Even though a Separator™ is a modified version of a Hydrocyclone, there is a difference in how they work. Because of the variance in functionality, they each fit certain applications better.
When trying to decide when to use a Hydrocyclone versus when to use a Separator™ in a sand plant, it can be helpful to look at the differences between them.
When to use a Hydrocyclone

A Hydrocyclone, or commonly called a cyclone, is more widely known and used.
The ideal condition for a cyclone is steady feed in regard to flow rate and solids. The steady flow rate is essential to maintain the desired pressure to make the predictable and repeatable separation.
Changes in the flow rate have a direct relation to the inlet pressure. High pressure will send a smaller particle into the underflow, while a low pressure will let a larger particle into the overflow.
For fines recovery
In some applications, a Separator™ can be used almost as effectively as a cyclone in regard to performance, but fines recovery is one area in which a cyclone is preferred.
A cyclone can operate at a pressure higher than 15 psi. This is important when looking to capture as much material as possible. The higher pressure will increase the centrifugal forces on all the particles through higher angular speeds.
With the higher centrifugal forces spinning smaller particles to the wall of the cyclone, finer particles will report to the underflow.
For feeds with consistent densities
When the solids content in the slurry changes, the effects are seen in the underflow. The size of the apex controls the water split between the underflow and the overflow.
In many applications, a secondary goal is to have the least amount of water reporting to the underflow.
While the underflow in a cyclone will not get as high of percent solids as a Separator™ can achieve, it can still remove the majority of the water when the proper apex is selected.
When the apex is not sized properly to the ratio of solids reporting to the underflow and the amount of solids is too great for the apex to handle, one of two things will happen:
- Roping in the underflow
- An increase in fines bypass to the underflow
Roping
Roping in the underflow happens when the amount of solids is greater than what the apex can handle. This causes the air core to collapse and the cyclone separation is no longer efficient.
Roped cyclone underflow (left) vs. ideal cyclone underflow (right).
In situations where roping can have significant impact on a downstream process, safeguards may be needed or Separators™ could be used. The chance to rope on a Separator™ is drastically reduced due to its oversized apex.
Increase in fines bypass
In the opposite direction, when the solids in the slurry decrease, more water reports to the underflow. This situation will increase the amount fines into the underflow since water will always carry some fine particles no matter what the cut is.
With more water, there is an increase in fines bypass to the underflow.
In order to receive the best performance out of a cyclone, the feed percent solids (also called density) should stay relatively constant.
For sizing
In situations where sizing is the diving factor in selection, the cyclone should be looked at first. This is especially true if the underflow does not need to be tightly controlled or if it is diluted back down below 50% by weight.
Some of the applications that fall into this scenario include de-sliming before a Classifying Tank, Screw Washers and counter-current classifiers (i.e. Hydrosizers™).
Having a cyclone in front of these type of applications can decrease the required sized of the subsequent equipment. This is accomplished by removing the unwanted fines while retaining the desired size fraction.
These applications are similar to using a scalping screen to reduce the load on a sizing screen.
When to use a Separator™
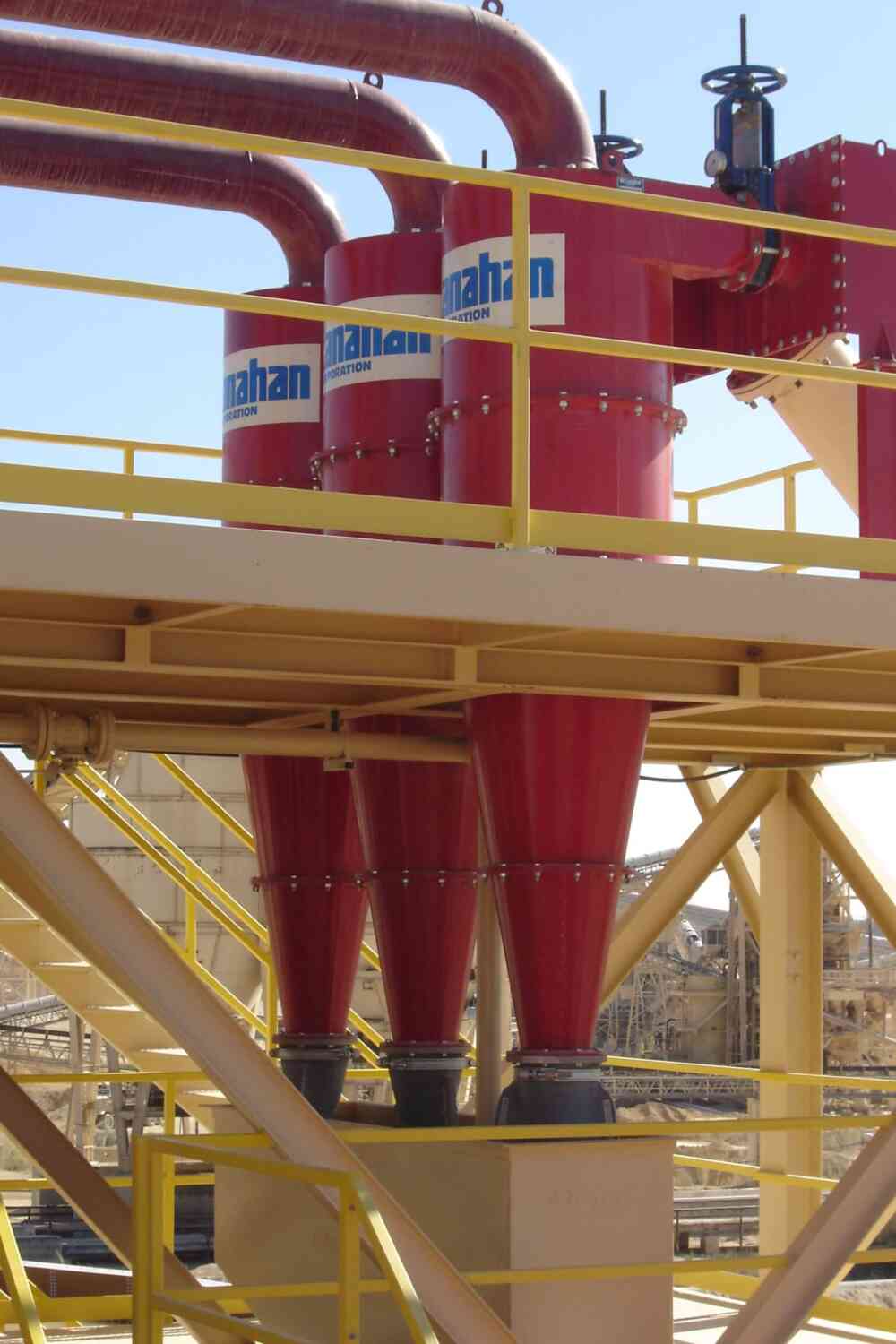
Separators™ were created to separate water from solids using a syphon to draw the water up through the vortex finder.
This method of creating the updraft to perform the separation limits the upper pressure in the range of 14 to 15 psi.
Applications that need predictable percent solids in the underflow or have large fluctuations in the percent solids in the feed are an ideal fit for the Separators™.
The range of feed density can fluctuate between 1% and 25% with little effect on the performance Separator™.
By removing the need for an air core, higher underflow densities can be achieved, as the solids will build up in the apex area above the underflow regulator.
For creating a stackable product
The main reason to use a Separator™ is to achieve a dry underflow. For this reason, a Separator is a good fit to stockpile material without additional equipment.
Separator™ discharging to stockpile.
When describing the underflow from a Separator™, the term “stackable” is most used. Although there is still some water in the underflow, the material will make a pile. This is ideal when the stockpile can be left alone for one or two days to allow additional water to drain away.
For producing a drip-free product
When the material cannot be left for a couple of days, a Separator™ and Dewatering Screen combination can produce a “drip-free” product.
Drip-free means that if you were to take a handful of the sand and squeezed, no water would come out.
Separator™ feeding Dewatering Screen.
This combination of Separator™ and Dewatering Screen removes the most water, short of using a filter and/or a dryer, preparing the final product for bulk storage or hauling.
While a cyclone can be used in the combination, as it is for fines recovery, it will create more wash-through of the fine fraction of the material.
For removing moisture
Some equipment, such as Attrition Cells, operates best when the percent solids in the material is controlled.
In this case, a Separator™ will actually remove more moisture than needed by getting the underflow consistently in the range of 75% to 79% solids by weight.
Separator™ feeding Attrition Cells.
An Attrition Cell will operate in the range of 65% to 75% moisture, but it is normally easier to add water to ensure proper operation.
While a cyclone can achieve an underflow density of up to 70% solids by weight, any fluctuations in the feed will cause inconsistences in the process.
The right choice
When the feed density is consistent and sizing is the highest process requirement, a Hydrocyclone is the right choice. High pressure requirements above 15 psi will automatically shift the choice to a cyclone.
A Separator™ fits the application when the underflow needs to have as little moisture as possible or when the feed density will have large swings.