Introduction
Lignite is a soft, low-grade coal formed from compressed peat. Also known brown coal, lignite has a low heating value due to its low carbon content and is typically used for the generation of electricity. It can also be used for the generation of synthetic natural gas, for the production of fertilizer and in fertilizer itself, for home heating, and for various other products and processes.
While lignite has its uses, it is often considered a contaminant in construction products, specifically concrete sand. The presence of lignite in concrete sand can cause structural and cosmetic issues with the final product.
Problems with lignite in concrete
Lignite is lighter than the aggregate that makes up the concrete, so it rises to the surface as the concrete hardens. This can potentially cause two main problems: staining and popouts.
Staining is caused by the brown color of the lignite, which can smear in the surface of the finished concrete product. Staining can be minor or severe, depending on the level of lignite contamination. This isn’t necessarily a deal-breaker in all construction applications using concrete, but ones where the appearance of the concrete surface is important, lignite stains can be unsightly.
Popouts are more worrisome than staining, as they can interfere with the structural integrity of the concrete. Lignite particles near the surface can expand, leaving holes or popouts in the concrete.
For these reasons, many concrete sand specifications allow only a minimal amount of lignite to be present. ASTM International’s specifications for C-33 concrete sand, which is used in the United States as well as some other countries, permit a maximum of 0.5% lignite if the surface quality is important and a maximum of 1% if surface quality is unimportant. Standards used by some other countries allow even less.
Several regions have developed a color test as a quick and visual reference of determining if the sand meets the requirements based on how the sand looks. Another, more accurate method is a burn test where the material is weighed before and after being subjected to heat. In this test, the lignite is turned to ash and presents a measurable loss of weight.
As lignite can be present in naturally occurring sand deposits, it is imperative that concrete sand producers remove as much of this material as possible to meet the specifications required in their region and to ensure a quality product.
Lignite contamination (the black particles) in a sample of sand
How to remove lignite from concrete sand
Lignite is typically removed during the wet washing stage of the production using various processes. One of the methods for removing lignite from concrete sand is with hindered settling equipment such as a Flat Bottom Classifier.
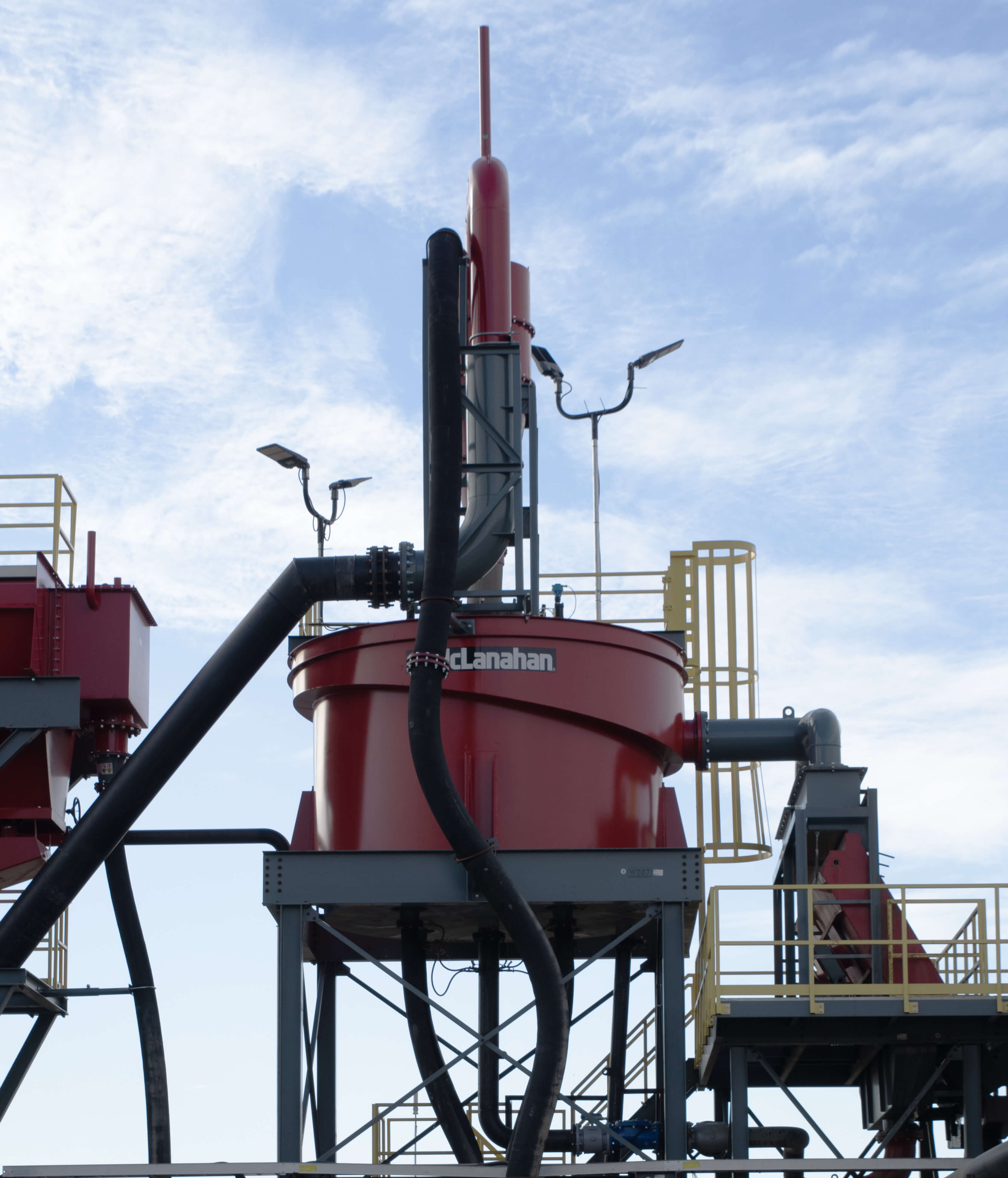
Flat Bottom Classifiers get their name due to the lack of an underflow discharge cone. Instead, Flat Bottom Classifiers contain valves that release the material. The flat-bottom style allows for use in areas with height restrictions, as the feed height of the plant is lower to the ground. This also decreases pumping power and structural requirements.
So how do they work?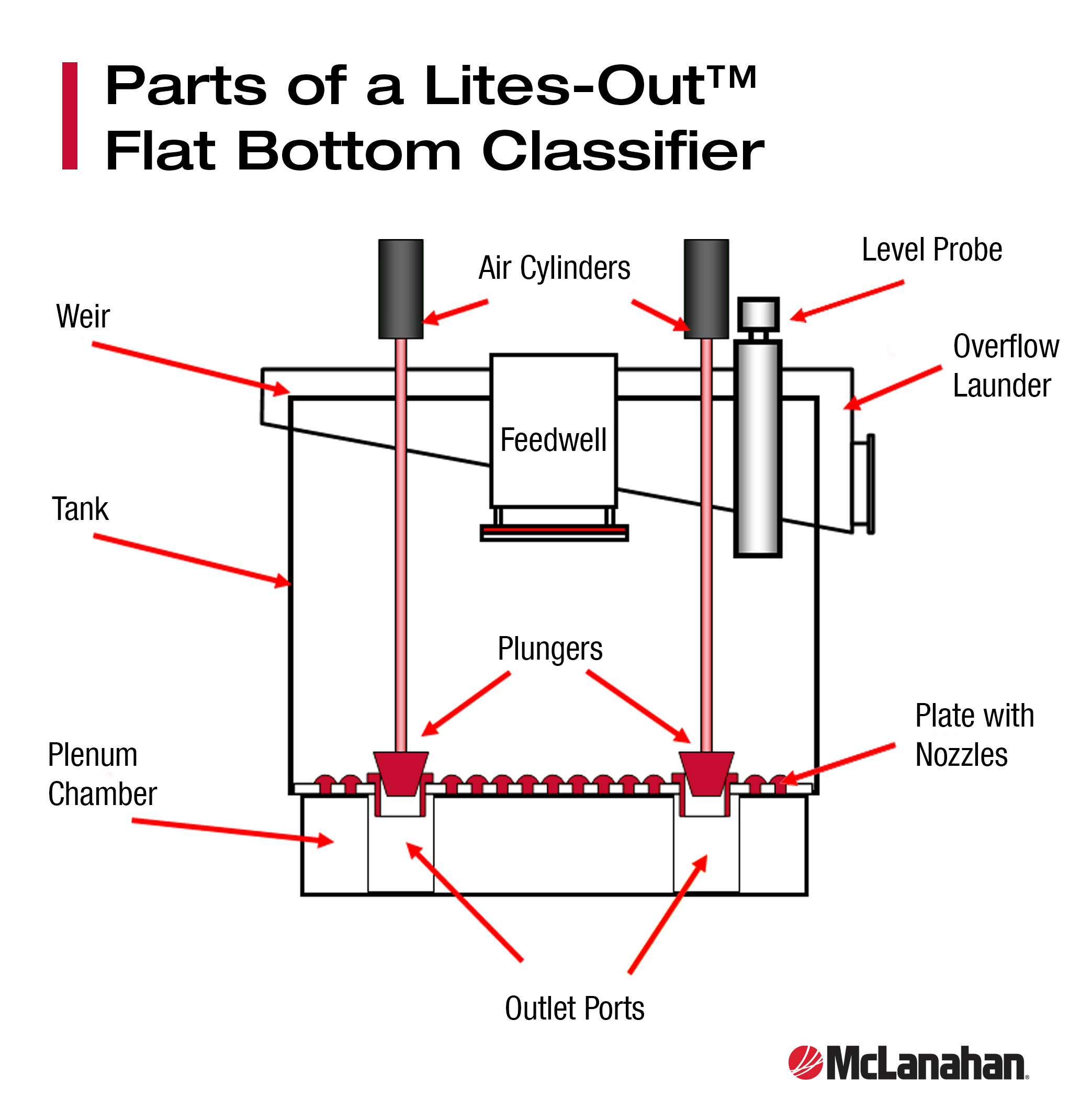
Flat Bottom Classifiers feature a plenum chamber near the bottom of the tank where water is injected. The use of a plenum chamber allows for a higher density of teeter nozzle, which spreads out the up-rising current more evenly. When this rising current of water meets the feed coming in at the top of the tank, a dense fluidized bed of near-size particles is formed. Coarse/heavy particles in the feed are able to penetrate the bed of material and fall to the bottom of the tank, where they are removed by valves and discharged to the next stage of the process. Fine/lightweight particles can’t penetrate the bed of material and are carried by the rising current of water to discharge over the weir surrounding the top of the tank.
When used in lignite removal applications, Flat Bottom Classifiers are able to separate the lightweight lignite from the heavier sand particles. Lignite has a specific gravity, or relative density, of about 1.3, compared to the specific gravity of sand, which is generally 2.7. The separation occurs because of this difference in specific gravity.
The amount of rising current inside the Flat Bottom Classifier is calculated to send coarse lignite particles into the overflow. Since coarse lignite particles are the highest contributor to popouts in a finished concrete product, removing them from the sand product is essential. However, because some fine product-sized sand particles may be light enough to overflow with the undesirable lignite (the fine sand being of a similar specific gravity as the coarse lignite), further separation of the overflow is often necessary after the Flat Bottom Classifier.
Typically, a sieve bend is used to separate the coarse lignite from the fine sand particles, which are then recombined with the underflow from the Flat Bottom Classifier and fed to dewatering equipment, such as Fine Material Screw Washers, Hydrocyclones and/or Dewatering Screens, for stockpiling.
Sieve bends are vertically curved screens that contain separation media. When the Flat Bottom Classifier overflow containing lignite and fine sand is fed onto the sieve bend, the sand particles pass through the openings in the screen media. The lignite particles that are too large to pass through these openings instead pass over the screening section and are sent to waste or used for site rehabilitation projects.
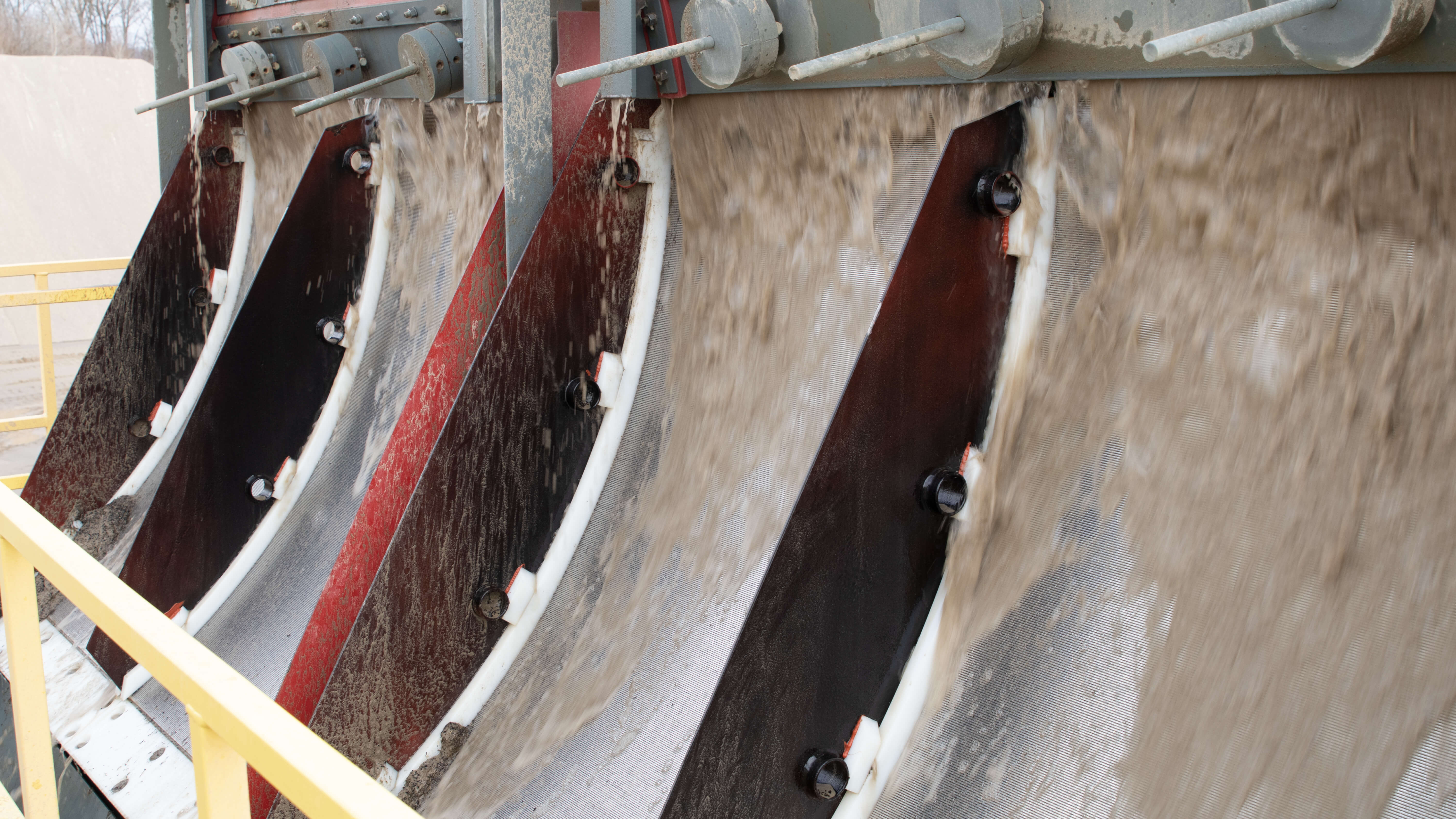
Small lignite particles that do pass through the screen media with the fine sand particles can be further removed with Fine Material Screw Washers, Hydrocyclones or even another Flat Bottom Classifier.
It is important to note that while this process is very efficient for removing lignite, not all lignite particles may be removed, and the sand may not be completely lignite-free. However, the sand will often meet required specifications with just the removal of the large lignite particles via the Flat Bottom Classifier.