Introduction
Frac sand is a high-purity silica sand used as a “proppant” in the hydraulic fracturing (or “fracking”) industry. The basic function of frac sand is to hold open the fissures created by the horizontal drilling of the earth to allow the oil and natural gas to flow through toward the wellhead.
To be classified as frac sand, sand grains must be round and spherical in shape, resist crushing and be free of impurities. These characteristics make frac sand ideal for use in fracking because they allow the sand to withstand extreme pressures and optimize conductivity, which is a measure of how easy it is for oil or natural gas to flow through the sand.
Frac sand processing involves several steps before it can be used in the wellbore. These steps can include extraction, wet processing, drying, final sizing and testing. The wet processing stage is just a small portion of this, but it plays a key role in the production of high-quality frac sand, ensuring the sand meets the tight tolerances required.
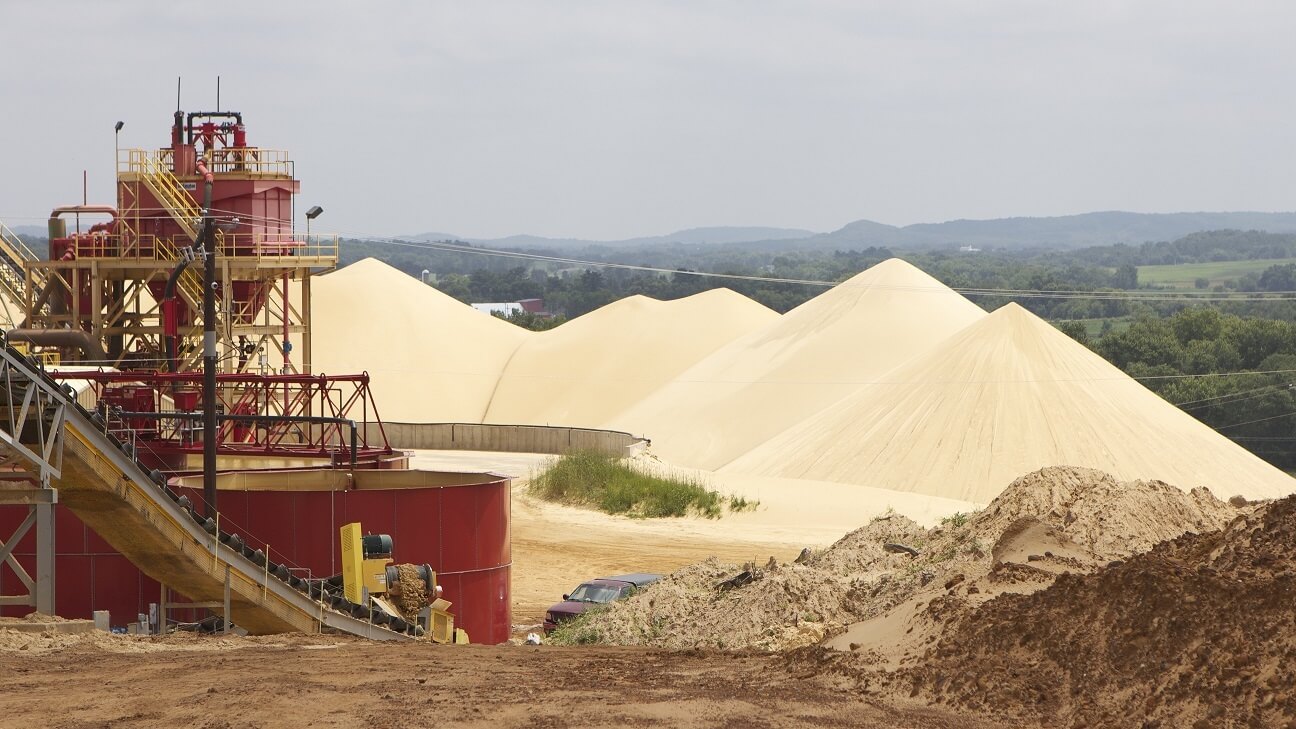
Technology for wet processing frac sand
After mining, frac sand typically undergoes a wet process to prepare the natural silica sand to feed the dryer and final sizing screen. The goal of the wet process is to wash the sand free of impurities, such as clay, and classify it into the size range needed by the end user.
Wet processing frac sand ahead of dry sizing reduces the load on the dryers and sizing screens. The wet processing stage typically includes the following steps:
- Screening and classification
- Washing and scrubbing
- Dewatering
- Tailings and water management
Screening and classification
The wet processing of frac sand typically begins with screening and classification. The coarse-end separation can be made using Horizontal or Inclined Vibratory Screens. Horizontal Screens are ideal for portable plants or applications with limited vertical space. Inclined Screens, which utilize gravity to assist in separation, require less horsepower and can handle larger tonnages.
These units can make as fine as an 8-mesh separation (depending on the deposit) when used as a primary screen; in some instances, secondary screens can be used to make a finer 30-mesh cut.
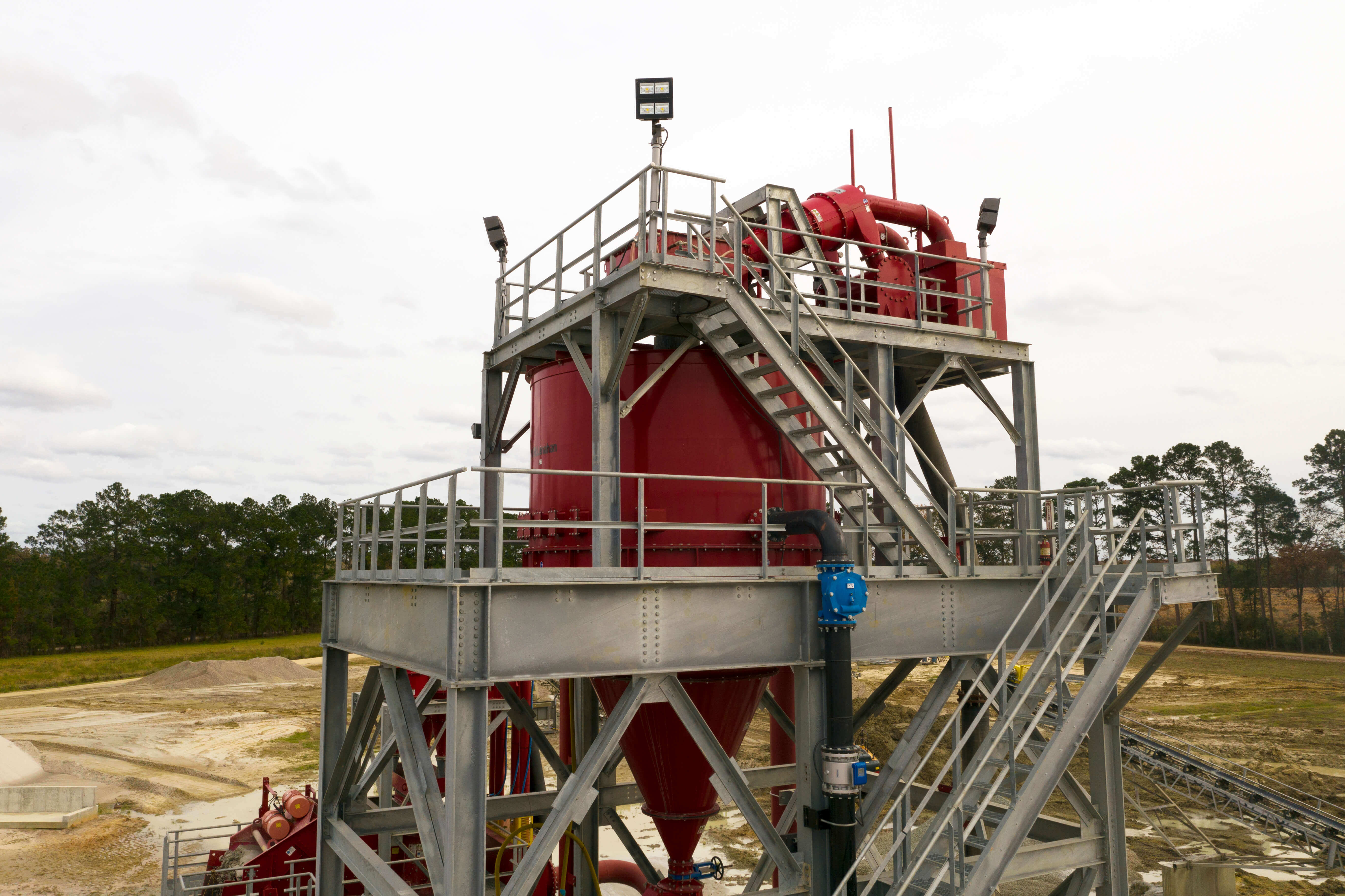
For the fine-end separation, hydraulic classifiers are often used to make sharp cuts in the range of 30 to 140 mesh. Hydrosizers® are one type of hydraulic classifier. They operate based on the principle of hindered settling, in which the settling of particles is impeded by other particles. Hydrosizers® are ideal for separating sand grains based on size or density using an upward flow of water.
The upward flow of water when met by the downward flowing feed of material to be classified creates a bed of near-size material known as a teeter bed. Larger or heavier particles are able to pass through this teeter bed to discharge out of the Hydrosizer® for further processing, while the smaller or lighter particles are not able to penetrate the bed and are carried out the top of the Hydrosizer® with the wastewater.
Hydraulic classifiers such as Hydrosizers® have a smaller footprint and cost compared to screens, and they offer cut point adjustments on the fly. The market has changed significantly over the years in the specifications of sand used in fracking, so it is incredibly beneficial to have on-line adjustability in the primary cut points.
Washing and scrubbing
After classification, the sand may need to be washed and/or scrubbed to remove clays and other impurities that can affect the turbidity of the sand. Turbidity is a measure of the cloudiness of a fluid caused by suspended particles, such as dirt, silt or clay. In other words, turbidity is a measure of how dirty the sand is.
Hydrocyclones can be used for desliming the sand, removing clays (typically minus 200 mesh material) from the classified sand. Separators™, siphon-assisted Hydrocyclones, allow for more consistent cut points than a Hydrocyclone when there is variation in the feed and provide more efficient washing of clays and other fines.
For heavier contamination, Attrition Cells/Scrubbers provide a more aggressive scrubbing to liberate stubborn clays, stains or other deleterious material that have adhered to the sand grains via particle-on-particle attrition. After, the material is sent to a Hydrocyclone to separate the liberated clays from the sand.
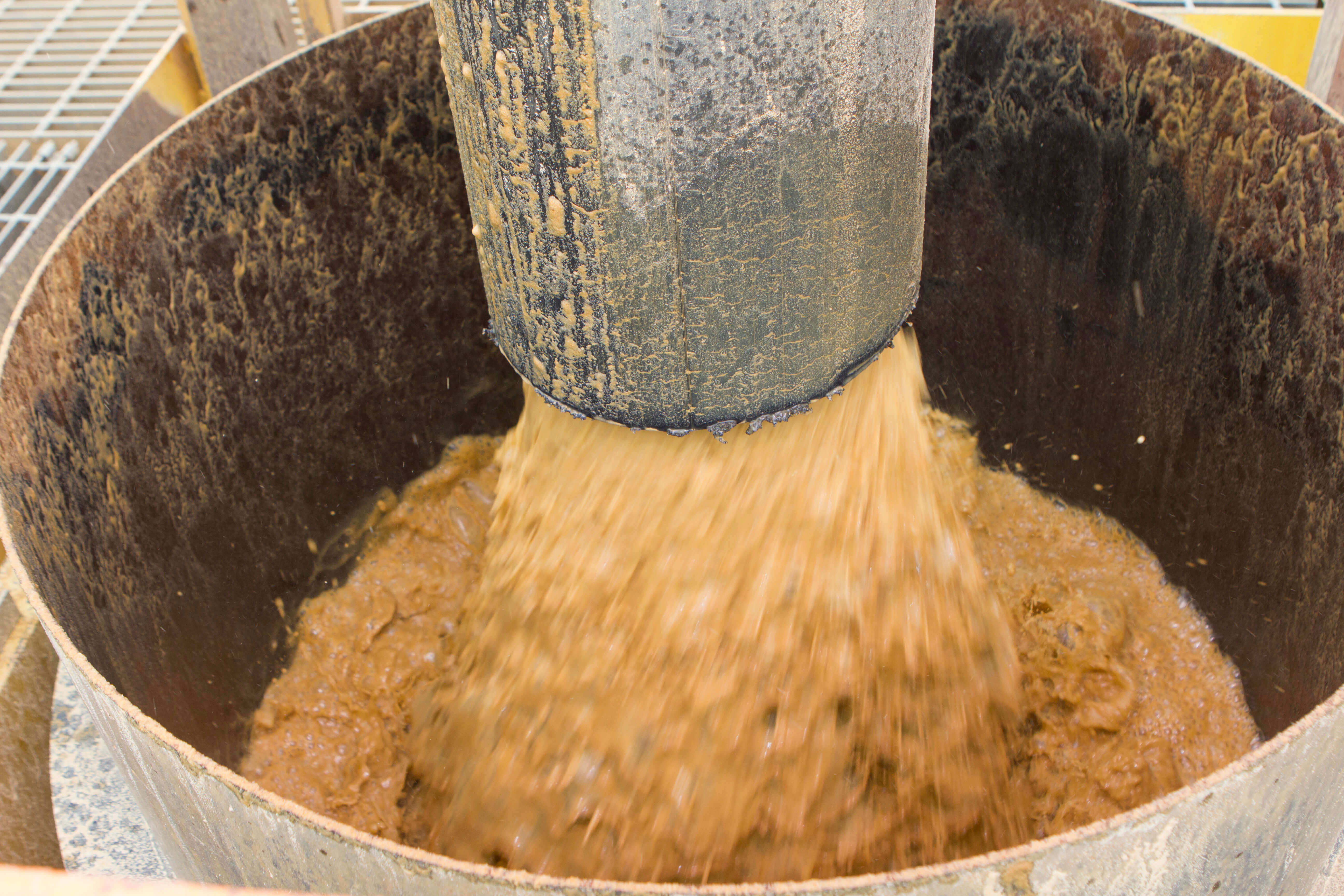
Dewatering
Dewatering is the last step in the wet process before stockpiling for drying and sizing. It is crucial because the wetter the sand, the more expensive it is to dry. Reducing the moisture content of the sand ahead of the dryer reduces the fuel consumption required to hit target moisture levels, thereby reducing the overall drying costs.
Once the frac sand has been washed to remove impurities, the dewatering stage removes excess moisture from the sand grains. This limits the amount of time and stockpiling space required before the sand has reached the desired moisture to put in the dryer.
Dewatering Screens are highly effective for removing excess moisture from frac sand. These units discharge drip-free sand, often in the range of 10-15% moisture (though this depends on the size and density of the material being dewatered).
In addition to reduced moisture content in the sand, Dewatering Screens have the added benefits of a final rinse of the sand, creating neater stockpiles, less water runoff on site, less mess underneath conveyors and reduced conveyor maintenance.
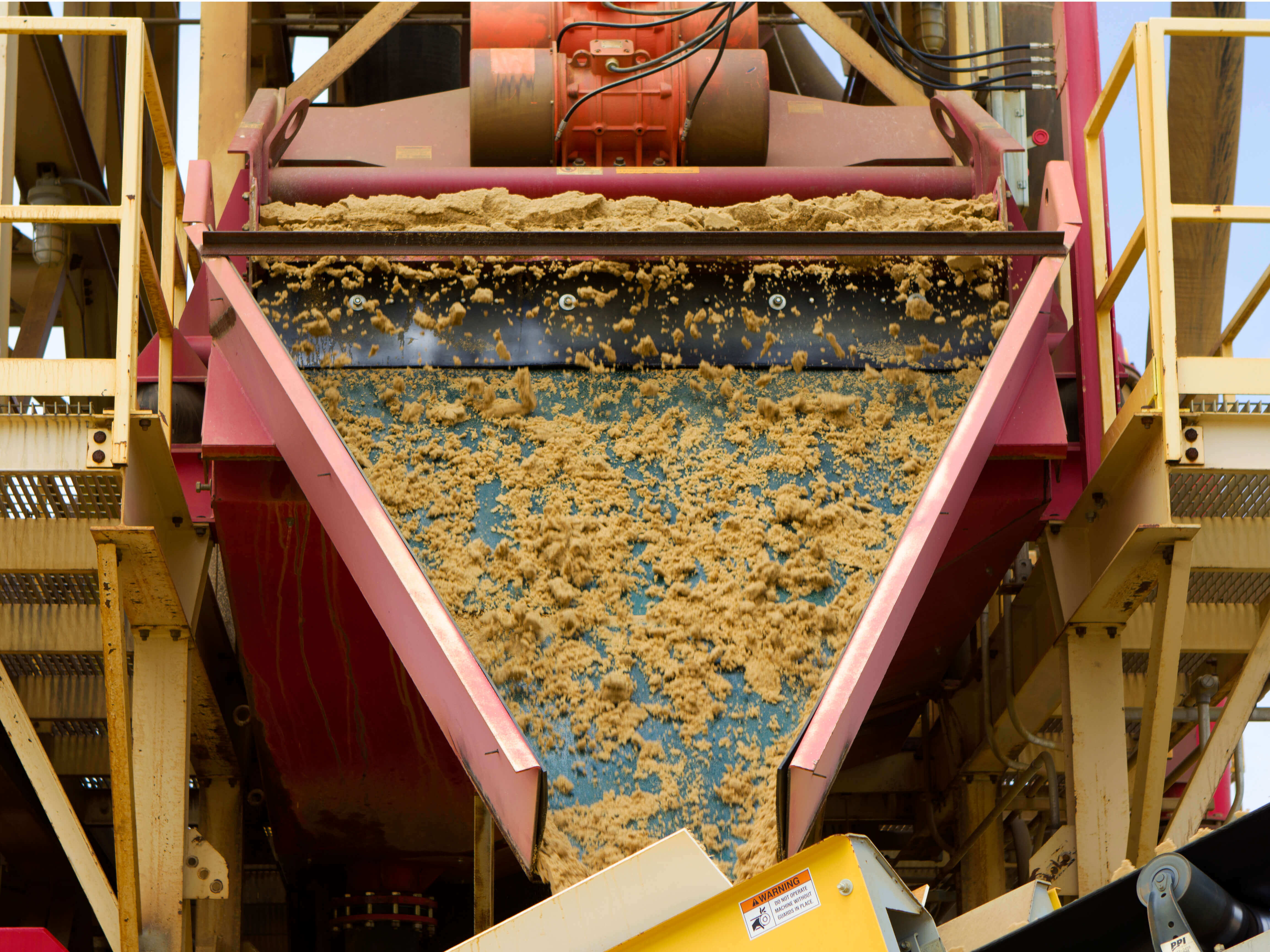
Separators™ can also be used for dewatering frac sand for stockpiling. While developed and used successfully for this purpose, Separators™ discharge material with a higher moisture content than Dewatering Screens, so the product must sit on the ground to drain for longer in the stockpile before it can be sent to dry sizing.
Tailings and water management
After the frac sand is stockpiled for dry sizing, producers need to manage the waste stream from the wet process. The waste stream includes the non-frac sand sizes, as well as the clays and process water used in the classification, washing, scrubbing and dewatering stages.
Ultra Fines Recovery Plants composed of Hydrocyclones and a Dewatering Screen are used to capture fine material (typically 400 mesh) from the waste stream. This material can potentially be sold, adding another revenue stream for the frac sand producer. By removing fine solids from the waste stream, Ultra Fines Recovery Plants reduce the load on downstream processing equipment and/or reduce the volume of material destined for the settling pond. This then reduces the frequency of pond cleaning and pond size requirements.
To further reduce or even eliminate the need for settling ponds, as well as recover immediately reusable process water, Thickeners, Centrifuges and Filter Presses can be considered. Wet processing frac sand requires more water than wet processing construction sand, but around 90% of this water can be recovered for reuse with a Thickener.
Thickeners are used to concentrate the waste slurry up to 60% solids, depending on the type of Thickener. This underflow can be sent to a much smaller pond than required for the entire plant effluent. To eliminate the pond completely, the Thickener underflow can be sent to a Centrifuge or Filter Press for further liquid-solid separation. Centrifuges and Filter Presses also recover immediately reusable process water and discharge a solids material that can be more easily moved with mechanical handling equipment such as conveyors and loaders. This material also has the potential for sale as backfill or pond lining, or it can be used for on-site reclamation.
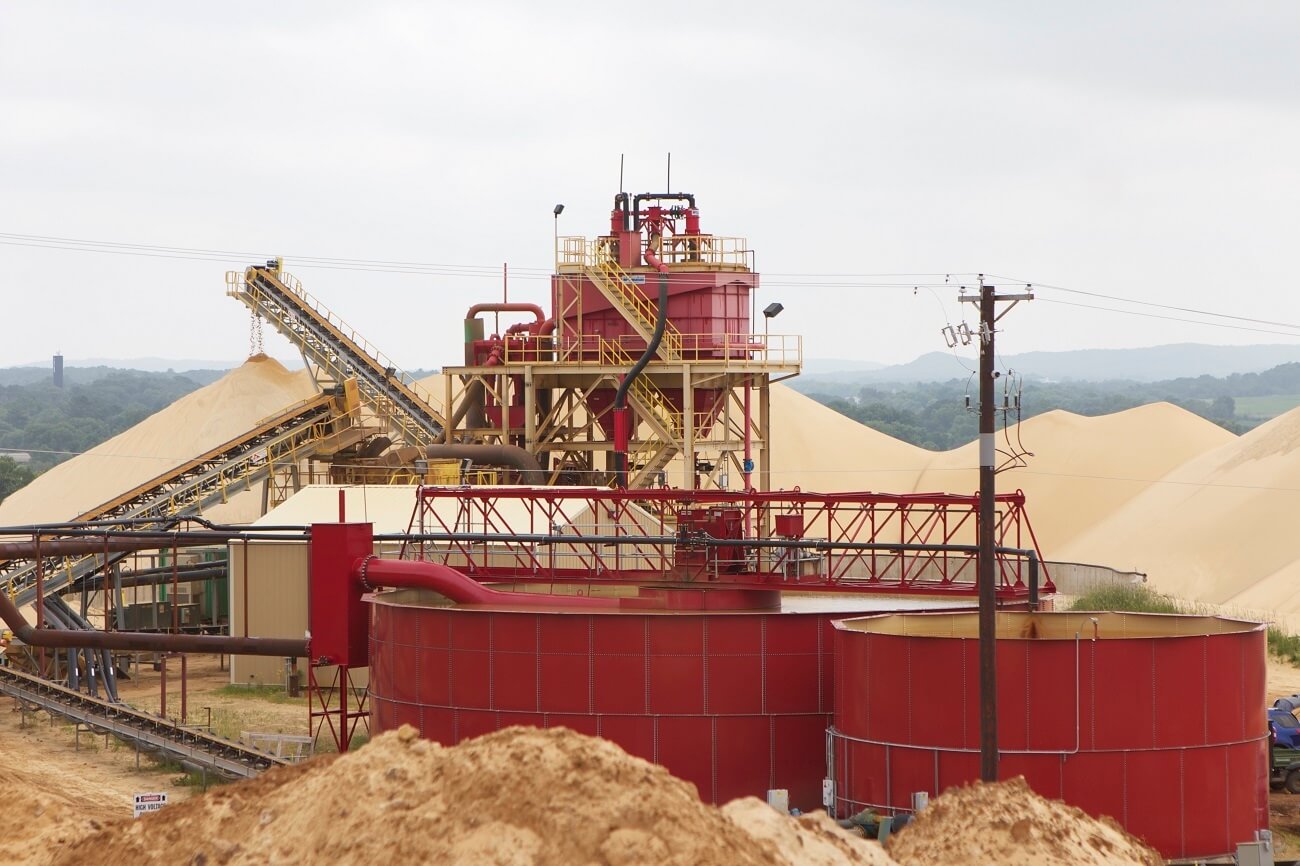
Frac sand must meet strict specifications for particle size and cleanliness, and wet processing is imperative to ensure the sand meets these requirements. Vibratory Screens can be used to make the coarse-end separation in some applications, while hydraulic classifiers like Hydrosizers® are key for producing the fine-end separation. Attrition Cells/Scrubbers are ideal for removing tough, stubborn clays to improve the turbidity of the sand, but Hydrocyclones and Separators™ can offer an effective washing if the sand grains are relatively clean. Dewatering Screens and Separators™ can be used to dewater the sand ahead of stockpiling for dry sizing, though Dewatering Screens are able to achieve much lower moisture content. Finally, Ultra Fines Recovery Plants, Thickeners, Centrifuges and Filter Presses can be used on the back end of the wet process to recover fine solids, recycle process water for reuse, and reduce or eliminate settling ponds.