Falling Stream Samplers are a style of sampling system that collects representative samples from a free-falling material flow that is traveling through a trajectory of some sort, such as the discharge of a conveyor.
The term “falling stream” encompasses a variety of different types of samplers, the most common of which include:
- Baffle Plate Samplers
- Carriage Drive Samplers
- Rotary Head End Samplers
Baffle Plate Samplers
Baffle Plate Sampling Systems maintain separation between the main process flow and the sample flow using a moving plate. The baffle plate acts as a physical barrier between the process flow and the side where the samples are ultimately diverted. A cutter mounted in the center of the moving plate collects samples when the plate moves from side to side and diverts that material out into a collection hopper to the next stage of the sampling process.
There are two styles of Baffle Plate Sampler:
- Vertical entry
- Tangential entry
In a vertical entry system, the material enters the sampler in a free-falling condition. The baffle plate then moves in and out of the material stream, with the cutter collecting the sample for discharge.
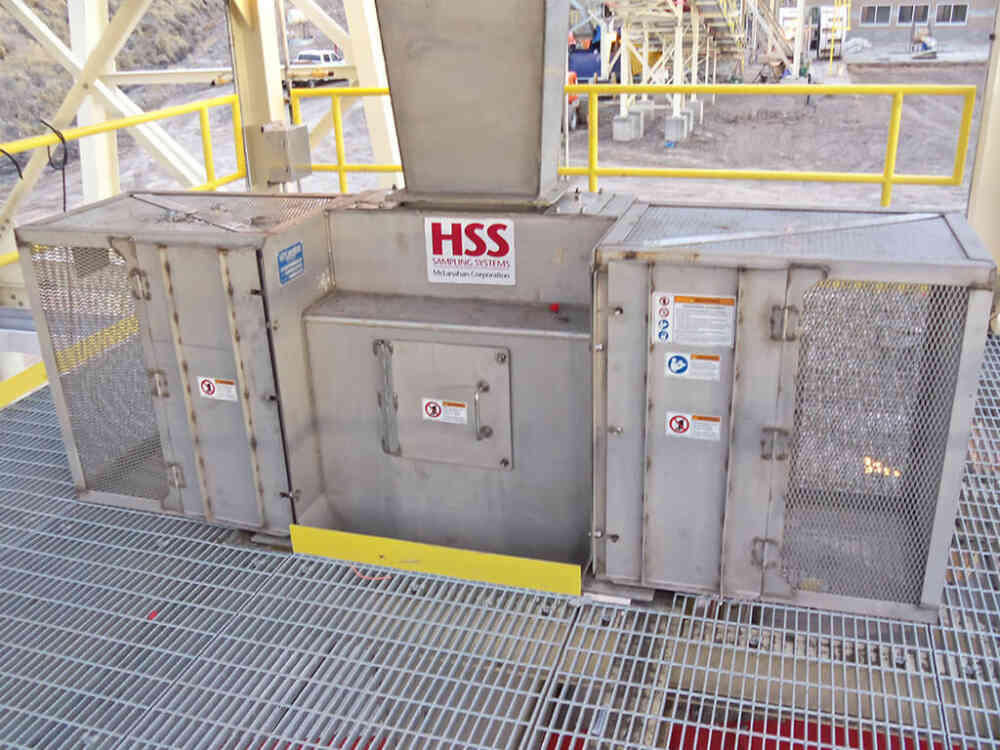
The tangential entry style is similar to the vertical entry machines. The main difference is that sample from the main process flow is intercepted during its normal trajectory from a belt conveyor as opposed to a free-falling condition. The main process flow is also in constant contact with the baffle plate during normal operation, requiring wear material to be added to the process side of the baffle plate.
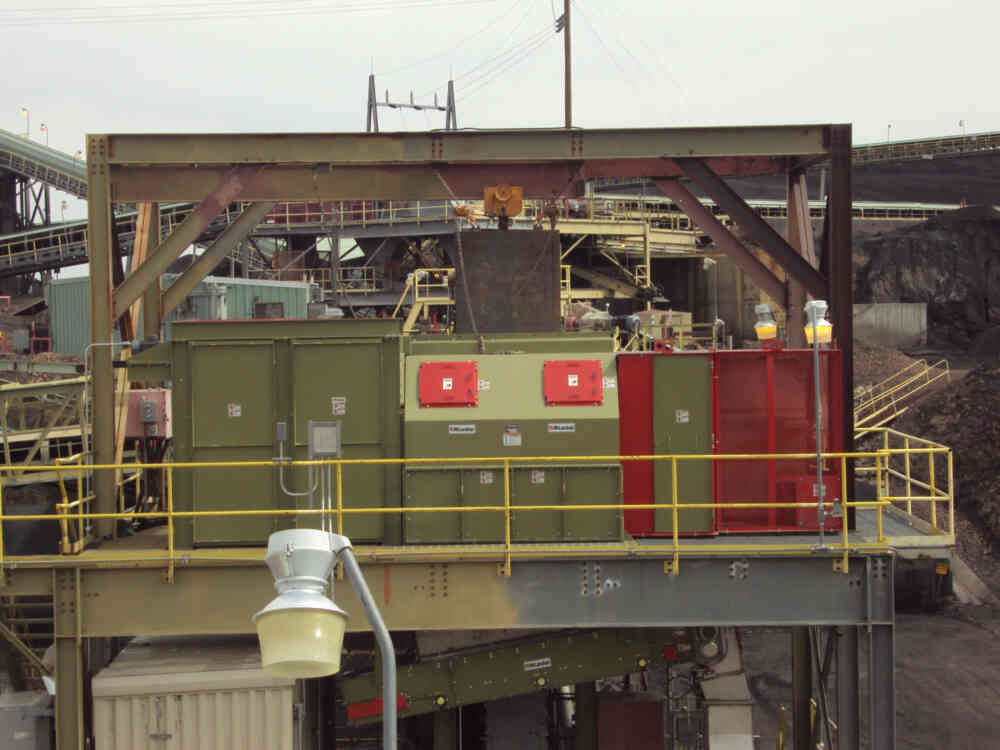
Baffle Plate Samplers with a vertical entry are quieter than the tangential entry style because the material isn’t constantly hitting into the baffle plate while the plant is in operation. However, the tangential entry is often a more attractive option because the material can enter the sampler straight off the main conveyor. With a vertical entry sampler, the material has to be funneled from the main conveyor into a vertical orientation so that it is falling straight down. The tangential entry sampler can be installed closer to the main conveyor, so less headroom is required.
Baffle Plate Samplers are relatively simple in operation and generally require less regular maintenance than other types of samplers. These machines are suitable for high tonnage process applications. They are commonly used in coal, potash and applications with an excess of fine, airborne particles that need to be kept separate from the sample side so as not to contaminate the sample. However, Baffle Plate Samplers can be used in any minerals processing application where the space to the sides of the sampler isn’t limited.
Carriage Drive Samplers
Carriage Drive Samplers are common in many types of mineral applications. They feature a cutter attached to a carriage drive mechanism that moves the cutter back and forth through the material stream to collect the sample.
There are two main styles of Carriage Drive Sampling Systems:
- Overhead carriage
- Horizontal carriage
Overhead carriage samplers are installed on top of a conveyor discharge hood. The cutter hangs below the drive unit to intercept the main process flow on its normal trajectory.
Overhead carriage samplers can incorporate a variety of cutter designs. The type of cutter depends on the type of application (dry or wet process), the orientation of the sampler with respect to the material flow and the required discharge location/direction for sample material.
Horizontal carriage samplers are similar to overhead carriage samplers. The key difference is that horizontal carriage machines are intended to have a cutter that projects perpendicularly from the drive unit. This results in a relatively compact, low-profile sampling option, though some vertical clearance below the conveyor discharge is often still required.
Both overhead and horizontal carriage samplers can be used for primary, secondary, tertiary, or quaternary stages of sampling, and can be used in both wet and dry process applications. Bottom-dump-style cutters are the commonly used in dry applications, but other cutter designs are possible, particularly in wet applications.
Bottom-dump cutters pass through the material stream to collect samples, stopping at each end of the cutter travel to dump the sample via a door at the bottom of the cutter. Another type of cutter is a diverter-type cutter. The conventional type directs sample material to another area of the sampler or to another machine in the sampling system in the direction of the material flow The reverse-spoon type diverter cutter re-directs the sample in the opposite direction of the material flow, usually to an area under the head pulley area of the main conveyor.
Carriage Drive Samplers are typically less of a capital investment compared to other types of Falling Stream Samplers since they are not as large and do not require as much space to implement – mainly because they do not incorporate a baffle plate in the design. They typically fit better into existing plant layouts with fewer design changes.
Rotary Head End Samplers
Rotary Head End Samplers are installed into the front of a conveyor discharge and feature a cutter that rotates on a hollow shaft. The cutter rotates downward though the material flow trajectory as it is discharged from a conveyor, collecting a sample and dumping it into the hollow shaft as it rotates back upward into its parked position. The hollow shaft directs sample material into a collection area or into the next machine in the sampling system.
The main benefit of this style of Falling Stream Sampler is that it is fairly compact and can fit in areas with strict space restrictions.
Which style is best?
Falling Stream Sampling Systems are available in a variety of designs, with different drives and cutter styles, as well as in a range of sizes and shapes. Baffle Plate, Carriage and Rotary Head End are three common types of Falling Stream Samplers, and they themselves are available in a variety of different configurations.
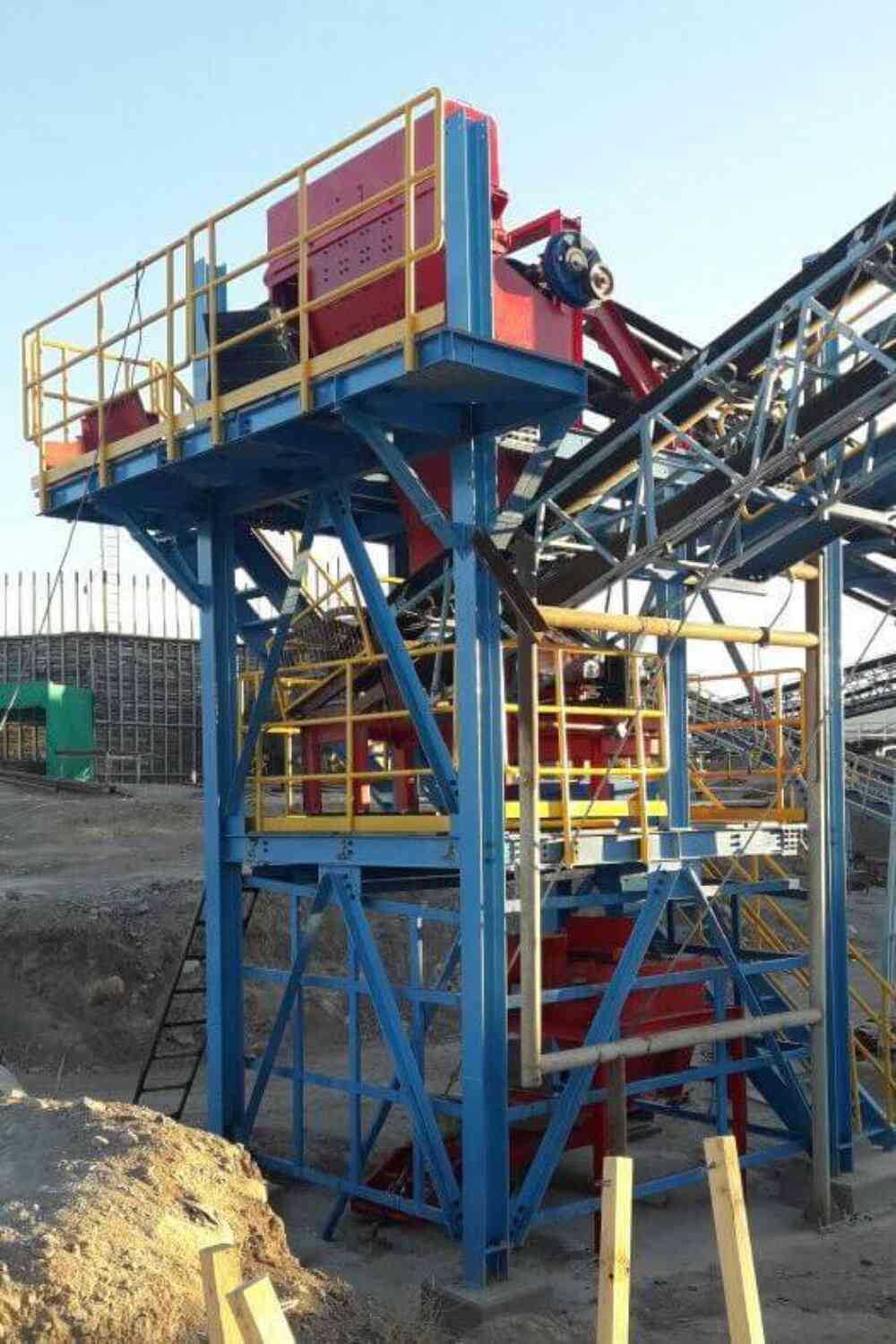
The Baffle Plate style is simple to use, low maintenance and provides separation of sample material from the process flow. The vertical entry model offers a quieter option, while the tangential entry model requires less headroom. The carriage drive style is cheaper than other Falling Stream Samplers, with the horizontal carriage model offering an added benefit of low headroom. The Rotary Head End style offers a compact solution for fitting into applications where space is extremely limited.
The best type of Falling Stream Sampler for an application will depend on the material to be sampled and available space. From there, the type of sampler can be chosen, along with the size of the machine, cutter type and drive arrangement.