Multi-Stage Sampling System Maintenance
What is the most common preventative maintenance recommendation you offer for sampling systems?
We most commonly recommend that interconnecting chute work be inspected, particularly if wet and/or sticky materials are being sampled. In applications involving difficult materials, it is not unlikely that some material accumulation can occur inside of chute work – this is a common material handling problem. If chutes are inspected and cleaned if necessary on a preventative basis, it will minimize the likelihood that more serious blockages and system downtime will occur.
We keep getting intermittent "zero speed" alarms on our sampler conveyor, but when the system is restarted, the conveyor belts are moving. Does this indicate a bad zero speed switch?
Possibly. More than likely the conveyor belting has stretched over time (this is often
the case with newer belts). Try adding tension to the conveyor belt by adjusting the takeups at the tail pulley of the conveyor, taking care to keep the belt centered on the tail pulley. This resolves the issue most of the time. If the problem persists, then try troubleshooting the zero speed switch.
My system is turned on, but it won't start in auto mode and I can't operate any equipment in manual mode. The screen shows a no control power alarm. What should I do?
The symptoms you describe can occur when the emergency stop button on the control panel is pressed. The e-stop button stays depressed once it is pressed and sometimes it is bumped or unintentionally pressed. Try pulling the e-stop button out and operating a machine or two in manual mode. If the machine(s) you tried will operate in manual mode, try starting the system in auto.
Operational Best Practices
How often should I inspect the chute work?
Interconnecting chute work must be inspected daily to ensure that material is not building up. If buildup occurs, sampling results can be negatively affected and plugging problems can result. Clean away any buildup that you observe.
Note: Chute work inspections can be made less frequently in some applications if more frequent inspections show no signs of material buildup.
Why should I check the access/inspection panels and chute/equipment connections?
Connections between interconnecting chute work and individual pieces of equipment, as well as access and inspection panels and doors, should be environmentally sealed to prevent the contamination of the sample being handled within the system and to prevent moisture loss or gain. Inspecting these components can ensure that an active seal against moisture loss/gain and sample contamination is maintained.
How often should I inspect the plugged chute monitoring devices?
Plugged chute monitoring devices should be kept clean to prevent the occurrence of nuisance alarms. These nuisance alarms occur when smaller amounts of material accumulate on or around the plugged chute monitoring device, resulting in an alarm condition being set when an alarm condition is not actually occurring. Inspecting the plugged chute devices daily can ensure that the material is not accumulated to the point where nuisance alarms occur.
Note: If more frequent inspections of the chute monitoring devices show no signs of material buildup, the inspections can be made less frequently.
Related Resources
Looking for more info on Multi-Stage Sampling Systems?
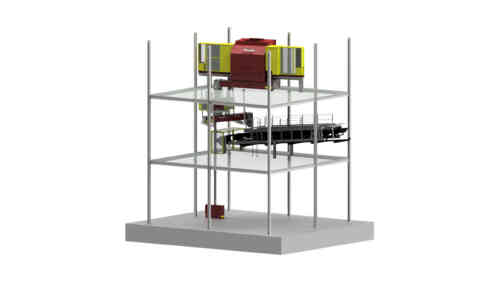