Los filtros prensa suelen utilizarse en la industria minera para desaguar residuos y recuperar agua de proceso. Estos equipos tienen placas que, al cerrarse, crean cámaras que luego se llenan de pulpa mediante una bomba de alimentación. La presión de la bomba de alimentación permite desaguar las pulpas. El agua pasa a través de un colector que se crea por los orificios en las esquinas de las placas de filtrado o a través de llaves individuales que se encuentran en cada placa, y los residuos de filtración sólidos quedan en las cámaras. A continuación, estos se descargan en el transportador o directamente en el suelo antes de que el ciclo se repita.
Si bien los filtros prensa mecánicos tal como los conocemos hoy en día pueden parecer relativamente nuevos, no son un invento reciente.
Los primeros filtros prensa datan de hace miles de años y tienen su origen en varias culturas de todo el mundo. En tiempos de la dinastía Shang (1600 a. C.), se ideó un tipo de filtro prensa de madera para producir té de camelia, un género de planta con flor oriunda del este y el sur de Asia. En la dinastía XVIII de Egipto (1543-1292 a. C), se extraía el jugo de las uvas con una prensa de saco que se exprimía mediante un gran torniquete. Los romanos comparten una historia similar. Catón el Viejo describió el modo en que los romanos producían vino con prensas de madera entre los años 100 a. C y 400 d. C.
El diseño de los filtros prensa se mantuvo mayormente intacto hasta la Revolución Industrial del siglo XVIII. En 1853, en el Reino Unido, se creó el primer filtro prensa automático del mundo. Esta máquina utilizaba células presurizadas para obtener aceite de las semillas de plantas y fue considerada la precursora de los filtros prensa Johnson Press. Fue el primer filtro prensa de placas y bastidores de acero en la historia, y se lo utilizó principalmente para el procesamiento de alimentos y aplicaciones industriales.
Este filtro de prensa tuvo su primera aparición en la industria minera en el siglo XX. El filtro prensa de placas y bastidores de acero Eimco se utilizó por más de un siglo para recuperar el polvo de zinc de las soluciones de cianuro de oro.
Placas de filtrado de placas y bastidores
Al igual que los filtros prensa Johnson Press y Eimco, los filtros prensa de placas y bastidores desaguan el material entre dos placas planas que se cierran contra un bastidor y forman una cámara. La pulpa se bombea dentro de las cámaras y las llena. La presión de la bomba de alimentación expulsa el agua de la pulpa y el material sólido queda dentro de la cámara. El número de bastidores determina la cantidad de residuos sólidos que se descarga del filtro prensa y el grosor de dichos residuos depende del grosor de los bastidores.
Un problema del filtro prensa de placas y bastidores era la remoción de los residuos al separarse las placas. Los residuos solían quedar adheridos a los bastidores y un operador debía quitarlos manualmente. Esto derivó en un pensamiento más innovador para solucionar el problema, y el equipo volvió a modernizarse.
Placas de filtrado con cámaras empotradas
En 1959, K. Kurita y S. Suwa modificaron los filtros prensa para mejorar la remoción de residuos y la absorción de humedad con filtros prensa con cámaras empotradas. Los filtros prensa con cámaras empotradas tienen placas empotradas (de allí deriva su nombre).
Cuando dos placas de filtrado con cámara empotrada se acercan entre sí, forman una cavidad. La cavidad resultante determina la profundidad de la cámara o el grosor del residuo. El grosor del residuo es igual a la suma de las dos placas adyacentes. Por ejemplo, si el lado derecho de la placa n.° 1 es de 20 mm y el lado izquierdo de la placa n.°2 también, la cámara que se forme cuando ambas placas se cierren será de 40 mm, lo que significa que el residuo tendrá el mismo grosor.
La primera y la última placa solo están empotradas en un solo lado para que no se forme un residuo parcial entre la placa y el bastidor del filtro prensa. Esto significa que la cantidad de residuos que se forma en los filtros prensa con cámara empotrada siempre será uno menos que el número de placas. Por ejemplo, si el filtro prensa con cámara empotrada tiene 150 placas, se formarán 149 residuos.
El proceso de desaguado es similar al de desaguar con filtros prensa de placas y bastidores. La pulpa se bombea dentro de las cámaras que forman las placas y la presión de la bomba de alimentación hace que las cámaras se llenen con los materiales sólidos y que el agua se expulse a medida que estos ingresan. El tiempo, la presión, la alimentación o las velocidades de flujo de filtrado determinan el momento en que los residuos están completamente formados. Una vez que los residuos están completamente formados, la bomba se apaga, las placas de filtrado se separan y los residuos caen con facilidad de entre las placas, ya que no hay un bastidor al que puedan adherirse.
A diferencia de lo que comúnmente se cree, ni los filtros prensa con cámara empotrada ni los de placas y bastidores escurren los residuos hasta desaguar la pulpa. Las placas se mantienen cerradas con un ariete hidráulico y la presión del fluido que producen las bombas desagua la pulpa. El filtro prensa solo se abre y se cierra al final de cada ciclo para separar las placas y soltar los residuos.
Placas de filtrado de membranas
Tras la invención de los filtros prensa con cámara empotrada, surgen, como variante de este estilo, los filtros prensa de membrana. Al igual que los filtros prensa con cámara empotrada, los filtros prensa de membrana presentan placas empotradas, pero además tienen un diafragma, o membrana, que recubre cada lado de la placa. Al final de cada ciclo, la membrana escurre físicamente cada uno de los residuos que se forman en las cavidades que se forman entre las placas.
En tanto que los filtros prensa con cámara empotrada y los de placas y bastidores dependen de la presión de la bomba que alimenta el equipo para realizar el desaguado, la pulpa se bombea dentro del filtro prensa de membrana a una presión de no más de 100 psi. Las membranas se presurizan con el agua o el aire que hay detrás de ellas, que hacen que estas se introduzcan en la cavidad y que cada residuo se escurra de manera individual. Debido a las propiedades de compresión y explosión del aire comprimido, se recomienda el uso de agua para presiones que superen los 125 psi. Una vez que se haya alcanzado el tiempo de escurrimiento deseado, el agua de las membranas se descarga y estas se despresurizan; la prensa se destraba y las placas de filtrado se abren y se descargan los residuos.
El filtro prensa de membrana puede beneficiar las operaciones al desaguar sólidos altamente compresibles. Un ejemplo hipotético para ilustrar esta situación: si escurre una pulpa llena de rodamientos de bolas, que no son muy compresibles, la membrana solo podrá reordenar esos rodamientos de bolas y dar lugar a residuos un poco más secos. Sin embargo, si escurre una pulpa llena de esponjas, que son muy compresibles, notará una gran diferencia.
Las placas de membrana pueden tener dos configuraciones principales: todas las placas tienen membranas o solo hay membranas cada dos placas. En esta configuración, llamada “membrana con paquete mixto”, las placas alternas tienen otras complementarias, que son similares a las placas con cámara empotrada. La membrana con paquete mixto se suministra con mayor frecuencia, ya que el costo inicial y los costos operativos a largo plazo son más bajos.
Hay dos tipos de placas de membrana: membranas soldadas y membranas reemplazables. Las membranas soldadas están soldadas por calor al cuerpo de la placa. Cuando estas membranas fallan por la fatiga que causa la flexión, debe reemplazarse la placa completa. Las membranas reemplazables se acoplan a las placas; por lo tanto, solo es necesario reemplazarlas cuando fallan.
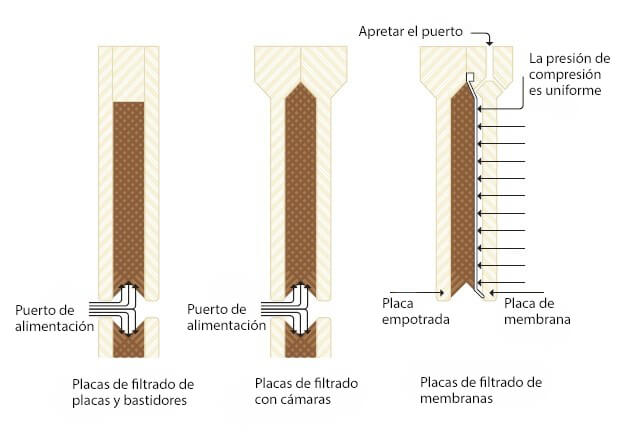
Viga superior en comparación con viga lateral
Los productores tienen dos opciones para apoyar las placas de los filtros prensa: La viga superior y la viga lateral. Los filtros prensa de viga superior soportan el peso de las placas con las vigas. Debido a que en los filtros prensa de viga superior las placas están suspendidas, la cargas dinámicas que se crean al mantener las placas cerradas se aíslan de las vigas. Esto es beneficioso, ya que las fuerzas pueden ser muy altas —1,5 millones de libras (680.389 kg) en una prensa de 2.000 mm x 2.000 mm que funciona a 225 psi.
Los filtros prensa de viga superior son más adecuados para sistemas de lavado de telas de alta presión debido al mayor espacio que hay entre las placas. La gran abertura que hay entre las placas permite una menor abrasión cuando se liberan los residuos, más movimiento para liberarlos, una abertura rápida de las placas para reducir los tiempos del ciclo y una liberación de residuos mejorada. Además, los filtros prensa de viga superior proporcionan un acceso más fácil para limpiar y cambiar las telas filtrantes.
Los filtros prensa de viga lateral soportan el peso de las placas con vigas que se extienden a lo largo de los laterales del equipo. Este tipo de filtro tiene un sistema de apertura rápido, sistemas de agitación de placas más fáciles de implementar, y son más cortos, por lo que se adaptan a aplicaciones pequeñas o portátiles. Permiten emplear sistemas de lavado de baja presión más rápidos que se utilizan comúnmente en aplicaciones de concentración de minerales.
Dónde nos encontramos hoy
Muchos clientes de las industrias minera, del carbón y de los áridos utilizan filtros prensa con cámara empotrada y de placas de membrana para desaguar los residuos como consecuencia del creciente número de reglamentaciones ambientales y del ahorro de costos comparado con las tecnologías alternativas, como las represas de residuos y las prensas de correa.
Es usted quien debe elegir el mejor filtro prensa para sus operaciones. Tenga en cuenta el tipo y la cantidad de material que necesita desaguar para elegir el estilo de placa, el tamaño y la cantidad, así como el grosor deseado de los residuos y el medio de filtro adecuado para el material de la pulpa.