Download McLanahan's Decanter Centrifuge Troubleshooting Guide for tips on torque overload, vibration, lubrication and more.
Decanter Centrifuge Maintenance
How do I clean out a Decanter Centrifuge?
If you need to take your Centrifuge out of service for a period of time or if the machine is running rough (increased vibration) due to a buildup of solids in the bowl or conveyor, you should wash down the internal portions of the Centrifuge. The amount and frequency of washing will depend on the product being processed.
To clean out the Centrifuge, shut off the feed and the main drive motor. Introduce ample quantities of wash water through the feed pipe while the machine is coming to a stop. If only washing out the feed compartment, you do not need to stop the machine. Flushing ports are provided to the cover; water introduced here (during operation) can also be used to clean material from the inside of the cover and the outside of the drum. If the machine is still showing signs of unbalance, stop and isolate/lockout/tagout/blockout the machine, remove the feed pipe, flush out all the feed and drain the compartments in the conveyor hub.
How do I adjust the pool depth?
The pool depth can be changed by adjusting the weir plates covering the discharge ports. For example, on a 900mm diameter machine adjustments can be made in 25 mm increments from 50 mm to 125 mm. All plates must be set at the same setting.
To adjust the weir plates, ensure the Centrifuge is stopped and isolate/lockout/tagout/blockout the machine. Follow all safety precautions listed in the manual, as well as all site-specific safety procedures, before starting work on the machine.
Remove the access panel on the liquid end.
Manually rotate the bowl until one of the discharged ports is visible.
Remove the retaining screws from the weir plate, remove the weir plate, and refit the weir plate to the desired pool depth as indicated by the depth indicator marking. Torque tighten the retaining screws.
Repeat this process for the five remaining discharge ports.
How often should I lubricate the bearings?
Decanter Centrifuges feature a main bearing, gearbox bearing, conveyor internal bushes, thrust bearings, splined drive shaft and drive motor bearings. Oil in the main bearings should be topped off every 1,000 hours and replaced every 8,000 hours. An oil change is required on the gearbox bearings after the first 500 operating hours on a new or refurbished gearbox. After that, the oil in the gearbox bearings should be drained and replaced every 4,000 hours. Grease should be added to the conveyor internal bushes and the thrust bearings every 1,000 hours or monthly. The splines can only be lubricated after it is removed from the drive shaft. Grease should be added to the main drive motor bearing on the drive end every 7,000 hours and to the non-drive end bearing every 13,000 hours. Lubrication type and mount for each bearing can be found in the operation and maintenance manual.
Operational Best Practices for Decanter Centrifuges
How do I optimize the solids dryness?
The dryness of the solids may be optimized in several ways, including:
- Lowering the weir plates on the discharge ports to increase the discharge port radius, thus decreasing the pool depth and increasing the dry deck or beach area
- Increasing the rotational speed to increase the separating G-forces
- Adjusting the feeding position closer to the liquid end of the bowl to reduce disturbance to the cake being formed on the beach
How do I optimize the liquid clarity?
The clarity of the liquid may be optimized in a number of ways, including:
- Increasing the pool depth by raising the weir plates to decrease the radius of the discharge ports
- Increasing the rotational speed to increase the separating G-forces
- Adjusting the feeding position closer to the solids end of the bowl to reduce turbulence in the pool and allow more time for sedimentation to occur
- Diluting very concentrated feed slurries to reduce the hindered settling effect, which prevents sedimentation and results in poor liquid clarity
- Reducing the volume of liquid in the feed slurry to give the solids more time to sediment
- Increasing the temperature of the feed slurry to decrease the viscosity of the liquid and increase the settling speed of the particles, resulting in better liquid clarity
- Adding chemicals, like flocculant, to the slurry to agglomerate particles and improve settling, resulting in clearer liquid
Looking for more info on Decanter Centrifuges?
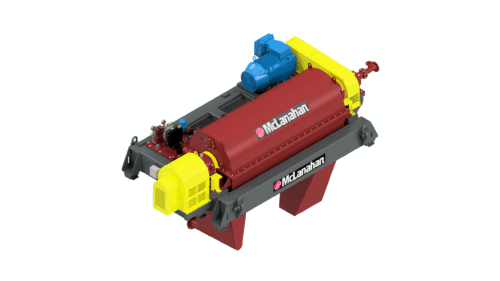