McLanahan Corporation’s Sampling Crusher Troubleshooting Guide focuses on situations such as the zero-speed switch fault alarm is off, the motor does not operate properly, the roll shaft does not turn and more to help you minimize downtime.
Sampling/Pilot Plant Crushers Maintenance
How do I know when I need to replace the hammers or screens in my Sample Hammermill or Rockertooth Crusher?
With Sample Hammermills and Rockertooth Crushers, wear occurs with impact hammers and crushing screens/bars simultaneously. In most applications, hammers tend wear more quickly than screens/bars. For that reason, it is a good idea to periodically inspect impact hammers to monitor wear. Impact hammers are usually reversible, and periodic monitoring and rotation of the hammers will allow for maximum hammer wear life. Hammers are generally considered excessively worn when the head of the hammer wears to a point where the distance between the hammer and the screen begins to increase or the desired crushed product size cannot be made even with new crushing screens or bars.
Crushing screens or bars are typically monitored by making a baseline evaluation of the crushed product from a crusher with new crushing media (hammers and screens or bars) installed. The crushed product is then monitored periodically thereafter for comparison. Wear is indicated by increasing top size or overall coarseness in the crushed product. Once the top size or overall gradation of the crushed product approaches an out-of-spec condition, crushing screens or bars should be replaced. Crushing screens or bars can also be monitored during regular inspection or rotation of impact hammers.
Are internal liners a common wear item?
Liners wear at a much slower rate than hammers and screens/bars. They are a typical replacement part but not necessarily a common one – a set of liners may last several years before replacement is required. This, of course, will depend on the application.
Do drive components need adjusted?
Most McLanahan Sample Crushers are powered by a V-belt drive. V-belt pulleys will wear over time (less frequent) and V-belts will wear and stretch over time (more frequent). If the grooves in the V-belt pulleys no longer have the distinct "V" profile or the V-belts appear to be riding significantly below the outer diameter of the pulley, the pulley should be replaced. V-belt drives on sample crushers typically have an adjustment (e.g. sliding motor base) that allows for tensioning of the V-belts as they stretch or wear. A rule of thumb for tension is to add tension until the slack side of the belts appear to bounce approximately 1/2" (12mm) or less. If V-belts lose their distinctive "V" profile, or any splitting or fraying is observed, the belts should be replaced. Note: Belts should be installed, adjusted and replaced in sets as opposed to individually.
Operational Best Practices
Why is it important to monitor the crushed product gradation?
Crushed product size will gradually increase as crushing media (hammers and screens) wears. This increase in crushed product size can be attributed to wear of the hammers or screens individually or, in some cases, both items at the same time.
Monitoring the crushed product gradation will allow you to establish a wear part/maintenance/replacement cycle. Rotate or replace the crushing hammers and replace the crushing screens as necessary to maintain the desired output gradation.
Why is it important to inspect the V-belt drives?
Sample Crushers are typically equipped with V-belt drives. As the belts wear and stretch, belt slippage can occur over time. When belt slippage occurs, rotor speed and throughput capacity of the crusher may be reduced. Inspecting the V-belt drives for wear allows you to adjust the V-belt tension as necessary, as well as replace the V-belt pulleys if they show signs of wear.
What should I include in a preventative maintenance schedule?
This preventative maintenance schedule should include greasing the crusher bearings. Sample crushers utilize grease lubricated spherical roller bearings. Correct lubrication levels must be maintained to prevent premature wear of internal bearing components, ingress of contaminants and excessive heat generation within the bearing unit. Alternatively, consider an automatic lubrication option that maintains correct grease levels with minimal operator intervention.
Recommended Spare Parts
McLanahan Corporation recommends keeping certain replacement parts at your facility. These parts will be available in the event of a breakdown and will also be available to perform any repairs that must be made as a result of regularly scheduled maintenance checks. McLanahan Corporation stocks a wide variety of commonly used components; however, storing these parts at your facility, will eliminate the expense of air-freighting critical parts that may be required during a breakdown situation.
Part Name | Quantity |
Crushing Screen | 2 |
Hammer Rod | 4 |
Impact Hammer | 8 |
Shaft Seal | 2 |
Related Resources
Looking for more info on Sampling/Pilot Plant Crushers?
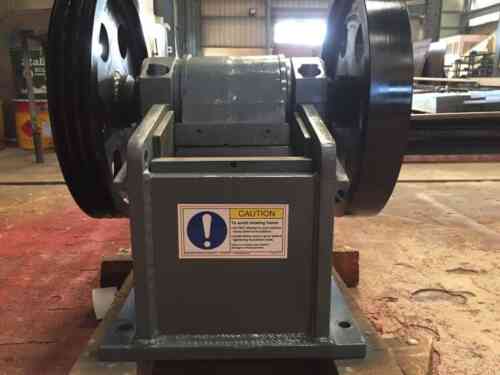