Los chancadores primarios reducen el material bruto de gran tamaño, como rocas y menas en terrones, a tamaños más pequeños para su posterior procesamiento aguas abajo, ya sea para transportarlo a chancadores adicionales o a una planta de procesamiento en húmedo. Es la primera etapa del proceso de chancado que, en algunas ocasiones, incluye etapas secundarias, terciarias e incluso cuaternarias, según el material y los requisitos de los productos finales.
Tipos de chancadores primarios
Existen varios tipos de chancadores primarios, entre los que se incluyen:
- Chancadores giratorios
- Chancadores de mandíbulas
- Molinos de martillos
- Chancadores de impacto de eje horizontal
- Chancadores
- Chancadores de rodillos
- Chancadores de cono
- Alimentadores-quebrantadores
Chancadores giratorios
Los chancadores giratorios son una excelente opción para un chancador primario, puesto que pueden manipular materiales muy duros y abrasivos. Son ideales para el material seco a ligeramente húmedo, pero no para material pegajoso.
Los chancadores giratorios son chancadores de compresión que se utilizan principalmente para materiales de minería pesada y cantera en aplicaciones de tonelaje extremadamente alto. Ofrecen un índice de reducción de 4:1 a 7:1.
Las características principales de un chancador giratorio incluyen una cámara de chancado alta revestida con placas de desgaste de manganeso reemplazables, un eje principal con cabezal y manto, y una araña para la sujeción con la parte superior del rodamiento del eje principal. Incorporan un sistema de posicionamiento ajustable del eje principal y un conjunto de transmisión, y están disponibles con diseños de un solo cilindro o varios.
El material que se chanchará se alimenta por la parte superior de la cámara de chancado y se comprime entre el manto vibratorio ubicado en el centro y los revestimientos cóncavos fijos que cubren las paredes internas de la cámara. Cuando se realiza el chancado del material al tamaño de producto deseado, se lo descarga hacia la parte inferior del chancador. Uno de los beneficios adicionales del chancador giratorio es que no existe necesidad de realizar un zarandeo o separación preliminares de los finos en la alimentación.
Se puede controlar la gradación mediante el ajuste de la separación entre el mando y los cóncavos en su punto más estrecho. Para obtener un tamaño de producto más pequeño, se puede subir el eje principal para crear un espacio más pequeño entre el manto y los revestimientos. Para obtener un tamaño de producto más grande, se puede bajar el eje principal para crear un espacio más grande entre el manto y los revestimientos. A medida que la máquina se ajusta en un nivel más estrecho para lograr un producto más fino, también se reduce el rendimiento volumétrico de esta. Una abertura más grande equivale a un mayor rendimiento.
Los chancadores giratorios generalmente tienen un costo de capital más alto y requieren una estructura de alojamiento más grande que puede representar una inversión significativa en ingeniería.
Chancadores de mandíbulas
Los chancadores de mandíbulas son otra excelente opción para las aplicaciones de chancado primario debido a que pueden admitir los materiales más resistentes, duros y abrasivos. Pueden manipular material seco a ligeramente húmedo que no esté pegajoso.
Estos tipos de chancadores de compresión son los más adecuados para aplicaciones de minería pesada, materiales de cantera, arena y grava, y reciclaje. Ofrecen un índice de reducción de 3:1 a 6:1.
Los chancadores de mandíbulas incorporan una pieza de acero móvil (denominada biela) y una pieza de acero fija que forman una cámara en forma de “V”. El material que ingresa en la támara se chanca al tamaño entre la piezas de acero móvil y la pieza de acero fija. La mayor parte de la acción de chancado se realiza en el tercio inferior de la cámara. En un ciclo de la biela giratoria, en primer lugar, el material de la cámara se comprime para chancharlo. A continuación, la cámara se abre, lo que permite que el material caiga más abajo por la cámara antes de que comience el siguiente ciclo de compresión.
Molinos de martillos
Los molinos de martillos pueden utilizarse como chancadores primarios en varios tipos de aplicaciones de áridos y aplicaciones industriales, como la piedra caliza, el mármol, el esquisto, el yeso, el fosfato, la bauxita, la escoria de aluminio, el uranio, la criolita, el clinker, la cal viva, el coque de petróleo, el carbón, entre otras.
Al utilizar una combinación de los métodos de reducción de impacto, corte y atrición, los molinos de martillos tienden a generar materiales más finos, además de la reducción de tamaño, lo que podría no ser deseable en todas las aplicaciones. El material ingresa por el chancador y se destruye al impactar con los martillos móviles que están sujetados a un rotor giratorio. Las partículas rebotan hacia fuera de las placas quebradoras en dirección al círculo del martillo y se trasportan hacia el conjunto de rejilla y a lo largo de la superficie de rejilla, lo que permite triturar las partículas más grandes. Una vez que el material alcanza el tamaño apropiado, sale por las aberturas del conjunto de rejilla. Se pueden realizar los cambios en la gradación de producción mediante los cambios de velocidad y las diferentes combinaciones de rejillas con diferentes tamaños de aberturas. Son una herramienta adecuada para su uso con aplicaciones poco abrasivas.
Configuraciones comunes de los molinos de martillos industriales:
- Estándar
- A prueba de obstrucciones
- Alimentación central
De estos tres tipos, los tipos de molinos de martillos estándares y a prueba de obstrucciones se consideran chancadores primarios debido al hecho de que pueden admitir tamaños de alimentación grandes de hasta 72" y son capaces de realizar una reducción nominal a 3".
Las diferencias entre los molinos de martillos estándares y a prueba de obstrucciones son la placa quebrantadora y los tipos de materiales que procesan. Los molinos de martillos estándares incorporan una placa quebrantadora fija y son perfectos para los materiales quebradizos de flujo libre con un tamaño de alimentación grande. Los molinos de martillos a prueba de obstrucciones incorporan una placa quebrantadora móvil y son perfectos para materiales húmedos, pegajosos y quebradizos con un tamaño de alimentación grande.
Los molinos de martillos para áridos se pueden utilizar para producir material de áridos cúbico y de alta calidad con una solidez superior o para producir cal pulverizada.
Chancadores de impacto de eje horizontal
Los chancadores de impacto de eje horizontal, como los modelos New Holland, Andreas y MaxCap (que es un híbrido de los dos), suelen utilizarse para la reducción de tamaño primaria de materiales de dureza baja o intermedia.
Estos tipos de chancadores de impacto pueden manipular material ligeramente abrasivo, seco o húmedo que no esté pegajoso. Ofrecen un índice de reducción de 10:1 a 25:1 y se utilizan generalmente para materiales de cantera, arena y grava, y aplicaciones de reciclaje.
Las impactadoras de eje horizontal incorporan una cámara de expansión grande dentro de la cual se encuentra un eje rotor giratorio cubierto con barras de impacto o martillos. El material que ingresa por la cámara de chancado se conecta con el rotor giratorio, que arroja el material a las placas quebrantadoras que revisten las paredes de la cámara. La mayor parte de la rotura del material se realiza en el contacto inicial del material con el rotor y su posterior impacto con las placas quebrantadoras. Cierta rotura adicional se produce mediante las colisiones entre las partículas a medida que el material se sacude dentro de la cámara.
Los chancadores de impacto de eje horizontal generan un producto altamente cúbico de solidez mejorada. La gradación es más uniforme y puede ajustarse cambiando las revoluciones por minuto del rotor. También se puede realizar un control adicional de la gradación si se ajustan las rejillas y las placas dentro de la máquina. Una configuración más ajustada permite obtener una producción más pequeña. Además, también reduce el rendimiento.
Sin embargo, un aspecto a tener en cuenta es que, si bien los chancadores de impacto de eje horizontal producen más finos que cualquier otro tipo de chancador primario en esa etapa, también podrían permitir una menor producción de finos en todo el circuito. Cuantas más etapas de reducción pase una partícula antes de su calibrado correcto, mayor será la cantidad de finos que producirá. Puesto que la impactadora primaria tiene un índice de reducción más elevado, crea un producto más acabado. Esto tiene como resultado una menor necesidad de reducción durante el proceso y podría provocar que se generen finos en todo el circuito.
Chancadores
Los chancadores de rodillos de accionamiento directo se utilizan para el chancado primario de materiales de dureza baja o intermedia y ligeramente abrasivos que pueden estar secos o húmedos y pegajosos. Son los más adecuados para las aplicaciones de minería pesada y ofrecen un índice de reducción típico de 4:1.

Los chancadores primarios incorporan dos rodillos que giran hacia adentro y que realizan el chancado del material entre los dientes y las estructuras de los rodillos. El material ya chancado pasa entre los rodillos o fluye alrededor de estos, lo que reduce la generación de finos.
Estos tipos de chancadores ofrecen un bajo perfil y altas capacidades de rendimiento con velocidades de rodillos bajas. Además, al igual que los chancadores giratorios, pueden admitir finos en la alimentación, mientras que otras máquinas de compresión, como los chancadores de mandíbula, requieren cierto zarandeo previo.
Chancadores de rodillos
De forma similar a los chancadores, los chancadores de rodillo pueden utilizarse para el chancado primario de materiales blandos o de dureza intermedia y ligeramente abrasivos que pueden estar secos o húmedos y pegajosos. Generalmente, se utilizan en aplicaciones de minería pesada y ofrecen un índice de reducción típico de 4:1.
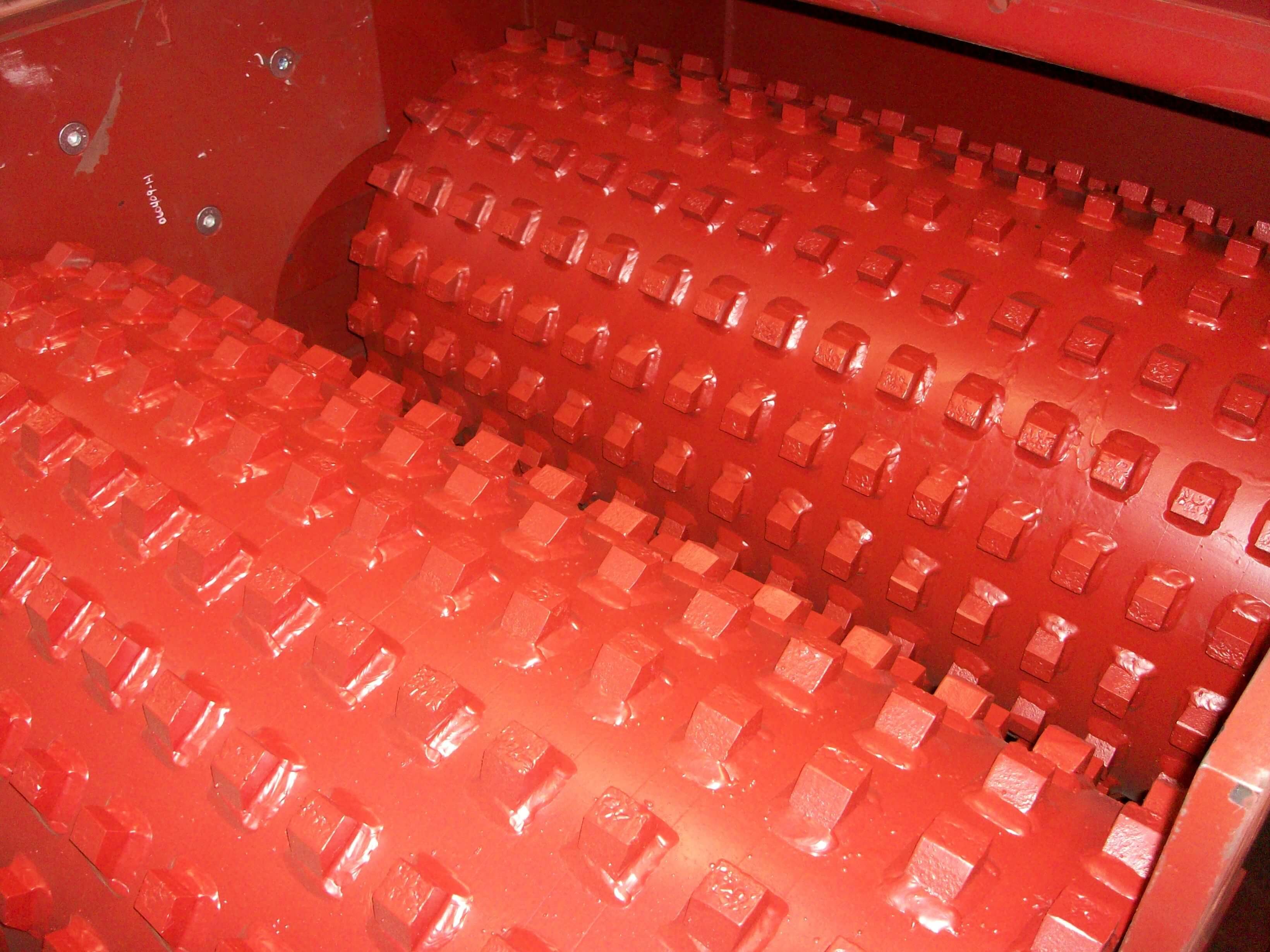
Los chancadores de rodillo están disponibles en varios diseños:
- Rodillo simple
- Rodillo doble
- Rodillo triple
- Rodillo cuádruple
Los chancadores de rodillo son máquinas de tipo de compresión, por lo que la gradación de producción se controla principalmente a través de la calibración de distancia entre los rodillos. Una configuración más ancha tiene como resultado un producto más grueso. Además, también proporciona un mayor rendimiento.
Los chancadores de rodillo simple incorporan un rodillo de chancado de baja velocidad que realiza el chancado del material contra una placa de chancado curva. Requieren menos altura libre que los otros chancadores primarios y producen una cantidad mínima de finos. Sin embargo, los chancadores de rodillo simple ofrecen un calibrado de producto limitado y restricciones en términos de capacidad de rendimiento.
Los chancadores de rodillos dobles incorporan dos ejes de rodillo giratorios que realizan el chancado del material entre los dientes y las estructuras de los rodillos. Estos tipos de chancadores de rodillo permiten obtener un producto cúbico con una mínima generación de finos y pueden manipular capacidades más grandes.
En la aplicación correcta, los chancadores de rodillos triples y cuádruples pueden realizar las etapas primaria y secundaria de reducción de material en una sola máquina. La etapa superior de un chancador de rodillos triples ofrece un índice de reducción de 6:1, mientras que la etapa inferior ofrece uno de 4:1. En una configuración de rodillo triple, la etapa primaria del chancado se produce en la etapa superior del chancador e incorpora una configuración de un solo rodillo que realiza el chancado inicial. Una disposición de rodillo doble en la etapa inferior de la máquina admite el material calibrado desde la etapa superior y lo calibra aun más. Es ideal para la manipulación de tamaños de alimentación más grandes debido al diseño y la abertura de alimentación más grande.
En una configuración de rodillo cuádruple, tanto la etapa superior como la inferior tienen un índice de reducción de 4:1. La etapa de chancado primario en la parte superior de la máquina y la etapa secundaria en la parte inferior de la máquina incorporan una disposición de rodillo doble. Debido a la abertura de alimentación y el diseño de la etapa superior, estos tipos de chancadores de rodillo son ideales para manipular material de alimentación de tamaño mediano.
Al igual que otros chancadores de rodillo enumerados, los chancadores de rodillos triples y cuádruples permiten obtener un producto cúbico con una mínima generación de finos.
Chancadores de cono
Los chancadores de cono son chancadores de tipo de compresión que se utilizan generalmente en las etapas de chancado secundario, pero también se pueden utilizar como chancadores primarios en determinadas aplicaciones. Pueden manipular materiales abrasivos de dureza alta e intermedia que pueden estar secos o húmedos, pero no pegajosos. Los chancadores de cono generalmente se utilizan con materiales de cantera y en aplicaciones de arena y grava. Ofrecen un índice de reducción de 3:1 a 5:1.
Los materiales que ingresan en un chancador de cono se comprimen entre un manto vibratorio y los cóncavos dentro de la cámara de chancado. Se puede controlar la gradación mediante el ajuste de la separación entre el mando y los cóncavos en su punto más estrecho. Esto se logra elevando y bajando la parte superior o el recipiente del chancador. Una configuración más fina permitirá crear un producto más fino, pero con un rendimiento más bajo. La velocidad también puede determinar la gradación de producción final. Se utiliza una velocidad rápida para la alimentación más fina para lograr una producción más fina.
Alimentadores-quebrantadores
Los alimentadores-quebrantadores, que combinan la alimentación y el chancado en una sola máquina, se utilizan para el chancado primario de materiales quebradizos y ligeramente abrasivos que pueden estar húmedos o secos, pero no pegajosos. Generalmente, se utilizan en aplicaciones de minería pesada para ofrecer un chancado primario y generar un producto que se puede transportar para un mayor procesamiento aguas abajo.

Estas máquinas de alta capacidad incorporan una cinta transportadora de arrastre de cadena y eslabones que dosifica el material hacia una púa horizontal. El material bruto se transporta hacia el rodillo con púas giratorio, que realiza el chancado del material contra los eslabones y la plataforma de la cinta transportadora.
Dado que los alimentadores-quebrantadores calibran en una sola dimensión únicamente, es posible que sean necesarias etapas de chancado secundarias e incluso terciarias para lograr el tamaño de producto final deseado. Se los puede alimentar con una pala, un camión, un cargador o una topadora, y se pueden hacer portátiles para las operaciones subterráneas.
Cómo elegir el chancador primario adecuado
Si bien todas estas máquinas pueden utilizarse como chancadores primarios, no se las puede emplear indistintamente en todas las industrias. Algunos tipos de chancadores primarios son más adecuados para el material duro, mientras que otros son mejores para la manipulación de material más quebradizo o húmedo/pegajoso. Algunos chancadores requieren el zarandeo previo y algunos admiten una alimentación completa. Algunos chancadores generan más finos que otros.
Chancadores primarios utilizados en las aplicaciones de áridos
Entre los tipos de chancadores primarios que se pueden encontrar generalmente en las aplicaciones de áridos, se incluyen:
- Chancadores de mandíbulas
- Chancadores giratorios
- Impactadoras
- Chancadores de cono
Chancadores primarios utilizados en las aplicaciones de minería
Entre los tipos de chancadores primarios que se pueden encontrar generalmente en las aplicaciones de minería, se incluyen:
- Chancadores de rodillos
- Chancadores
- Alimentadores-quebrantadores
- Chancadores de mandíbulas
- Chancadores de cono
- Impactadoras
El chancador primario adecuado para una aplicación depende de varios factores:
- Material que se chancará
- Tamaño de la alimentación
- Tamaño del producto deseado
- Capacidad requerida
- Resistencia a la compresión de la alimentación
- Contenido de humedad
El material y sus características, por ejemplo, su dureza, densidad, forma y condición, incidirán en el tipo de chancador que se debe utilizar. Conocer las características del material, además de las ventajas y limitaciones de los diferentes tipos de chancadores, ayudará a determinar el mejor chancador primario para una aplicación determinada.