Sizing the Dewatering Screen
Two main factors are used to size a Dewatering Screen:
- Equipment design
- Desired moisture level of the discharge
Equipment design
The first factor, Dewatering Screen design, deals with the screen's ability to handle the throughput. This boils down to the crossbeams and strings underneath the screen media and the media itself.
Monitoring the mass on the screen
Too much mass on the screen will begin a cascade of failures. These failures can show up in a number of places, but one of the easier to control and easier to observe is where the screen is isolated at the mounting point.
Isolation is achieved with rubber buffers, coiled springs or other methods that are designed for the upper mass limitation of the Dewatering Screen's physical capacity. Each one of the isolation methods has a limited ability to recover from deformation caused by overloading.
Once permanent deformation or breaking has occurred, the vibration of the screen is no longer fully focused on the effort to dewater the material. This impacts the life of the Dewatering Screen and the effectiveness of the dewatering process.
Monitoring the height of material discharge
Monitoring the height of material discharge is another way to observe overloading, but it is not applicable to fine material dewatering. Therefore, the screen structure sets the upper level of physical capacity, but many applications never approach that limit because of the other main factor, which is desired moisture level.
Heavy loaded screen.
Desired moisture level
The desired moisture level of the discharge is the other main factor used to determine the Dewatering Screen's effective capacity.
The majority of the time, the goal is to make a “drip-free” product. That means if a person was to grab a handful of the Dewatering Screen discharge and squeeze it into a ball, there should be no water dripping out.
Several physical properties of the Dewatering Screen and the material influence water removal rate, including:
- The drainage rate of the screen
- The drainage rate of the material
Drainage rate of the screen
Every Dewatering Screen has a maximum drainage related to the open area of the screen media. The larger the open area, the higher the drainage rate or the amount of water that will pass through the screen media.
The open area has to be balanced against the opening in the screen media. Too large of an opening will allow material to go through the screen deck along with the water. In some cases, this may be desired.
Alternatively, if the opening is too small, the drainage rate may not be sufficient to adequately dry the material.
Dewatering Screens generally have a much lower open area than a sizing screen. Because of this, it is beneficial to introduce the new material to the Dewatering Screen at 50% solids by weight or higher.
The lower amount of water in the new feed to the screen will increase the chance of retaining fines on the screen and producing a drier product.
Too much water for drainage rate.
Drainage rate of the material
The material itself has a drainage rate and is a major influence in the water removal process. The different physical characteristics have to be considered for each application.
The gradation of the material is an important factor, as coarser material generally has a higher drainage rate and allows the Dewatering Screen to operate at high capacity.
A coarse material will have a thicker bed depth in terms of measurement but will have less layers of particles. This creates an easier path for the water to move through the material and report to the screen's underside.
Coarser material’s capacity on a Dewatering Screen will be close to or at the screen’s physical capacity and will generally have a lower percent moisture.
In contrast, a fine gradation will reduce the capacity of the unit. Material with a finer gradation will have more layers and the material will be tightly packed. This creates a more difficult path for the water to drain through the material and report to the underside of the screen media.
To further complicate the matter, some material can have interlocking characteristics, which will further decrease the drainage rate through the material. Even though a drip-free product is achieved, the finer particles have a tendency to retain a larger percent of moisture.
Fines follow the water
“Fines follow the water” is a comment I have repeated for numerous times, but it is still true. The water will carry finer particles through the screen openings. This leads to difficulty retaining the finer particles on the screen deck.
It is especially tricky to retain material that is smaller than the screen media opening. As mentioned above, the finer material will have more layers, but the bed depth will be less. Keeping the material on the screen deck longer will improve the dewatering process. This is especially true if the coarsest fraction is kept on longer.
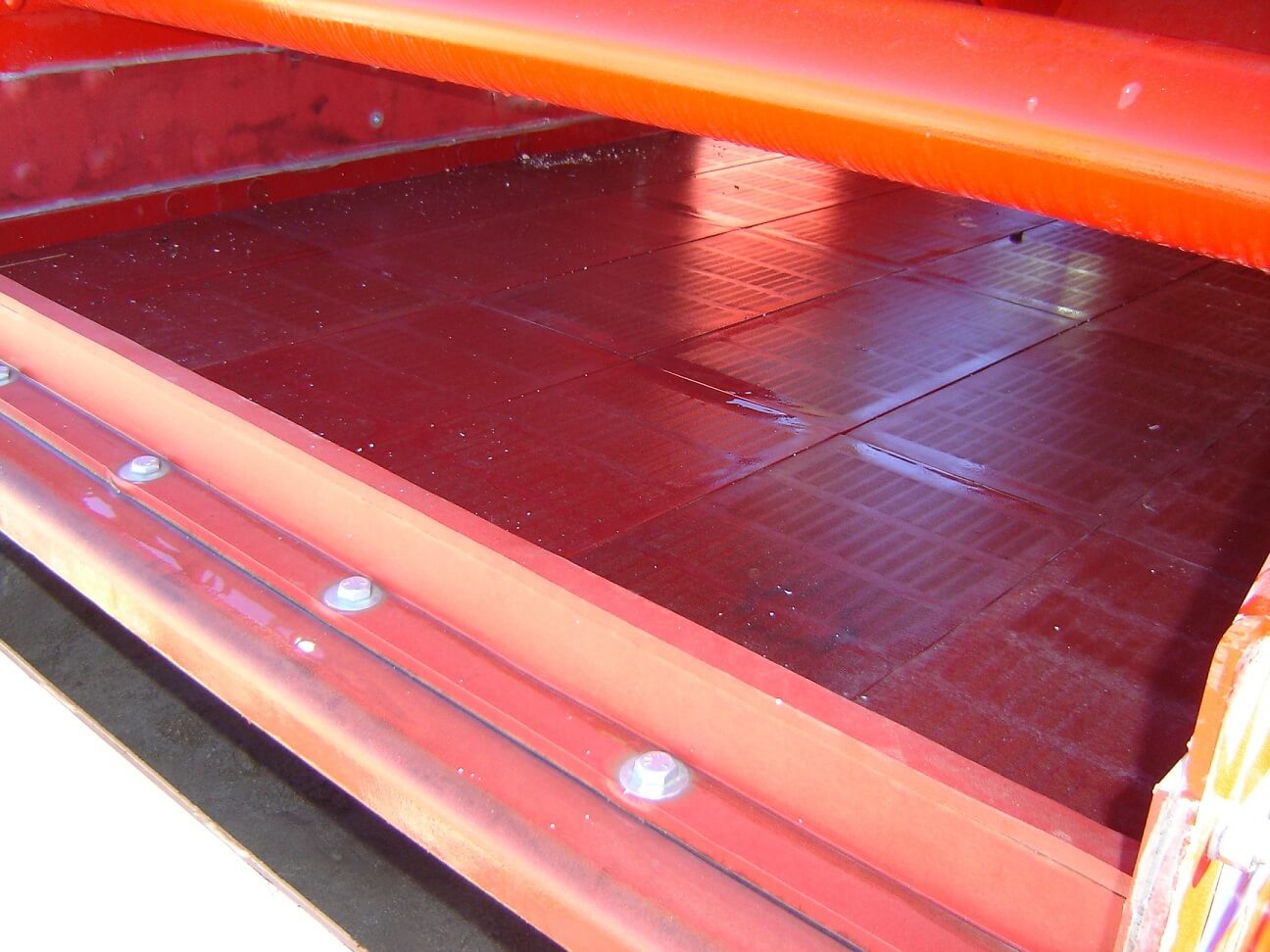
Heavy-duty screen media with discharge weir.
Final considerations
In the end, the drainage rate of the screen and the material drive the sizing for most applications.
There are several methods to increase each of the drainage rates. Some of them, such as weirs and dams, attempt to increase the material drainage. Other approaches, such as speed and media openings, focus on the screen drainage.
Because each application has its own unique properties, it takes experience and experimentation to find the right adjustment to maintain throughput and produce the driest discharge.