Slurry Pumps Maintenance
What should I check if the gland leaks at first startup?
First, check what type of gland is fitted to the pump – this is important, as adjustment can have a reverse effect when tightening the bolts versus loosening them. For example, in an H gland, tightening increases the flow; in a G gland loosening increases leakage.
The gland has been set up in the factory to leak at startup to prevent burning up the gland.
With water-purged glands (H and P types), check the gland water pressure, which should be 5 psi above duty pressure. If the pressure is too high, put a pressure regulator in the line.
Referring to the manual, adjust the gland when pumping water only. Allow a little excess leakage at this time.
When the plant is at operational tonnage, re-adjust the gland to a drip every 10 seconds.
When should I replace the rubber casing liners and impeller?
- Inspect liners for areas of wear. It is common for some tracking of the wear patterns, especially near the cutwater area (the point of discharge where the liner to impeller distance is at its minimum). Also check at the suction inlet (and suction bush liner where fitted).
- Inspect impellers for wear and damage at the outer tips of the vanes. Inspect inside the impeller at the back face and where the vanes meet the front and back plates.
- Compare wear from previous inspections to assess the rate of wear.
- If this is the first inspection, note the levels of wear for future reference. If the wear is more than 50% of the rubber thickness, order spares if not already in inventory. If the level of wear is unexpectedly high, contact the dealer or the manufacturer for confirmation on expectations — various operational conditions can cause more rapid wear.
What do I do if the pump bearings are running hot?
If this measurement has been taken by hand at 150°F/65°C, the bearing assembly will be uncomfortable to touch. Obtain a suitable temperature reading device and recheck. Check the temperature at both motor-end and wet-end bearings. The maximum operating temperature for these bearings is 248°F/120°C. Higher speeds will result in higher temperatures for the same size pump.
Operational Best Practices
Can I use an existing sump?
Almost all pump problems are associated with the suction side of the system. McLanahan has a range of purpose-designed sumps, which are a good investment for operational and safety reasons.
Volumetric capacity versus the duty flow-rate, overall dimensions, tank depth, internal angles of the tank walls, size gradation of the materials to be handled and size of suction-side piping, all factor into the suitability and safety of the sump. Too large or too small a volume can create problems of different types.
At best, a poorly designed sump can cause damage to the pump and high maintenance costs. At worst, it can cause a significant safety hazard.
I'm rebuilding my bearing housing and hearing a crackling sound inside the pump, and the bearings seem to be chattering.
This could be a condition called cavitation that is due to the imbalance between NPSHa and NPSHr (Net Positive Suction Head available compared with required).
It can also be caused through low sump levels creating vortexing (air entrainment), which can sound similar to cavitation. This is usually accompanied by the gland irregularly running dry then flooding water.
Bearings can be compromised by an ingress of particulate-laden slurry and from induced mechanical means where the shaft suffers significant and violent vibration from the above causes. While new installations are designed to eliminate these causes, including sufficient head of fluid above the pump and correctly designed suction conditions, homemade sumps or second-hand installations can often miss the necessary calculations. Confirm with the manufacturer when reworking a system to get the best advice and to avoid the high maintenance costs and downtime.
What is the best material to use for piping the slurry I'm handling?
There are multiple choices available, including steel, lined steel, HDPE and mine hose. While PVC is quick and simple for installation, it is not recommended in a wash plant environment due to surges on startup and vibration from multiple sources.
The most important thing is to make the right choice on the diameter. Too small a pipe results in wasted energy (higher head imposed on the pump) and higher wear rates due to velocity. Too large a pipe will result in settling of the particles in the pipeline, which can be a safety issue as well as an operational problem.
Particle size and relative abrasiveness should also be considered. The coarser the materials, the thicker and/or harder any linings may have to be. Fine materials are often overlooked as a problem, but if they are high in silica, steel can wear out in a matter of weeks, yet rubber linings can last years. There is typically a balance in cost benefit, and the cheapest up-front option can be the most expensive even in the short term – even resulting in complete replacement in a matter of weeks.
Consider also the path the pipe has to take in the system – multiple twists and turns versus a tailings line across a flat field. For straight runs of pipe, steel can be a viable option. While requiring specialized equipment for fusion, HDPE is popular, but care should be taken in selection of the DR rating, i.e. thicker walls equals longer wear but more resistance to flow. Hoses of suitable quality provide excellent wear resistance (especially with long sweeping bends), but it challenges any designer with providing adequate support for long runs.
Care should be taken with mismatched IDs, which cause wear points and head loss. Before changing any pipe or adding or subtracting pipe length, consult the pump manufacturer to see if there are adjustments needed to the pump speed and or power. For example, reduction in pipe length can result in the motor tripping out.
Recommended Spare Parts
It is recommended that you keep certain Slurry Pump replacement parts at your facility. These parts will be available in the event of a breakdown and will also be available to perform any repairs that must be made as a result of regularly scheduled maintenance checks.
Part Name | Quantity |
Gland Casing Liner | 1 |
Gland Repair Kit | 1 |
Impeller | 1 |
Suction Casing Liner | 1 |
Related Resources
Looking for more info on Slurry Pumps?
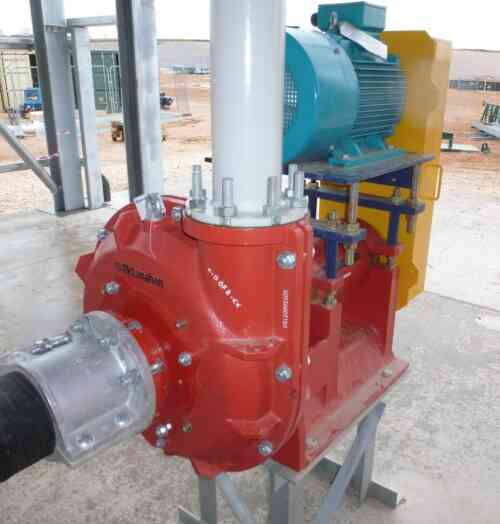