Introduction
Apron Feeders are a popular material handling choice for a variety of applications, including aggregates, coal and other mining ore, and scrap/recycle material, because they deliver material at a constant uniform rate. They play an important role in helping sites meet their production goals by achieving maximum throughput and optimum uptime.
An Apron Feeder feeding material to a Roll Crusher.
What is an Apron Feeder?
Apron Feeders are a mechanical type of feeder used for transferring material to a crusher or other piece of downstream equipment at a uniform rate. They are typically used to feed primary crushers, but they can be used in primary, secondary and tertiary applications as a:
- Primary feeder
- Primary crusher discharge feeder
- Stockpile feeder
- Rail unloading feeder
- Storage bin feeder
These types of feeders are ideal for handling very hard, abrasive and tough materials that are beyond the scope of other feeders. Built to withstand extreme impact loading, Apron Feeders can handle larger lumps of material, and both small and large capacities.
Apron Feeders are preferred for several reasons, including:
- Apron Feeders can handle extremely small and extremely large capacities beyond the capacity of other types of feeders.
- Apron Feeders can withstand extreme impact loading beyond the capability of other types of feeders.
- Apron Feeders provide the most accurate feed rate of all the feeders.
- Apron Feeders can meter many types of wet or dry materials, such as mineral, aggregate and recycle, in a variety of sizes and shapes.
- Apron Feeders have the longest service life with the lowest maintenance of all the types of feeders.
Although Apron Feeders can accept the direct load of material, they often receive the dumped loads via a hopper. They can operate horizontally or at an incline to save space and/or lessen the height requirements of the hopper.
The Apron Feeder is the most robust feeder in the mining industry under 24/7 operation, with years between maintenance periods.
An Apron Feeder and Triple Roll Crusher.
History of the Apron Feeder
Apron Feeders had been operating in the aggregate industry for a while when National Iron Company designed and developed its Apron Feeder in 1954.
Using parts directly interchangeable with the world’s leading crawler tractor, the National Iron Company Apron Feeder was developed for the mining industry to provide continuous 24/7 operation. Here, it earned its reputation for long service life and durability.
In 1983, National Iron Company moved the Apron Feeder product line to its sister company, Universal Engineering, which sold and manufactured these Apron Feeders from its Cedar Rapids, Iowa site.
When McLanahan acquired Universal Engineering Corp in 2012, the company added Universal’s established product line to its portfolio, including the rugged and robust National Iron Company Apron Feeders.
Today, this style of Apron Feeder is used in a wide variety of applications. Although they are a popular feeder choice for many industries, Apron Feeders remain a workhorse in the mining industry because of their durable design. Hundreds of Apron Feeders still operating across the globe attest to this reliability.
Apron Feeder Components
Apron Feeders consist of cast manganese pans bolted to a dozer-style chain that wraps around a head shaft and tail idler. The chain and pan assembly rides on dozer-style carry rollers, and the movement of the flights provides a metered flow of material.
The components that make up Apron Feeders include:
- Head shaft assembly - The head shaft assembly consists of chain drive sprockets bolted to a hub mounted to a head shaft. This assembly rotates to move the chain and flights forward.
- Tail idler takeup assembly - The tail idler takeup assembly returns the chain and flights to the working surface of the feeder.
- Chain - The chain wraps around the head shaft and tail idler and rides on carry rollers to provide movement.
- Carry rollers - Carry rollers provide load carrying to the working side of the feeder.
- Return rollers - Return rollers support the chain/flight assembly on the return side.
- Flights - Cast manganese steel flights or formed steel flights provide a corrugated surface to grip the material being conveyed.
- Drive sprockets - Drive sprockets intermesh the chain, moving it and the flights.
- Impact rail - Impact rails are installed under the flights in the loading and strike-off area to prevent permanent deflection of the flights.
- Main frame - The main frame provides a base for the operating components.
- Drive - Electro-mechanical and hydraulic drives are typically the two options for controlling Apron Feeders.
- Pull cords/motion switch - Emergency stop pull cords and a zero-speed sensing switch stop the flow of material immediately.
- Drag scraper (optional) - Drag scrapers capture fine wet material that may filter between the flights.
- Dribble belt (optional) - Optional dribble belts capture fine dry material that may filter between the flights.
- Auto-lubrication (optional) - Auto-lubrication equipment delivers controlled amounts of a lubricant to the head shaft. The head shaft is typically the only component that requires lubrication on a McLanahan Apron Feeder — the rest of the components are sealed for life. However, if an Apron Feeder is designed with a tail shaft instead of sealed-for-life tail idler wheels, the tail shaft will also need to be lubricated.
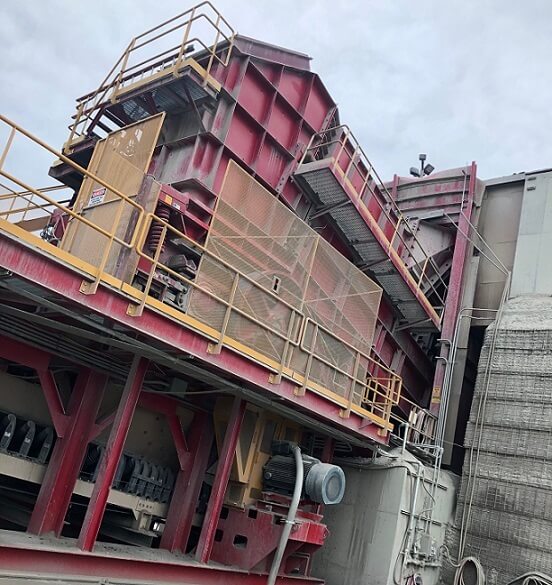
An Apron Feeder and Roll Crusher.
Apron Feeder vs. Belt Feeder
Apron Feeders and Belt Feeders, though both used for bulk material handling, differ in design and applications.
Most Belt Feeders feature a flat belt that moves on idles and is driven at the head pulley. They are typically used for material no larger than 6” and are not suited for impact, larger material and heavy loads as well as Apron Feeders. Belt Feeders require more maintenance as well.
Belt Feeders can carry material longer distances than Apron Feeders. They also operate at faster speeds than Apron Feeders because high speeds can cause accelerated wear on Apron Feeders.
Apron Feeder Price
In general, Apron Feeders are higher in capital investment than other feeders but high on investment returns.
The overall cost of an Apron Feeder can vary based on the size of the feeder. Larger feeders are most likely going to be more expensive than smaller feeders; however, Apron Feeders need to be sized appropriately for an application to achieve the highest ROI. Size a feeder too small to save on CAPEX and it won’t be able to handle the feed, nor will it give you your desired throughput. Size a feeder too large and it may take longer to see a return on investment.
Optional features such as auto-lubrication systems, drag scrapers and dribble belts will also factor into the cost. Consideration should be taken as to whether the long-term maintenance benefits justify the upfront cost.
Apron Feeder Size Calculation
Selecting the right size Apron Feeder for an application depends on several factors, including the material description, application requirements and general site information.
Material characteristics include:
- Type of material
- Bulk density - the bulk density of the material determines the speed and power necessary to meet the required tonnage per hour.
- Material size in three dimensions (height, width and depth)
- Material temperature
- Moisture content
- Maximum feed size
- Material characteristics (Is the material free-flowing? Sticky? Non-abrasive, mildly abrasive or very abrasive?)
Application requirements include:
- Capacity desired (in tons per hour)
- Desired feeder width (if known) - this is determined by the maximum feed size, typically two times larger than the max size. Sizing an Apron Feeder width two times larger than the max feed size helps to prevent bridging of the material, which is what can happen when two larger size lumps in the feed become wedged in such a way that no other material can move around them.
- Desired feeder length (if known) - the optimal length achieves the required duty in the shortest length possible. Factors to be considered include sheer length, bed depth, and hopper flexibility and positioning. The correct Apron Feeder length reduces CAPEX, operating power requirements and OPEX.
- Angle of operation (in degrees)
- Method of loading (Will the feeder be loaded by a truck, end-loader or other?)
- What the feeder will discharge into (crusher, scalper, conveyor, other feeder, etc.)
- Feed rate
- Space available
Other general information that is helpful to know when sizing an Apron Feeder includes:
- Preferred drive type (Fixed speed or variable speed? Hydraulic power or electric motor?) - Electro-mechanical drives are less costly and limited in speed range and starts/stops per hour. Hydraulic drives are more costly, with infinite speed range and infinite starts/stops per hour.
- Site elevation and temperature
- Electrical characteristics at site
It’s important to work with a knowledgeable OEM who knows the size calculation for an Apron Feeder. Apron Feeders are tailored to fit many applications and installation requirements. Whether you need to process large or small capacities of coal, mining ore, recycling or any other type of quarrying material, Apron Feeders can deliver precision material handling at a uniform and controlled rate.