Challenge 1: Market perception – virgin aggregate vs. recycled aggregate
A perception exists in the construction industry that virgin aggregate provides greater performance over recycled aggregate.
Virgin aggregate refers to minerals that have been extracted from above or below the earth’s surface. Sand, gravel and stone are obvious examples. Most virgin aggregate used in the construction industry is supplied by a local mine; however, in some cases, aggregate is transported in from distant locations. Virgin aggregate is a finite resource.
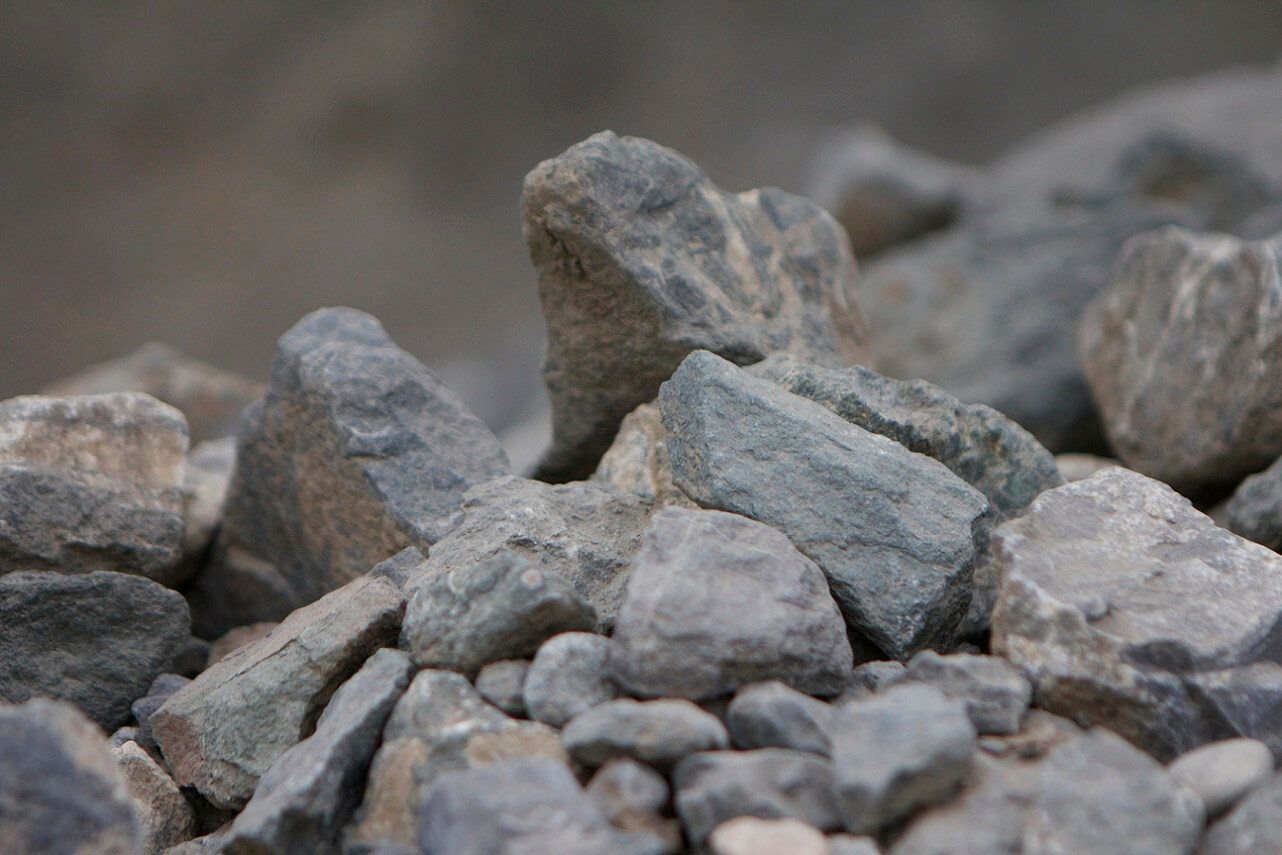
Recycled aggregate is made by reprocessing construction and demolition (C&D) debris, either in-situ or at a recycling facility (generally, contractors will pay a tipping fee to dump C&D debris at a recycling facility). Concrete, brick, asphalt and non-hazardous soils are examples of C&D debris that can be crushed, screened, scrubbed and washed to create valuable recycled aggregate. Recycled aggregate is a sustainable resource.

While the argument for virgin aggregate performance superiority over recycled aggregate may hold true in certain load-bearing applications, such as reinforced concrete, it is certainly not true for many other applications, particularly non-load bearing ones. Market perception, driven by individual cognitive bias, has caused society to believe that recycled aggregates are not of the same quality as virgin aggregates.
In many instances, there are significant cost savings when purchasing recycled aggregate, particularly in haulage. Many recycling facilities are situated in urban locations, providing convenience to contractors who wish to dispose of C&D debris close to their job site, lowering haulage costs.
Recycled aggregate can have higher volumetric yield per ton compared with virgin aggregate. The specific gravity of coarse reclaimed concrete material (RCM) aggregate ranges from 2.0 to 2.5, which is slightly lower than that of virgin aggregates, which is typically 2.65 - 2.7.
To put this in context relevant to a buying customer, 1.5” minus recycled, crushed concrete can be 15% lighter than the virgin equivalent, providing 15% more volume per ton.
Changing the market’s perception on recycled aggregate is not going to happen overnight, but C&D recycling producers can begin to overcome these challenges by adopting one or more of the following strategies.
Strategies to change market perception
To begin to change the market’s perception of recycled aggregate, suppliers should promote the thoughtful choice of aggregate for their customers’ projects. Be aware of the many applications where recycled aggregate is an adequate substitute for virgin aggregate. A few of these include:
- Fill sand
- Pipe bedding
- Trench backfill
- Landscaping
- Interlocking concrete blocks
- Road subbase
- Canal lining
- Landfill capping
- Screened soil
If you are considering becoming a recycled aggregate supplier:
- Locate your recycling facility in an urban location that is close to a large customer base. This minimizes transportation costs to and from your customers.
- Research local landfill tipping fees and set your recycling facility tipping fee accordingly, encouraging a steady stream of C&D debris (feed material) for your processing plant and to divert material from the landfill.
- Research local virgin aggregate prices in you market, and set your recycled aggregate prices accordingly, particularly for aggregate suitable for non-load bearing applications.
- Follow RFQs (requests for proposals) with requirements on recycled aggregate for concrete and road construction. The benefits of using recycled aggregates has already been ascertained.
Providing tools and knowledge of best applications of recycled aggregate materials will help to change the market’s perception of recycled aggregate inequality.
Challenge 2: Knowing your material and processing capabilities
The biggest challenge with recycling C&D debris is the variability and inconsistency of the feed material. Inconsistent feed material can result in lower-grade products.
With the right strategy, however, combining the right equipment for the job and the right equipment supplier, process variabilities and inconsistencies can be met with flexibility.

Strategy to overcome feed inconsistencies
First and foremost, understand that C&D debris recycling plants are not designed to process hazardous material. C&D debris with hazardous contaminants should be rejected. C&D debris recycling plants are designed for processing inert waste, defined as:
- Waste that does not undergo any significant physical, chemical or biological transformations
- Waste that does not dissolve, burn or otherwise physically or chemically react in a way likely to give rise to environmental pollution or harm to human health
- Waste that does not endanger the quality of any surface water or groundwater by its total leachability, pollutant content and the ecotoxicity of its leachate
As C&D debris is received, operators need to understand its makeup and level of suitability to process. When doing so, consider the types of C&D debris you are permitted to process. This can be made easier by investing in on-site feed material testing, including:
- Asbestos quantification testing
- Heavy metal and hydrocarbons testing
- Waste Acceptance Criteria (WAC) testing for analyzing the leaching ability of contaminants
Understand how your recycling system will respond when processing various types of C&D debris and build in the required processing capability and flexibility to make system adjustments based on material.
As C&D debris can be snagged with irregular-shaped steel rebar, it’s advantageous to:
- Minimize change in direction of material flow
- Carefully design transfer points
- Include multiple stages of metal removal
- Be thoughtful in choice of belt cleaners for conveyors
- Design in sufficient room around equipment for housekeeping
Regular sampling of finished products is beneficial for maximizing yield and quality control. This can be achieved with automated sampling systems.
When designing a C&D recycling plant, invest in an equipment supplier who:
- Creates a solution with your goals in mind
- Uses a conservative approach toward defining performance ratings
- Provides ability to monitor, adjust, troubleshoot and maintain operations safely
- Provides ongoing support through the lifetime of your operation
With significant infrastructure spending, increased mandates surrounding carbon emissions and an upward trend in sustainability efforts, there is growing demand for recycled aggregate. Although there are perceptions and challenges to overcome, recycled aggregate offers great rewards for suppliers, customers and the environment.