What is hydrovac waste?
Hydro excavation is a non-destructive method of digging, exposing underground utilities or maintaining pipelines using high-pressure water and a vacuum system. The byproducts generated during this process are often referred to as hydrovac waste.
Hydrovac waste is the slurry waste generated during the hydro evacuation process. It consists of:
- Water
- Soil
- Debris such as rock, gravel and vegetation
- Contaminants, which can include chemicals, oil or other hazardous materials depending on the nature of the excavation site
Traditionally, hydrovac waste is disposed of in landfills or treatment facilities. However, there is growing interest in finding ways to recycle or repurpose the water, soil and debris as valuable resources as part of C&D recycling.
For example, gravel debris can be separated out of the waste stream, washed free of contaminants and sold for use in new construction projects. The water can be filtered, treated and recycled for reuse in the hydro excavation process or on-site housekeeping.
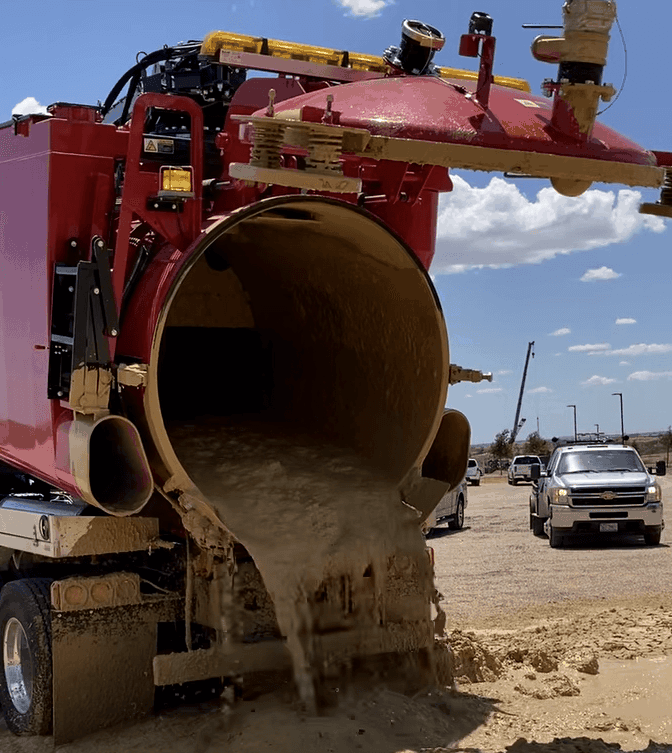
The need for sustainable hydrovac waste solutions
Managing hydrovac waste can be challenging.
Because hydrovac excavation uses pressurized water to break up soil, the waste stream is mainly liquid – about 60%. The solid-liquid state of the slurry makes it unsuitable for most conventional landfill sites to process, so many landfills do not accept this material.
Another concern is the nature of the slurry itself; hydrovac waste is notoriously unpredictable in terms of composition. Because hydrovac waste can contain hazardous materials, proper disposal is imperative to avoid contamination of the surrounding environment.
There are disposal sites authorized to accept hydrovac waste; however, the time and costs associated with transporting the slurry to these facilities can add up.
With landfills around the world reaching capacity and closing, as well as increasing societal pressure to seek more sustainable alternatives to dumping waste, hydro excavation companies are looking for better ways to manage hydrovac slurry, including resource recovery for reuse.
Hydrovac waste recovery solutions
Hydrovac Waste Recovery Systems are designed to salvage valuable materials from hydrovac slurry for reuse. These systems accept hydrovac slurry directly from a hydrovac truck, which dumps the slurry into a hopper to feed the plant. The solids are separated from the liquid, sorted into coarse and fine fractions, washed and stockpiled. The liquid is then further processed to remove suspended solids and/or treated to remove impurities.
While Hydrovac Waste Recovery Systems can be composed of different types of processing equipment, here are a few innovative technologies for transforming hydrovac waste into a valuable resource.
Trommel Screens
Trommel Screens are used in Hydrovac Waste Recovery Systems for initially separating the coarse aggregate from the fine material and liquid. They consist of a rotating cylindrical drum composed of screen plates and internal lifting bars.
The hydrovac slurry enters the feed end of the drum, where the rotation of the cylinder repeatedly lifts and drops the material onto itself. This helps to separate the different sizes of material, as well as to break down softer fractions.
The water and smaller size particles in the slurry exit the drum through holes in the screen plates and fall into a sump beneath the Trommel. The coarse material continues to tumble along the length of the drum to discharge out the end. Spray bars inside the drum rinse the material as it passes, providing a cleaning function. Spray bars affixed to the outside of the machine rinse the screening sections to keep the holes from plugging with material.
Trommel Screens are beneficial for size separation in Hydrovac Waste Recovery Systems because they can handle the high volume of water associated with hydrovac waste slurry in a compact unit.
Separators™
Separators™ are used as the first stage in the double washing of the fine material fraction. Double washing provides a cleaner product, which leads to more opportunities for sale. These siphon-assisted Hydrocyclones classify the fine material, separating the sand particles from the silts, fines, clays, topsoil, etc. and discharging them to the next stage of the process.
The silts, fines, clays, topsoil, etc., along with a majority of the water, exit out the top of the Separator™ and flow into the sump of the water recycling module.
Separators™ provide several advantages for processing hydrovac slurry. First, they can handle changes in feed density better than a Hydrocyclone. They can also handle large volumes of water and make a consistent cut.
Fine Material Screw Washers
Fine Material Screw Washers are used as the second stage in the washing of the fine material. Sand is fed through a feed box into the pool area of the screw. Larger, heavier particles of sand sink to the bottom, while the light, fine particles overflow the weirs surrounding the pool area and flow into the sump of the water recycling module. An upward rising current of water in the pool area helps to keep finer particles in suspension so they discharge with the wastewater, aiding in classification.
The larger, heavier particles of sand are conveyed out of the pool area and up the incline deck by a rotating spiral shaft. Excess water drains from the material as it is conveyed up the incline toward the discharge.
Fine Material Screw Washers offer the benefit of flexibility in the final sand spec due to the rising current classifier. They are also effective at floating out lightweight organic material.
Dewatering Screens
Dewatering Screens are used to remove excess moisture from material ahead of stockpiling. In a Hydrovac Waste Recovery System, Dewatering Screens accept material from a Fine Material Screw Washer and discharge a drip-free sand product.
Producing a drip-free product has additional site housekeeping benefits, including less water leaching out of stockpiles. The Dewatering Screen can also be equipped with a Slurry Pump to recirculate fines back into the process.
Thickeners
Thickeners are used in Hydrovac Waste Recovery Systems to recycle water for reuse in hydro excavation or for on-site housekeeping activities, such as washing down the hopper grates.
The wastewater from the washing process is pumped into the Thickener, where it is combined with chemical polymers to aid in settling of the suspended solids. The polymers attract the suspended solids together to form larger particles called flocs. The flocculated particles settle to the bottom of the Thickener tank, where a rake mechanism moves the particles toward the discharge cone in the center to move on to the next stage of the process.
The liquid portion, now free of a majority of the suspended solids, overflows weirs surrounding the Thickener and into a holding tank to await reuse.
Decanter Centrifuges
Decanter Centrifuges offer additional water recycling by further separating the solids from the liquid in the Thickener underflow. These machines consist of a feed pipe inside a helical screw conveyor inside a bowl and all enclosed in an outer casing.
The Thickener underflow and additional polymer is fed into the inside of the rotating helical screw conveyor. Through feed ports in the conveyor, the slurry emerges into the region between the screw conveyor and the bowl. Centrifugal forces acting on the material force the solids to the inside surface of the bowl, while the liquid flows freely toward the discharge end. The liquid flows into the holding tank to await reuse.
The solids are conveyed toward the solids discharge end and ejected out of the bowl in a drip-free state suitable for mechanical handling.
Decanted Centrifuges are ideal for Hydrovac Waste Recovery Systems because they can handle the tough clays that can be present in hydrovac slurries better than other types of liquid-solid separation and dewatering equipment. They are also adept at handling variations in feed composition.
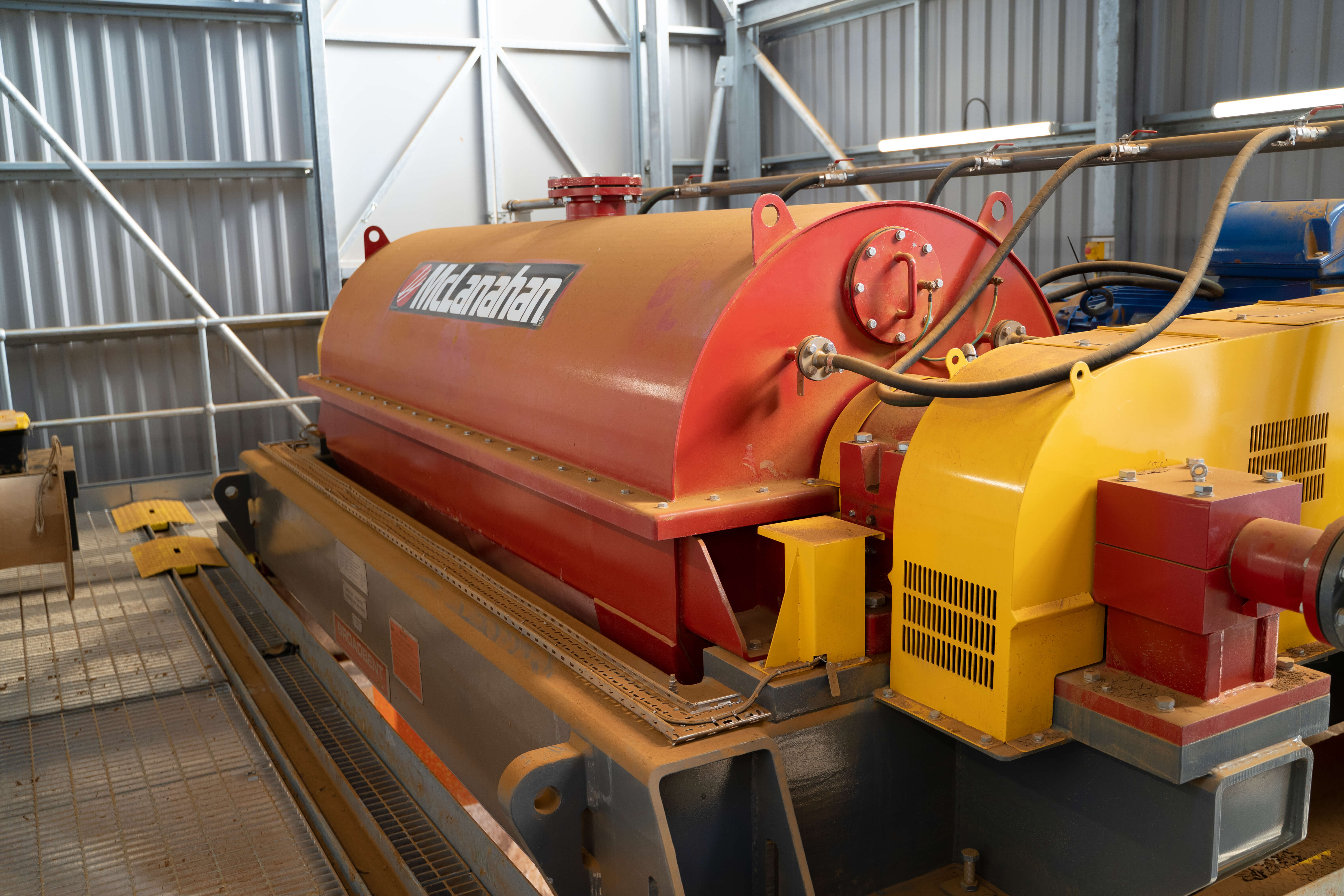
Benefits of recovering material from hydrovac waste streams
Hydrovac Waste Recovery Systems offer a range of benefits.
First, they recover solid material, such as aggregates (sand, rock, and gravel), for reuse. This itself is beneficial for a variety of reasons.
- It creates value from what would otherwise be classified as waste, creating an additional revenue stream for the operation.
- It prevents usable material from piling up in landfills, helping to lessen the amount of waste sent there.
- It helps producers with sustainability efforts and having a role in the circular economy, promoting a culture of reduce, reuse and recycle rather than one-time use.
Second, Hydrovac Waste Recovery Systems recycle water for reuse. This too offers a number of benefits, including:
- Reducing freshwater requirements, as the recycled water can be used in the hydro excavation process as well as for on-site housekeeping tasks
- Conserving freshwater resources by reusing water
Finally, Hydrovac Waste Recovery Systems reduce transportation costs and disposal fees. By recycling waste material on site, producers can avoid the time and costs associated with hauling the hydrovac waste to approval disposal site. They can also avoid the often costly fees associated with disposing of hydrovac waste.
In all, Hydrovac Waste Recovery Systems are beneficial for hydro excavation producers looking for sustainable alternatives to landfill disposal who want to reduce transportation costs, produce a salable product and recycle water for reuse as part of the circular economy.