Automated mechanical Sampling Systems offer the benefits of personnel safety, better accuracy, more repeatability and less bias due to human error in a sampling application. Some examples of Sampling Systems include:
- Cross Belt Samplers – Samplers that are installed over a conveyor belt and collect samples of the material from the moving conveyor without having to stop the belt
- Falling Stream Samplers – Samplers that collect material from a free-falling condition, such as from the discharge end of a conveyor
- Multi-Stage Sampling Systems – Systems that incorporate multiple stages of sampling and material size reduction
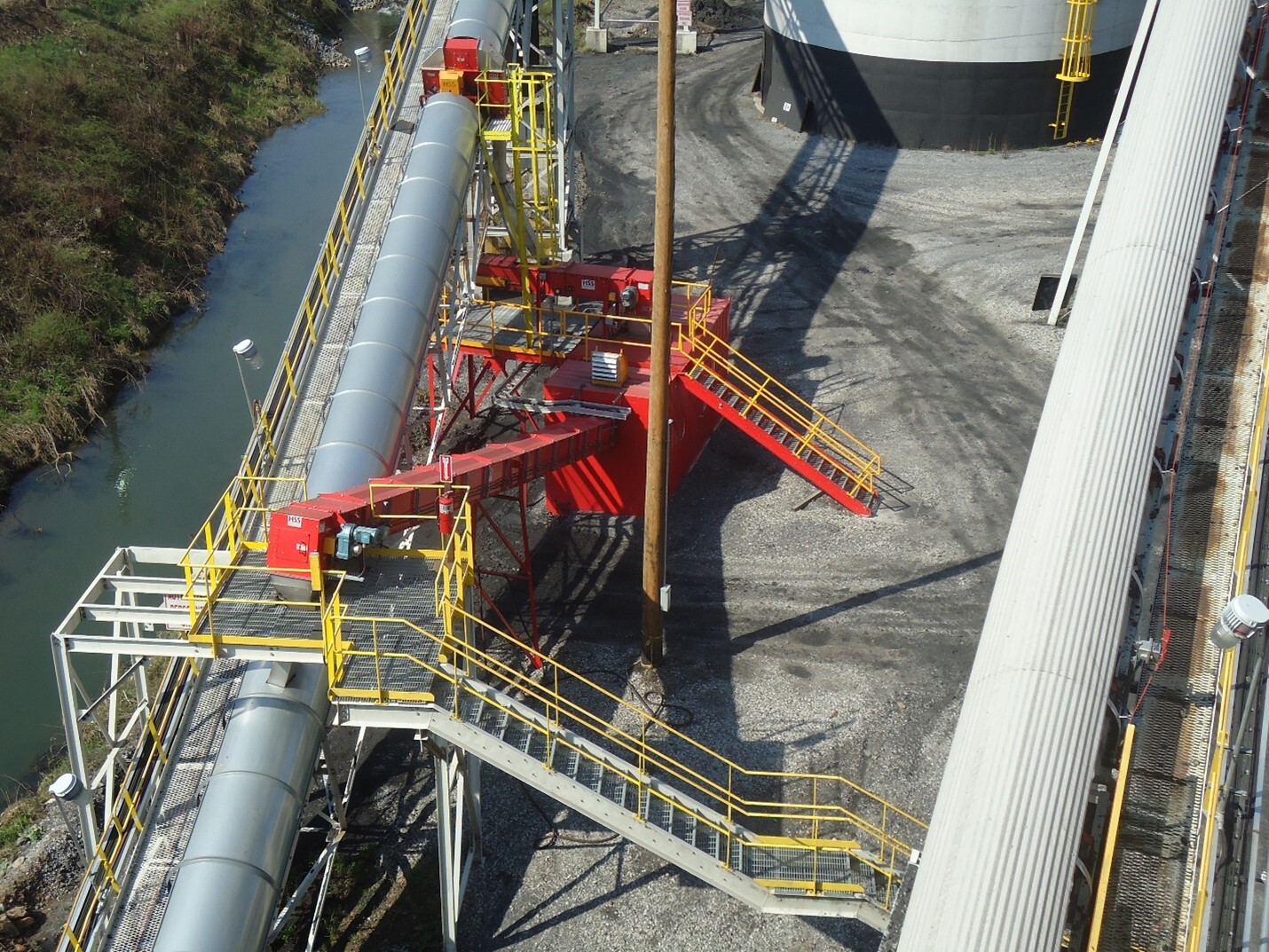
What is a Multi-Stage Sampling System?
Multi-Stage Sampling Systems are mechanical systems designed to collect and process primary samples in multiple stages to reduce downstream handling costs. These systems typically include sampling equipment, such as Cross Belt Samplers or Falling Stream Samplers , and small-scale sampling crushers , such as Sampling Hammermills, Sampling Jaw Crushers or Sampling Roll Crushers/Sizers, as well as ancillary equipment such as conveyors, dividers, mixers and collecting bins.
An example of a Multi-Stage Sampling System may look like this: a primary Sampler, such as a Cross Belt Sampler, collects a sample increment from the material flow and drops it into a Sampling Crusher , such as a Sampling Hammermill Crusher. The crusher reduces the size of the material in the sample and discharges it onto a conveyor belt, where a secondary Sampler, such as another Cross Belt Sampler collects a sample from the material stream. The sample is discharged into a collection bin, while the remaining material rejoins the main material flow.
Benefits of Multi-Stage Sampling
The biggest benefit of Multi-Stage Sampling Systems is reducing the amount of material personnel have to handle in the lab. This itself provides a host of benefits inherent to mechanical sampling as a whole, including:
- Less labor costs associated with handling/processing samples for analysis
- Less chance for human error or bias associated with manually handling the samples
- Improved safety
- Better repeatability
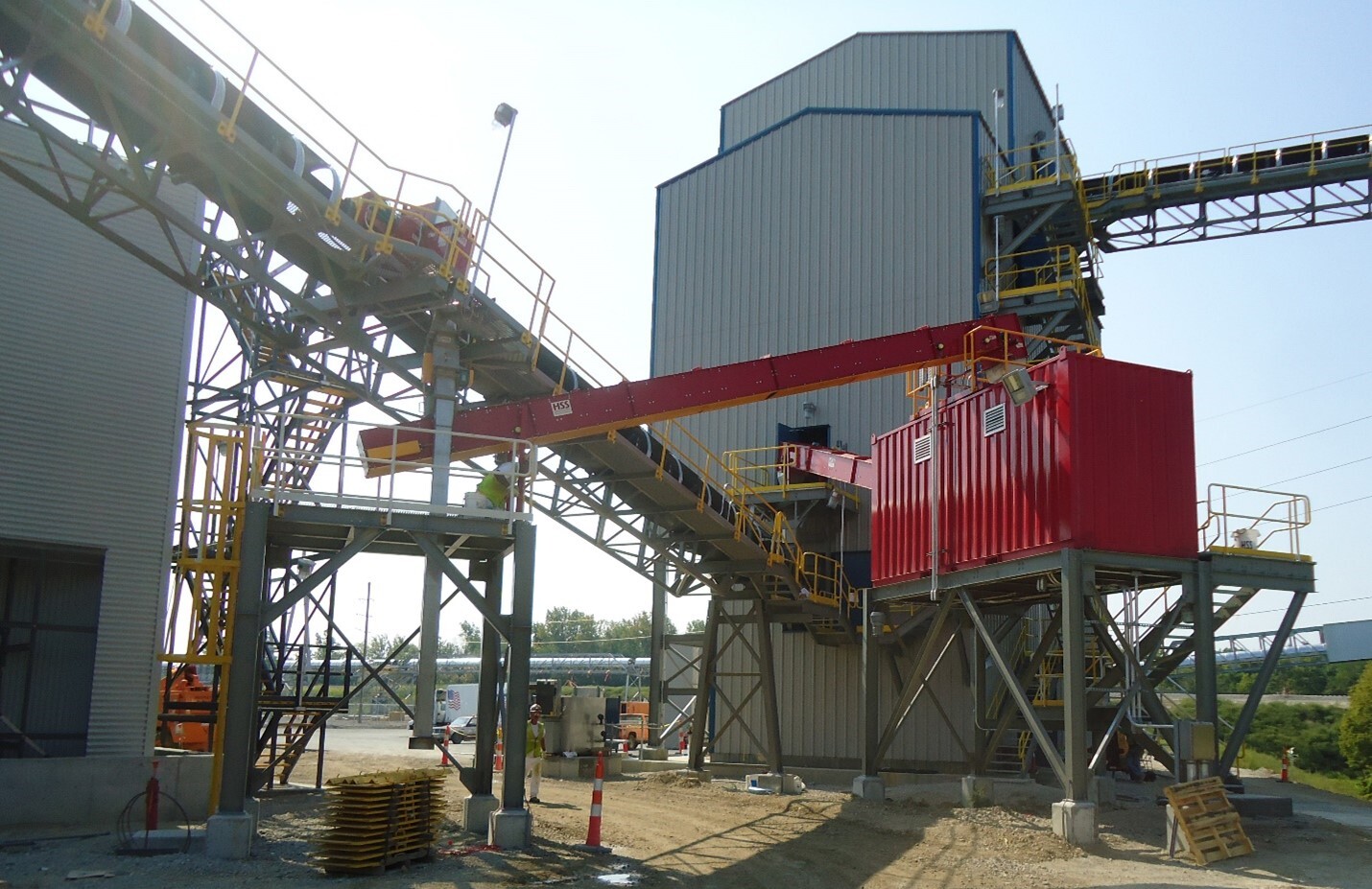
Do you need a Multi-Stage Sampling System?
Not every application will warrant a Multi-Stage Sampling System. If you’re wondering whether a Multi-Stage Sampling System is right for you, consider the following questions.
What is the flow rate of your material?
Material flow rate can indicate whether you need a Multi-Stage Sampling System. Applications with a high flow rate of material can benefit from Multi-Stage Sampling Systems because higher flow rates typically result in larger sample increments. Larger sample increments mean more material is collected that must be dealt with in the lab.
A Multi-Stage Sampling System can reduce the amount of sample material that goes to the lab. By implementing additional stages of material reduction and sampling, you can reduce the amount of processing required by lab technicians and thereby reduce labor costs.
Do you have inconsistent or nonhomogeneous material?
Material makeup can also indicate the need for a Multi-Stage Sampling System. If you have an inconsistent or nonhomogeneous material, you will need to collect more sample increments to get a sample that is representative of the feed. The more samples are collected, the more material that will have to be handled in the lab.
By automatically collecting smaller sample increments of larger sample increments taken from the main material flow, Multi-Stage Sampling Systems reduce the amount of sample material sent to the lab. This also reduces the amount of material handling required at the lab level when preparing the sample for analysis.
What is the size of your material?
Particle size is another indicator of whether a Multi-Stage Sampling System will benefit an application. Larger particle sizes typically require a Sampling System with a cutter large enough to accommodate them. Larger cutters collect larger amounts of sample. Not only does this equate to more material that lab technicians have to handle in general, but it also means that more material handling may be required to get the large particles into the size required for analysis.
With Multi-Stage Sampling Systems, much of the material handling is done mechanically before it even goes to the lab. Smaller sample increments are taken from the larger sample increments collected from the main material flow, which reduces the overall amount of material sent to the lab for processing.
Many Multi-Stage Sampling Systems also feature a crushing element that reduces larger particles in the sample increment into smaller sizes. This reduces the amount of manual crushing that has to be done in the lab to get the particles to the size required for analysis.
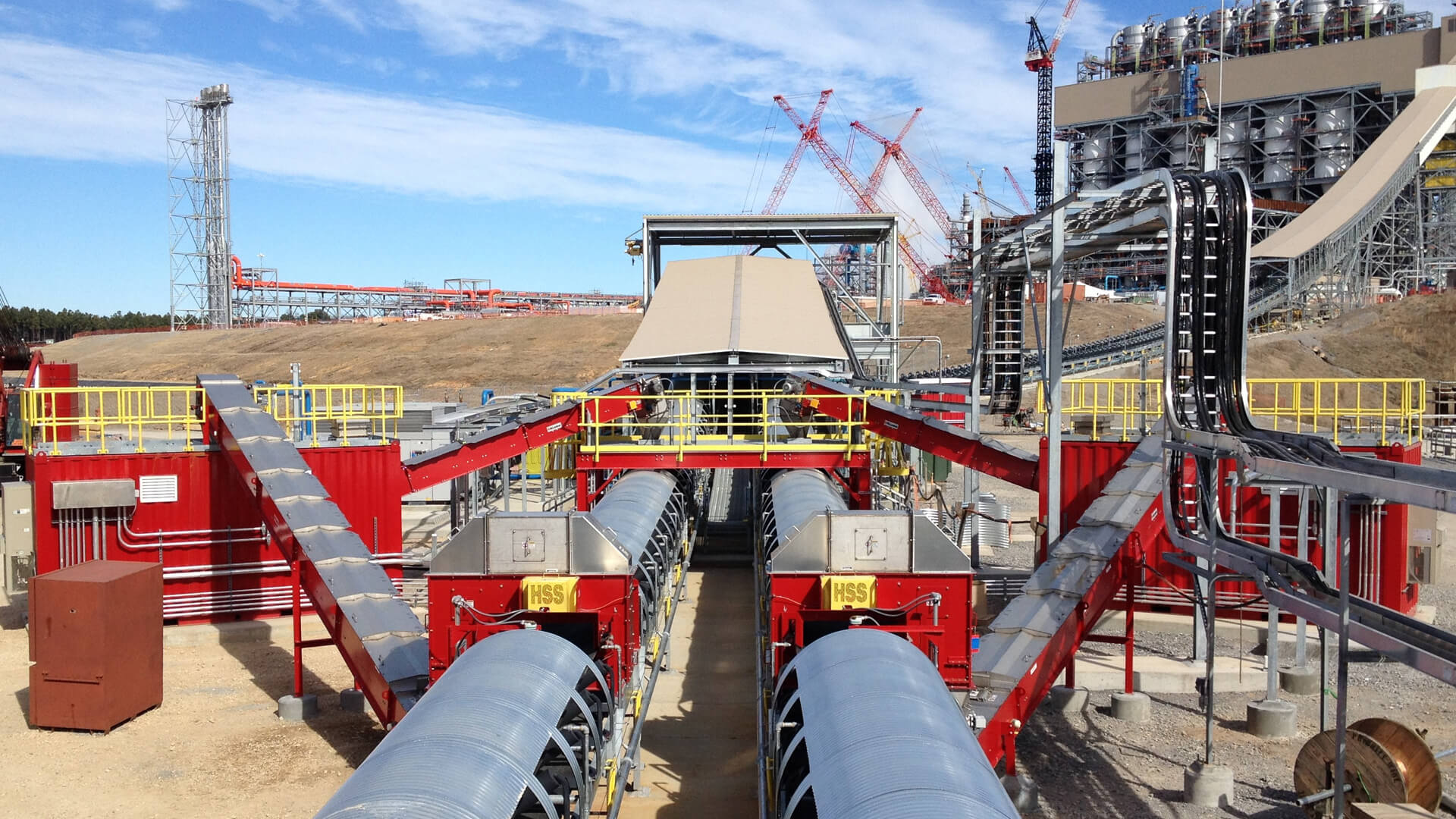
Whether you need a Multi-Stage Sampling System or not depends on the characteristics of your material, the size of the particles and the flow rate of the material. If you have a large sample size, large particle size or nonhomogeneous material, you may want to consider a Multi-Stage Sampling System to help you reduce the amount of processing required at the lab.