Tailings. Refuse. Gob. Even to those not involved with the mining industry, it is obvious by the very words — rejects, slimes — that we probably won’t see red carpet stars adorned with, majestic high rises built from, or energy production fueled by tailings or any of its other worthlessness-invoking monikers. We mine because the materials we extract have value and demand. As concentration and refinement processes reduce these values to ever smaller volumes, we discard the barren or low-value materials and, by human nature, focus more on the values: the gold, the clean coal, the competent aggregate.
It’s no revelation that past practices of tailings “mismanagement” by mining companies haunts every sector of the industry to this day. What most people don’t get, though, is that we have by and large been very cognizant that to remain in business, to open new properties, to sustain modern living, the way we deal with or plan to deal with tailings is as paramount to the success of the venture as the deposit itself.
The best way to deal with tailings is to answer the question “What do you envision as the long-term solution?” This will often depend on the characteristics of the tails. If the tailings are comprised of relatively coarse particles (+38 microns), then the answer may be as simple as pumping them to cyclones for recovery and dam building with the fine cyclone overflow being impounded behind the dam.
This method has, for many decades, been employed to both collect/store tailings as well as clarify water for reuse in the process plant. What could possibly be cheaper than to dig a hole or build a dam and create a space for the waste generated by our activities? There are certainly costs associated with this plan. Two of the most frequent laments are: “We don’t have enough screens,” and “Our ponds are running out of space.” Dredging a pond to create more room for incoming tails may not be an everyday operational cost, but when the time comes, the piper wants his cut. Of course, an additional pond could be opened, but space and/or permitting might not be possible. Additionally, there is the potential to be covering up reserves that you may need to get to one day and the loss of process water due to evaporation or percolation.
Besides the costs associated with the pond solution, there are also risks. Social risks include placing people on or near the water while maintaining the pond or building ever higher impoundment structures. Graver social and environmental impacts from impoundment failure are real and should weigh heavily into any risk analysis. It's our industry’s obligation to reduce these risks as much as possible.
Thickeners
If the tailings are finer (-38 microns) and if ponds are still the desired method for storage, it may be worthwhile considering a thickener to prepare the tails before sending the entire stream out to a pond. The thickener has the benefit of reducing the total volume headed to the ponds as well as returning a majority of the process water to the plant immediately. In processing operations today, there are three basic styles of thickeners:
- High rate
- High density
- Paste
Each of these thickeners share a similar operation as far as feeding and collection of the settled solids. Feed enters the unit via a feedwell, which is designed to provide optimum mixing and residence time for contacting suspended solids with a flocculant and allowing flocs to form. The flocculated suspension then flows out of the feedwell and is dispersed across the area of the tank. The flocculated solids fall while clarified water rises up over a peripheral weir for collection in a process water tank. The flocculated solids collect in the cone section of the thickener. To gather this mud and bring it to a central discharge area, these tanks use slowly rotating rake mechanisms. It should be noted here that lower yield stress muds, such as those produced in a high rate thickener, require less torque to move these rakes through the mud.
Again, the selection of a thickener to fit your needs depends heavily on what the plans are downstream for the resulting mud. As we progress from high rate to the paste thickener, the underflow solids concentration possible will increase. Here is where the concept of yield stress comes in to play. In rheology, the yield stress is the minimum amount of shear stress required to initiate and sustain flow. The higher the underflow solids concentration, then the higher the yield stress. Mine planners can best determine the thickening process by starting at the end of the system and working backward. Answers to the questions regarding how the tails are to be stored, placed, transported, and produced are key to honing in on the thickener design.
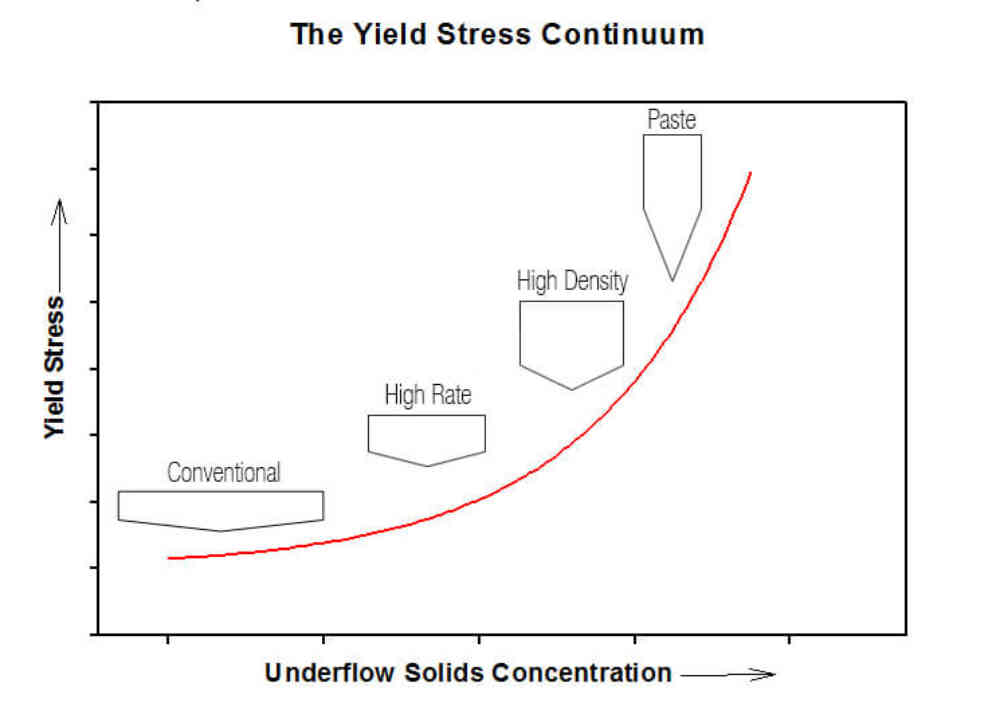
High Rate Thickeners
High rate thickeners are used to provide lower yield stress muds. These are muds that can be easily pumped and flow out over relatively large areas under gravity conditions alone. They are by far the most used thickener in the industry today and provide operations with a relatively inexpensive way to recover water and transport thickened tailings to an impoundment. Water and solids will further segregate in the impoundment area, which will need to be dealt with either by return to the process plant, evaporation or discharge.
The high rate thickener, whether it sits flat on the ground or is elevated, collects mud in a shallow cone, generally between 9 and 12 degrees. The side walls for these units are the lowest for the three styles of thickeners and offer the shortest residence time for the mud to compact.
High Density Thickeners
High density thickeners are used when you need a bit higher solids concentration or mud yield stress. The thickeners are sized to give longer mud residence times to allow for further compaction, and the rake drives and supporting structures must be designed to deal with a higher yield stress mud.
Both the high rate and high density thickeners are generally supplied with rake lifting mechanisms to pull the rakes up out of the mud should a high torque condition occur. The torque is constantly monitored. As the torque decreases due to higher pump-out rates or reduced inflow of mud, then the rakes are indexed back down to their lowest position.
Paste Thickeners
Paste thickeners offer the operator the ability to produce the highest underflow concentrations and yield stress muds possible with gravity settling alone. These tanks typically have aspect ratios (height:diameter) of 1:1 to 1.5:1 and steep underflow cones ranging from 25 to 60 degrees. The principal design consideration for a paste thickener is the mud residence time. Paste is a term used to describe a mud from which there is little to no further segregation of free water from the solids. To further enhance the formation of the paste, the rakes are often equipped with vertical rods or angles that protrude upward in the tank. These pickets are used to cut channels through the mud to allow passage ways for trapped water to be liberated from the mud as it compacts.
Due to the high yield stress of the muds, paste thickeners must often be equipped with special pumping arrangements for mud removal and transport. Positive displacement pumps such as piston or piston diaphragm pumps are often used. However, many mineral based muds will exhibit a viscosity characteristic known as rheomalaxis. This is the irreversible thinning of a slurry with time as it is subjected to shear. In such cases, the underflow cone of a high density or paste thickener may consist of two process pumps. One pump has the duty of withdrawing sludge and pumping it back into the cone via a shear loop. This serves to reduce the yield stress of the mud. The second pump is employed to move the lower yield stress mud from the thickener and transport it toward the placement area. Rheomalaxic muds can make dealing with the paste less expensive as centrifugal pumps may be employed and placement can make better use of the area available for the material to flow. Additionally, if the placement of the low water content mud is made in shallow lifts, drying time for the mud can be greatly reduced.
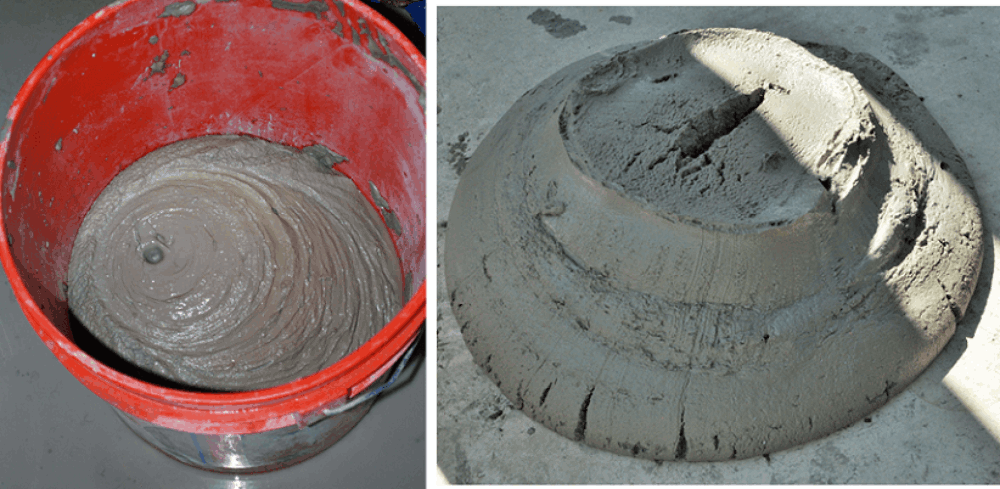
So why would someone want to go through the trouble of creating these higher yield stress muds? There are, of course, several reasons why this would be considered, including higher recovery of water and usefulness in mine backfill, but a reason that has great benefit is the stability of the mud once in place. Higher yield stress muds pose lower risk of impoundment failure. The benefits of this are well understood.
Success of your thickening system really requires that a sound effort is made to understand the tailings. This is done by a number of suppliers through detailed settling and viscosity analysis of the muds. Methods for continuous settling tests have been developed in the past 15 years and have been shown to give a much better set of data for sizing and selection of the thickeners than static tests.
If we progress on in the thickening continuum, where do we go after paste thickeners? We now pass into an area where forces other than gravity alone must be introduced to create higher solids concentrations. This is the realm of filters and centrifuges. Most recently, the coal and aggregate industries have discovered recessed plate presses, an old technology used by the wine and olive oil industries but redesigned for successful use by mining operations. Of particular interest with this technology is the ability to prepare tailings, without additional chemicals, that allow dry stacking and total elimination of impoundments to restrict flow of muds and water.
Recessed Plate Presses
At its most basic level, the filtration process of a filter press consists of covering two plates with filter media, applying enough force to create a seal between the two filter plates, and then using a feed pump to supply the pressure necessary to pump the slurry into the cavities formed between the two sealed plates. The filter cloth prevents solids from escaping from the plates while allowing the filtrate to pass through the openings in the filter media. Once the chamber is packed full of solids, the feed pump stops, the pressure sealing the plates is released and the filter plates are pulled apart from each other, allowing the dewatered cakes to discharge via gravity.
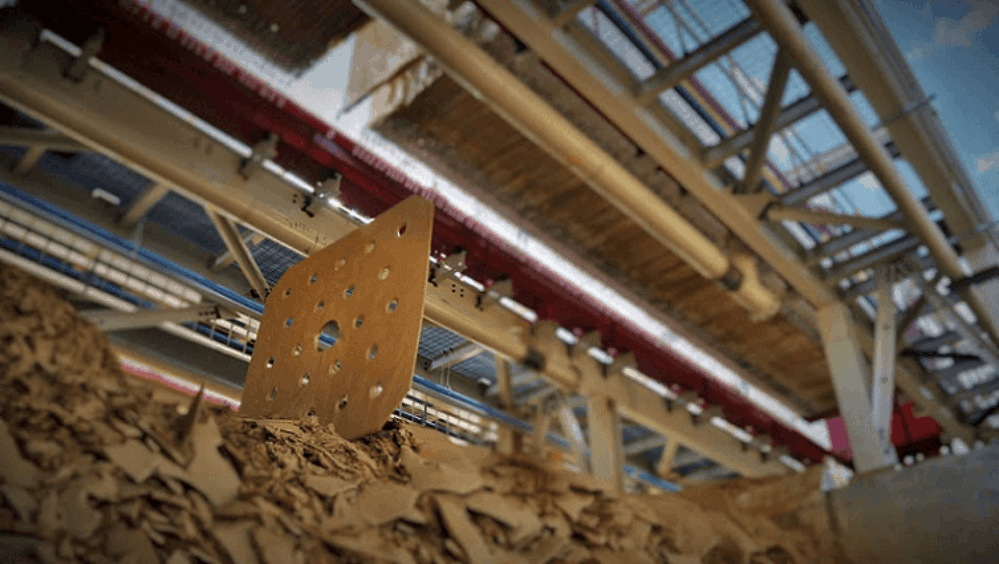
It is a common misconception that these presses squeeze the plates in order to dewater the cakes. In actuality, there is no movement of the press during the formation of the filter cakes. Plates connect together to form a seal, and the feed pump supplies the necessary pressure to dewater the fine solids. The only movements of the press during operation are typically for opening the press to discharge the cakes and closing the press to start another cycle.
The simplicity and limited movement of filter presses is what lends them to high-levels of automation and reliability. The ability to select cycle times, cake thickness, feed pressures and plate styles are what allow filter presses to achieve much drier discharges than many other competing technologies.
The recessed plate press operation is a batch process and when asked, “What is the capacity of the press?” we must answer that the capacity is strictly a function of the cycle time. Each press comes with a finite volume to form cakes. Shorter cycle times (the time it takes to go from start to start) are promoted by:
- Optimizing cake thickness – Thinner cakes can form quicker than thicker ones.
- Higher permeability of solids – The easier it is for water to pass through the cake, the quicker the filtration stage.
- Optimum cake moistures – If 18% moisture is achievable in 40 minutes, is 20% after perhaps 30 minutes acceptable?
- Higher feed solids concentrations – The less water to push through the cake, the more rapid cake formation.
- Faster opening and closing – Discharging cakes and resetting the press for the next fill stage can play a big role in press capacity on a tph basis.
Once again, testing your material is always a good place to start when looking at a recessed plate press. Most manufacturers will have facilities for in-house testing to determine, quite accurately, filtration times and moistures as a function of feed solids concentration and cake width.
Filter presses are frequently categorized into two main styles: overhead beam and side beam. Each have their own advantages and disadvantages.
Overhead Beam

- The filter plates hang from overhead beams.
- No parts on the sides of the press, providing unobstructed access to change filter cloths on the press without plate removal.
- Much wider plate openings often exceeding 3' (0 .9 m ) between the plates. This creates more movement to aid cake release while also allowing easier access for cloth washing and inspection.
- Dynamic loads are typically isolated from the beams of the press using tension shafts in various configurations.
Side Beam
- The filter plates are supported by beams running along the side of the press.
- Easier to implement shaking systems for applications requiring shaking systems.
- Lower upfront cost.
- Less access to plates for cloth washing and inspection. Automatic wash systems should be considered more heavily with side beam style presses due to limited plate access.
You may also be interested in
Best Practices for Tailings Management
[EBOOK]
Every mine discharging tailings needs to have a tailings management plan that covers how the tailings will be disposed or stored, how that facility will be maintained even after the mine shuts down and how emergency situations will be handled should the facility fail.
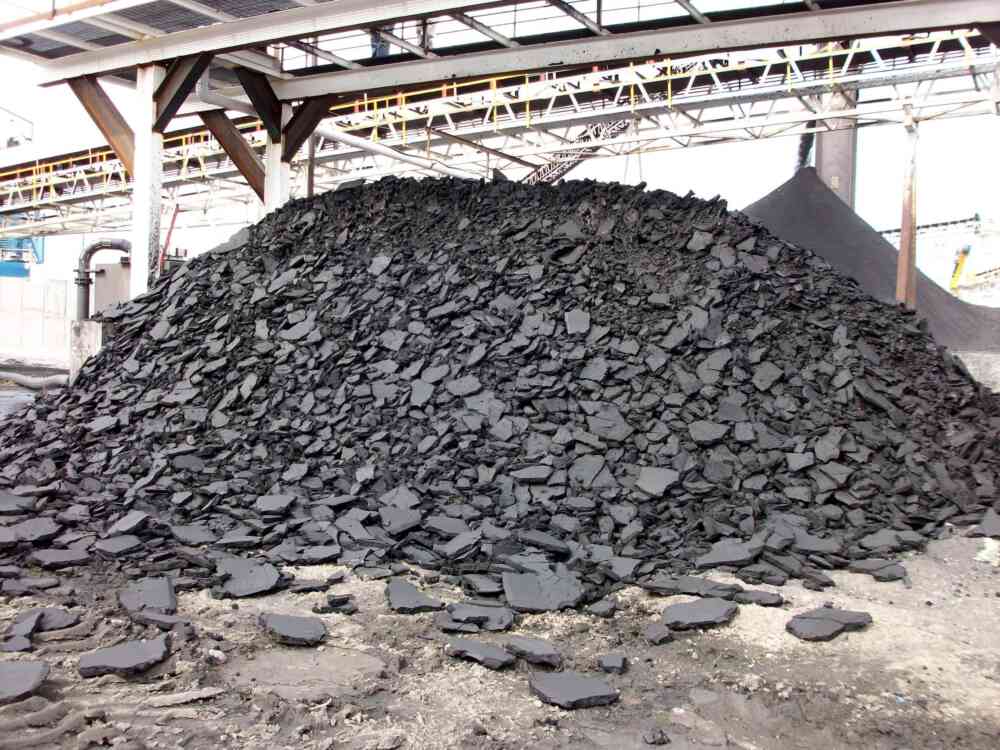