McLanahan Corporation’s Filter Press Troubleshooting Guide can help you maximize the production of your machine by offering corrective actions that can be taken when troubleshooting this equipment. This guide focuses on situations such as: hydraulic cylinders do not move with HVLP pumps running; hydraulic cylinders do not move with LVHP pumps running; high temperature shutdown; and more.
Filter Press Maintenance
How do I replace the filter cloths?
Before replacing the filter cloths, complete the appropriate lockout/tagout procedures and wear appropriate personal protective equipment. Make sure there is adequate space on both sides of the plate and that there is a stable work platform across the opening of the press.
The cloths can be replaced without removing the plate from the press. The backer cloth is secured with zip ties around all the edges, while the outer cloth has hook and look strips on the vertical sides and zip ties across the top and bottom edges.
How do I check and adjust the chain assembly tension?
Before checking and/or adjusting the chain assembly tension, complete the appropriate lockout/tagout procedures and wear appropriate personal protective equipment.
A slight amount of slack on the return side of the machine allows the press to operate most efficiently. Be sure to check the tension at the drive end of the machine where the chain returns off of the head shaft.
Do not allow the returning chain to be pulled tight, or hang loose. The proper condition is for the chain to be slightly slack with constant tension.
To tension the chain, use the screw jacks at the tail shaft end of the machine. Replace the chain when it has stretched 3% of the total length, making sure to replace the entire chain assembly with claws.
The chain is connected and disconnected at the provided master links. When installing a chain, make sure the claws rotate freely and do not lock into position. If they do not rotate freely and lock into position, adjust the tension on the claw locking screws.
Note: Used chain assemblies can be inspected, and parts from them can be used to build a new chain assembly.
If a chain has not been operated for an extended period of time, it may require lubrication to operate properly. A spray-on dry lubricant is preferred, but an oil lubricate can be used if excess oil is cleaned up properly.
How should the filter press be secured and stored for extended downtime (one week or greater)?
- Run all material out of the machine and thoroughly wash down the equipment, including the filter cloths.
- Lockout/Tagout all controls and secure all components to prevent unexpected movement before performing any maintenance, repairs, or adjustments on any portion of this equipment.
- Be sure to protect the filter cloths and plates from ultraviolet light.
- Be sure to protect any slurry or water piping from freezing.
- Be sure to protect any slurry or water pumps from freezing.
- Store the plates vertically for extended periods of time.
- Keep the motor and/or hydraulic power unit clean and dry (refer to the Motor and/or Hydraulics sections for detailed storage information).
- Add the appropriate lubricant to the gear reducer(s) until the level is roughly 95% full, which minimizes the risk of corrosion caused by water condensation (refer to the Reducer section for detailed information).
- Add the appropriate lubricant to the fluid coupling, if applicable, until the level is roughly 95% full, which minimizes the risk of corrosion caused by water condensation (refer to the Coupling section for detailed information).
- Rotate the shafts one complete revolution per week to maintain a film of lubricant on all bearing surfaces and to lubricate the gear reducers (refer to the Reducer section for detailed information).
- Rotate the gear reducers at least one complete revolution per week.
- Rotate the chain one rotation weekly, and lubricate as required.
How do I check the PEMO Pump mechanical seal?
This pump has a sealing system that consists of a double mechanical seal, located inside the mechanical seal box, that must be constantly lubricated with clean flushing water at a minimum pressure and with a minimum flow. Refer to the filter press manual for minimum pressure and flow value calculation.
Before starting the pump, open the valve that delivers flush water to the mechanical seals chamber. The water must flow into the lower part of the mechanical seal box through a pipe having a minimum diameter of 1/4”. It will exit out from the upper part of the chamber. This operation is extremely important because if there is no flush water, the mechanical seals will be operating dry and can be seriously damaged in just a few seconds.
An improperly functioning mechanical seal can be detected by observing the clarity of the outlet flushing water. The presence of impurities in the seal water or the accumulation of impurities in a seal water supply tank indicates the seal should be replaced immediately to avoid greater damages to the bearings.
Operational Best Practices
How often should I inspect the filter cloths?
- Document and track the cloths’ cycle count, as well as when they were installed, repaired, cleaned, etc.
- Inspect/cloth filter cloths weekly.
- Clean cloths with excessive mud buildup on the sealing and stay boss area to prevent uneven loading pressure between the plates and potential slurry blowouts.
- The cloths can be cleaned in place using a common washup hose or a high-pressure spray washer. Care must be taken to prevent cloth damage when using the high-pressure spray washer.
- Replace/repair cloths with tears immediately to prevent abrasive wear damage to the plate surface.
How do I increase press capacity?
- Increase the density of the feed slurry, maximum thickener underflow percent solids.
- Increase the slurry-fill stage flow rate.
- Increase the pressure in the filtration stage.
- Increase the pressure at the end-of-filtration stage. This decreases cake percent solids.
How can I maintain the pump?
- Inspect the pump gland’s water flow and pressure each shift.
- Inspect the pump’s operational temperature and noise daily.
- Inspect the pump’s internals every 3,000 hours of operation.
- Change the pump impeller/casing/shaft assembly as needed to prevent excessive loss of pump pressure and flow capacity.
- Change bearing lubrication oil every 5,000 hours.
How do I choose a filter cloth material?
Filter cloths are typically made from synthetic monofilament or multi-filament thread materials. The most common materials are nylon, polypropylene and polyester. The cloths’ weave pattern and surface treatment can be varied to provide optimum solids/liquid separation, solid release, abrasion resistance and life expectancy. Slurry material testing is required to determine the best cloth material and style for a specific application. All cloth materials should be protected from excessive exposure to heat and prolonged sunshine to prevent premature aging.
Recommended Spare Parts
Some Filter Press components are exposed to wear with normal operation and will require periodic replacement. The most common wear components include:
Part Name | Recommended Quantity |
Filter Cloths | 25 |
Backer Cloths | 1 |
Slurry Feed Pump Assembly | 1 |
It is recommended that you keep other certain Filter Press replacement parts at your facility to perform any repairs or in the event of a breakdown. Please contact the McLanahan Parts and Service Department with your equipment serial number to obtain the recommended parts for your specific Filter Press equipment.
Related Resources
Looking for more info on Filter Presses?
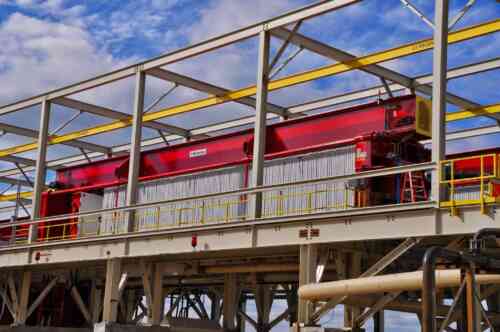