McLanahan Corporation’s Aggregate Conditioner/Blade Mill Troubleshooting Guide offers correction actions that can be taken when troubleshooting your equipment to help you get the most out of your machine. This guide focuses on situations such as: the machine fails to start, the motor is operating but the screw shafts are not rotating, the bearings are hot to the touch, the pulley and leave stalls and more.
Blade Mill Maintenance
What are the lubrication requirements for the lower bearing assembly?
The lower bearing assembly lubrication requirements vary depending on the size of your machine. However, all McLanahan Blade Mill Twin Seal Pak lower bearing assemblies have three lube fittings. The Zerk fitting located on the bearing housing cover is for inserting grease into the bearing cavity to lubricate the supporting roller bearing. Grease should be inserted with a grease gun every eight hours of operation.
The Zerk fitting on the underside of the roller bearing housing is for inserting grease into the internal cavity. Make sure to insert enough grease to maintain a 50%-75% capacity in the lubrication cup covering the third Zerk fitting.
Grease is not to be inserted into the Zerk fitting on the lubrication cup.
The amount of grease required to lubricate the lower bearing assembly depends on your Blade Mill. Refer to the Installation, Operation and Maintenance Manual for more information.
How do I know when to replace my wear shoes and/or paddles?
Conduct a visual inspection of these wear parts regularly to make sure all of these components are in good shape in order to avoid downtime. When the leading edges of wear shoes or paddles are worn and close to exposing the paddle bases and spiral flights that are welded to the pipe shaft, these should be replaced. Having some spare paddles and wear shoes in your stock is recommended.
What are the lubrication requirements for the pillow block bearings?
The type and volume of grease required differs for Blade Mills of different sizes. Refer to the Installation, Operation and Maintenance Manual for the lubrication requirements for your machine.
How often should I replace the gear reducer oil?
The oil in the gear reducer should be changed every 2,000 hours. Check the Installation, Operation and Maintenance Manual for your specific machine for more information on changing the gear reducer oil.
Operational Best Practices
How can I get the best performance from a Blade Mill?
Try to minimize the rock feed entry from directly impacting the Blade Mill shafts.
How far into the washer box should the rock/ore enter?
The rock/ore entering the Blade Mill should be 40 inches or 1m forward of the back plate of the washer box.
How long should I run the Blade Mill after I shut it down so the unit can empty itself of rock and/or sand on the shafts?
10-20 minutes.
How do I remove oversized rock from the washer box?
Shut off the unit and follow all proper lockout/tagout procedures on the motor's starter before removing the oversized rock from the machine.
Recommended Spare Parts
McLanahan Corporation recommends that you keep certain replacement parts for your Blade Mill/Aggregate Conditioner(s) at your facility.
Part Name | Quantity |
Lower Bearing Assembly Rebuild Kit | 1 |
Pillow Block Bearing | 1 |
Pillow Block Bearing Housing | 1 |
Seal Installation Tool | 1 |
Related Resources
Looking for more info on Blade Mills?
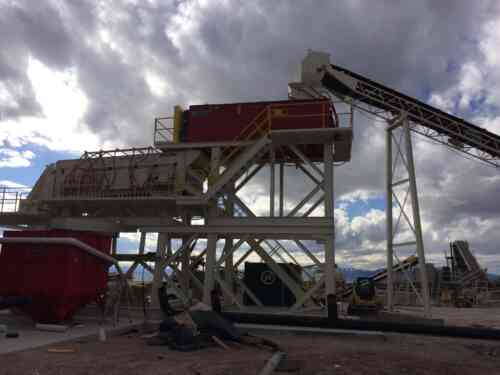