Introduction
In almost all cases, mined rock needs to be crushed and sized before it becomes commercially viable. Aggregates need to be crushed and sized before they can be used to build roads, bridges and buildings, and mineral ore needs to be crushed and sized before it can be refined to concentrate the materials.
Crushing is the process of reducing large lumps of material into smaller sizes suitable for further handling downstream. It typically involves one or more stages, including:
- Primary crushing
- Secondary crushing
- Tertiary crushing
- Quaternary crushing
Primary Crushing
Primary crushing is the first stage in the crushing process. In this stage, raw or run-of-mine material that has been blasted, mined or otherwise extracted from the ground is crushed to a size that can be easily transported by a conveyor belt and handled by downstream processing equipment.
Primary crushers can handle large feed lump sizes and typically include Jaw Crushers and Gyratory Crushers, but Impact Crushers may also be used as primary crushers if the material is easily crushed and not abrasive.
After the primary crushing stage, further stages of crushing may be required to better control the size of the output and/or refine the shape of the product. This is where downstream crushing with secondary, tertiary and quaternary stages comes in.
Secondary Crushing
Secondary crushing (or intermediate crushing) accepts the material from the primary crushing stage and reduces it even further, whether for final product sizing or in preparation for final product sizing in the tertiary or quaternary stages.
Tertiary and Quaternary Crushing
The tertiary and quaternary crushing stages are used for the final sizing of products. Since quality requirements for final products can be stringent, it is important to include a properly designed and engineered crusher system for the job.
Types of Secondary Crushers
Secondary crushers typically include (but are not limited to) Cone Crushers, Horizontal Shaft Impactors, Hammermills and Roll Crushers. Occasionally, a Jaw Crusher may be applied as a secondary crusher.
Cone Crushers
Cone Crushers are compression-type crushers, which reduce material as it advances downward through the chamber (with the help of gravity and the weight above) by means of squeezing the material between a moving piece of steel (mantle) and a stationary piece (liner). Eccentric rotation causes the main-shaft and the head to wobble.
Rock is fed into the open top and gravity pulls it through the tapered crushing chamber. As the chamber gets tighter, the material gets smaller until it is small enough to pass through the cavity at the bottom of the crusher.
The gradation is controlled by adjusting the distance between the stationary concave and the moving mantle at their closest points. However, adjusting the closed-side setting tighter reduces the throughput capacity of the machine.
Cone Crushers are are well suited for hard to medium hard materials. They perform well in abrasive material with relatively low operating costs. In secondary applications, they typically provide a reduction ratio of 6:1, through 8:1 reduction ratios can be achieved with coarser applications.
Horizontal Shaft Impactors
Horizontal Shaft Impact Crushers feature a horizontal spinning rotor equipped with hammers. As the material enters the crushing chamber, it is fractured at its weakest point upon its initial impact with the hammers on the spinning rotors.
The fractured pieces are then flung toward the breaker plates inside the chamber, where they are fractured again perpendicular to the first break. Additional breakage occurs from the inter-particle collisions with the other material in the chamber.
Gradation changes are made by either changing speed of the rotating rotor and the gap setting between the adjustable curtains and the rotor. Faster speed results in finer output, while adjusting the curtains also affects the overall reduction.
These impact-type crushers offer reduction ratios of 8:1 to 10:1 in secondary crushing applications. They are ideal for soft to medium hard, slightly abrasive materials.
Hammermills
Hammermills feature swinging hammers attached to a spinning rotor. Similar to Horizontal Shaft Impactors, the material shatters upon its impact with the swinging hammers.
The shattered particles break against the breaker plates lining the crushing chamber and are carried across a grate surface, where they are ground down into smaller sizes. Openings in the grating allow the release of appropriately sized material to ensure controlled product sizing.
These crushers offer reduction ratios as high as 20:1. They are adept at handling less abrasive materials in aggregate and industrial applications.
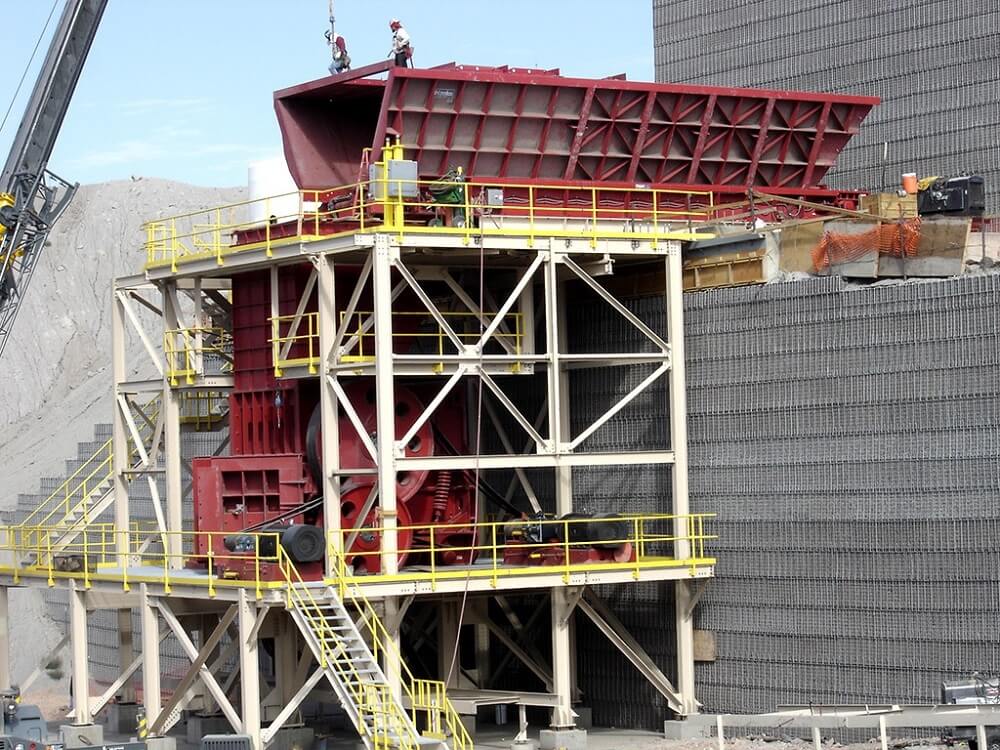
Roll Crushers
Roll Crushers can be used in the primary, secondary, tertiary or quaternary crushing stages. They are compression machines and work by crushing rock between a single or pair of rotating rolls equipped with teeth.
Depending on the configuration (single roll, double roll, triple roll or quad roll), the material is crushed between the roll bodies and teeth on the two rolls or, in the case of single roll and the top stage of the Triple Roll Crushers, between the roll and the crushing plate.
Depending on the design, Roll Crushers have a reduction ratio of 6:1 (single roll and the top stage of the Triple Roll) and 4:1 (double rolls). They are great for handling soft to medium hard, slightly abrasive material that can be dry or wet and sticky.
Types of Tertiary and Quaternary Crushers
For fine sizing, tertiary or even quaternary crushing stages may follow the primary and secondary stages. Cone Crushers are the most common types of tertiary and quaternary crushers, though Vertical Shaft Impactors and Roll Crushers can also be used depending on the application.
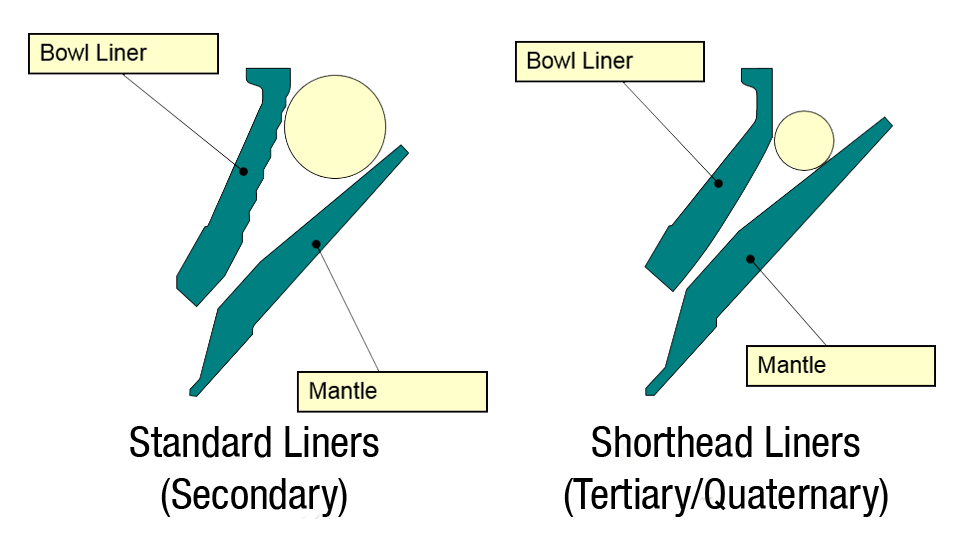
Short-Head Cone Crushers
Short-head Cone Crushers are specified for many tertiary and quaternary crushing applications. Short-head Cone Crushers work exactly like Standard Cone Crushers, but they feature a smaller crushing cavity, making them ideal for finer crushing applications.
The closed-side setting on a Short-head Cone Crusher can be adjusted tighter than a standard cone to improve final product size and shape. Short-head Cone Crushers offer reduction ratios around 4:1.
Vertical Shaft Impactors
Vertical Shaft Impact Crushers have a rotating vertical shaft with a table or rotor at the top. Rock is fed down a feed tube in the center of the machine and onto the rotor. The rotor accelerates the rock, throwing it sideways. The rock then impacts a stationary surface (metal shoes or rock shelf). The rock breaks and falls out the bottom.
These types of crushers are usually applied as tertiary or quaternary crushers with less than 2” (75 mm) feed or smaller. Some Vertical Shaft Impactors can be used as secondary crushers with larger feed.
Vertical Shaft Impactors are very application-specific. They are sensitive to abrasive materials and can experience very high maintenance and operating costs. Some of these machines are equipped with a rock shelf to reduce wear costs. The rock shelves improve the maintenance costs but sacrifice in the amount of reduction achieved.
Choosing the Right Secondary Crusher
Each of the crushing stages plays an important role in the production process, whether it be material reduction for further handling downstream or final product sizing.
Selecting the right crusher for each stage of the crushing process depends on an understanding of the material to be crushed and the site’s production goals. Jaws and gyratories will most often be found in the primary crushing stage, while cones, impactors and roll crushers are most often used in the secondary, tertiary and quaternary crushing stages.
Knowing which crushers best fit in each stage, as well as ensuring a properly sized crusher for the task, will help a site achieve optimum crushing efficiency and overall profitability.