Fine Material Screw Washers are used to wash, classify and dewater minus 3/8” (10 mm) sand or fine material in one machine. They are well-known, industry-preferred and field-proven over many decades for producing a clean, in-spec product suitable for conveying and stockpiling.
What Is a Fine Material Screw Washer?
Also called spiral classifiers, sand screws, screw washers or just plain “screws”, Fine Material Screw Washers are primarily used to remove excessive fines such as dust, clays or silts that are nominally minus 200 mesh (75 µm) with water. They are widely used in North American wet aggregate processing plants to wash construction and industrial sands (both naturally occurring and manufactured sands).
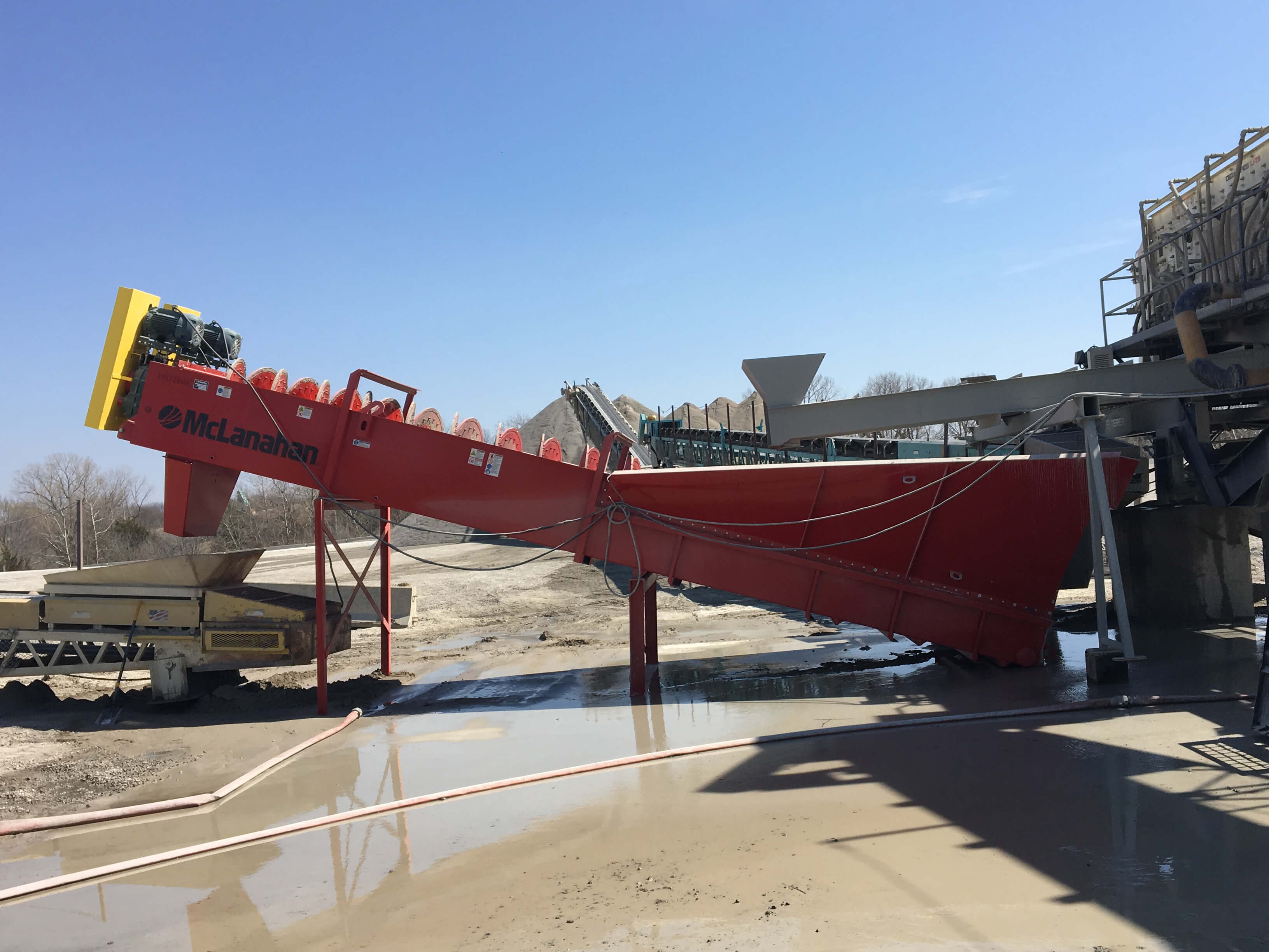
Fine Material Screw Washers can accept a dry feed from a belt conveyor or a wet slurry of material and water from a wet wash Vibrating Screen, Sand Classifying Tank, Hydrosizer®, Hydrocyclone/Separator™ or other piece of wet processing equipment. They can also accept feed directly from another Fine Material Screw.
They feature a rotating screw shaft (or shafts in double screw or twin configurations) housed inside a metal box (or tub) with flared-out sides at one end that is filled with water. This is the pool area or feed end of the machine where the washing and classification takes place.
The feed enters the pool area in front of a baffle plate, which helps to minimize turbulence that can hinder classification. Heavier, product-sized particles in the feed settle to the bottom of the washer box, while the smallest fractions float out over weirs on the sides and back of the machine.
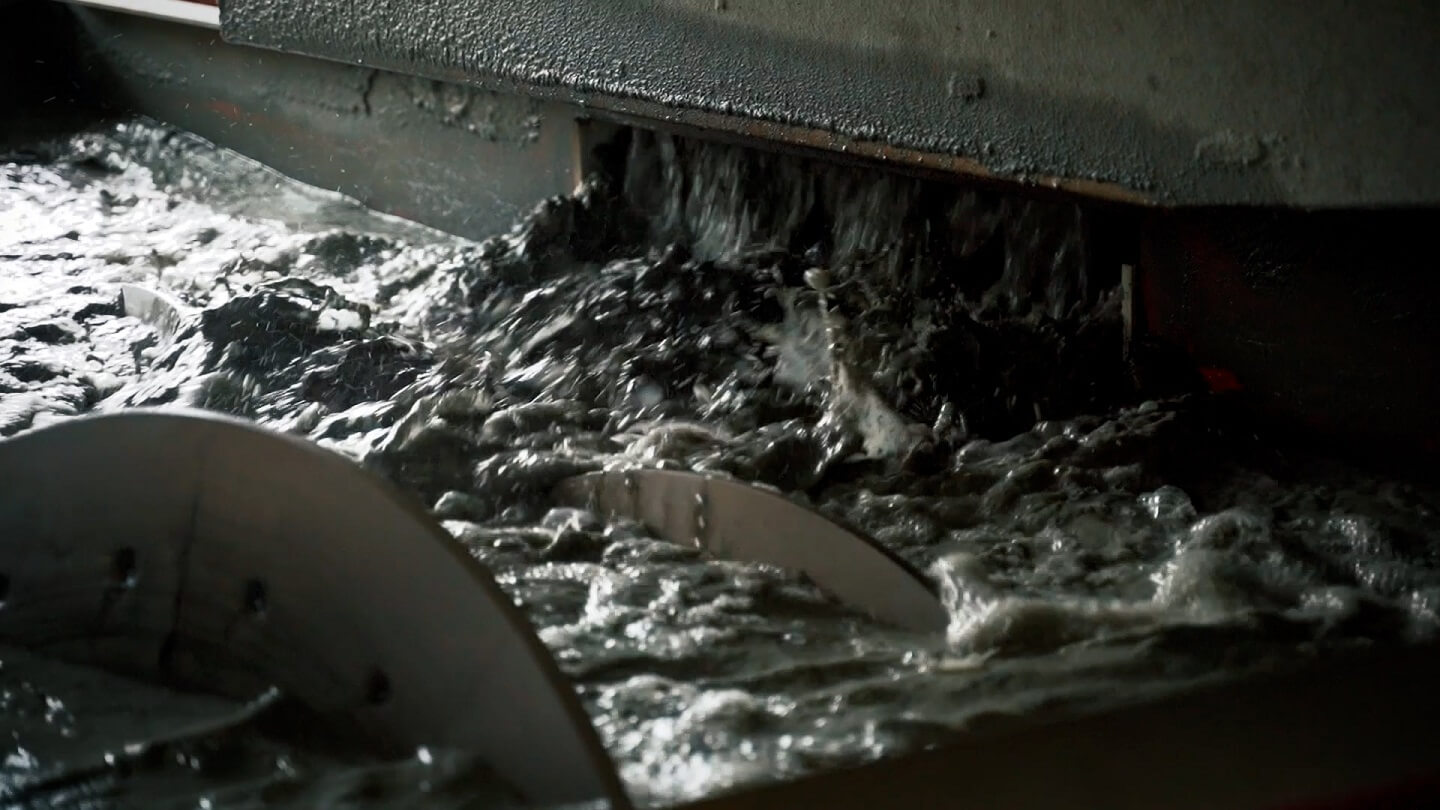
The heavier, product-sized particles that settle to the bottom of the washer box are conveyed out of the pool area by the rotation of the screw flights.
Sand screws are installed on an 18-degree incline, which allows excess water to drain from the material as it is being conveyed by the rotating screw shaft toward the discharge end of the machine. The material is discharged at around 20% moisture content, which is suitable to be conveyed and stockpiled for further water drainage before sale. Moisture content is dependent on the washed particle size gradation of the solids discharging from the machine.

History of the Fine Material Screw Washer
Fine Material Screw Washer designs are based on the Archimedes Screw, which was a device used for pumping water. It was allegedly invented by (and so named after) the famous mathematician who lived from 287-212 BC. These spiral screw shafts were driven by a hand crank to elevate water to a higher area.
Their simplicity and ruggedness eventually led to their use for dewatering ore and sand contained in a dilute mixture of water and solids. The designs evolved further in the 1930s-1950s and were manufactured to dewater fines in milling circuits that would discharge from wet processes including Ball Mills, Rod Mills and other autogenous grinding.
Since then, screw washers have also been used for dewatering and processing ores including phosphate, iron ore, solar evaporated salt and other minerals. They became commonly used for washing sand when concrete pavements using cement, rock and sand were developed for the growing infrastructure requirements for buildings and highways. Bituminous asphalt pavement also came into play in the early to mid-20th century, also requiring clean, washed rock and sand to provide sound, competent materials required for the pavement designs that evolved from the depression era of the 1930s.
Before McLanahan began developing its line of Fine Material Screw Washers in the mid-1950s, the company looked at older designs and the styles produced by their competitors. McLanahan noted producers’ and operators’ desire for improved product-sized fine solids retention and less maintenance and created its designs to meet these needs.
McLanahan Fine Material Screw Washers feature a larger pool area for more water volume capacity resulting in better product-sized fine solids retention. They also feature a longer dry deck area for lower product moisture content upon discharge.
On the maintenance side, McLanahan Fine Material Screw Washers feature a 2.5” gap between the screw flights and the dewatering plate in the dry deck area (more than double the size of competing units). This allows a bed of material to form on the bottom that protects the box from abrasive wear and thus reduces or eliminates the need for patching or replacement.
Another feature unique to McLanahan Fine Material Screw Washers is the Twin Seal Pak submerged lower bearing assembly. McLanahan’s lower bearing provides several of years of maintenance-free service (with proper lubrication) in comparison to typical seal replacement requirements in competing units.
Best Add-ons for a Fine Material Screw Washer
Fine Material Screw Washers work well as a standalone solution for washing, classifying and dewatering sand and other fine material, but their operation can be enhanced with various add-on equipment, such as a Dewatering Screen or a Scavenger System consisting of a Hydrocyclone/Separator™.
Dewatering Screen
Dewatering Screens remove excess moisture from partially dewatered material. Material is fed onto an inclined screen deck to achieve rapid drainage. Two counter-rotating vibratory motors throw the material upward and forward. As the material moves along the screen deck toward the discharge, water detaches from the particles and drains through the screen media.
Installed after a Fine Material Screw Washer, Dewatering Screens have discharged solids at as low as 7% moisture in some applications. The lower moisture content provides several benefits. First, the drier solids are able to be sold more quickly. Second, it improves housekeeping, as drier material minimizes spillage under conveyors and water seepage around stockpiles. Finally, it reduces load on hauling vehicles, as they can carry more solids and less water.
Dewatering Screens placed after Fine Material Screw Washers can also improve Sand Equivalency of the final product. As the water drains through the screen media, it carries with it some of the finer particles to discharge a cleaner product.
Scavenger System
Scavenger Systems can be installed with Fine Material Screw Washers to recover fine product-sized solids that would typically be lost to ponds. With a Scavenger System, the screw overflow is directed to a sump, where it is then pumped up to a Separator™ installed over the dry deck area near the discharge end of the screw. The Separator™ recovers the fine product-sized solids from the screw overflow and puts them back into the screw product.
Taking a sample of your screw washer overflow can help you to determine if you are losing good sand to your pond as well as if a Scavenger System makes sense for your operation. Recovering fine solids with a Scavenger System is only beneficial if adding the material to your pile doesn’t throw your product out of spec.
However, if you can recover even some fine material and still have your product meet specifications, a Scavenger System can pay for itself in a short time. Consider an application that recovers an extra 16 tph of fine material with a Scavenger System and sells their product at $5 a ton. In just one 2000-hour year, that’s an extra $160k in their pocket.
Key Features of a Fine Material Screw Washer
The key components that make up a Fine Material Screw Washer include:
Adjustable Weirs
The weirs lining the sides and the back of the washer box are adjustable to compensate for out-of-level conditions. For optimum fines retention, these weirs should be set level, but they can be raised or lowered to control the amount of fine solids that overflow into the waste stream. Raising the weirs will retain more fines for a finer cut, while lowering them will remove more fines for a coarser cut.
Flights and Wear Shoes
The spirals on a Fine Material Screw Washer shaft are also known as the flights. These are what move the material toward the discharge end as the shaft rotates. The flights are protected by replaceable wear shoes. The wear shoes bolt onto the flights and can be replaced much more quickly and easily than repairing a worn flight.
Baffle Plate
The baffle plate separates the turbulence of the feed material entering the Fine Material Screw Washer from disturbing the calm pool area. A calm pool area is key to efficient classification, allowing the product sized solids to settle out and any fines to overflow with the waste.
Rising Current
Rising current injection points are installed in the pool area to assist with classification. It introduces an upward current of water to separate the fines from the product.
Fine Material Screw Washer Price
Fine Material Screw Washers are relatively inexpensive compared to other similar classifying and dewatering technologies, such as Hydrocyclone and Dewatering Screen plants. However, the price of a sand screw can vary based on the size of the machine, material of construction on wear components, and special features or upgrades that are added.
Fine Material Screw Washer Maintenance
Fine Material Screw Washer maintenance begins with daily inspections. Establishing a preventative maintenance schedule is key to obtaining peak operating efficiency from a screw washer.
Before performing any maintenance, repairs or adjustments, de-energize the screw washer, lockout/tagout all controls and secure all components to prevent unexpected movement.
A sample Fine Material Screw Washer maintenance schedule may look like this:
8-10 Working Hours (or Once Per Shift)
- Lubricate all applicable components.
- Make sure that if equipment has banked fittings that all components receive adequate lubrication.
- Inspect reducers for excessive heat.
- Inspect all bearings for excessive heat. No bearing should be overly hot to the touch.
- Inspect motors for excessive heat.
- Inspect all electrical cables and connections for damage.
- Inspect all water lines and connections for damage.
- Inspect all belts for proper tension and alignment.
140 Working Hours (or Once Per Week)
- Inspect all bearing housing bolts for tightness.
- Inspect all motor bolts for tightness.
- Inspect area around motor cooling fins and fan for cleanliness.
- Inspect all seals for proper performance.
1800 Working Hours (or Once Every Three Months)
- Inspect all bolts and fasteners for tightness.
- Inspect wear shoes for proper operating condition.
- Replace any wear shoe before it wears down to the same diameter as the screw flights.
Spare Parts
Keeping a stock of Fine Material spare parts on hand is recommended in case of a breakdown or to perform any repairs that must be made as a result of regularly scheduled maintenance checks.
Recommended spare parts include:
- Pillow block bearing housing
- Pillow block bearing
- Pillow block bearing adapter
- Lower bearing assembly
- Lower bearing assembly rebuild kit
- Seal installation tool
- V-Belts
- Wear shoes and fasteners
For part number information, refer to the parts list and assembly drawing located in the manual.
Fine Material Screw Washers have been around for a long time. They are a popular choice for washing, classifying and dewatering fine solids in the aggregate industry as well as the minerals industry. These reliable, robust machines discharge an in-spec product that is stackable and conveyable.
With the addition of a Dewatering Screen, the product discharge will be drip-free and available for quicker sale, and with the addition of a Scavenger System, less product-sized solids will be lost to the pond.
Sand screws work well by themselves or as part of a larger wet processing system. Despite newer technology, Fine Material Screw Washers remain a tried and true method for producing a clean product.