Rotary Breakers are one of the most suitable pieces of equipment for scalping off undesirable material and performing size reduction in a single operation. Designed primarily to process run-of-mine coal feeds, Rotary Breakers can accept large lump sizes at high capacities. They are durable, low-maintenance, low-power-consumption machines.
Rotary Breaker design and working principle
Rotary Breakers consist of a cylinder that rotates at a relatively slow speed on four trunnion rollers. Thrust rollers mounted on the base frame at both ends of the Rotary Breaker prevent lateral movement as the cylinder rotates.
A conventional Rotary Breaker drive uses an electric motor/coupler/reducer drive configuration. A large driven sprocket is bolted to the machined circumference of the cylinder’s feed end, while a smaller drive sprocket is mounted to the reducer output shaft. An engineered chain connects the two sprockets and is enclosed in an oil bath chain case.
The cylinder is covered by a dust housing to contain fugitive coal dust. The dust housing is equipped with replaceable dust seals and inspection doors to facilitate maintenance.
ROM coal and refuse that enter the cylinder are picked up by internal steel lifters and carried to approximately the 11 o’clock position on the cylinder diameter. From there, the material drops onto the screen plates that line the inside. This lifting and dropping action, coupled with the impact of the harder refuse, causes the coal to break and pass through the screen plate openings. The repeated lifting and dropping action effectively reduces the coal and passes it to the product stream, while uncrushable waste material continues to advance through the cylinder.
The lifters are adjustable for advancing and retarding the flow of material through the Rotary Breaker.
The waste material is then discharged out of the opposite end of the cylinder, assisted by discharge plows bolted to the end section.
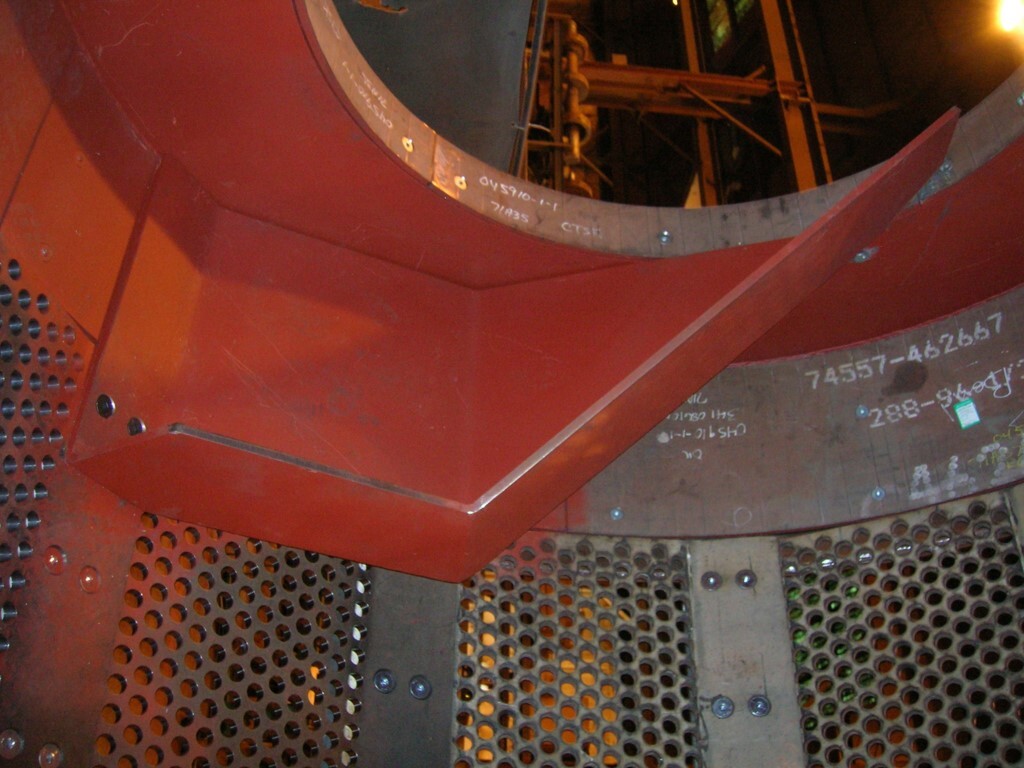
Sizing and selection
When considering what type of crushing equipment to use to reduce ROM coal, the characteristics of the feed material are often one of the most important factors. This is especially true when the ROM coal stream contains significant quantities of refuse, such as rock, timbers and similar uncrushable waste material that can be a nightmare for downstream processing.
Crucial to the selection process is gaining a thorough understanding of the material to be crushed and the refuse that may be encountered. Refuse may consist of hard rock, pyritic sulfur balls, clay, mine timbers and roof bolts.
For any coal crushing application, the following factors must be considered when selecting the right type of crusher, sizer or breaker for the job:
- Material to be crushed
- Feed size
- Desired product size
- Capacity required
- Type of and percent of refuse in the feed
- Percent of oversize and of half size
- Hardness of the coal
- Moisture content
- Gradation
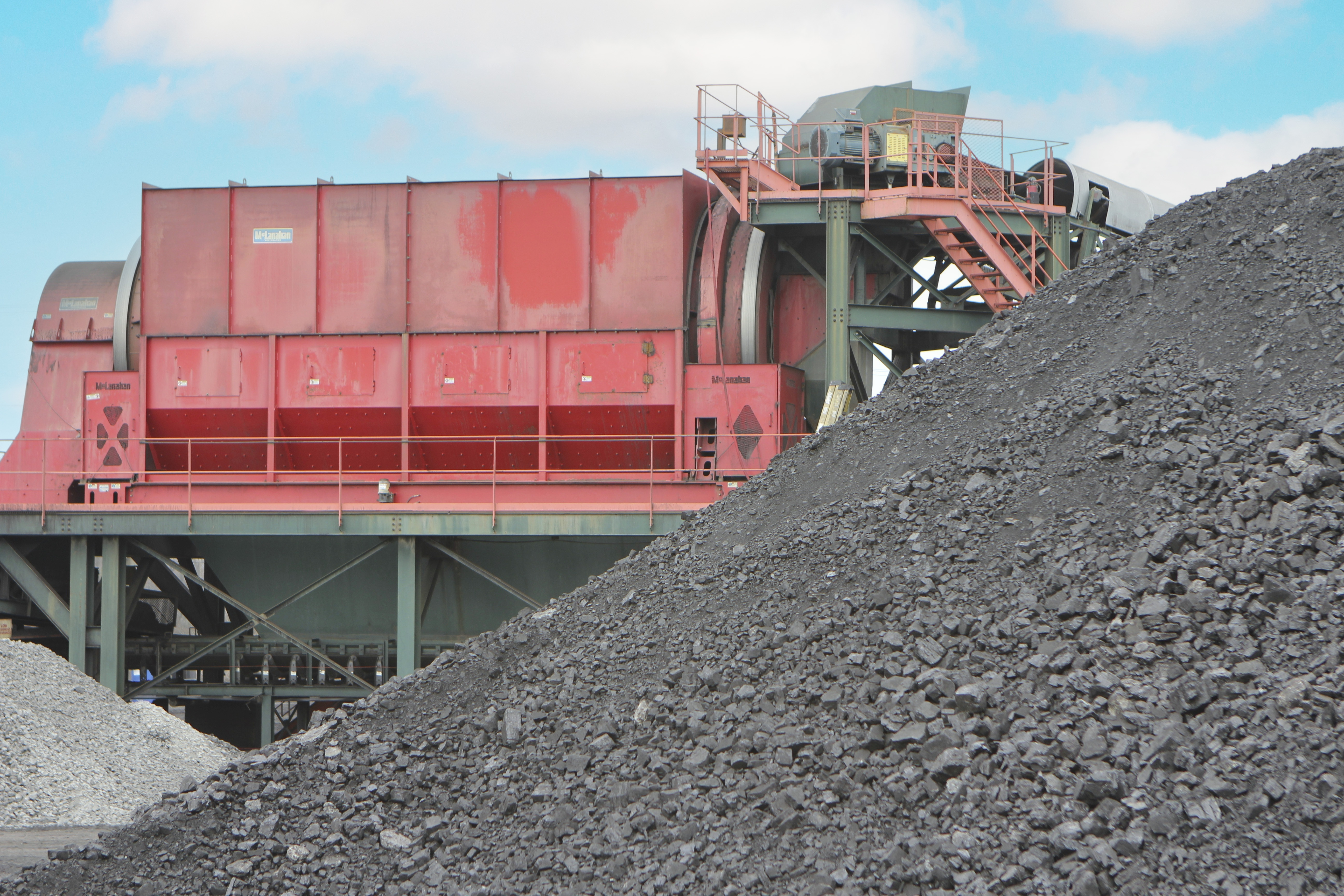
Rotary Breakers perform most effectively on soft to medium-hard coal with a significant percentage of rock. Coal that is too hard or too woody may not break down and can lead to product being discharged with the reject material. Not enough harder refuse in the feed may prevent the coal from breaking as desired. Refuse that is too soft and breaks easily may pass through the screen plates and compromise the quality of the final product.
It is imperative that the hardness of the coal and refuse is identified. Refuse is considered any material that is not identified as coal, such as shale, slate, clay, sandstone or limestone. The hardness or grind of the coal is usually expressed as a Hargrove Grindability Index (HGI) number, while refuse is typically measured by its compressive strength in psi.
Moisture content and the presence of clay in the feed material must also be recognized. Moist fines and clays can plug the screen plate holes and can also cause a cushioning effect on the falling material, inhibiting the ability of the coal to break apart on impact. An all-in feed is acceptable; however, it is recommended that a scalping screen be installed prior to the Rotary Breaker to remove the undersized material, thus increasing the efficiency of the Rotary Breaker.
Diameter and length
Rotary Breakers are typically referenced by their diameter and length, with a variety of sizes available. Drop shatter testing can confirm the size required for an application. Establishing the most favorable drop height aids in determining the breaker diameter, while the number of drops help to determine the breaker length.
Screen hole size
Throughput capacity and desired final product size are also vital to selecting a Rotary Breaker. A Rotary Breaker’s maximum capacity is relative to the product size it is required to produce. The smaller the screen plate openings equates to a lower the capacity rating.
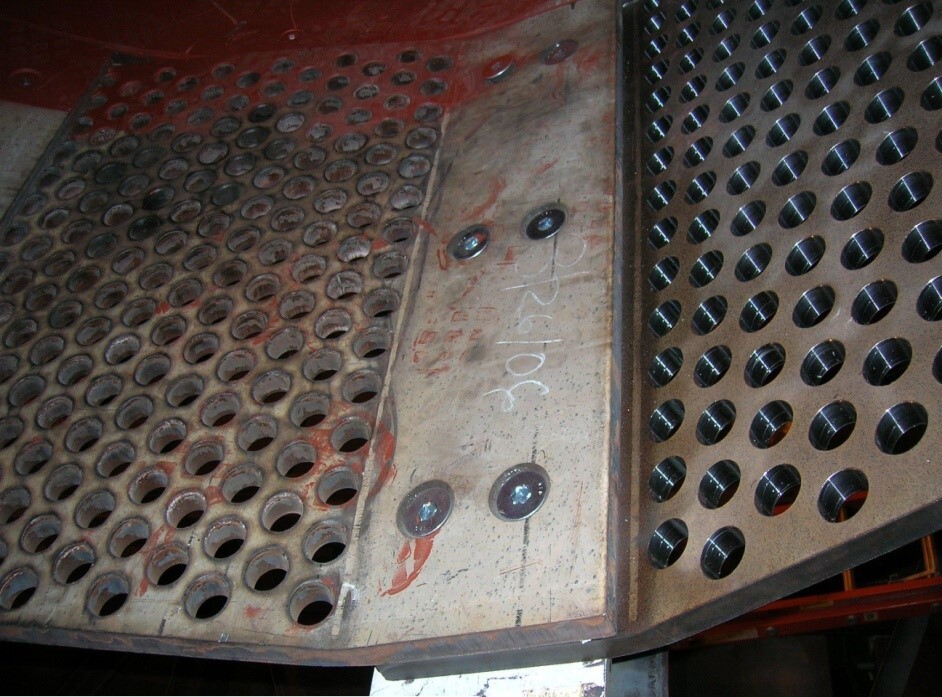
Rotary Breakers can accept feed lumps as large as 30” (762 mm) and discharge product sizes ranging from 1.5” to 6” (38 mm to 152 mm). The desired product size will determine the diameter of the holes used in the screen plates. The screen hole diameter selected is ½” larger than the desired product size. For example, if the desired product size is 2” (50 mm), the screen hole size would be 2.5” (63 mm). This is because while the Breaker is rotating, the holes appear as oval shapes to the falling material.
All about maintenance
Noted for relatively low power consumption, typical Rotary Breaker requirements can range from 50-125 hp for most ROM coal applications. Together with the low operating speeds, the simple drive arrangement allows for minimal maintenance and low operating costs.
Alignment
Coupled with a regular maintenance program, accurate alignment of the Rotary Breaker is essential to getting the most from the equipment. Precise alignment is critical to successful operation of rotary equipment. An improperly aligned cylinder can lead to the premature wear of key elements, such as the cylinder and trunnion tires, thrust rollers, bearings, cylinder sprocket, chain and other drive components. An improperly aligned Rotary Breaker may, over time, develop a wobble or vibration that could create unwelcome noise and possible damage to its structural supports.
Lubrication
Lubrication is vital to equipment operation. Many component failures are directly traceable to factors such as contaminated lubricant, improper lubricant and/or improper lubricant quantity. Such failures are often preventable through good housekeeping and proper lubrication practices.
Several fundamental steps should be followed:
- Seal all grease and oil storage containers to prevent dust, grit and moisture contamination
- Thoroughly clean all grease and oil lines before installation
- Wipe all fittings with a clean rag before lubricating to prevent forcing of contaminants into the component
- Establish a regular lubrication schedule and follow it faithfully
- Visually inspect all lubrication points to ensure proper lubrication
Some commonly lubricated components on a Rotary Breaker include:
- Trunnion roller bearings
- Thrust roller bearings
- Checking the oil level in the chain case
Centrally banked lubrication lines can be fed through an automatic lubrication system to keep a positive grease flow to all bearings.
Scalping the feed stream and sizing the coal product in a single operation, Rotary Breakers are ideal for processing ROM coal containing considerable amounts of refuse. With a straightforward, durable and maintenance-friendly design, Rotary Breakers have been a substantially economical element in the coal mining industry.
Many factors are involved in the selection of a Rotary Breaker, and the correct choice is dependent on accurate application details. To achieve optimum results, a Rotary Breaker manufacturer should be consulted to review all details and provide a professional recommendation.