Hydrovac Waste Recycling Systems
McLanahan’s Hydrovac Waste Recycling System is a configurable solution for recovering and washing aggregate material, such as rock, gravel and sand, from hydrovac waste streams.
Applications
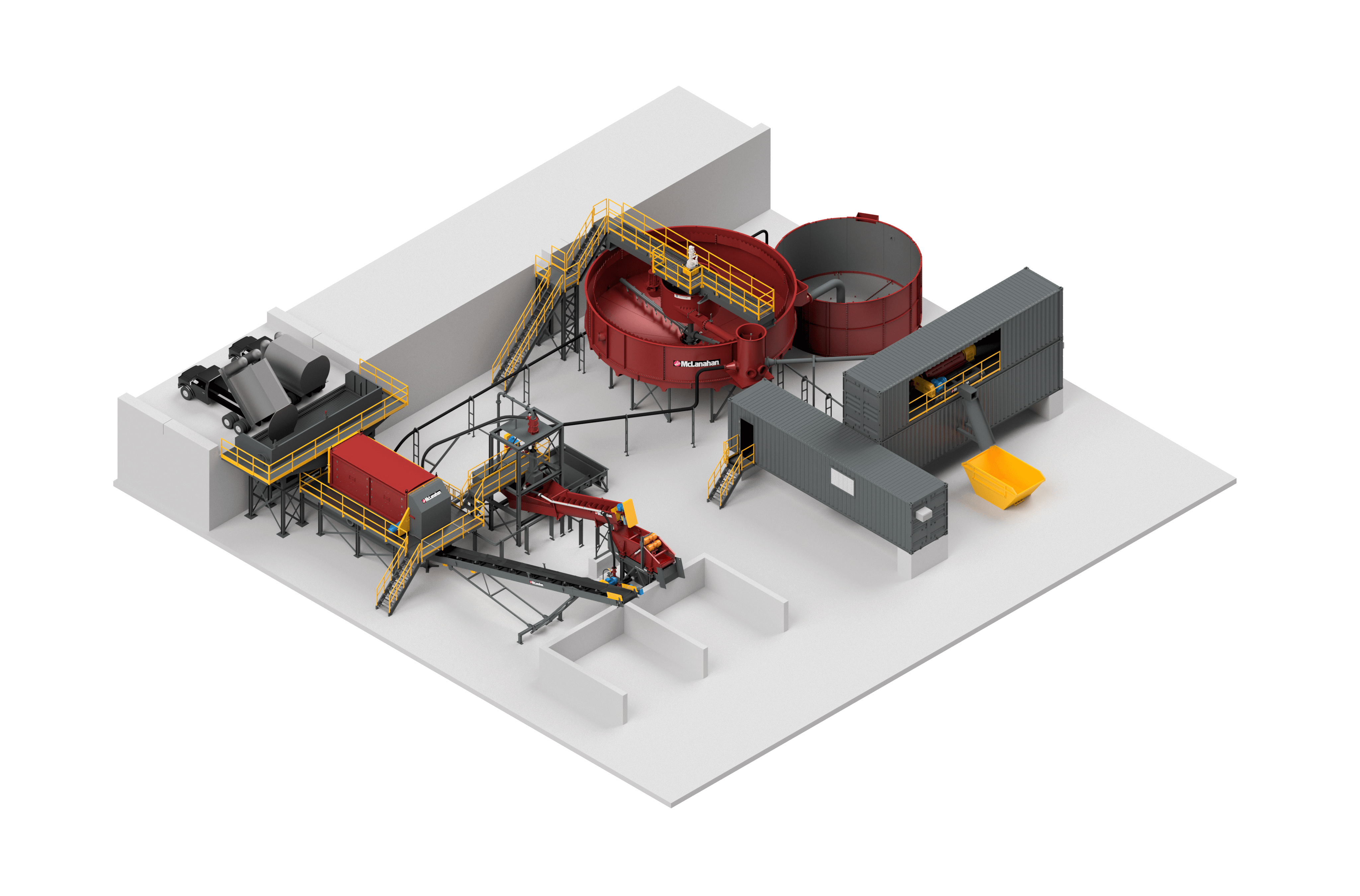
McLanahan’s Hydrovac Waste Recycling System is a configurable solution for recovering and washing aggregate material, such as rock, gravel and sand, from hydrovac waste streams.
Applications
Jump To:
McLanahan has taken a different approach to hydrovac waste recycling from incumbent suppliers to provide a more marketable washed sand and aggregate product for the construction industry. McLanahan’s Hydrovac Waste Recycling Systems provide a double washing of the sand as well as a light scrubbing of the coarse rock to provide a cleaner product that is useful in a wider range of applications.
With McLanahan Hydrovac Waste Recycling Systems, producers can transform waste material into a valuable product, including rock and clean sand, as well as recycle water for reuse in hydro excavation.
McLanahan Hydrovac Waste Recycling Systems feature a dual-bay feed hopper to accept the hydrovac slurry discharged from hydrovac trucks. It features weight cables embedded in the offloading ramp and strobe lights to indicate when a truck is ready to unload.
The slurry then enters a Trommel Screen to separate the coarse material from the fine material and liquid. Internal spray bars rinse the coarse material as it moves through the drum toward the discharge end. External spray bars rinse the screening panels to prevent plugging.
The fine material and water exit the Trommel through holes in the screening panels and fall into a sump underneath. From there, the material is pumped to the Separator™, which is the first stage of the double washing module. The Separator™ classifies the sand product, separating it from the fines, silts, clays, topsoil, etc. and discharges it into the Fine Material Screw Washer, which is the second stage of the double wash.
The Fine Material Screw Washer further removes deleterious material from the sand and discharges the clean sand onto a Dewatering Screen. The Dewatering Screen removes excess moisture ahead of stockpiling.
The wastewater, which includes the fines, silts, clays and topsoil that were removed during the washing process, is then processed through the water recycling portion of the Hydrovac Waste Recovery System. The slurry enters the Thickener, where suspended solids are separated from the liquid. The nearly solids-free liquid portion flows to a holding tank for reuse, while the thickened solids are sent to the next stage of the process.
A Decanter Centrifuge provides further liquid-solid separation, discharging a drip-free solids material that is suitable for mechanical handling and a liquid portion that joins the Thickener overflow in a holding tank for reuse.
McLanahan’s complete product portfolio combined with decades of aggregate processing knowledge and experience allows an unbiased approach to equipment selection. This ensures producers get the best option for recovering and washing aggregate from Hydrovac waste streams.
For hydrovac waste recycling, feed material characteristics will vary from truck to truck. However, it is beneficial to do test work to provide a reference point based on average (or representative) feed samples to validate the selected size and quantity of equipment to achieve the most efficient operating configuration in the field. Each Hydrovac Waste Recycling System is designed based on lab testing by McLanahan’s skilled team of process engineers who analyze the operating parameters of each customer, including number of trucks to process per hour, available footprint, etc. Dedicated project managers offer a single point of contact throughout the design, manufacture, installation and startup process, and each Hydrovac Waste Recycling System is backed by world-renowned service and lifetime factory-direct support. McLanahan also provides controls support services staffed by knowledgeable application and controls engineers who can provide remote troubleshooting guidance and recommend solutions. Additionally, McLanahan’s field service engineers are available to provide on-site support alongside our local dealers.
Using a Separator™ and Fine Material Screw Washer in a Hydrovac Waste Recovery System provides a double wash of the sand, delivering a cleaner product that can be used in a wider range of applications. Additionally, McLanahan designs its Hydrovac Waste Recovery Systems with Separators™ (a siphon-assisted Hydrocyclone) because Separators™ are more adept at handling variations in solids concentration of incoming feed material, which is a characteristic of hydrovac waste, than Hydrocyclones.
Rotary Trommels are beneficial for Hydrovac Waste Recovery Systems because they can handle large volumes of slurry when the system is fed from hydrovac trucks better than Dewatering Screens and can process that slurry more quickly. Hydrovac waste slurry is around 60% water, and the Rotary Trommel is able to scalp water and fine material out of the system due to openings in the screen media as well as internal lifters that prevent the water from surging toward the discharge end. Rotary Trommels are also equipped with internal spray bars that rinse the material as it tumbles through the drum. The spray bars combined with the material-on-material tumbling action provides a light scrub of the coarse aggregate to deliver a cleaner product.
Hydrovac Waste Recycling Systems are modular in design, so they have a more compact footprint. Height wise, the Hydrovac Recycling System is designed as gravity flow plant, utilizing gravity to move the hydrovac waste from truck dump hopper to the scalping screen, and then from the scalping screen to the washing module. Gravity flow designs limit pumping and therefore power requirements.
However, for applications with height restrictions, McLanahan can design a low-profile Hydrovac Waste Recycling System tailored to the specific vertical requirements.
Operating costs for the Hydrovac Waste Recycling System are based on several factors, including number of operators, operating hours, electrical horsepower for the system and polymer (anionic and coagulant) consumption. Polymer selection and average consumption can be predicted based on static and dynamic settling tests of representative samples at McLanahan’s in-house lab.
Hydrovac waste is unique in that the feed material is already in a slurry, so producers need to take water out of the feed for efficient processing. This will lead to a surplus of unwanted water on the site. Producers should plan for how they will dispose of this excess water. Some options include reusing the water in the hydro excavation process, for washing out hydrovac trucks on site or for cleaning the hopper grates of the Hydrovac Waste Recycling System.
Closed-loop Hydrovac Waste Recycling Systems are imperative, as they allow producers to separate solids from liquid in the slurry and recover as much water as possible. Typically, Thickeners and Centrifuges will allow for maximum recovery of water and the production of a more-easily managed solids material, though Filter Presses can also be used depending on the characteristics of the material. Contaminated water treatment systems are also an option to polish the process water so that it is fit for reuse in the hydro excavation process or for housekeeping activities on site. Each site will need to consider the specific region’s regulations regarding water disposal and reuse.
McLanahan Hydrovac Waste Recycling Systems offer options for washing aggregate recovered from hydrovac waste streams.