Since the inception of confined dairy housing, dairy producers around the world have used “waste” materials for dairy cow bedding.
For dairy farms in proximity to the lumber or furniture industries, that waste was wood shavings or sawdust.
In wheat producing areas, straw was the answer.
In Michigan — a peninsula surrounded by fresh water lakes — it was (and continues to be) sand.
In the early 1990s, the widespread adoption of sand bedding in Michigan revealed a drawback of sand bedding — manure handling.
Producers found sand wore out equipment prematurely, clogged pipes and filled manure storages.
So prevalent were these issues, Michigan producers lobbied the state legislature to allocate funds to study and solve issues related to handling sand-laden manure, and the legislature followed suit.
In the lab
Early university research at Michigan State's Department of Agricultural Engineering showed what still holds true today: Settling sand from manure slurry is the most effective means of separating sand from manure and mixing recycled water. This is because grains of bedding sand are 2.5 times more dense than manure.
In laboratory settings, researchers determined just how much water is required to allow sand grains to settle. In fact, the settled sand in these conditions was remarkably clean.
The challenge was how to scale-up the process.
Industrial sand washing
The agricultural engineers at Michigan State University were aware that sand is commonly washed for the purpose of making construction aggregates — particularly as an ingredient for concrete and mortar.
Sand processing equipment, unlike traditional manure equipment, is designed to be resistant to abrasive wear thanks to the wear-resistant materials of construction and low operating speeds.
Recognizing the synergies between industrial sand washing and separating sand from manure, the Michigan State University engineers contacted McLanahan Corporation to partner in the development of a full-scale sand-manure separation system.
The laboratory process of diluting sand-laden manure to settle sand and reclaiming settled sand was incorporated into a commercially manufactured sand washer with modifications to achieve the removal of large, coarse organic solids like hay stems and corn kernels.
The first commercial Sand Separation System was commissioned at Green Meadow Farms in Elsie, Mich., in January 1998.
Developing a system
Just as a cropping system is more than just a tractor, separating sand from manure requires more than a sand separator. It is a system — a sand-manure separation system.
There are many things to consider with this system:
- How is manure conveyed to a Sand-Manure Separator?
- How is sand-laden manure metered into the Sand-Manure Separator?
- What is the source of recycled water for diluting sand-laden manure, thereby driving the sand-manure separation process?
- How is manure effluent pumped away?
- What are the sizes of the process tanks?
Answering of these questions led to the development of a complete line of sand and manure handling equipment, including:
These pieces of equipment were all tied together by providing producers with complete site-specific system designs.
Increasing sand recovery
Sand-manure separation systems proved to produce clean sand suitable for reuse with lactating dairy cows. The challenge was how to capture and recycle more sand since there are limits to how much sand can be captured simply by gravity settling.
Again, industrial sand processing equipment was the answer. The irony is that sand and gravel producers face the same challenges as dairy producers —they strive to produce as much clean product as possible without filling ponds with sand.
To increase sand recovery, Hydrocyclone separators are used to increase sand recovery. When integrated with existing sand-manure separation systems, sand recovery jumped from 85 to 90% up to 90 to 95%.
In fact, effluent from Sand-Manure Separators began to be used with anaerobic digestion systems. Yes, sand can be used with anaerobic digestion systems.
Traditional sand settling lanes and self-cleaning sand lanes
Recognizing the effectiveness of gravity settling, settling basins and sand settling lanes found prominence with some producers and remain popular today.
With no separation equipment required per se, sand settling lanes are viewed as a simple and “non-mechanical” means of sand separation despite the fact they rely heavily on payloaders to scrape, stack, condition and move sand.
Whereas sand lanes have been shown to be effective at sand removal, the cleanliness of the recovered sand is not to the liking of some producers since it is impossible to discriminate between clean settled sand and settled organic matter.
Self-cleaning sand lanes were developed as a way to rely on gravity settling while at the same time eliminating the need for payloaders to scrape, stack and condition sand.
Self-cleaning sand lanes utilize the same principle of settling sand down a long channel, but instead of using a payloader to periodically remove settled sand, the sand removal process is automated using mining-duty sand handling equipment, such as collection augers and Inclined Augers.
The result is sand settling lanes that produce clean sand.
Closed loop sand-manure separation
Obtaining recycled water on dairies was proving to be one of the biggest challenges facing producers with sand-manure separation systems since the source of recycled water was most often manure storage effluent.
When manure storages were full and a layer of liquid was present, sand-manure separation systems functioned well.
When storages were emptied in spring and fall, sand-manure separation performance suffered. What’s more, recycled water from manure storages had a really strong odor, being partially anaerobically degraded. Dairy producers needed a way to obtain recycled water from a source other than manure storages.
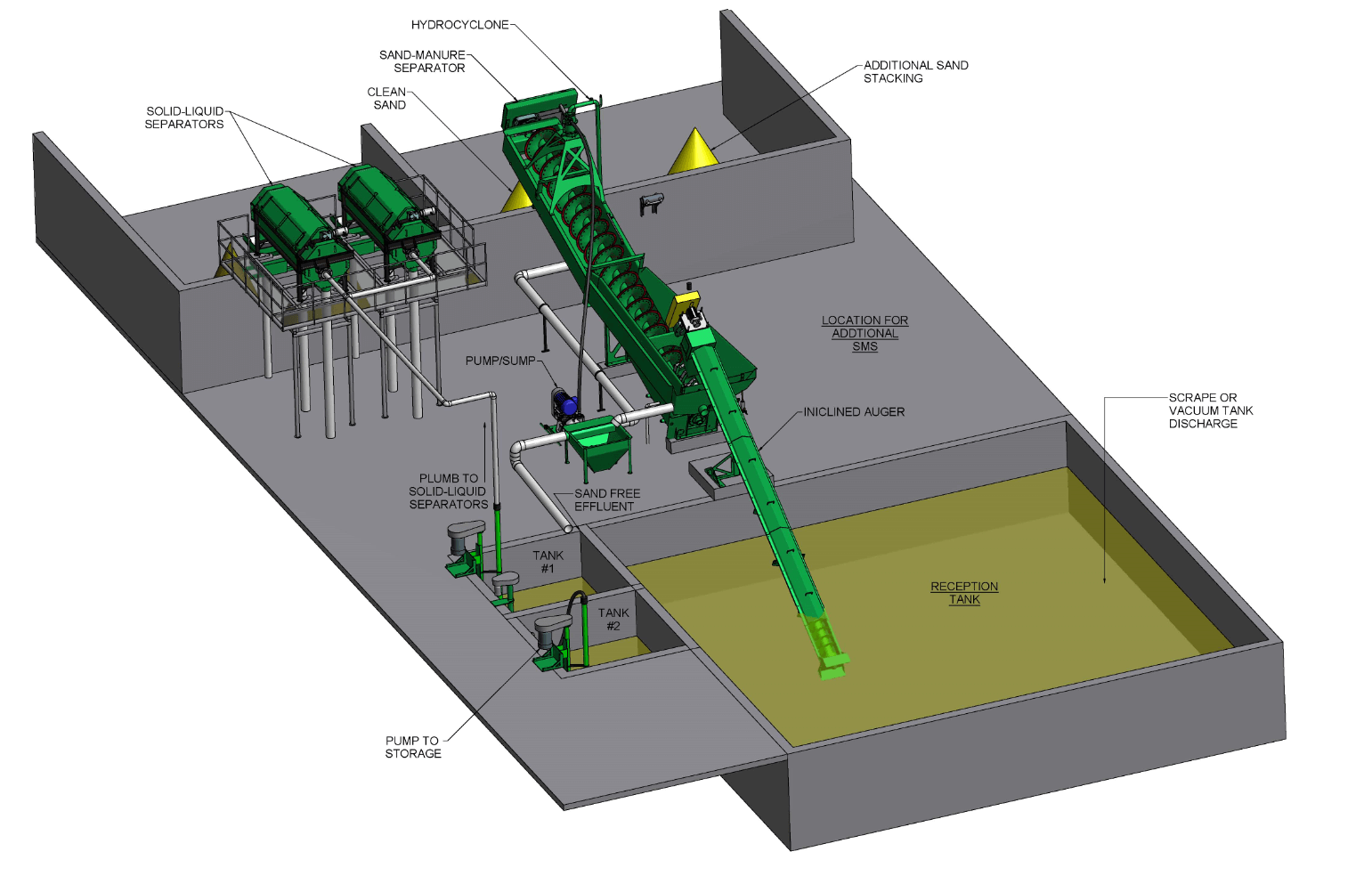
The solution was to perform solids separation immediately after sand-manure separation and reuse the liquid effluent from liquid-solid separation, all while blending in parlor water.
These closed-loop sand-manure separation systems now produced more, cleaner sand more consistently than ever before.
Cleaner, drier sand
Dairy producers are always striving to improve and enhance cow comfort knowing there is a direct relationship between cow comfort, milk production, milk quality and cow longevity.
Primary sand-manure separation systems produce sand and approximately 20% moisture. Ideally, this sand is allowed to drain by gravity for a period of two weeks to one month.
To increase sand dryness, vibrating Dewatering Screens, also used in industrial sand processing, were adopted into sand-manure separation systems.
Dewatering Screens decreased sand moisture to 12% while at the same time reduced organic matter content by another 50%.
Sand can be reused in one week or less, with some producers re-bedding with sand immediately after separation.
The net result of the cleaner, drier sand is a decrease in sand inventory and an increase in cow health.
Higher capacity and lower capacity sand-manure separation
The capacity of the sand-manure separation systems originally developed were based on the size of the farms requiring sand separation.
Since that time, dairies have grown larger, and many small farms still remain. To address the needs of all farms, the sand-manure separation system offering was increased to make sand-manure separation cost-effective for farms up to 500 cows.
At the same time, a system was developed where a sand-manure separation unit could handle 4,000 cows.
Both systems utilize all the system features that allow producers to maximize sand recovery and sand cleanliness.
The future
In all likelihood, dairies will continue to grow, as will the size and capacity of sand-manure separation systems.
To be certain, dairy producers are dedicated to excellence and continuous improvement. With an ever-present and increasing focus on cow health and milk production, there will continue to be a demand for still cleaner and drier sand.
And as sophisticated, advanced manure treatment systems gain prominence, so will the need for higher and higher sand recovery.
The future will also see an increase in robotic milking barns and less reliance on labor. Sand-manure separation systems will need to evolve accordingly.
It may have started out as a regional dairy management practice, but sand-bedded freestalls are now found throughout the world. From its meager beginnings in the laboratory to today’s small and large dairies, sand separation systems have changed to suit the demands of dairy producers worldwide.
Thanks to companies helped by innovative dairy producers, the sand-manure separation systems of 20 years from now will be different and higher performing than the sand-manure separation systems of today.