Introduction
Flat Bottom Classifiers and Hydrosizers® are both part of an equipment class known as hindered settling classifiers.
Hindered settling classification creates a suspended field, or teeter bed, that restricts smaller or lighter particles from passing through. Larger/heavier material passes through this teeter bed and is removed in the underflow, while the smaller/lighter material is carried into the overflow. Compared to free settling classifiers, in which the settling velocity is determined by gravity, hindered settling classifiers produce an upward velocity through a reduced underflow opening and/or injection water. This type of settling offers the highest separation performance, meaning it makes the sharpest cut.
Hindered settling classifiers are used to make a size separation between 20 mesh and 140 mesh at a much sharper cut than other types of wet gravity separation. They require a steady supply of clean water, with the amount of water required depending on the desired cut. A coarser cut requires more water than a finer cut, because more water is required to separate the fine particles away from the coarse particles.
The height of the teeter bed is important for classification. High teeter beds allow for a higher-quality material in the underflow, while low teeter beds allow for higher recovery of material.
Hindered settling classifiers are available in three main designs recognizable by the shape:
- Square with dewatering cone
- Round with dewatering cone
- Round with flat bottom (no dewatering cone)
Square Hydrosizers®
Square Hydrosizers® feature rectangular tanks with a dewatering cone at the bottom. Slurry feed (typically from a Hydrocyclone) enters the tank though a feedwell at the top center of the tank. At the same time, water is injected via downward facing nipple-style nozzles in the top of the dewatering cones. This creates an upward rising current of water that meets the feed slurry entering from the top of the tank.
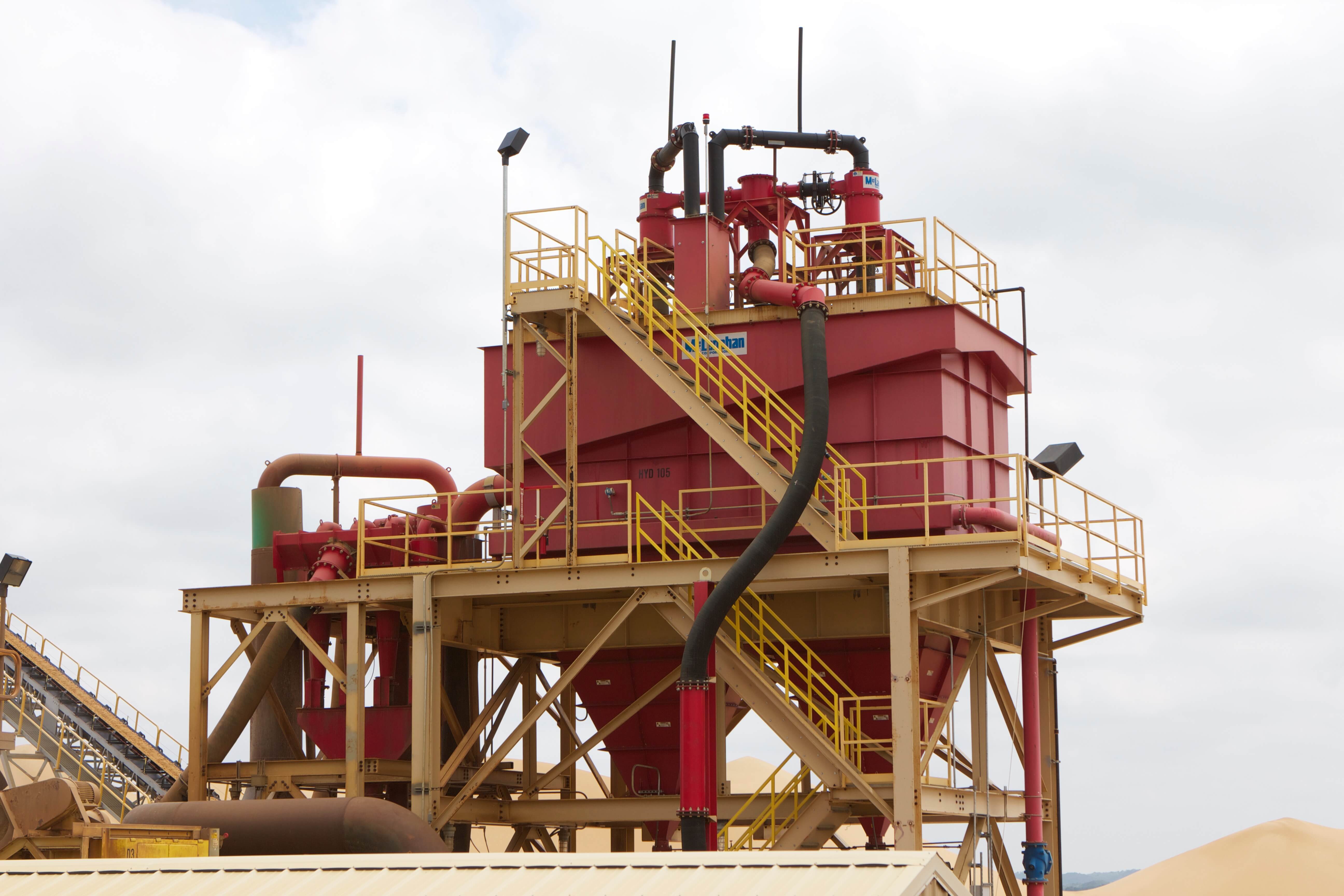
As particles try to settle through the rising current, a dense bed of near-size solids form that teeter on the edge of separation. For this reason, the dense bed of particles is called the “teeter bed”.
Heavy/coarse particles pass through the teeter bed into the dewatering cone, where they are discharged via an automatic discharge valve at approximately 60% solids by weight. Light/fine particles cannot penetrate the teeter bed. These particles rise with the water and are carried out the overflow.
The main advantage of this design is the ease of changing out the teeter water nozzles. The teeter bars are generally removable from the side, so it is not required to enter the unit to replace the nozzles.
Round Hydrosizers®
Round Hydrosizers® feature a cylindrical tank with a dewatering cone at the bottom. Similar to Square Hydrosizers®, feed enters through a central feedwell at the top of the tank, where it is met by an upward rising current caused by the injection of water into downward-facing nozzles at the top of the discharge cone to create a teeter bed. Light/fine particles overflow the weirs at the top of the unit, while heavy/coarse particles make their way to the dewatering cone for discharge via a single valve at approximately 65% solids by weight.
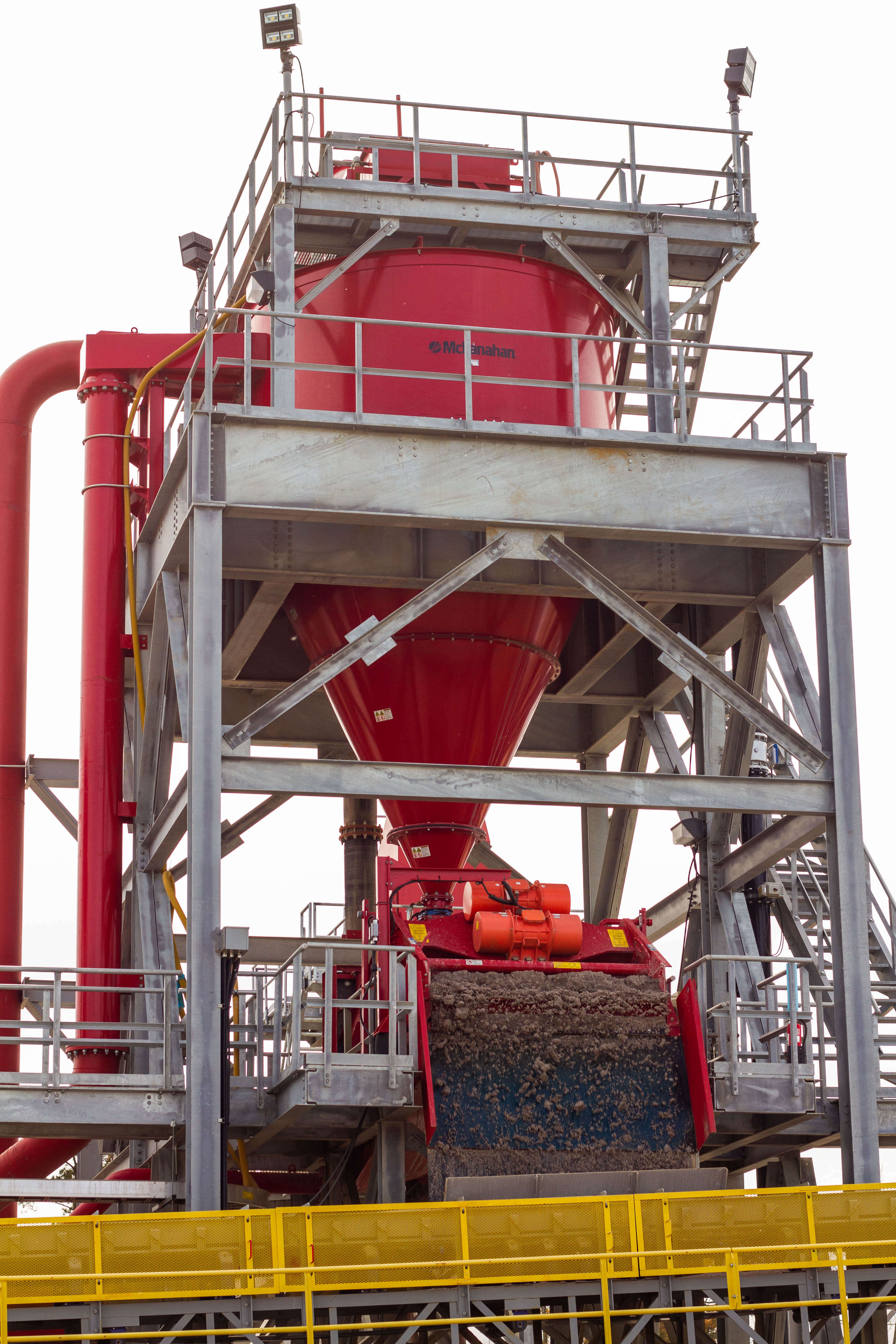
Because of the round tank design, Round Hydrosizers® may be more efficient than their square counterparts. This is because the overflow weirs are equidistant from the feedwell and the lack of corners in the round design for material to build up, potentially creating dead zones of material.
Changing out the teeter water nozzles may be more difficult on this design, as the side teeter bar removal is complicated by the round chamber.

Hydrosizers® can be used in a wide variety of applications, including the production of various specification sands, precious and base metals, coal, iron ore, slag, organics removal and more.
Flat Bottom Classifiers
Flat Bottom Classifiers feature a cylindrical tank with a flat bottom. While the principle of hindered settling is the same as with Hydrosizers®, Flat Bottom Classifiers feature some physical and operational differences.
First, Flat Bottom Classifiers are designed with the plenum chamber for the teeter water at the bottom of the tank, as well as a diffusion plate featuring dome-shaped nozzles through which water is injected upward into the tank. The teeter water is distributed evenly and at the same pressure across the settling chamber. This design requires an individual to enter the chamber in order to change out the teeter water nozzles.
Similar to Hydrosizers®, the slurry feed meets the rising current of water to form a teeter bed. Fine/light particles overflow the weirs at the top of the tank, while the coarse/heavy particles are discharged out the bottom of the tank.
Because they lack the dewatering cone present in Hydrosizers®, Flat Bottom Classifiers feature on/off valves or top-down dart valves at the bottom of the tank. These valves open at designated intervals to release the settled particles that have accumulated at the bottom of the tank.
Flat Bottom Classifiers also feature an overflow sensor for monitoring the specific gravity of the upper region of the settling chamber.
Flat Bottom Classifiers are commonly used by aggregate producers for making construction and specialty sands, but they can also be used for the separation of minerals and in soils washing. They are also ideal for the removal of lignite from sand in aggregate applications to improve the durability of the final product.
For lignite removal applications, Flat Bottom Classifiers are typically paired with a Sieve Bend to complete the system. Because small sand particles may be of the same specific gravity as the larger lignite particles, some small sand particles may overflow the Flat Bottom Classifier weirs with the lignite. The overflow is directed to a Sieve Bend or similar screening device to further separate the lignite from the sand. The small sand particles pass through the screen media and join the underflow from the Flat Bottom Classifier, while the larger lignite particles flow over the screen to waste.
Discharge valve type
The type of valve and control strategy is important for the stable and consistent operation of any application. The modulating pinch valve is the most common, especially in the units with a dewatering cone; however, this type of valve provides the lowest level of control. The opening action of the pinch valve can allow large swings, especially when the feed to the unit is fluctuating, but when the feed is relatively steady, the pinch valve will provide a constant discharge from a single point.
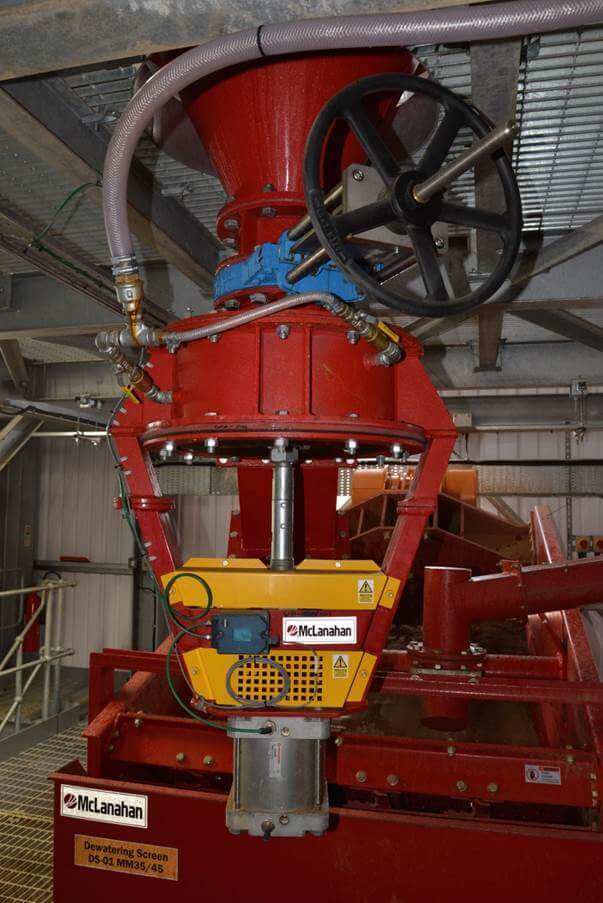
Other valve options include top dart valves, on/off pinch valves and linear dart valves. Top dart valves offer a simple and straight forward method of control. They handle swings in the feed well but usually require discharge from multiple points.
On/off pinch valves are a variant of the top dart valve. These can be beneficial over dart valves in some applications because dart valves are set in the slurry and can get clogged.
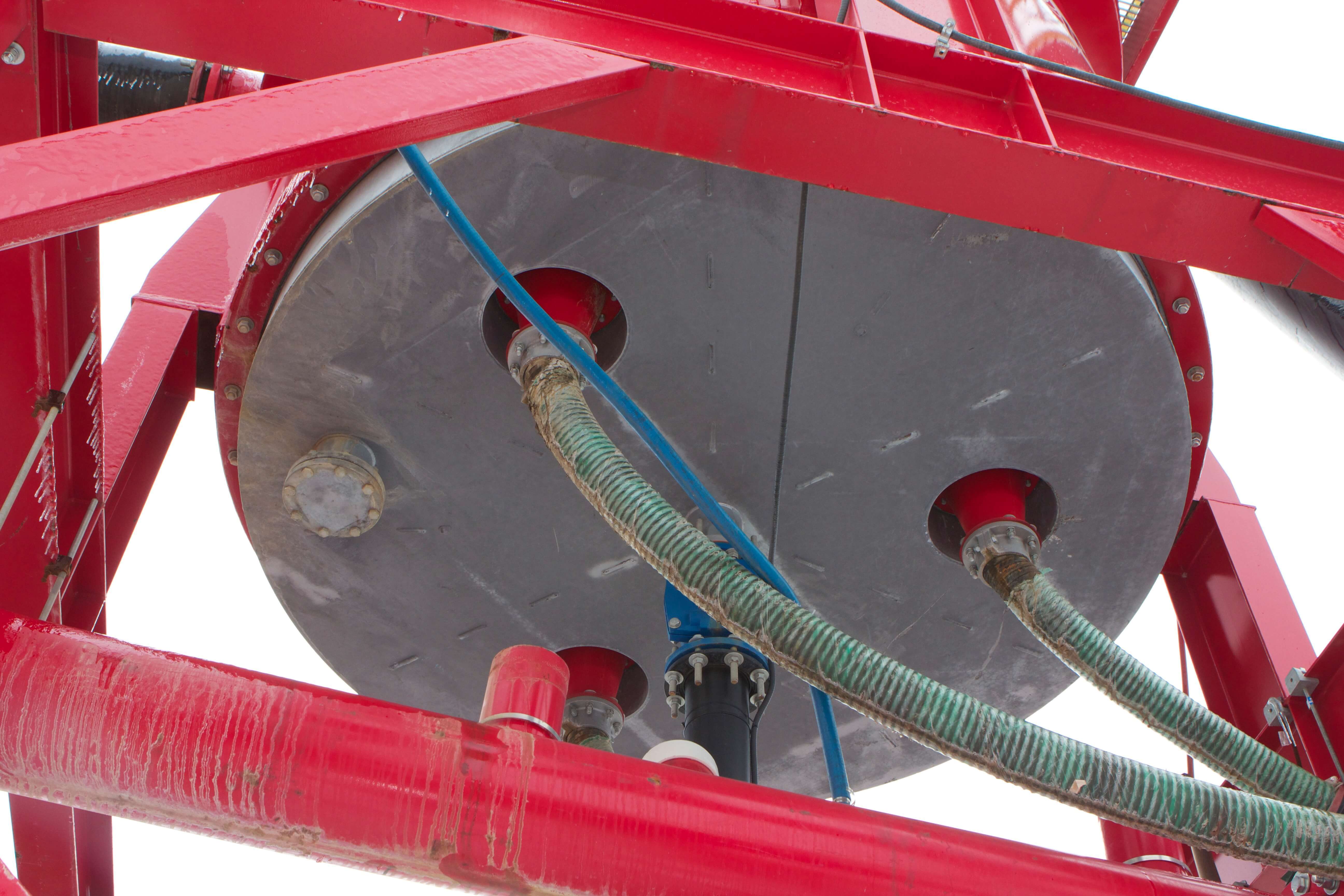
Linear dart valves are similar to modular pinch valves, but they provide a linear control for the underflow discharge to help minimize swings.
Cone bottom vs. flat bottom
When it comes down to performance, Flat Bottom Classifiers and Hydrosizers® with dewatering cones have basically the same cut efficiency.
However, Flat Bottom Classifiers can be more stable during feed fluctuations. They feature a smaller area of unclassified material due to improved water distribution via the plenum chamber and diffusion plate. Flat Bottom Classifiers are advantageous if height restrictions and/or vertical profile are of concern.
Hydrosizers® offer 5-10% better dewatering of the final product than Flat Bottom Classifiers, with a higher percent solids in the underflow. Hydrosizers® also cost less than the flat-bottom style.
The best choice for an application will depend on the characteristics of the feed material and the end product specification.