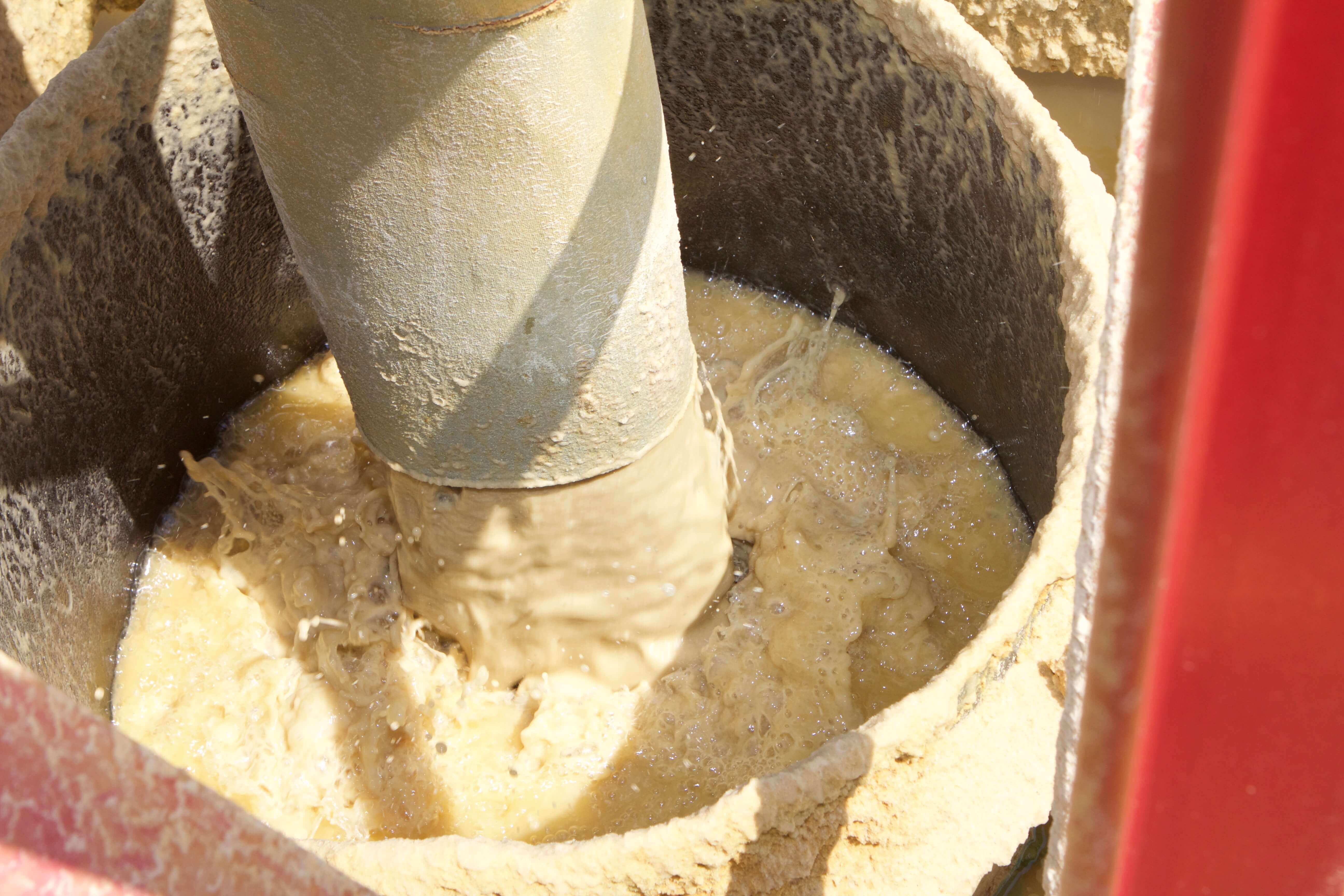
RESULTS
Since installing the McLanahan system, A.F. Gelhar has been able to fulfill orders for frac sand with the plant running as the Wisconsin weather permits, usually about eight months a year from March through November.
“We’ve had a very good return on the McLanahan system. It’s extremely reliable and easy to operate,” Grahn said. “The system has the ability to work around the clock with very few, if any, breakdowns, and that’s important because we can’t afford downtime during our season. It’s been a very premium machine.”
In addition to the power of the McLanahan system, A.F. Gelhar also enjoys a strong working relationship with the company’s representatives.
“Their field service is excellent. Whatever we need, whenever we need it, they will get back to us quickly and that’s a big deal,” Grahn said.