Introducción
Cuando se trata de elegir el mejor chancador para su operación de reducción primaria, primero tiene que considerar los detalles de la aplicación. El tamaño de producto deseado, la capacidad, el índice de molturabilidad de Hardgrove (HGI), el porcentaje de roca y la dureza de la roca presente en el material de alimentación son algunos de los factores que influyen en la selección de los equipos de chancado primarios.
Dado que muchos de los tipos disponibles de chancadores se utilizan en distintas aplicaciones, es posible que en la decisión final con respecto a la selección de chancador, deban tenerse en cuenta otros aspectos, como las limitaciones de espacio, los métodos de minería y los costos.
Veamos los diversos chancadores que se emplean para la reducción del carbón en la etapa primaria.
Alimentadores-quebrantadores
Los Alimentadores-Quebrantadores están diseñados para operaciones de chancado fijas, portátiles o semimóviles. Les han permitido a los operadores mineros aumentar la producción y mejorar la manipulación de materiales.
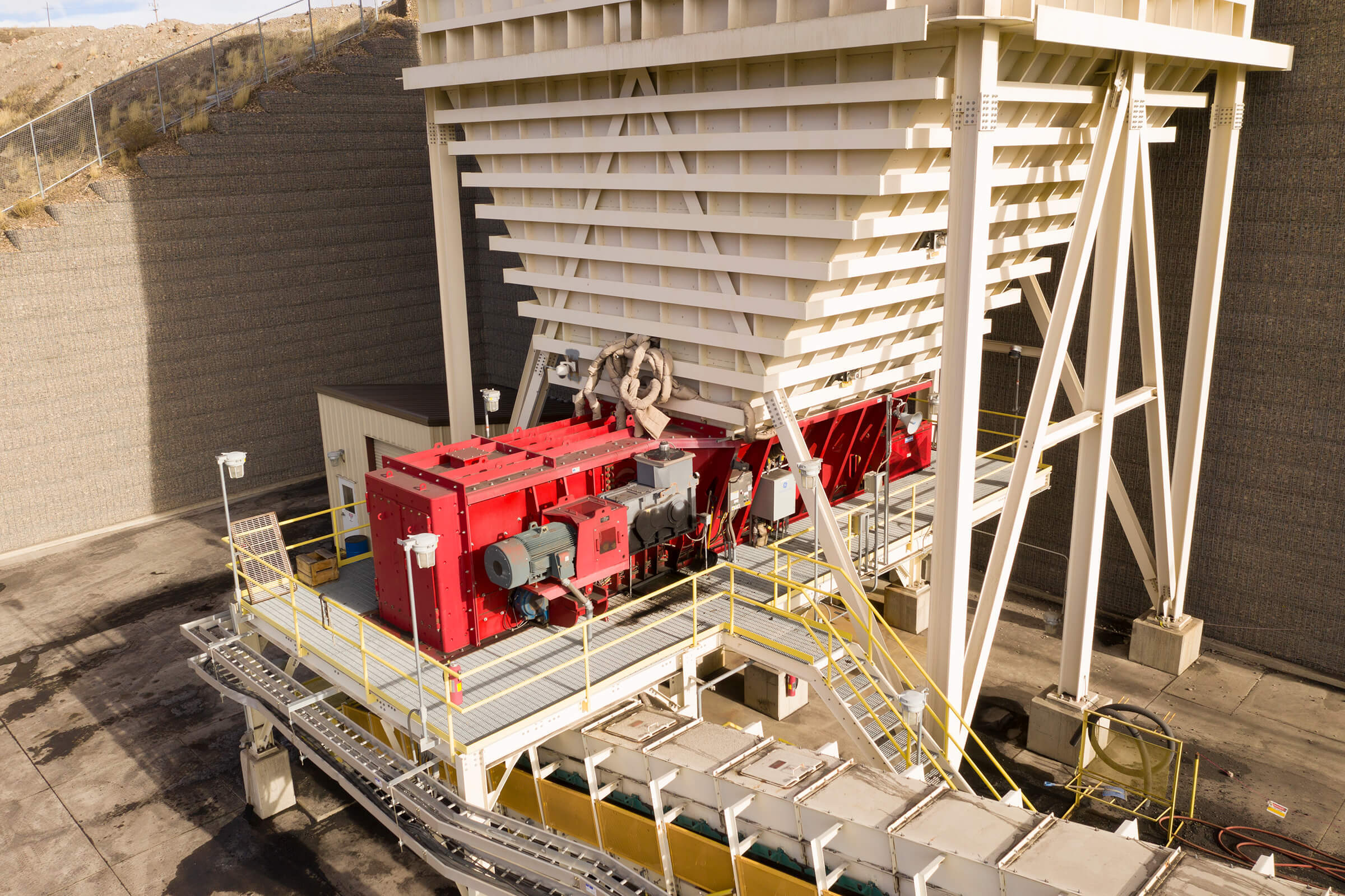
En general, los alimentadores-quebrantadores son capaces de procesar el material de alimentación en bruto y reducirlo hasta lograr un producto transportable por cinta para continuar la reducción de tamaño en etapas posteriores. Estos equipos ofrecen las siguientes posibilidades:
- Pueden ubicarse debajo de tolvas para recibir el material de alimentación de camiones de transporte
- Cuentan con una tolva integrada para recibir el material de alimentación de cargadores
- Pueden tener un diseño del tipo trampa para topadora con una entrada abierta para la carga con topadora, carro lanzadera u otro método
Los alimentadores-quebrantadores están diseñados para emplear una cinta transportadora estilo cadena de arrastre o barra de desplazamiento, conectada a cualquier extremo mediante conjuntos de ejes de acero equipados con piñones y rodamientos. El mecanismo quebrador consiste en un rotor horizontal que chanca el material contra los eslabones y la plataforma de la cinta transportadora, situados en dirección al extremo de descarga de la unidad.
Según la capacidad, los alimentadores-quebrantadores pueden tener un diseño de arrastre simple o doble. Resultan ideales para procesar el material de alimentación en bruto durante la etapa primaria de chancado y reducirlo hasta lograr un producto que pueda transportarse.
Estas unidades pueden procesar tamaños de alimentación de hasta 72" y generar un tamaño de producto nominal de entre 6" y 14". Dado que los alimentadores-quebrantadores calibran en una sola dimensión, es posible que sean necesarias etapas de chancado secundarias y terciarias para lograr el tamaño de producto final deseado.
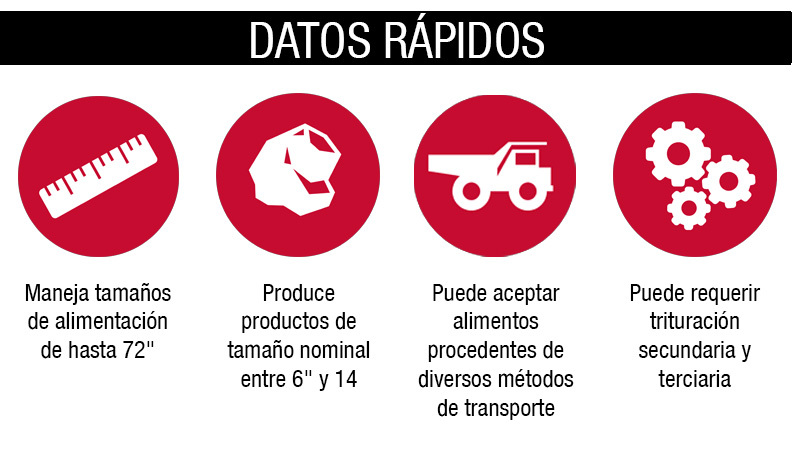
Quebradores rotatorios
Los Quebradores Rotatorios se usan con mayor frecuencia en el procesamiento de carbón. Son particularmente útiles cuando los flujos de alimentación tienen cantidades considerables de desechos en forma de roca, trozos de madera provenientes de la mina, pernos de anclaje, etc., que deben eliminarse antes de continuar el procesamiento.
Los quebradores rotatorios reducen por medio de la atrición al levantar y dejar caer repetidas veces el material de alimentación contra las placas de zarandeo resistentes, reforzadas y perforadas que recubren el interior del cilindro. La presencia de roca dura en el material de alimentación ayuda a romper el carbón durante la acción de caída.
Las plataformas elevadoras atornilladas al interior del cilindro levantan el material de alimentación y son ajustables para adelantar o retrasar el flujo de material a través del quebrador rotatorio. Esta acción de elevación y caída reduce el carbón con eficacia, al tiempo que evita la roca, los fragmentos extraños de hierro y los trozos de madera provenientes de la mina.
El producto deseado pasa a través de las aberturas de las placas de zarandeo hasta llegar a la cinta transportadora de producto que se encuentra abajo, mientras el material de desecho se descarga por el extremo del cilindro con ayuda de los arados de descarga.
Por lo general, los quebradores rotatorios admiten tamaños de alimentación desde 8" hasta 30" y generan productos cuyo tamaño oscila entre 2" y 6". Son varios los factores que determinan el diámetro y la longitud de un quebrador rotatorio, entre ellos, el tamaño máximo de alimentación, el índice de molturabilidad de Hardgrove (HGI) del material de alimentación, el tamaño medio porcentual del material de alimentación, el tamaño del producto y el porcentaje de desechos. La selección puede confirmarse mediante pruebas de caída/rotura.
Las características del material de alimentación son sumamente importantes a la hora de considerar el uso de quebradores rotatorios.
Si el carbón es muy duro o muy leñoso (p. ej., el lignito), no se romperá adecuadamente, y una parte considerable del producto se descargará junto con los desechos.
Si hay un bajo porcentaje de roca en el material de alimentación o si la roca es demasiado blanda, es posible que el carbón no se rompa tal como se desea. Esto puede provocar que se rechace el producto o que la roca blanda se rompa, lo que implicaría la entrada de material de desecho en el flujo del producto.
El carbón con alto contenido de humedad y un elevado porcentaje de finos o arcillas puede obstruir las placas de zarandeo, especialmente cuando se utilizan placas con perforaciones más pequeñas.
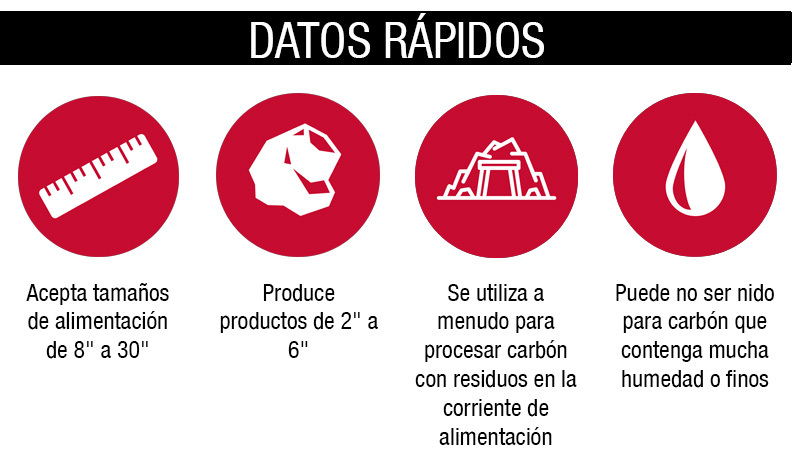
Chancadores calibradores de accionamiento directo
Un chancador calibrador es un chancador de accionamiento directo y bajo perfil que se utiliza para las etapas de reducción primaria, secundaria y terciaria.
Los chancadores calibradores pueden recibir material descargado directamente de un cargador o, de modo más uniforme, de una cinta transportadora, zaranda vibratoria o alimentador. Son ideales para aplicaciones de chancado portátiles o en el pozo debido a su baja altura libre.
El tamaño del material de alimentación, el tamaño del producto y la capacidad son los factores que normalmente determinan el diámetro de los rodillos y el ancho del chancador calibrador. En ocasiones, el tamaño máximo del material puede imponer la necesidad de contar con una unidad mucho más grande que la sugerida únicamente por los requisitos de capacidad.
Los chancadores calibradores primarios son similares a los chancadores de rodillos dobles en el sentido de que tienen dos rodillos con dientes entrecruzados y chancan hacia dentro, lo que genera un producto cúbico.
Pero las similitudes acaban allí. Los chancadores calibradores utilizan unidades de accionamiento con un reductor de engranajes montado en el eje que permiten el funcionamiento de los rodillos a baja velocidad, al tiempo que emplean un grado elevado de torsión para proporcionar potencia de chancado.
Se usa un acoplamiento limitador de torsión entre el reductor y el motor para brindar alivio en caso de que se produzca un estancamiento debido al encuentro con fragmentos extraños de acero u otros materiales no triturable.
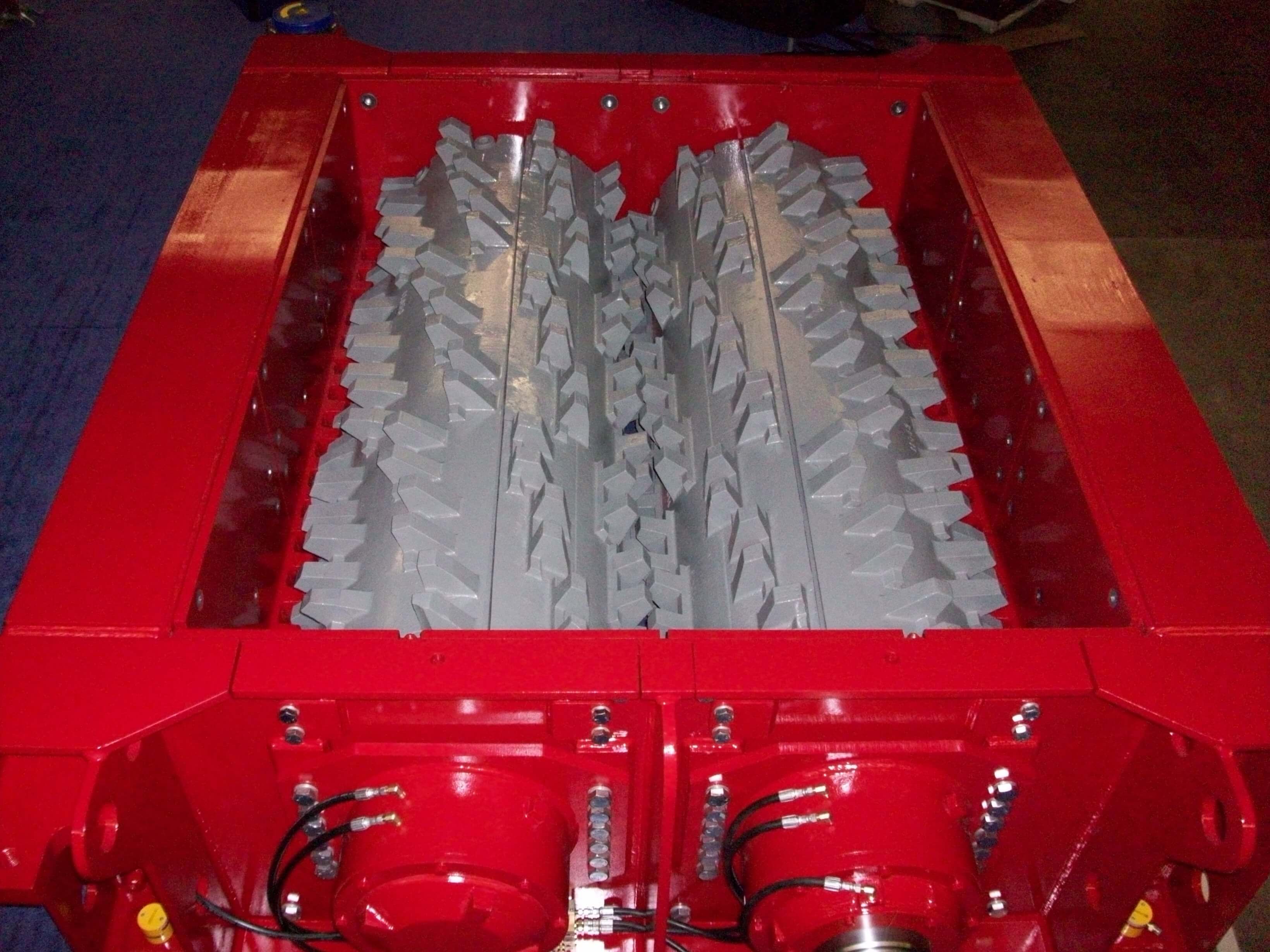
La velocidad de los rodillos de los chancadores calibradores primarios puede ser hasta cuatro veces más baja que la de los chancadores de rodillo convencionales accionados por correa. Debido a que los chancadores calibradores presentan un grado elevado de torsión y baja velocidad de rodillos, tienden a fracturar el material a lo largo de las líneas de separación naturales, lo que genera una cantidad mínima de finos.
Los chancadores calibradores se alimentan por encima de todo el interior de la estructura, lo que permite que los finos pasen a través de las aberturas entre los dientes de chancado y los peines de calibrado. En teoría, solo se chanca el material de tamaño aproximado y el material de gran tamaño. Por lo tanto, incluso con los rodillos a baja velocidad, es posible alcanzar una gran capacidad de producción.
Los diámetros típicos de los rodillos varían de 20" a 60" (menos la altura de los dientes) y el ancho oscila entre 48" y 144". En el caso de los chancadores calibradores primarios, los tamaños de alimentación varían de 32" a 60" y generan tamaños de producto de entre 8" y 15". A la hora de seleccionar el chancador, se considera un índice de reducción de 4:1 del material de alimentación con respecto al tamaño del producto.
Como ocurre con otros chancadores, el tamaño del material de alimentación normalmente determina el diámetro de los rodillos y el ancho del chancador calibrador. Sin embargo, a veces se encuentra una excepción a esta regla dependiendo de las propiedades del carbón o las características específicas del material de alimentación.
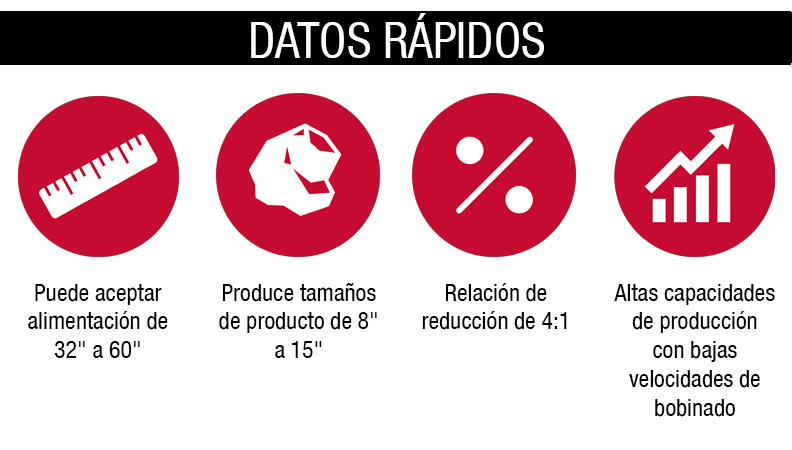
Los chancadores de rodillo simple
Con un índice de reducción de 6:1, los chancadores de rodillo simple son ideales para reducir grandes terrones de material de alimentación hasta lograr un producto de tamaño mediano y, al mismo tiempo, producir un bajo porcentaje de finos. El calibrado del producto al mínimo con un chancador de rodillo simple por lo general se limita a 2" o 3".
El chancado se realiza a lo largo del ancho total de la placa de chancado curva y el rodillo de chancado de baja velocidad. La curvatura de la placa de chancado posee una abertura de garganta amplia para capturar terrones grandes e irregulares de material de alimentación. Las puntas o revestimientos reemplazables de la placa de chancado poseen ranuras para encajar con los dientes de los rodillos a fin de generar un producto cúbico y reducir de manera eficaz el desbaste.
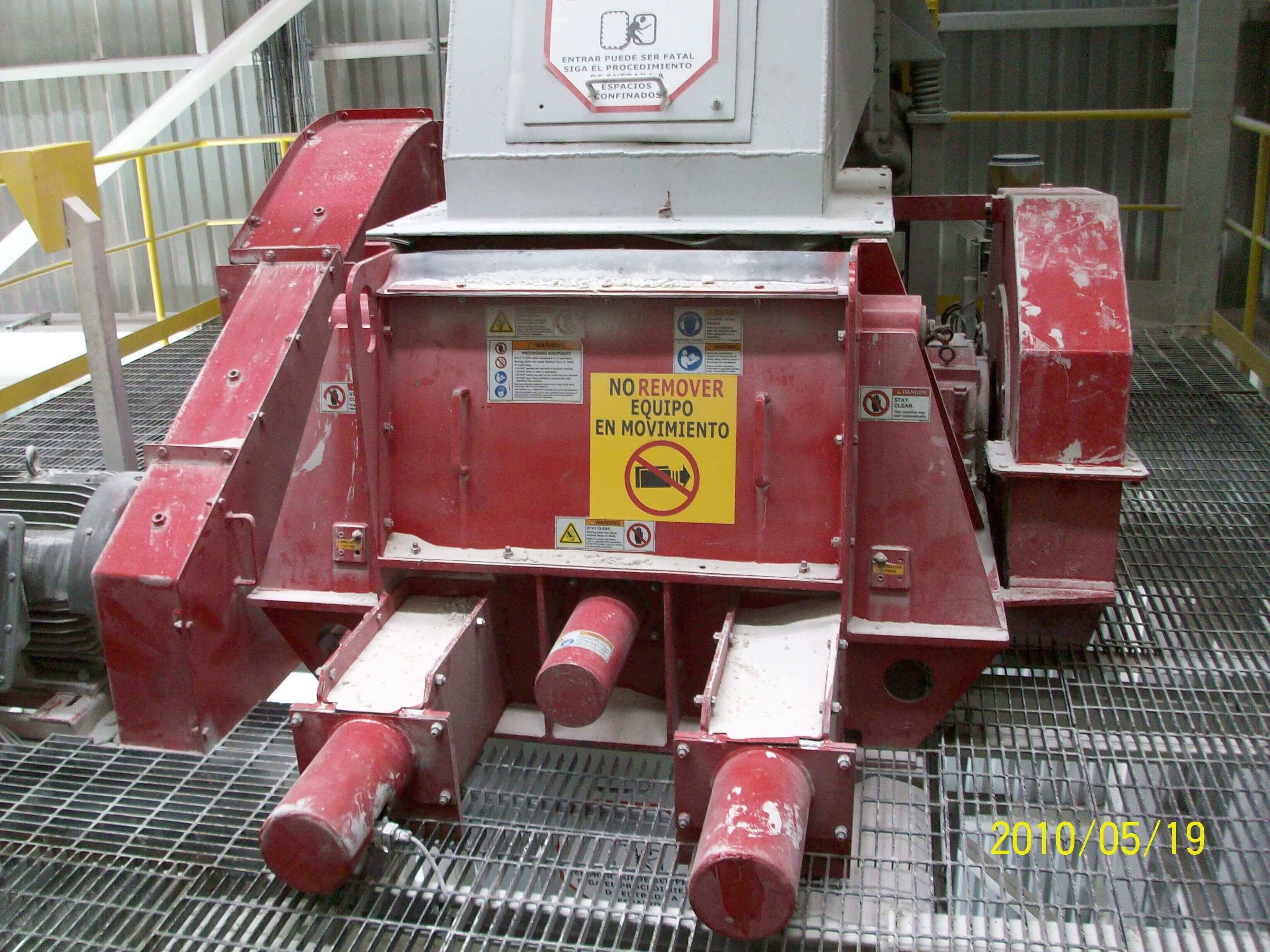
Los chancadores de rodillo simple se accionan por medio de correas V y emplean un volante de inercia de gran diámetro con un conjunto de engranajes y piñones para reducir la velocidad del rodillo. Con ayuda de la inercia generada por el volante, este chancador funciona con un nivel relativamente bajo de potencia y requiere menor altura libre en comparación con otros chancadores utilizados para la etapa primaria de reducción.
En general, los chancadores accionados por correa emplean alguna forma de mecanismo de alivio para fragmentos extraños a fin de permitir el movimiento momentáneo de la placa de chancado o de uno de los rodillos de chancado. Esto se logra mediante un sistema mecánico de resorte y articulación.
Los chancadores de rodillo simple, aunque resultan ideales para diversas aplicaciones, se encuentran limitados en términos de capacidad de producción y, por lo tanto, no son útiles para numerosos requisitos de alto tonelaje.
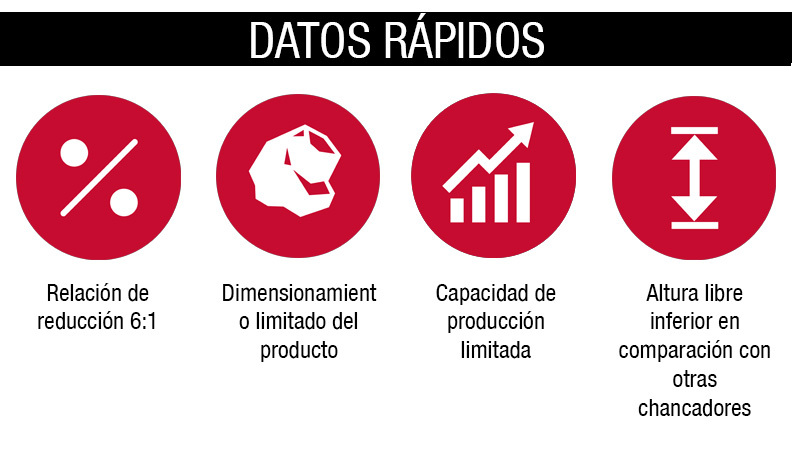
Chancadores de rodillos dobles
Los chancadores de rodillos dobles accionados por correa pueden utilizarse en aplicaciones de chancado primario si se calibran correctamente, pero por lo general se emplean para la reducción de diversos minerales en las etapas secundaria y terciaria.
Los chancadores de rodillos dobles ofrecen numerosas ventajas, como un nivel elevado de capacidad, baja altura libre, menor potencia, la capacidad de manipular materiales de alimentación húmedos y pegajosos, y la generación de un porcentaje mínimo de finos, al tiempo que se obtiene un producto cúbico.
Como ocurre con otros chancadores, el ancho y el diámetro de los rodillos dependen del tamaño del material de alimentación, el tamaño del producto y la capacidad del chancador de rodillos dobles. Como regla general, el índice de reducción de un chancador de rodillos dobles es de 4:1.
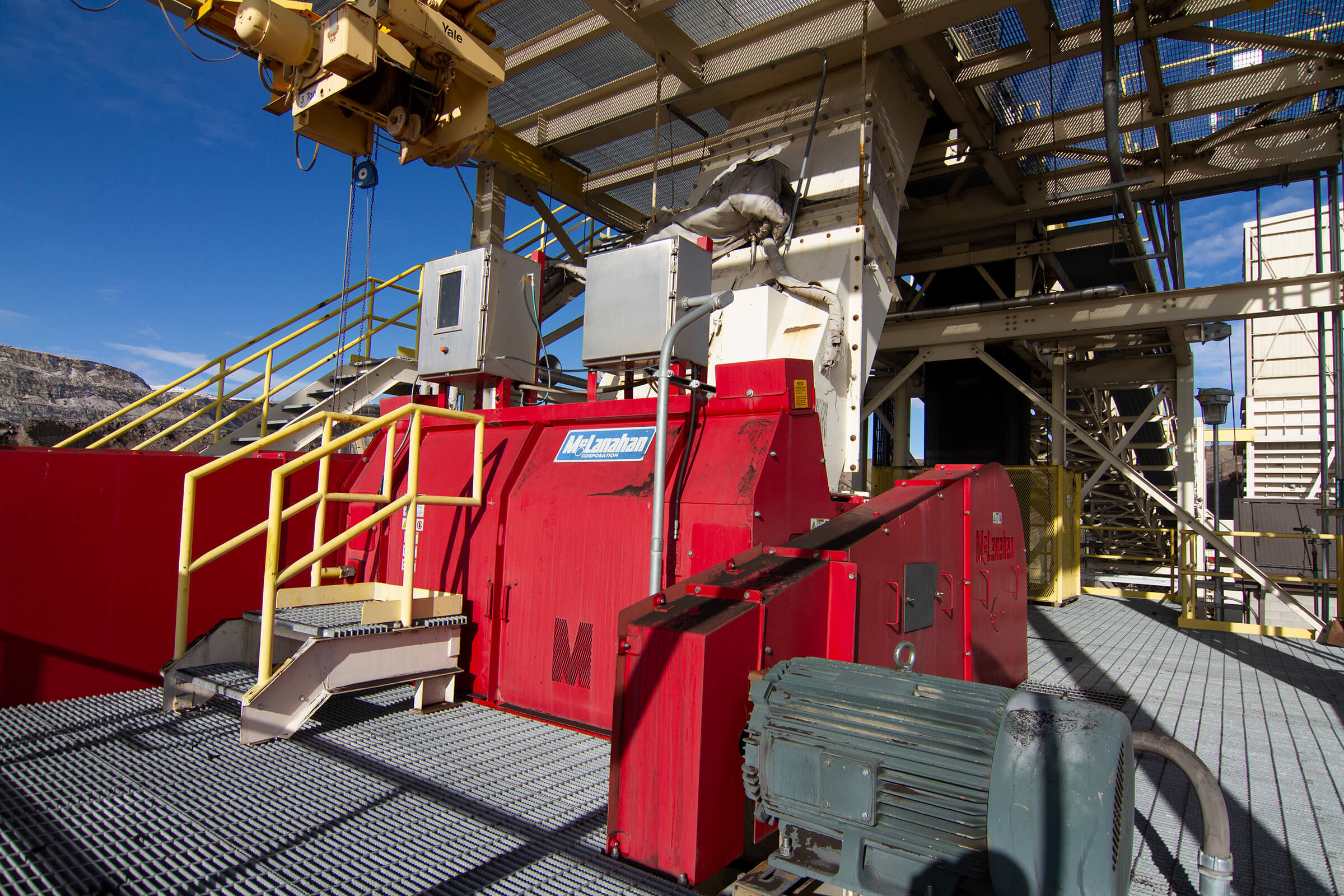
El diseño simplificado otorga a estas unidades una excelente confiabilidad y exige muy poco mantenimiento. Los chancadores están diseñados con un mecanismo de alivio para fragmentos extraños que permite el paso de materiales no chancables a fin de asegurar un funcionamiento ininterrumpido. Una vez que ha pasado el material no chancable, el chancador regresa al ajuste de producto inicial.
En el caso de los chancadores de rodillos dobles, todo el material de alimentación debe pasar entre los rodillos de chancado, que permiten el chancado entre partículas además del chancado mecánico.
Con diversos diseños de superficie de rodillo disponibles, este chancador es capaz de generar un producto mucho más fino que cualquiera de los otros chancadores mencionados.
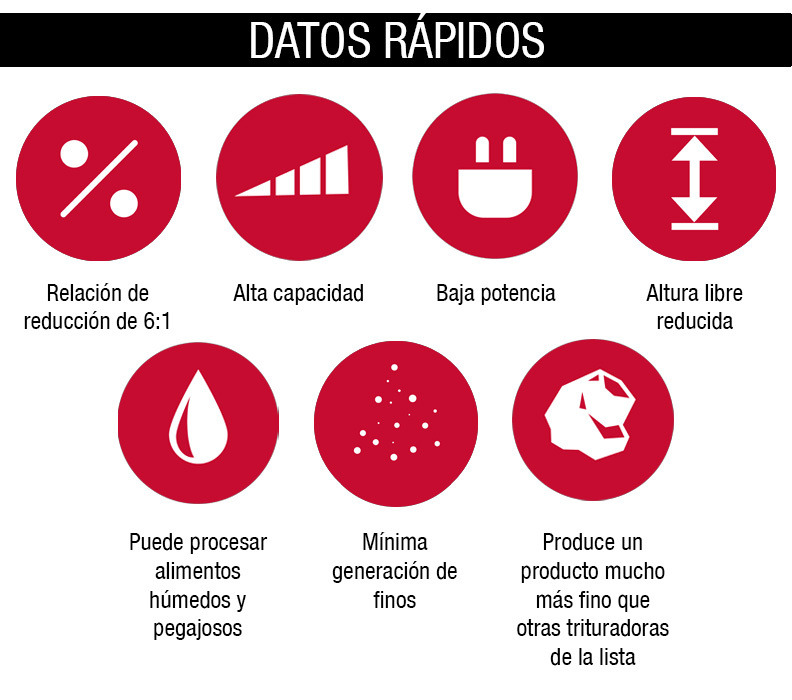
Chancadores de rodillos de dos etapas
Los chancadores de rodillos de dos etapas, como los chancadores de rodillos triples y cuádruples, también son equipos accionados por correa. Son capaces de efectuar el chancado primario y secundario, o secundario y terciario, con solo pasar una vez a través de un único equipo.
Los chancadores de rodillos triples y cuádruples reducen el material de alimentación en bruto hasta lograr tamaños aptos para la comercialización.
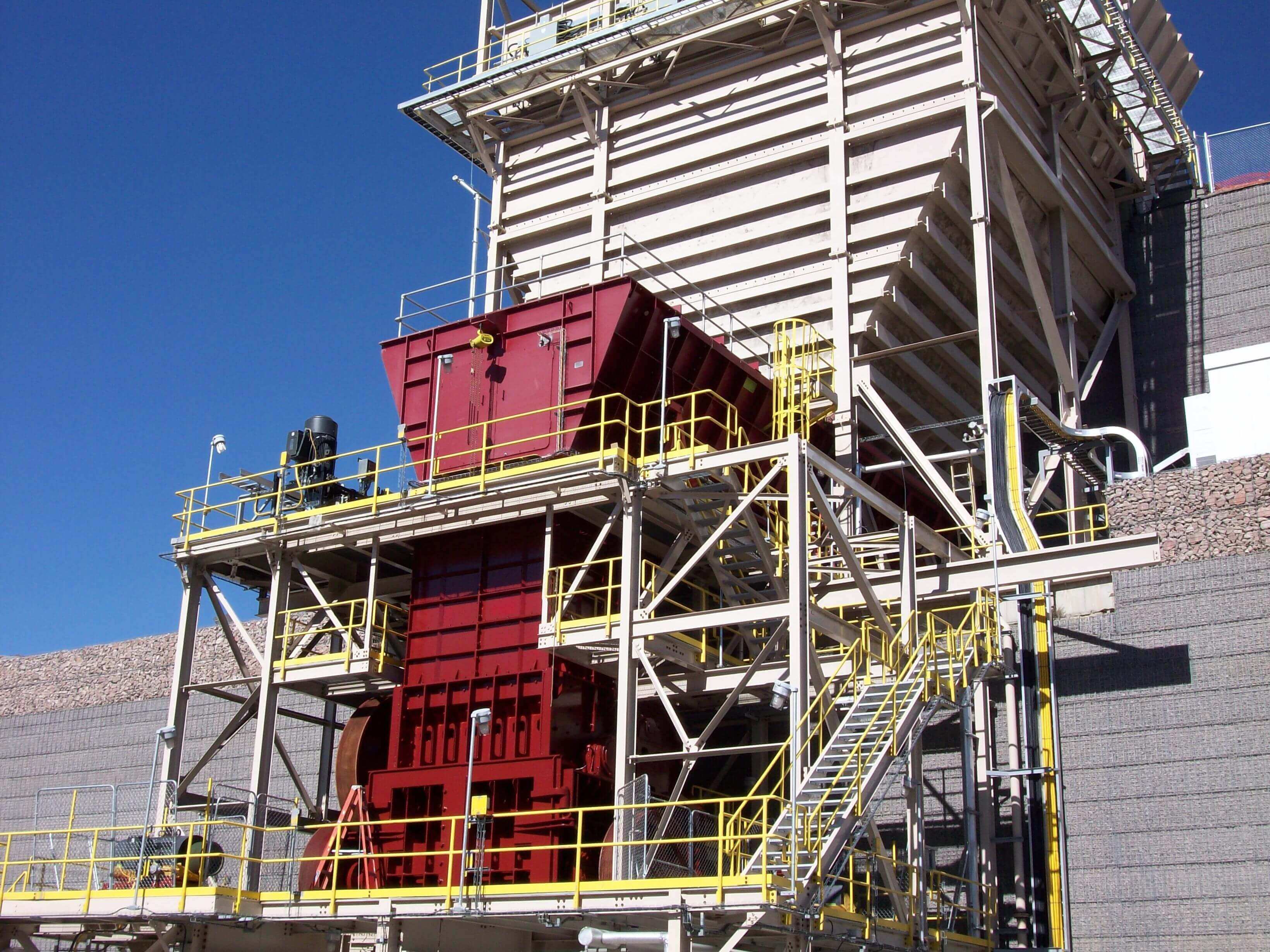
Según el diseño, la etapa primaria del chancador consiste en un rodillo simple o una configuración de doble rodillo. En la etapa primaria, se recibe el material de alimentación y se efectúa la reducción inicial antes de llegar a la etapa inferior secundaria.
La etapa inferior secundaria de cualquiera de los modelos consiste en una configuración de doble rodillo, que recibe el material desde la etapa superior y reduce el producto hasta alcanzar el tamaño final.
El diseño de dos etapas, en combinación con la configuración adecuada de dientes, genera un producto uniforme y cúbico con un porcentaje mínimo de finos. Una mayor velocidad de los rodillos, que es posible gracias al uso de correas de transmisión, permite alcanzar una enorme capacidad de producción.
En general, se recomienda un chancador de rodillos cuádruples para el material de alimentación de tamaño mediano, mientras que el chancador de rodillos triples, con su rodillo simple en la etapa superior, resulta eficaz a la hora de manipular material de alimentación de mayor tamaño. Estos equipos hacen el trabajo normalmente asignado a dos chancadores por separado.
Los tamaños de alimentación típicos varían de 18" a 72", con un tamaño de producto final de entre ½" y 3".
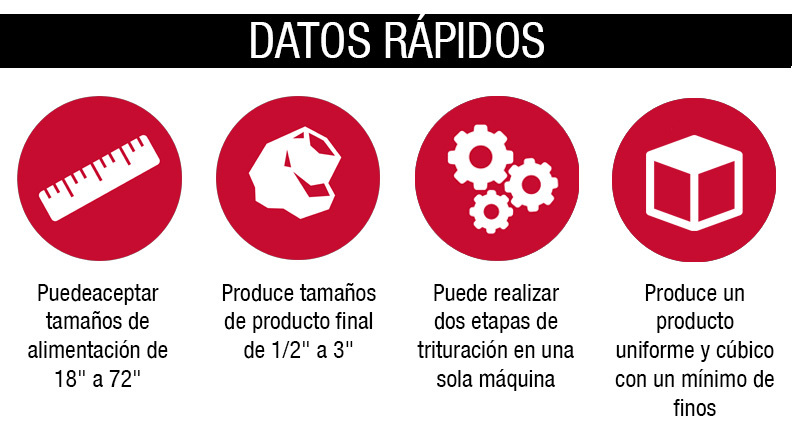
Cómo seleccionar el chancador primario adecuado
Son muchos los factores que entran en juego a la hora de seleccionar los equipos de chancado primarios adecuados y, en numerosas aplicaciones, hay más de una opción correcta.
Comuníquese con un fabricante de chancadores para revisar los detalles de sus aplicaciones. Ellos podrán ofrecerle una descripción general de todas las opciones disponibles y brindarle una recomendación profesional para su proyecto carbonífero.