Introduction
Washing is a process that removes deleterious materials, such as clay, dust, coatings and light vegetation, from rock, gravel and ore feeds to meet various specifications. Many different types of equipment are available for washing sand to a finished state, including individual machines and entire sand washing plants.
Determining how much a wash plant can cost depends greatly on what your site’s material processing needs are. The price of equipment can range from a few thousand dollars to a multi-million dollar system.
A McLanahan Sand Washing Plant.
Types of washing equipment
Wash plants can range from simple Fine Material Screw Washers for washing, classifying and dewatering sand to product specifications, to complete process systems that include myriad equipment to accomplish a variety of tasks.
Tasks of wash plants include:
- Feed preparation – to prepare a raw feed for processing by breaking down and removing clays and surface contamination
- Sizing – to screen the raw feed to reject the oversized material to further processing or waste
- Pumping – to transfer the slurry material from one process to the next
- Desliming – to remove liberated ultra-fine material before classification
- Wet classifying – to separate particles based on size or specific gravity
- Organics removal – to classify material based on specific gravity to remove organic material such as lignite
- Densifying and Dewatering – to concentrate a slurry to a specific density to feed to downstream equipment and to remove moisture from a product for improved stockpiling and quicker sale
- Effluent treatment – to recover process liquid from the waste stream for reuse in the wet plant
- Waste solids management – to separate liquids from the solids in a waste steam, where the liquid can be reused in the process plant and the remaining solids are stackable, to reduce or eliminate settling ponds
- Or a combination of any or all of the above processes
For feed preparation
The following equipment types are typically used in the feed preparation stage, which is the contaminant removal process before classification:
Attrition Cells | $$
Attrition Cells scrub the surface of particles to liberate and break down clays, oxides, chemicals and other contaminants to improve a sand’s durability and turbidity. They accept a top size of ½” (12 mm) and can handle high plasticity clays.
Often used in the feed preparation stage if multiple products are being processed, Attrition Cells can be found at any stage of the wet process to scrub material to improve the final product.
Four Attrition Cells as part of an aggregate washing plant.
Blade Mills | $$
Blade Mills are designed to liberate light, loamy clay or dirt from either coarse rock and/or sand before further processing. Blade Mills can be placed ahead of a wash screen to result in cleaner rock or ore, or ahead of a Sand Classifying tank or Fine Material Screw Washer in fine sand applications.
Blade Mills are not designed to remove tough, plastic clay or high percentages of clay. They usually work in conjunction with another type of processing equipment such as a Sand Classifying Tank or Wash Screen.
A Blade Mill has alternating paddles and flights on the shafts to scrub the material.
Coarse Material Screw Washers | $ - $$
Coarse Material Screw Washers are designed to wash crushed stone and gravel ranging from 3/8” to 4” (9.5 mm to 102 mm). They effectively remove light loamy clays, dirt crusher dust and coatings that cannot be removed by wet screening alone.
They also can be used to take out floating vegetation and soft aggregate, although all vegetation and water-logged sticks may not be removed completely. Coarse Material Screw Washers are not intended to remove tough plastic clay.
A Coarse Material Screw Washer.
Log Washers | $$
Log Washers remove tough, plastic clay from natural and crushed gravel, crushed stone and ore feeds. Log Washers must have a controlled top size, with the larger machine sizes being able to accept a feed material up to 6” (152 mm) cubed.
It is recommended that the sand-sized fraction be removed prior to the Log Washer, since the finer material tends to cushion the washing action. This sand fraction should only be fed to the Log Washer when severe washing of fines is required.
When processing fines, it is necessary to capture the overflow of the unit to save this fraction for further processing or close off the overflow opening so that material is carried the full length of the box for scouring of the fines.
A Log Washer.
Rotary Scrubbers | $$$ - $$$$
Rotary Scrubbers are designed primarily for the removal of loam and light clays and soft, soluble waste materials from aggregates, stone and ore. They are not intended for use in applications where tough plastic clays are contaminating the material to be cleaned.
When these tough clays are fed to a Scrubber, the clay particles have a tendency to pelletize through the tumbling action of the material and, instead of breaking down, may actually increase in size.
Rotary Scrubbers can accept large feed sizes, up to 10-12” (254-301 mm), and they are sometimes used as a primary washer before any crusher or screening is accomplished.
Two Rotary Scrubbers.
For special washing and screening applications, a Scrubber Screen (a combination of Rotary Scrubber and Rotary Trommel Screen) can be effective.
For sizing
Vibratory Screens ($ - $$) are used to separate material according to size. These can be horizontal or inclined with a varying number of screen decks depending on the application. In a wash plant, Vibratory Screens are used to screen the raw feed into fractions appropriate for downstream processing.
An Inclined Vibratory Screen.
For pumping
Slurry Pumps ($ - $$) are used to transfer material, in the form of a slurry, from one process to the next. Gravity-fed plants can be an alternate option, but Slurry Pumps are able to capture all salable materials that may be lost to waste in gravity fed operations.
A Slurry Pump.
For desliming
Hydrocyclones ($) are the preferred method for removing ultra-fine material before the classification process due to their high shear and efficiency. Adding a Hydrocyclone or Hydrocyclones before a Sand Classifying Tank or Screw Washer in feeds with high fines can improve the performance of these machines.
A Hydrocyclone.
Feed Regulating Sumps can also be used in high volume applications, such as dredge operations. These devices remove fine material from the feed by allowing it to settle in the base
For wet classifying
Wet classification is the process of separating particles based on size or specific gravity. The following types of equipment are often used for classifying sand:
Sand Classifying Tanks | $$
Sand Classifying Tanks are used to remove excess water in a dilute slurry feed, to classify material by removing an excess of intermediate sieve sizes, to retain finer mesh sizes and to make multiple products from a single feed material.
Sand Tanks can work with either a slurry or dry feed. They handle gradation swings in the average plant while minimizing waste. The discharge from a Sand Tank must be further processed in a Fine Material Screw Washer or Dewatering Screen.
A Sand Classifying Tank.
Sand Tanks are generally used in sand and gravel plants, as well as manufactured crushed stone sand plants.
An optional rising current classifier can be installed in the first two or three stations of a sand tank. The rising current classification improves sand classification by injecting fresh water near the slurry feed entry to deter the settling of fine sand until later in the sand tanks. This allows for higher sand product yields when re-blending coarse, intermediate and fine sand for construction grade specifications.
Fine Material Screw Washers | $ - $$
Fine Material Screw Washers are primarily used to dewater, classify and wash minus 3/8” (9.5 mm) sand or fine minerals. These machines are designed to accept feeds from a belt conveyor or slurry feeds from washing vibrating screens, Sand Tanks, Hydrosizers®, Hydrocyclones or other Fine Material Screw Washers.
The product-sized sand sinks to the bottom of the Fine Material Screw Washer washer box and is conveyed up the incline toward the discharge, while fine particles float over the weirs with the overflow liquid.
A Fine Material Screw Washer.
Hydrosizers® | $$
Hydrosizers® are used to make extremely sharp cuts between 150 and 30 mesh using the hindered settling principle. These devices accept feed sizes up to ¼” (6 mm) and handle wide fluctuations in solids feed rate without affecting performance.
Hydrosizers® have the highest efficiency of all wet gravity equipment in a smaller footprint and are typically used for creating specialty sands like glass, frac, filter, sports and foundry.
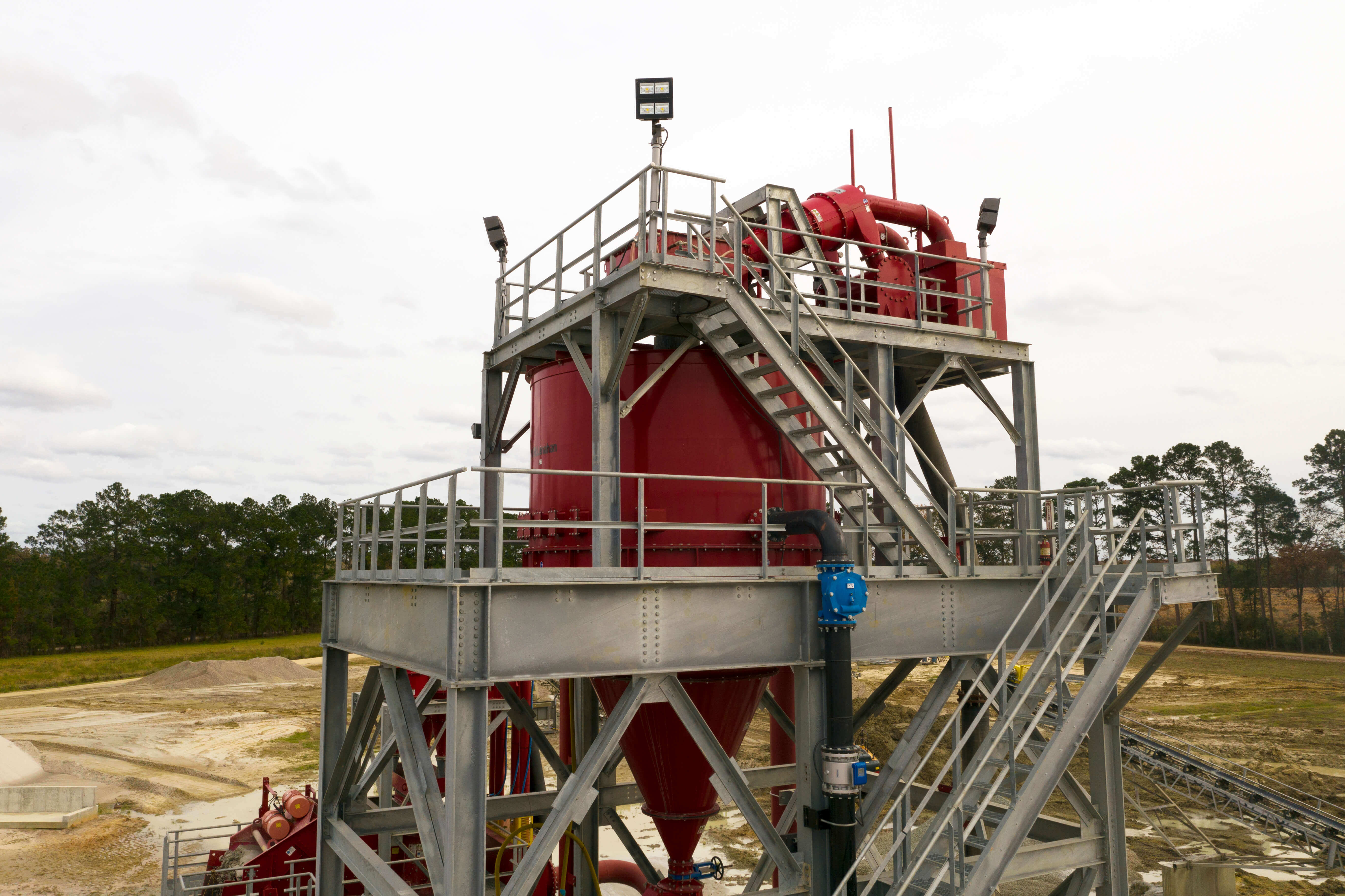
Hydrocyclones feeding a Hydrosizer®.
Hydrocyclones | $
Hydrocyclones can be used in many different parts of a wash plant. They can be used for desliming, as aforementioned, but they (and their variant the Separator™) can also be used for classification of sizes 140 mesh and finer.
A group of Separators™.
In fines recovery applications, Hydrocyclones can capture down to 400 mesh of a typical 2.7 SG material.
Hydrocyclones have no moving parts, so they generally require a pump in order to function, which is an additional cost to consider.
For organics removal
For classifying material based on their specific gravities, such as necessary with organics removal like lignite, a Hydrosizer® or Lites-Out™ Flat Bottom Classifier ($$) can be used to remove these materials from a <4 mesh sand stream.
Similar to Hydrosizers®, Flat Bottom Classifiers rely on hindered settling and a dense fluidized teeter bed of near-sized sand to float off lightweight materials (like lignite) while the heavier sand fractions pass through the bed for discharge.
A Lites-Out™ Flat Bottom Classifier.
For densifying and dewatering
When dilute slurries need to be concentrated before being fed to equipment like Hydrosizers® or Attrition Cells, Separators™ are often used.
Separators™ are modified Hydrocyclones that offer the ability to control the density of the underflow discharge. In this way, it can provide a denser slurry when necessary, either before downstream process equipment or for stockpiling directly.
To remove moisture from a final product, a Fine Material Screw Washer, Separator™ or Dewatering Screen ($) can be used. Fine Material Screw Washers dewater material as it is conveyed up the incline by the rotating screw shafts inside the machine. The material typically discharges around 20% moisture from a sand screw.
Separators™ were invented to provide underflow density control when stockpiling a final product. The addition of an underflow regulator, overflow pipe and siphon valve to an otherwise typical Hydrocyclone allow the density to be adjusted, preventing low densities that could wash out the stockpile.
Dewatering Screens offer the most moisture removal, discharging products at as low as 7% moisture. These devices are used in a wide variety of applications to provide a drip-free product that is stackable and conveyable for improved stockpile management and housekeeping.
The addition of a spray bar on a Dewatering Screen to wash out excess fines also helps to improve sand equivalency in the final product.
A Dewatering Screen.
For effluent treatment
Though not necessarily a part of the washing process, Thickeners ($$$ - $$$$) are used to recover immediately reusable process water, up to 85%, for reuse in the wet plant. With water being a valuable resource as well as an important part of the wet process, recovering as much as possible for reuse helps improve site sustainability, as well as reduces water buying costs and reduces the amount of material reporting to the settling pond.
A Thickener.
For waste solids management
A washing process is inevitably going to contain a waste stream containing the water and liberated deleterious material. An UltraFINES Recovery Plant ($$) containing a Hydrocyclone and Dewatering Screen can be used to capture fine particles in the waste stream to reduce the load on downstream equipment and/or the amount of material reporting to the settling pond, as well as create a potential salable product from the recovered material.
An UltraFINES Recovery Plant.
A Thickener can be used to recover up to 85% of the water from the waste stream for reuse, while a Filter Press ($$$ - $$$$) can separate the solids from the liquid in the remaining slurry, providing additional process water and a stackable, conveyable, potentially salable product from the solids that would have typically gone to waste.
A Filter Press.
So, how much does a wash plant cost?
The cost of a wash plant depends largely on the material you are processing and your production goals. The material being processed and capacity required will dictate the size and therefore the investment to be made in equipment (larger equipment for higher capacities will cost more money), as well as how many pieces of equipment are required.
For example, extremely dirty material may require several of the same piece of equipment in series to achieve the desired quality end product, while extremely high capacities may require more than one of the same piece of equipment to meet production goals.
You also need to factor site restrictions and/or site sustainability into the design of your wash plant, which will have an impact on upfront costs.
For example, if you live in an area where water is scarce or expensive, you may want to invest in a Thickener and/or Filter Press to recover the water for reuse in the plant. This could lead to a larger upfront investment, but one that will have a higher overall ROI.
A McLanahan Frac Sand Plant and Thickener.
If you have a small site footprint or are tired of spending thousands of dollars to muck out a settling pond only to fill it back up again, you may want to consider adding equipment like an UltraFines Recovery Plant, Thickener or Filter Press, or combination of all three, to your wash plant. Each of these helps to decrease the amount of solids reporting to waste, reducing the size of — and in some cases the need for — settling ponds.
Adding tailings management equipment will increase the capital expense of the wash plant, but the long-term maintenance and housekeeping benefits may save you money down the road and may even yield a salable product.
You many also want to invest in a mechanical sampling system. Mechanical Sampling Systems are used for collecting a final product from a conveyor belt or product stream without having to stop the flow of material. Though not part of the washing process itself, these automatic Sampling Systems ($ - $$$$) are a great device for ensuring final products are meeting specifications.
The more equipment and features you add to your wash plant, the higher the investment, which is why it is important to test your material before arriving at a solution. The best wash plant will give you a clean, in-spec product at your desired capacity with the highest return on investment.
Finally, you’ll also want to take into consideration any ancillary equipment costs, such as supporting structures and conveying/stacking systems, that are typically not included in the cost of the plant. Stationary plants that require a large support structure are typically more expensive than a pre-engineered modular plant.
McLanahan's UltraWASH Modular Plant.
However, stationary, modular and portable plants are not always interchangeable for every site. Modular and portable plants are limited in throughput, so a stationary plant may be the best financial decision for a site that needs to process high volumes.
Conversely, a stationary plant may not make sense for a site with multiple locations or a site with a short lifespan on reserves where ROI will be realized sooner with a modular or portable plant. This is where knowing your site and your site’s goals comes into play.
In regard to material handling, knowing how many products or material streams you need to move to a stockpile or other part of the process, as well as how far you need to move them, will help you to determine how many conveyors and/or pipes you will need and what length they will need to be.
While capital cost immediately comes to mind when considering washing equipment, long-term cost savings from reduced maintenance, improved site sustainability and potential additional salable products should be considered when purchasing a wash plant.