Introduction
Leftover concrete is a problem that all ready-mix facilities have, whether it is excess concrete after returning from a job or washout from cleaning the trucks at the end of a shift. Some facilities dispose of the leftover concrete at authorized landfills. Some pour the leftover concrete into blocks and other non-structural forms, while others allow the leftover concrete to harden in pits and then break it into smaller pieces for sale.
But what if you could recover the aggregate used in the leftover concrete for use in new ready-mix batches? What if you could further recycle the water for use on site, limiting the freshwater required for cleaning out trucks, washing down equipment, batching concrete and more?
With concrete recycling equipment, you can! Traditional aggregate processing equipment can be used to turn concrete washout into valuable resources, with various options available to meet your goals.
Here’s how different aggregate processing equipment in various configurations can be used to recycle leftover concrete.
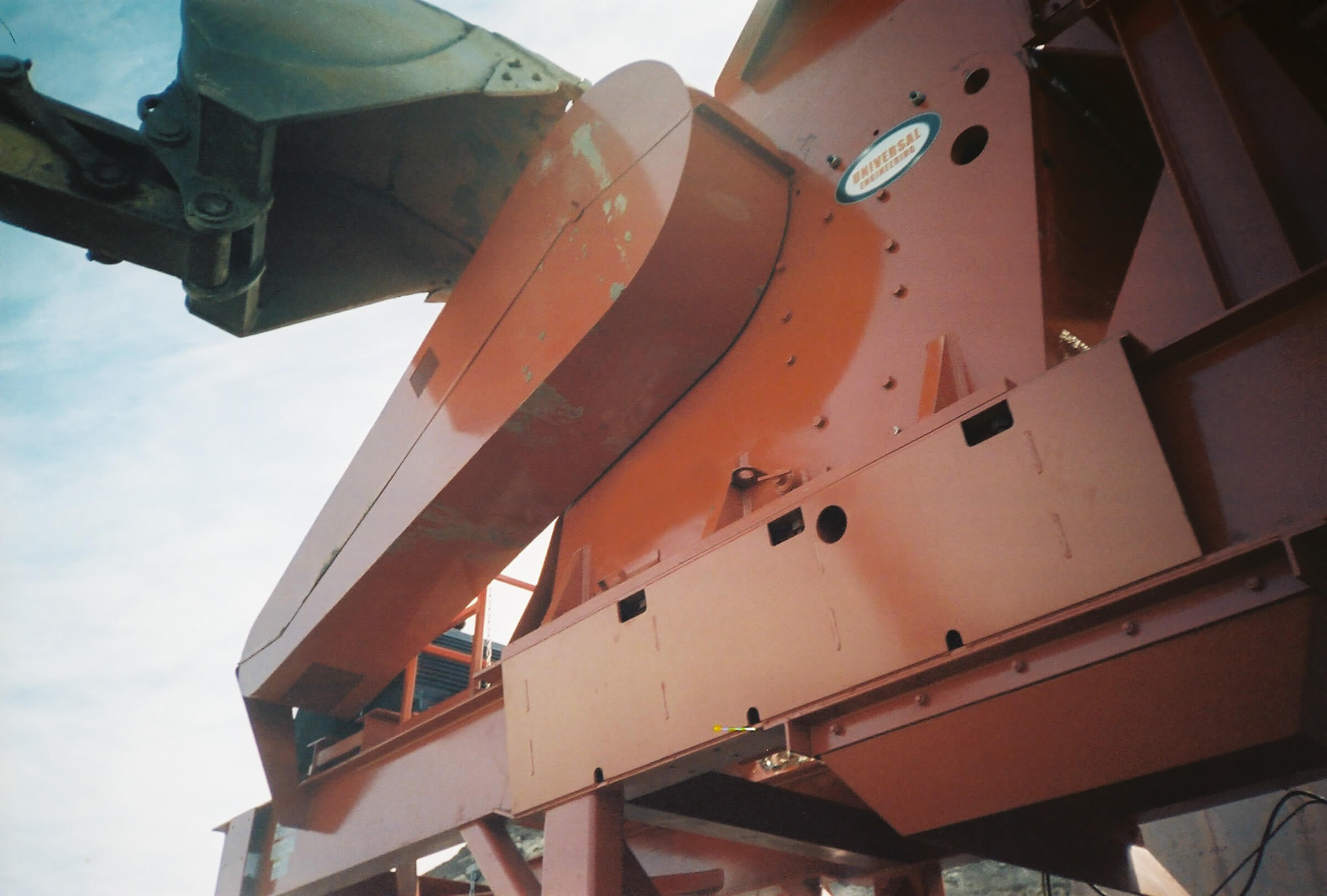
Feeders, crushers and screens
Crushing equipment is used to reduce larger particles into smaller sizes that are suitable for sale or further downstream processing. Material is typically introduced into the Crusher by a Feeder in stationary, mobile or skid-mounted configurations. Smaller Crushers that can be fed directly with an excavator or skid-steer are also available for crushing options. Sizing Screens can then follow the crusher to sort the material into various sizes.
Feeders, crushers and screens are ideal for producers who are pouring the leftover concrete into pits or rows and then breaking or chipping it into smaller slabs. Crushers can reduce the slabs into smaller sizes, while screens can sort the crushed material into various sizes.
Because crushed concrete contains dust and fines along with the sized aggregate, its end uses are limited. Crushed concrete can be sold and/or used for sub-base, drainage, erosion control, walkways, paths and landscaping materials.
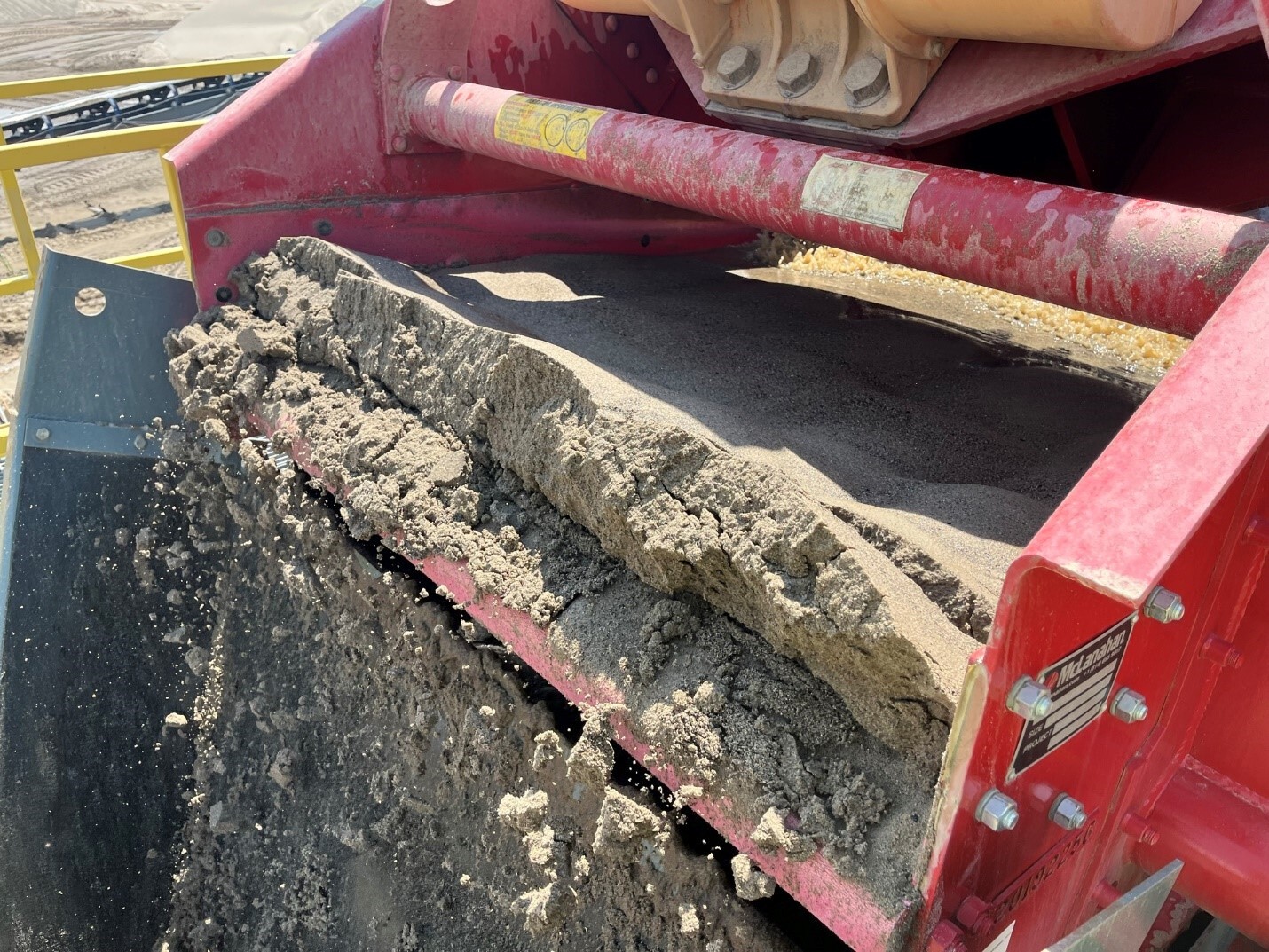
Aggregate washing equipment
To increase the value of crushed concrete for end use in a broader range of applications, washing equipment can be used to remove dust and fines from the sound aggregate. There are numerous types of aggregate washing equipment and numerous configurations to achieve the desired outcome. Types of aggregate washing equipment commonly used for cleaning crushed concrete include:
- Attrition Cells
- Blade Mills
- Coarse Material Screw Washers
- Log Washers
- Flat Bottom Classifiers
- Hydrocyclones/Separators™
- Hydrosizers™
- Fine Material Screw Washers
All this equipment uses water to clean crushed concrete, removing dust and fines.
The type of equipment appropriate for each application depends on the level of contamination in the crushed concrete. Simple washing can be achieved with Screw Washers and Hydrocyclones/Separators™. Tougher contaminants can be removed with Attrition Cells for the sand fraction and Log Washers for the coarse aggregate. Dewatering Screens remove excess moisture from the material ahead of stockpiling.
In some cases, multiple stages of washing or multiple pieces of equipment may be necessary to achieve the desired outcome. Compact, modular washing plants are also available for quick setup and ease of movement around site.
Water recycling and tailings management
Washing crushed concrete improves the value of the aggregate, but it also creates a waste stream consisting of the wash water and fines and dust that were removed during the washing process. Tailings management equipment, such as Ultra Fines Recovery Systems, Thickeners, Centrifuges and Filter Presses can be used to separate the solids from the liquid in the waste stream, resulting in immediately reusable process water and/or drip-free solids material that can be sold or used for site rehabilitation.
Tailings management equipment reduces the volume of material reporting to the settling ponds and, in some instances, can eliminate the need for settling ponds altogether.
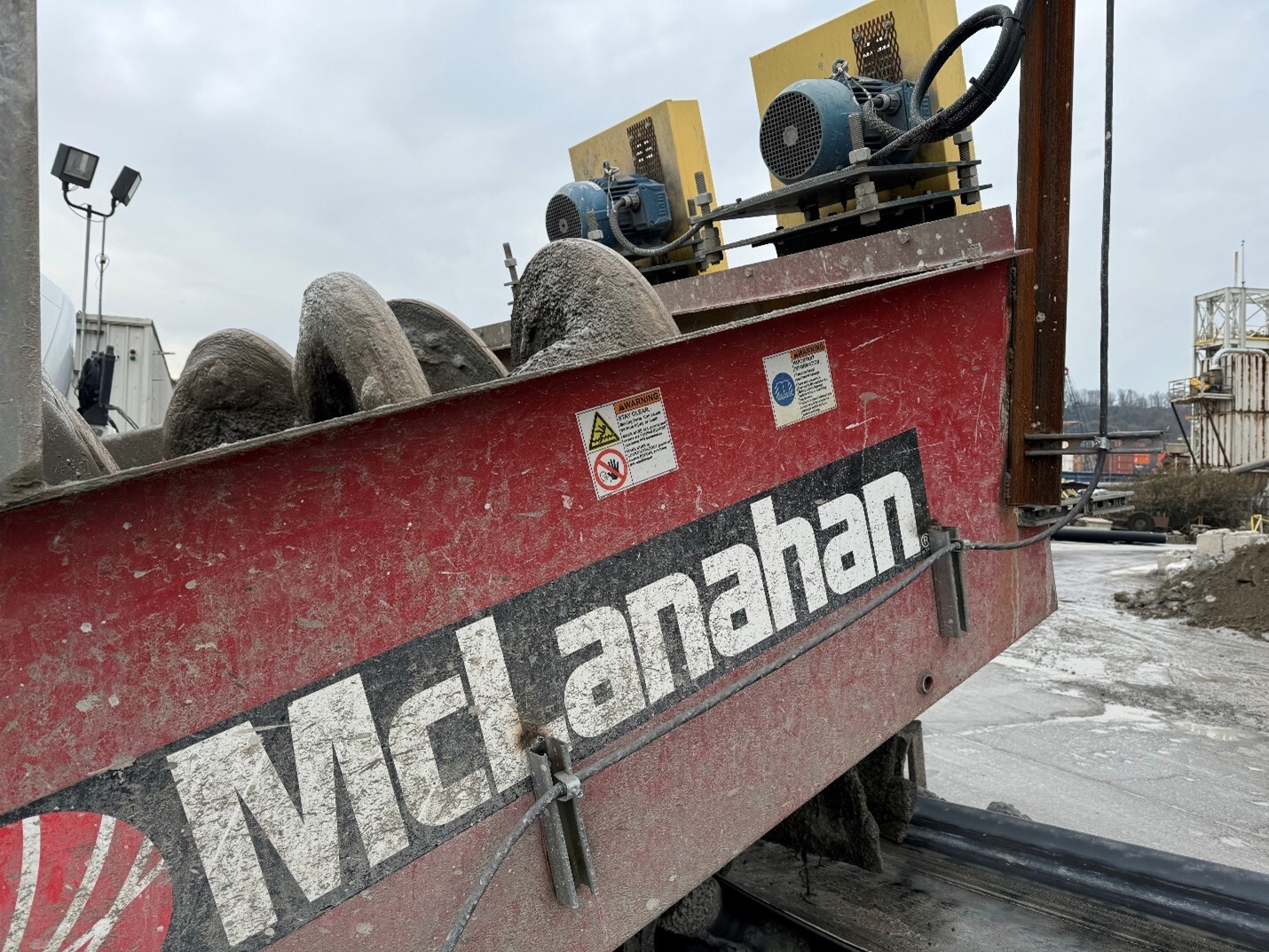
Recovering aggregate and water from wet concrete washout
Concrete washout recycling systems can be used to recover aggregate and water from leftover concrete directly from the trucks. This can be achieved with a few key pieces of processing equipment, including Fine Material Screw Washers, Sizing Screens and Filter Presses.
Concrete trucks returning from jobs can unload the leftover concrete into an auger that feeds a Fine Material Screw Washer. The aggregate material settles out of the slurry and is conveyed toward a Sizing Screen that separates the coarse aggregate from the fine aggregate. The fine aggregate is further washed in a second Fine Material Screw Washer. The coarse and fine aggregate can then be stockpiled for reuse in the batch plant.
All the water from this process, including the water in the concrete washout and the water used to rinse the aggregate material, is collected in a surge mixing tank that feeds a Filter Press. The Filter Press separates the ultrafine suspended particles in the slurry from the water, discharging a drip-free solids material and water that can be recycled for washing out trucks. With a pH adjustment, the water can even be reused in the batching process. The solid filter cakes can be crushed to produce a fill material that can be sold into the construction market, resulting in 100% recovery of materials.
With concrete washout recycling equipment, you don’t have to pour the leftover concrete into pits or rows and wait for it to harden, and then you don’t have to deal with handling the solid material after it dries. The system immediately recovers the aggregate and process water for reuse.
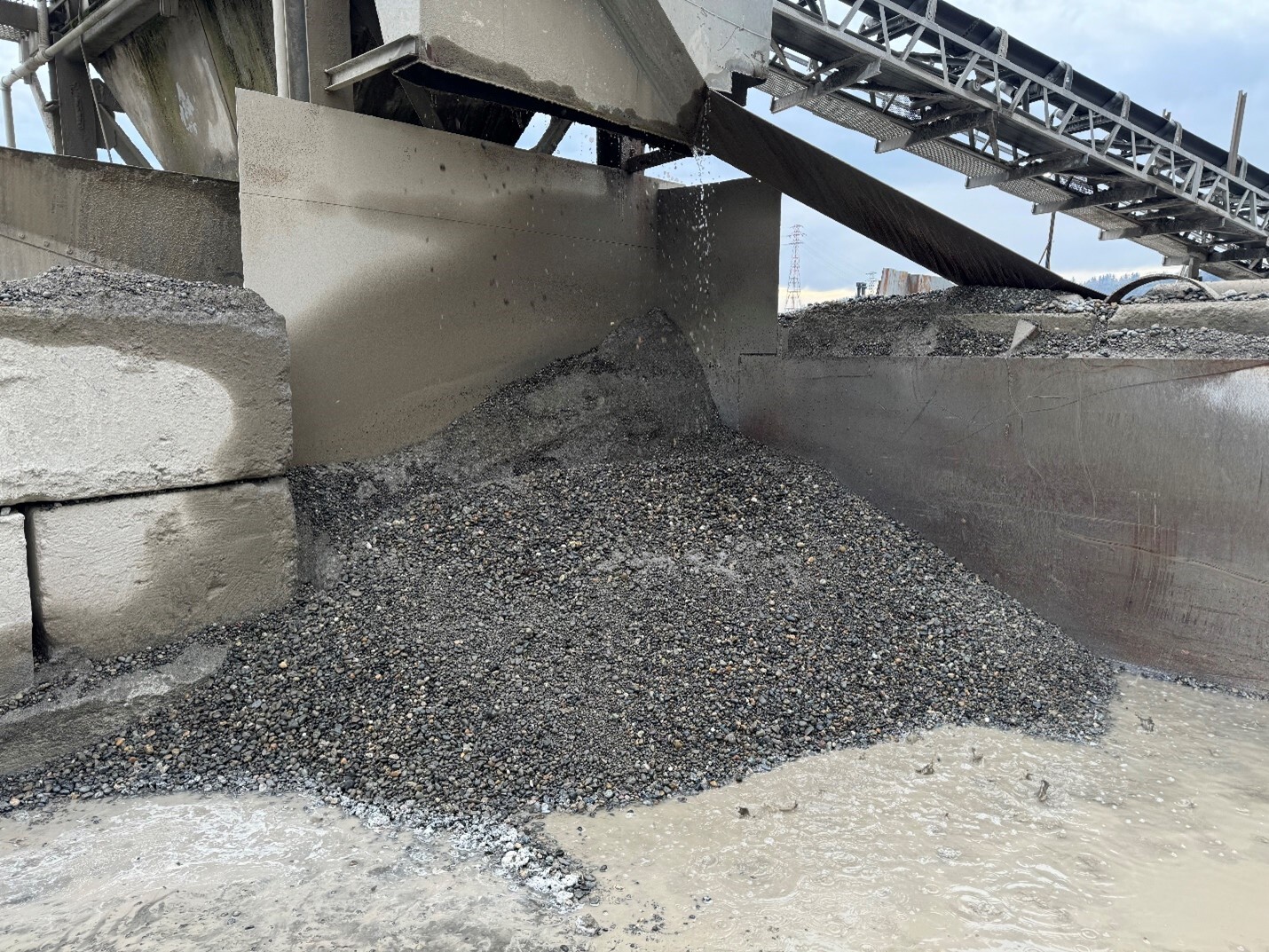
Benefits of reclaiming aggregate from concrete washout
Not only does recycling leftover concrete produce reusable aggregate materials and recycle water for reuse on site, but it also offers several additional benefits.
First, recycling leftover concrete reduces the amount of material sent to landfills. This itself provides two major environmental benefits: it saves valuable landfill space for non-recyclable materials, and it reduces carbon emissions from haul trucks since the material doesn’t need to be taken to the landfill. At a producer level, recycling leftover concrete saves landfill disposal costs as well as the fuel and personal costs associated with hauling material to the landfill.
Second, recycling leftover concrete reduces the need for virgin aggregate in the batch plant, since a certain ratio of recycled aggregate is allowable in the ready mix. This can save the producer money in purchasing or hauling in new aggregate material, as well as extend the life of the sand and gravel pit. It also reduces mining costs and protects natural reserves, which are a finite resource.
Finally, recycling leftover concrete allows producers to play a role in the circular economy and improve their company’s own sustainability initiatives.
Whether you want a simple crushing solution for dealing with leftover concrete, you want to wash crushed concrete to improve salability of the product or you want to completely recycle the leftover concrete into reusable aggregate and water, traditional aggregate processing equipment can help you improve your sustainability and recycling goals.