Introduction
It may be another water bill, a permitting issue or maybe it’s the frightening silence of your wash plant as you survey the job of cleaning out your pond to reclaim room for more feed when the plant starts to produce again. Whatever it is, reclaiming water for immediate reuse might be just the remedy for the pain you feel.
Not much good happens without water in your wet process systems. Moreover, managing your water does not have to be such a boat anchor as it may seem sometimes. At McLanahan, we prefer to tailor a solution to meet your specific needs when it comes to most processes, and this is certainly no special case.
When we look at how we can help you manage your water, we often consider a tiered approach, making use of technologies that fit both your budget and your needs. What do we mean by tiered approach? It’s pretty simple, actually; the tiers are based on three unit operations to handle your tailings stream:
- Ultra Fines Recovery
- Sedimentation
- Filtering
These tiers may be implemented individually or in series depending on the level of water recovery and solids handling you wish to achieve.
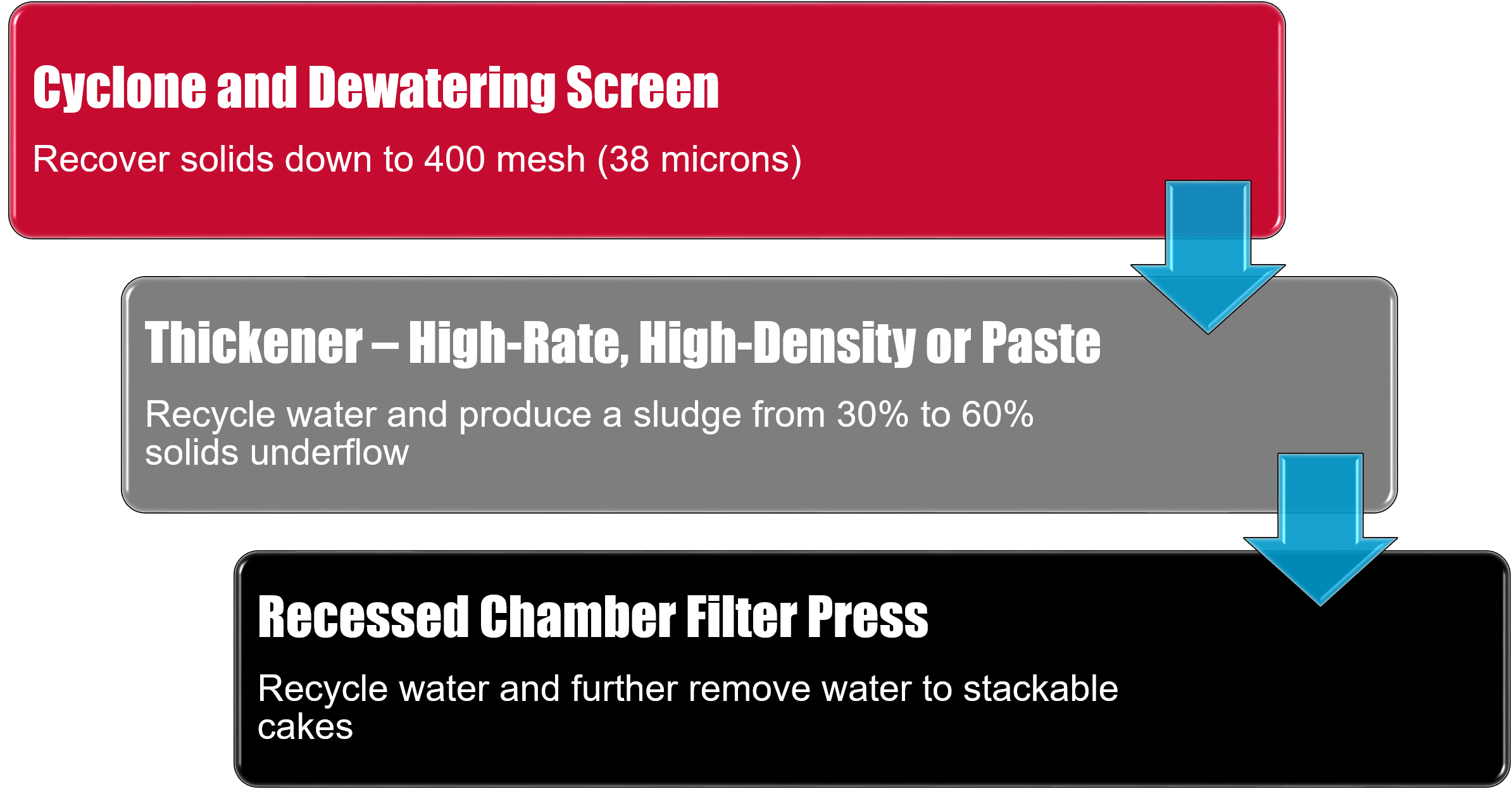
McLanahan's tiered approach to water recovery and tailings management.
Ultra Fines Recovery
While not necessarily a water recovery operation per se, the Ultra Fines Recovery (UFR) System is typically used to offload pressure on your tailings pond by removing particles down through 30 microns (based on 2.7 specific gravity) while producing a very manageable (i.e., conveyable, stackable) fines product. For many years, producers struggled with these fines in their waste stream, mostly being focused on what sort of product could be made with these fines or how they might even be treated to a state where they were easily handled.
In 1993, McLanahan’s Linatex Process Technology Group used the idea of combining cyclones with their Dewatering Screen to provide this solution. The cyclones were set up to recover the solids, while the Dewatering Screen, with its attendant low open area and caking abilities, was used to trap ultra-fines in its oversize. The systems are robust in that they are comprised of well-known, proven equipment and are easily deployable, as they are built as modular systems that can be erected with several simple crane picks. Producers have relied on these systems to extend their pond lifecycle and water quality now for a quarter of a century.
The typical flowsheet for a UFR system is shown in Area 3000.
Were we to take the UFR on its own, it is obvious that while the UFR can help from a pond maintenance and extended water quality aspect, the water must travel to the pond and meander its way about through several ponds before it can be brought back to the plant for reuse. The pond system, while seemingly benign in its day-to-day existence, does have its costs beyond the cleanout. Some issues include:
- Exposure of your resource (water) to losses through seepage from the pond and/or evaporation.
- Safety hazards for employees while working near the ponds.
- Possibly overlying mineable reserves.
Sedimentation
Sedimentation is the basis for the processes known as thickening and clarification. The devices normally used for these operations include:
- High-Rate Thickeners
- High-Density Thickeners
- Paste Thickeners
- Plate Clarifiers
For want of a better description, each of these units are different designs of buckets in which we allow suspended solids the opportunity to settle by gravity through the water in which they are dispersed. You can imagine that these could be some large tanks if we wait for gravity alone to act on the fine particles. To assist this process, these suspensions of solids are destabilized by the use of two types of chemical reagents:
- Coagulants
- Flocculants
Particles are kept in suspension via their small size (high drag forces) and electrical charges that exist on the particle surfaces. Coagulants typically carry a positive, or cationic, charge and attack the negative surface charge of the particles, reducing their ability to repel one another electrically. In nature, we see this coagulation in action wherever a river meets an ocean. Ocean water is a coagulant in this respect because it contains salt. Therefore, fine suspended particles of clay that arrive in the brackish and salt water of the land/ocean environment are immediately reduced in surface charge, which helps them to coagulate and fall out of suspension.
Many such salts are available to water treatment operations, but in mining operations, we see the use of liquid cationic polymers (such as polyDADMAC) as a more common reagent.
A McLanahan High-Rate Thickener.
Flocculants are often made of long-chain polyacrylamide molecules that carry a negative, or anionic, charge. These reagents serve to attract positively charged particles, which attach to the negative charge sites on the molecule. As small particles of solids accumulate on the chains, an aggregate is formed and gains sufficient mass to drop from suspension, therefore creating a clean water phase and a thickened settled sludge zone in the bottom of the Thickener. Under this scenario, the accumulated mud has an appreciably higher solids concentration than the incoming feed. The water from which these particles settle rises up through the Thickener, where it flows over a peripheral weir into a collection launder. This water is usually directed to a large water tank, where it awaits use as recycled water in the plant.
How a Thickener can help you
Consider now what a Thickener can do for you. Below are two mass balances. On the left, you see a typical effluent stream from an aggregate plant. The Thickener in this case produces an underflow solids concentration of 35% solids by weight. As a result, the clarified water that exits the overflow is 1588 m3/hr. This represents an immediate water recovery in excess of 88%. This 1588 m3/hr does not get sent to the ponds, it is now available for reuse.
Moreover, if the Thickener and process water tank are placed local to the plant, the energy to bring water back from a distant pond is greatly reduced.
As mentioned above, Thickeners come in a variety of designs. The design that is right for your plant largely depends on your goals for handling the underflow slurry. The most common Thickener style in the mining industry is the High-Rate Thickener. This is because it is not only the least expensive from a capital standpoint, but it will often produce an underflow that is easily handled with conventional centrifugal slurry pumps — all while getting the most bang for the buck in returned water.
High-Density Thickeners may be considered if you are planning on dry stacking your fine waste by processing the sludge through a recessed Filter Press or similar device.
Paste Thickeners are utilized to gain maximum water removal by sedimentation methods alone. These units are designed to produce, as the name suggests, a paste. Pastes are defined as slurries in which there is no further separation of free water from the slurry.
Filtration
Further water recovery can be realized through the use of filtration methods. Such methods have historically been belt filter presses, but recent improvements and developments with recessed plate presses have shown that this latter technology offers many more benefits, including consistently drier filter cakes, no additional use of flocculant post Thickener and cake products that often hit compaction requirements for surface disposal. Considering the example given in the mass balance in the tables above, a recessed Filter Press could well improve the sludge solids concentration from 35% to perhaps 75-85% solids by weight. A similar mass balance for a press operation is given below:
Typical Recessed Plate Filter Press mass balance.
Combined with the Thickener above, the addition of a recessed plate press shows a 98% recovery of your process water. What goes to the settling pond? Nothing. There is now no need for a settling pond, as the cakes can be handled by conveyor or front-end loader and a haul truck.
Unlike others who may push cookie-cutter solutions, McLanahan can and will assist you with options for your specific needs in water recovery and tailings. Many factors come into play depending on your material characteristics, your water chemistry and the response gained from the operations described above.
To ensure that you are informed about the actual performances you can expect with your material, we maintain a lab in which we perform both static and dynamic settling tests, rheology characterization of the sludges produced, filtration studies and laser diffraction of particle sizes down through 0.1 micron. All these tests enable us to give you an eyes-wide-open expectation of what we can do together in assisting your operations.