Introduction
When selecting the proper Roll Crusher for an application, you must fully consider all the components of the crushing process.
There are numerous factors to be considered, such as:
- Material to be crushed
- Feed size
- Product size
- Ratio of reduction
- Capacity
- Compressive strength
- Moisture content
- Amount and type of refuse present in the feed
- The definition of fines and if minimizing fines generation is beneficial
All of these factors, and possibly others, should be considered so that the proper crusher is selected for the application. Let’s look at how some these factors can influence the crusher selection process.
Material to be crushed
The material to be crushed plays a major role in the proper equipment selection. Consideration needs to be given to the following:
- The friability or grindability of the material, which is typically referred to as the Hardgrove Grindability Index (HGI)
- The hardness in compressive strength (psi)
- Other factors, such as moisture and abrasiveness:
- Is the feed material a tacky, clay-type material that requires more of a shearing/tearing action?
- Is it friable where compression crushing is applicable, or is it a hard material that requires impact?
If the material is hard, shock loading may occur and therefore special consideration needs to be given to the crusher design and drive configuration. Some materials are considered too hard for Roll Crushers and may need to be tackled by a Jaw, Impactor or Gyratory crusher.
McLanahan Double Roll Crusher.
Therefore, the material characteristics determine the duty class of the equipment to ensure that the crusher is competent for the intended application.
Feed size
Once the material is known, one of the primary factors to consider is the feed size. The top size of the feed material along with the required product setting must be considered for properly selecting the roll diameter and width.
Diameter
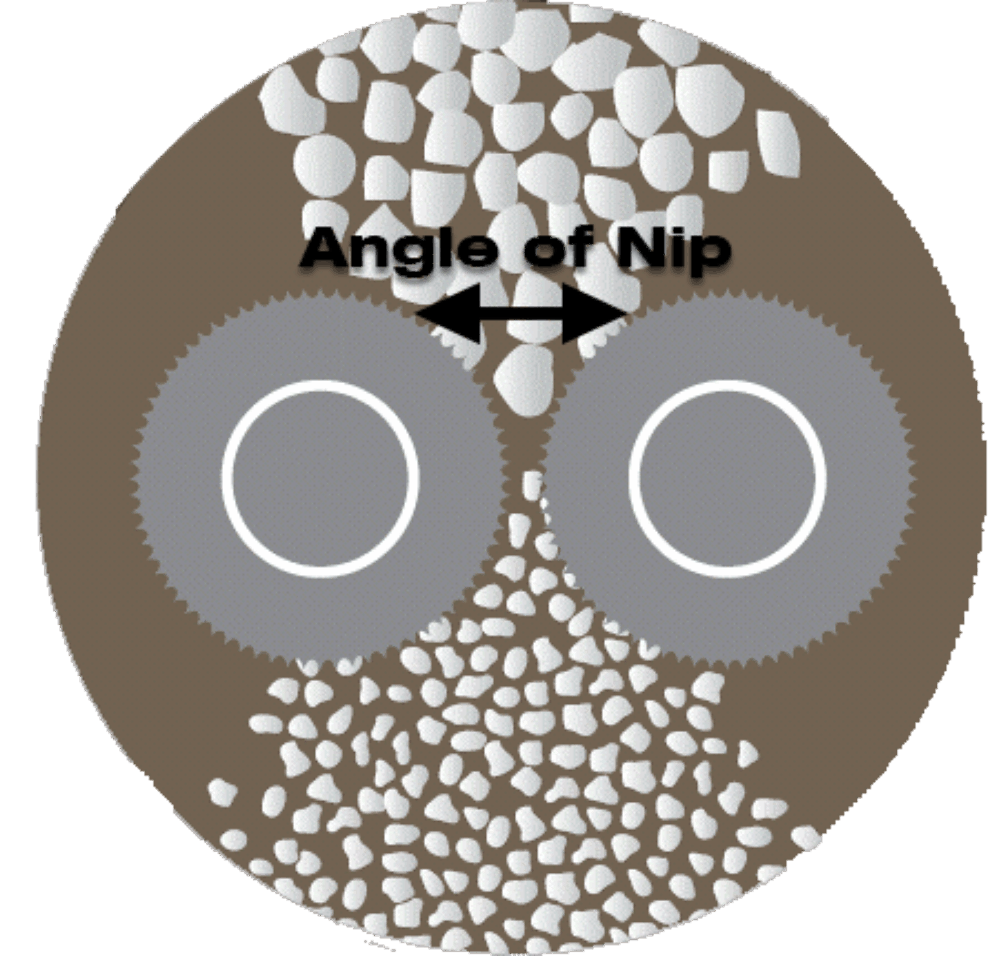
The roll diameter has to be sized correctly to provide an adequate angle of nip, as shown in the photo on the right. This angle of nip ensures that the crusher has the ability to grab the feed material and pull it into the crushing zone without delay.
If the roll diameter is insufficient in this regard, a few issues begin to occur, most notably loss of capacity and accelerated wear of the crushing elements.
If the angle of nip is insufficient, it can lead to the feed material riding on top of the rolls while the crusher is attempting to grab and process the material. When this happens, you inhibit material flow and diminish the throughput capacity of the crusher, which may result in material backing up and plugging the feed chutes.
Also, as the material rides on top of the crushing rolls, it begins to act as a grinding agent, thereby accelerating the wear of the crushing elements.
Width
The width of the crusher must also be considered when taking into account the feed size.
Selecting a crusher that is too narrow compared to the size of the incoming feed can result in the bridging of the feed material across the crusher opening. When this occurs, once again, throughput capacity is diminished and plugging of the chutes can occur.
It is good practice to size the width of the rolls to 1-1/2 to 2 times the size of the largest feed lump even though the capacity requirement of the application may be lower than what the crusher can produce.
Required product size
Next to be considered is the required product size.
When taking this into account, you must also refer back to the feed size to see if the ratio of reduction requires multiple stages of crushing.
A good rule of thumb for single-stage crushers is that a Single Roll Crusher provides up to a 6:1 ratio of reduction and a Double Roll Crusher provides up to a 4:1 ratio of reduction.
In the event that the application requirement exceeds the guidelines discussed herein, dictating more than one crushing stage, then a determination will have to be made as to whether a single two-stage crusher or two individual crushers should be employed.
If the two-stage crusher is selected, consideration has to be given to the overall headroom available. When selecting a two-stage crusher, feed size generally dictates if a Triple Roll Crusher or Quad Roll Crusher is the appropriate choice.
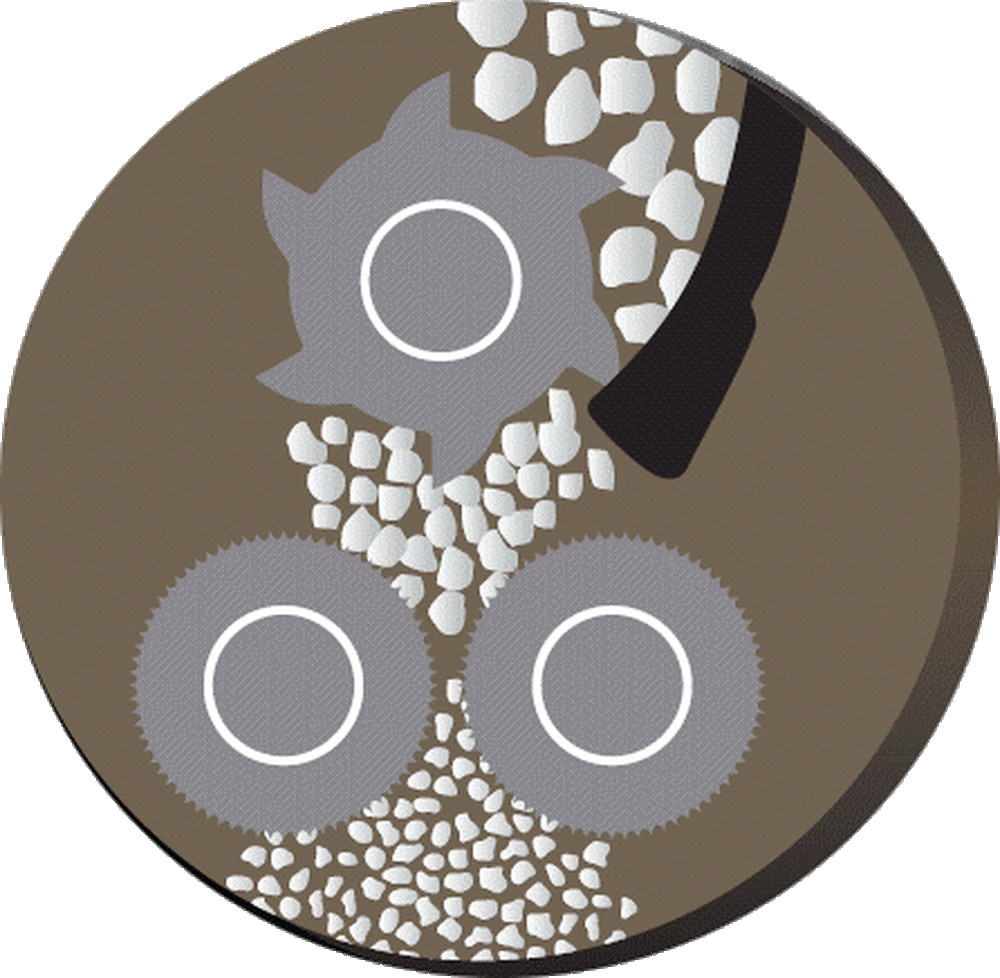
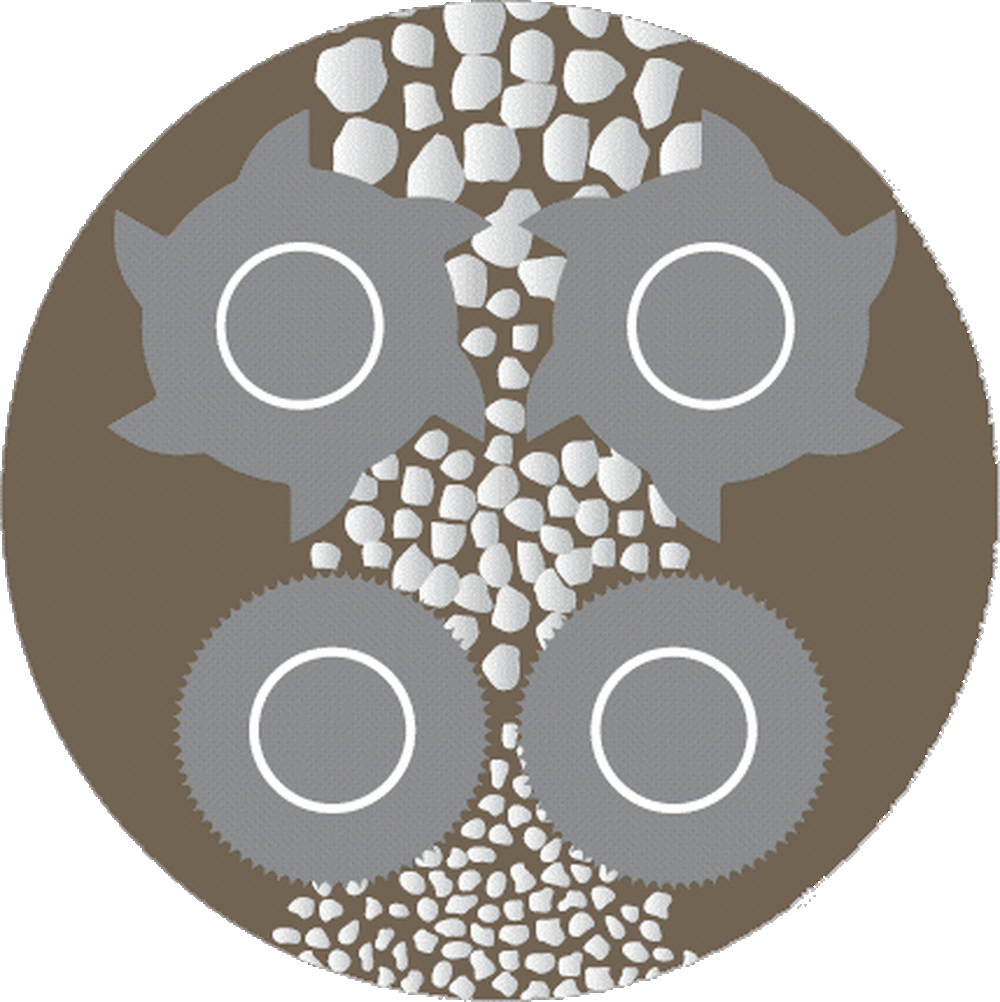
When larger feed sizes require up to a 6:1 ratio of reduction to achieve the final product, a Triple Roll Crusher should be chosen due to the inherent design, which allows the larger feed sizes to be readily grabbed in the large throat opening between the top (primary) roll and crushing plate. If the feed-to-product-size can be accomplished with 4:1 and 4:1 ratios then a Quad Roll crusher can be considered.
Tooth configuration
At this point in the selection process, the tooth configuration required to produce the desired product size and the proper metallurgy for the application can be selected.
There are a multitude of tooth patterns, designs and configurations available on Roll Crushers today. Selecting the correct metallurgy and tooth configuration is extremely important to maximize crusher capacity, product shape and sizing and wear life.
Metallurgy and tooth configuration is an important aspect of Roll Crusher selection.
Improvements in quality to castings and availability of more exotic metals has created a desire for better wear elements. McLanahan Corporation worked closely with one of our suppliers to develop a weld-on carbide tooth, which initially was developed to provide the coal industry with extended wear life of their crushing elements. The success in this area has led to extended offerings to other mineral processing industries.
Flowability
Consideration must also be taken in reference to the flowability of the feed material and if it has a tacky, clay-like quality.
- Are roll scrapers or differential roll speeds required to provide a self-cleaning action to prevent material build-up on the roll surfaces?
- Is water being added?
The differential in roll speeds imparts compression crushing but also the added benefit of a tearing/shearing action. Sticky, clay-like material has the possibility of building up between the stages of a two-stage machine and eventually plugging between the stages. In many cases, your only option in instances such as this is to employ two single-stage machines.
Throughput capacity
Throughput capacity of a crusher has multiple variables, which are taken into account when calculating crusher capacity. With Roll Crushers, 100% of the material flow is processed between the roll bodies or roll and crushing plate. The space created between the width of the rolls and the distance from roll-to-roll or roll-to-crushing plate must be calculated using the following variables:
- Roll diameter
- Roll width
- Roll speed
- Gap setting
- Bulk density
- The crushing factor of the feed material
Knowing these factors and taking into account how each material reacts in the crushing process helps determine the overall crusher selection.
Once all the information is gathered, then the proper crusher(s) can be selected. In some instances, multiple crusher options and combinations are available for the same application, and the ultimate decision is left up to the operator or contractor.
In the end, many factors play a part in the selection of the proper crushing equipment, and in many applications, there is more than one correct choice. A crusher manufacturer should be contacted to review your application details and outline all the available options to provide a professional recommendation for your mineral processing project.