Introduction
Before we get into the issues commonly faced when washing and dewatering sand, such as sand that is discharging to the product pile too wet, product sized sand being sent to waste, sand that isn't consistently in spec and too many hours spent cleaning out settling ponds, let's first address the types of equipment used to wash and dewater sand.
Several choices are available for washing and dewatering sand that is typically minus 5mm (4 mesh) and finer. These options range from simple to more complex and can vary in capital purchase price, operational cost (including wear parts) and electric power consumption.
Other factors, such as the range of moisture in the washed product discharge when the sand goes onto the finished stockpile, should also be reviewed when setting up a sand washing plant.
Fine Material Screw Washers
Among the simplest devices for washing sand and removing silts and clays is a Fine Material Screw Washer, often called a sand screw. It can be installed on the ground next to a wet vibrating screen. Via a simple flume or chute, a slurry flow of water and sand can be used to feed the sand screw.
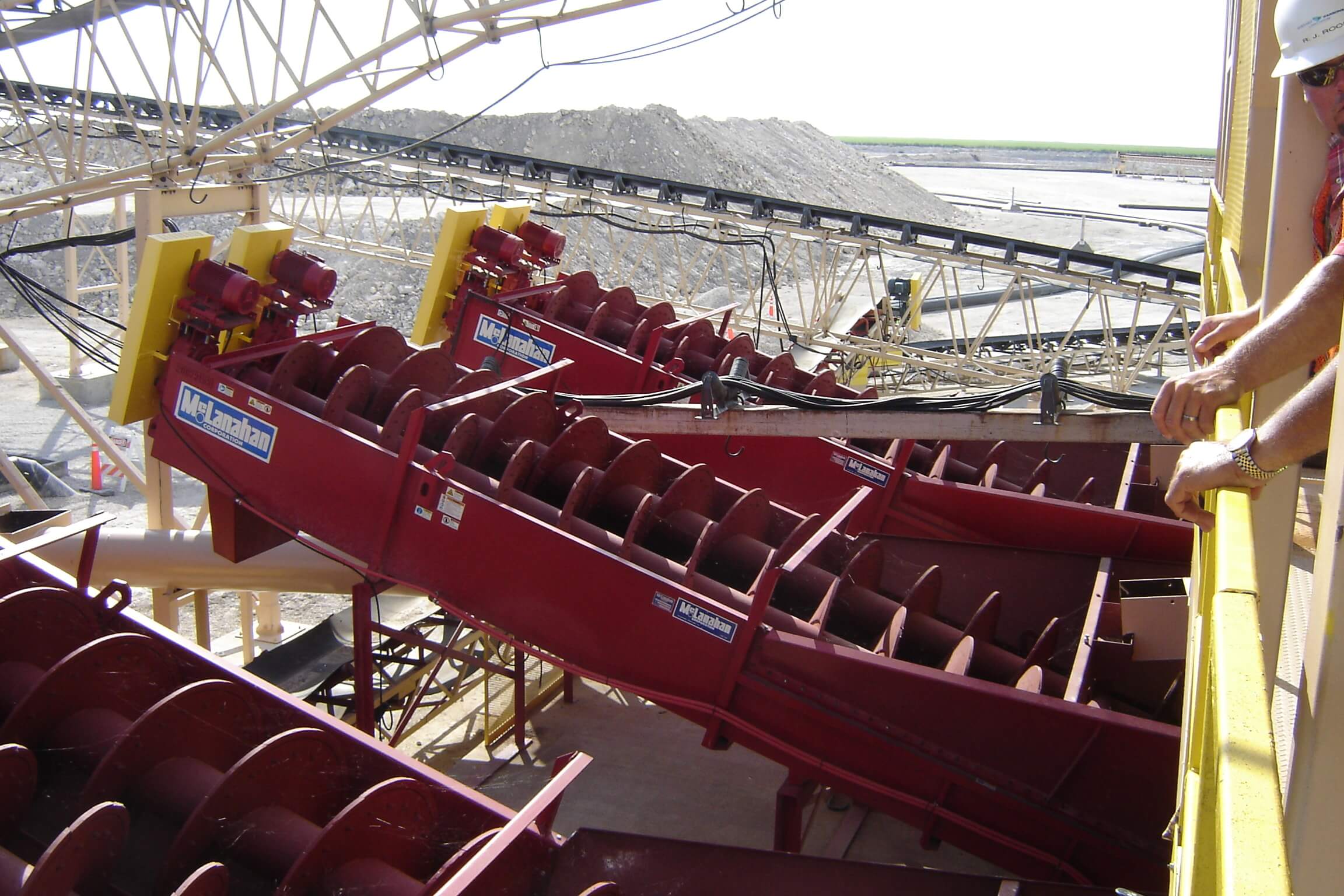
McLanahan Fine Material Screw Washers wash, classify and dewater fine material.
If properly sized by a local dealer or manufacturer, you should be able to retain most of the required +75 micron (200 mesh) sand. For a 75-100 tph of sand feed, you only need about 10 kW or 15 hp of electric power to put a conveyable sand on a product pile via an elevating belt stacking conveyor.
Hydrocyclones
Globally, Hydrocyclones have widely been used for a similar fines removal and dewatering function. Having no moving parts, a Hydrocyclone or group of Hydrocyclones in a cluster can be installed in several ways. Some are mounted on towers or some type of structure and positioned away from the other processing equipment.
In order to achieve proper performance, Hydrocyclones must typically be fed via a pumped slurry in a consistent percent solids range and at a pressure required by the Hydrocyclone supplier. With these requirements, the capital and operating costs, including the necessary electric power, should be reviewed when considering Hydrocyclones.
Dewatering Screens
Recently, varying designs of Dewatering Screens have hit the market. A properly designed Dewatering Screen discharges the driest washed sand product of any dewatering device commonly used. Also, the space required is less than other options.
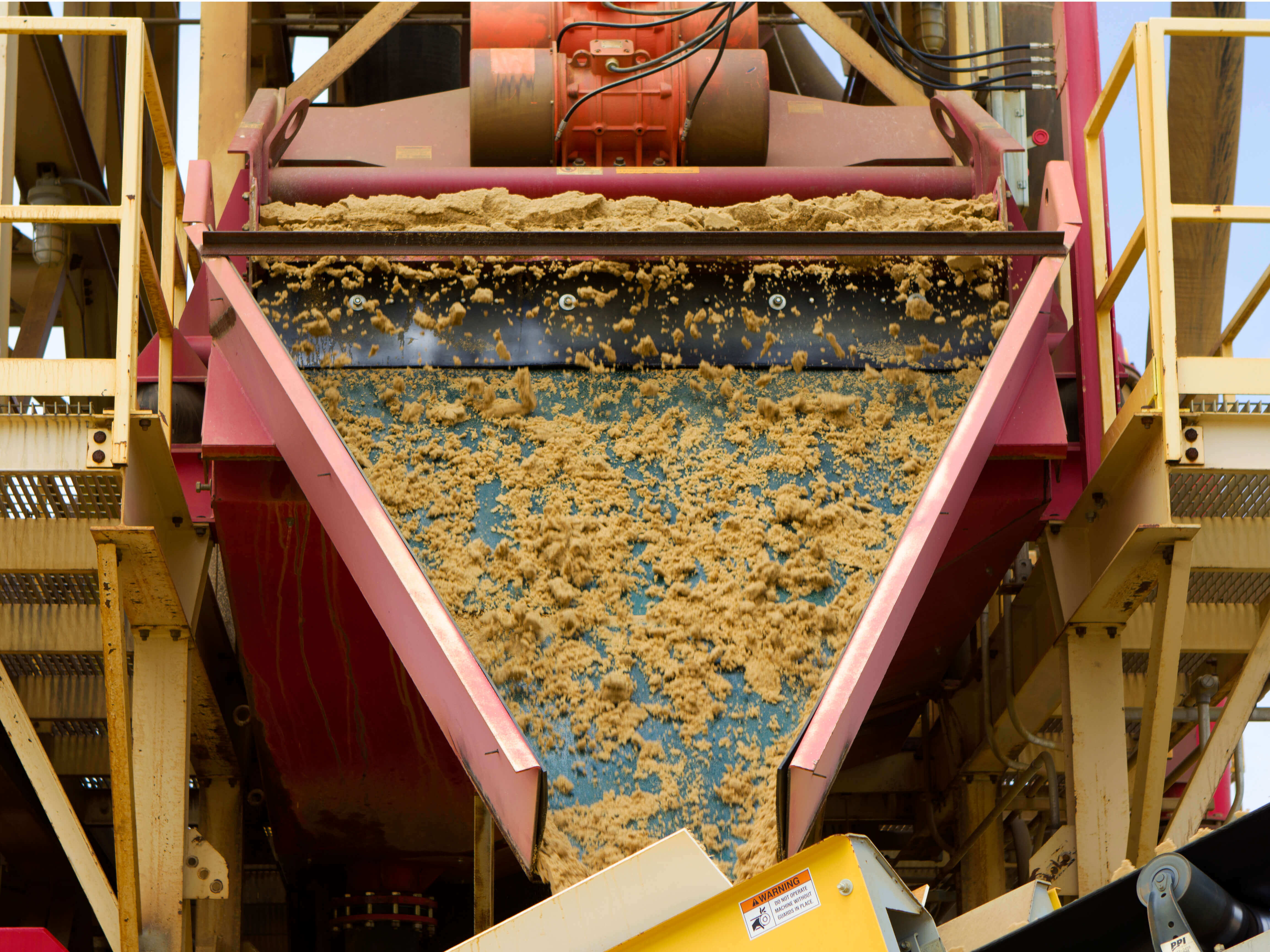
McLanahan Dewatering Screens can reduce the moisture content in a final product to as low as 7%.
Depending on the slurry of the sand feed and specifically the percent solids of the sand flow, these units often require a sump, pump and a Hydrocyclone or two to partially dewater the slurry to allow the screen to adequately perform. The capital cost required for a Dewatering Screen system is often more than two times more than the other choices, and up the electricity cost is often up to three times more.
Bucket wheels
Bucket wheels are another option for dewatering a slurry of sand. Some designs are more complex when compared to others for retaining +75 micron (200 mesh) washed sand. While typically low in the electric power costs required for driving the wheel assembly, their capital cost can be higher than some sand dewatering equipment choices.
Thickeners and Filter Presses
When operating a wash plant, environmental regulations typically require that you contain the effluent of the silt/clay-laden dirty washwater on your property. You will have lots of washwater, but as it may contain 10% ultra-fine solids, it can’t be used back into your plant — unless you can somehow separate the silt and/or clays from most of the water.
A Thickener allows a wash plant to reclaim up to 85% of the water for immediate use back into the washing plant. Concentrated mud discharging typically at a 40% solids content also reduces the space required for tailings containment. Various types of Thickeners are used widely by mining and aggregate construction industry washing plants.
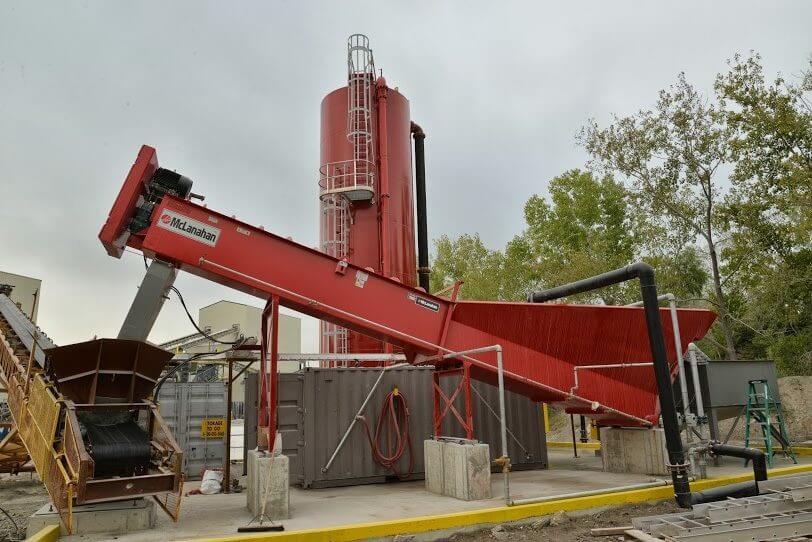
A McLanahan Fine Material Screw Washer and Thickener.
Other devices that can further dewater a Thickener solids discharge include Filter Presses, centrifuges and belt filter presses. Some aggregate companies have totally eliminated the settling ponds associated with their rock and sand washing plants when using these technologies.
Common issues with washing and dewatering sand
Now that we've looked at the equipment typically found in sand washing plants, let's address some typical questions with washing and dewatering sand.
My sand is wet when discharging onto the stockpile from the dewatering equipment.
Depending on what equipment you’re using, sometimes all it takes is a simple adjustment or the addition of water at the right injection point (yes, adding water at the right point) to make the sand going onto the pile drier.
If you have sand screws, ensuring sure you have washback water to flush accumulated fines out of the dewatering zone channel can make a big change, resulting in a drier sand discharging from the machine.
Sometimes we’re asked: "How much water is needed in the water connections?" These connections can range from 3/4" (19mm) to 1.5" (38mm).
While there are published tables from some manufacturers, the right answer is that you only need enough water to keep the trough or channel clear of fine sand.
Whatever your plant's water pressure may be, having a hand control valve on these water lines can easily allow an adjustment to add enough (not an excessive amount of) water.
If you operate vacuum-assisted Hydrocyclones, sometimes called Separators™, a simple adjustment of the vacuum air line that varies the opening of the rubber underflow regulator can result in a drier sand to discharge.
Adjusting the vacuum air line on a Separator™ can result in a drier sand discharge.
Just a periodic visual observation of the units you may have in your sand washing plant, be it in a primary sand circuit or a secondary fine sand recovery system, can reduce the moisture content of the material discharging to your sand pile.
Weir positioning on sand screws and bucket wheels is used more for controlling fines retention, and the weirs can be adjusted to a lower position to provide more dewatering. This option is often overlooked as a potential adjustment to discharge a drier sand to a stockpile.
I’m losing +75 micron (+200 mesh) product sized fine sand.
Perhaps you’ve recently added more water to the wash screen that precedes your sand dewatering gear to make the rock cleaner. This can result in losing +75 micron (+200 mesh) sand to your settling pond. You can’t cut back on the wash screen water, as the rock is too dirty, out of spec.
A McLanahan Fine Material Screw Washer follows a wet screen in the above photo.
If you must keep the water volume the same to what now may be undersized equipment and you want to keep this fine sand in your washed sand, some type of capital equipment changes or additions will be needed.
If you use a bucket wheel or sand screw, the addition of a properly sized Hydrocyclone to handle the dewatering unit's overflow has successfully been used to recapture lost, product sized fines. This would also require the addition of a sump and pump to feed the Hydrocyclone at the required inlet pressure. Mounting the Hydrocyclone over the discharge of your existing dewatering unit is common.
Another option if you're using a sand screw is to replace the existing unit with a larger machine. The capacity of a larger Fine Material Screw Washer shaft might not be needed, but the bigger tub and higher water volume capacity will oftentimes keep the finer sand in your product pile.
Talk to several of your suppliers to get ideas as to what might be the best solution to this issue. A lot of sand producers have had this problem.
I can’t consistently make spec C-33 sand.
There could be several reasons why an operation is unable to consistently make in specification concrete sand, beginning, perhaps, with their material deposit. This can happen in either a crushed stone manufactured sand plant or an alluvial sand deposit.
A change in the mesh screen aperture you use on the wash screen before your sand processing equipment can make a difference. A slight variance in the screen mesh or type of screening media can make a significant difference in the sand gradation that goes on the washed sand pile.
The issue of making a specification C-33 concrete sand may be because your equipment is not retaining sufficient -150 micron (100 mesh) fines. Having the right gear to retain the needed fines as discussed previously may help you make a spec sand.
Lastly, you may need to consider the addition of a sand classifier to be used before your washer/dewatering unit. There are two basic types of sand classifiers that can remove an excess intermediate sand that’s +150 micron (100 mesh). One is the V-box, multi-valve discharge station Classifying Tank. Another is the up-current classifier sometimes referred to as a Hydrosizer®.
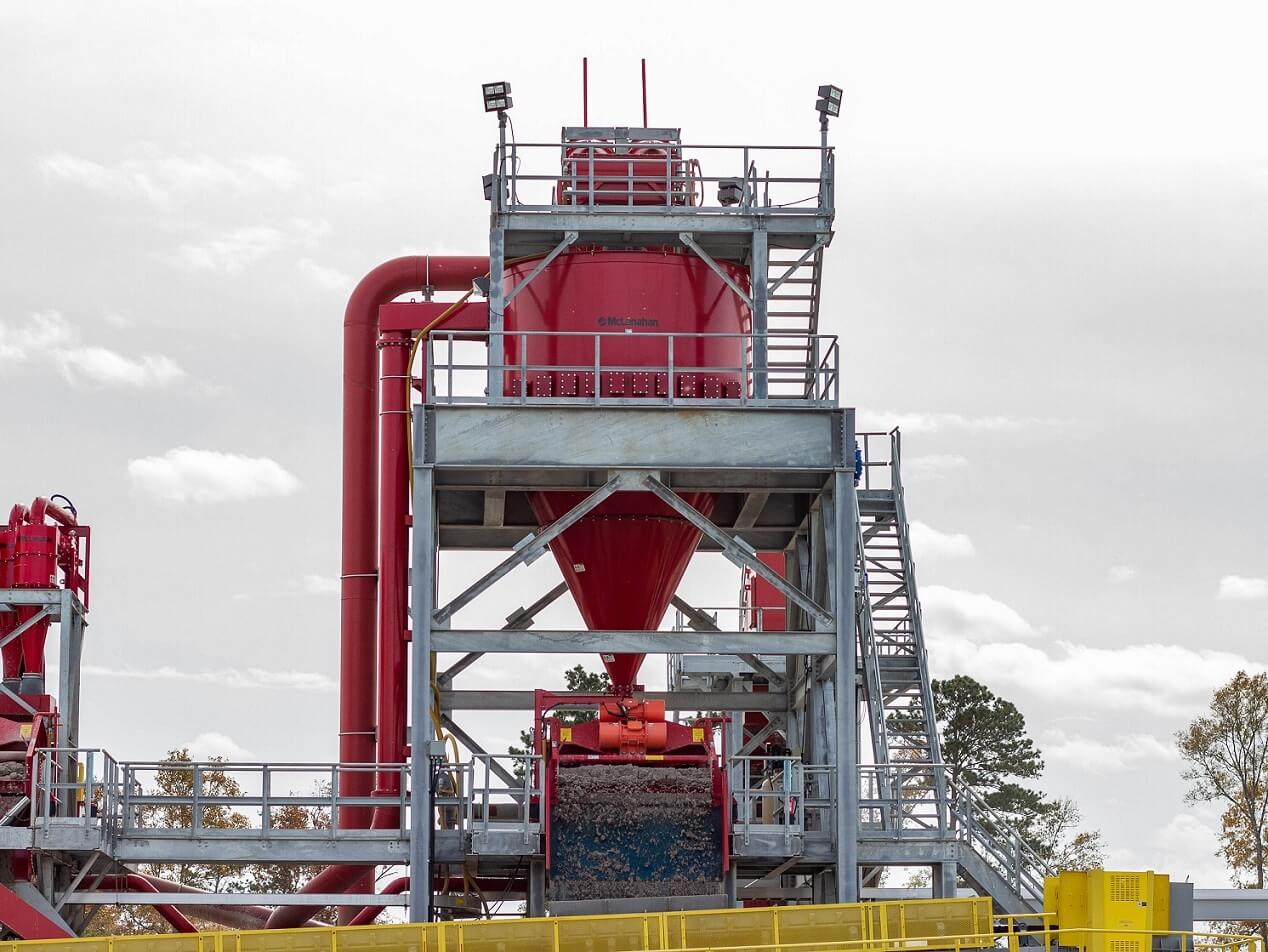
Hydrosizers® allow for the reblending of sand into two or three products.
These units allow the re-blending of coarse, intermediate and retained fine sands into two or three products, depending on the configuration, allowing for the production of a spec construction sand like C-33 concrete sand.
My boss says we need to reduce the number of hours bailing out our settling ponds.
Some sand plant operators don’t keep track of the number of man and equipment hours spent bailing out settling ponds. If you’re filling in a mined-out, abandoned section of a stone quarry, you can just keep filling the hole you’ve mined out.
Other operators must maintain containment ponds so as not to discharge super fines into nearby streams or onto adjacent land. Some aggregate plants use many acres of land to contain super fines. Certain operators have to limit their plant running hours to keep up with the constant mucking out of their settling ponds.
If the latter example is you, several equipment options are available to reduce or eliminate the need for these containment ponds. The use of Hydrocyclones or a system with Hydrocyclones and Dewatering Screens can recover ultra-fine material 38 micron (400 mesh) and larger. The use of this gear can reduce the volume of flow into a settling pond.
Filter Presses separate tailings slurry into reusable process water and drip-free cakes, potentially eliminating settling ponds.
If your solids effluent fraction is more -38 micron clays and silts, the use of Thickeners and Filter Presses are more and more commonly implemented. Thickeners separate solids from the liquid in a slurry to reduce the volume of material destined for settling ponds and to recycle clear process water for reuse in the plant.
Filter Presses also separate solids from the liquid in a slurry, producing a drip-free cake from the solids and clear process water for reuse in the plant. With a Filter Press, settling ponds can be completely eliminated, and with that, the time required for cleaning out those settling ponds.