Introduction
The goal of any crushing plant is to produce the required material sizes at the lowest cost per ton. With small changes to their existing crushing and screening circuits, such as adjustments to the crusher speed and closed-side setting, producers can turn out a few extra tons each hour to really make the most of their operation.
When making changes to your crushing and screening circuit, keep these two things in mind:
- Do not make a lot of changes at one time. If you make too many changes at once, you won’t be able to tell what is working and what is not working.
- Document everything. You can’t manage what you don’t measure. Keeping a written or typed log of even the simplest of things will prove beneficial in the long term.
Plant optimization
Plant optimization is an ongoing process that is part of the circuit; it is not simply a task to be performed. You must have a system in place to achieve the lowest cost per ton. The system is the process of measurement and adjustment — how you look at your process, how you make your adjustments, how you measure, etc. — and it needs to be consistent.
To begin the plant optimization process, follow these three steps:
1. Assess the capabilities of the circuit
Establish the design capacity of every piece of equipment within the complete circuit by first gathering the production capacities as rated by the manufacturer. Consider the external factors that can affect the capacity of the equipment, such as the material hardness, shape, moisture content, gradation, etc. Identify the design limitations or bottlenecks that will decrease capacity.
Perform a physical assessment of each component to identify actual capabilities.
Conduct a crusher performance assessment of the following:
- Confirm that the crusher is operating at a choke level.
- Take belt cuts of the feed and discharge from each crusher.
- Record the crusher closed-side setting.
- Record the crusher power draw.
- Check the conveyor belt speeds.
- Identify the condition of the crusher liners at the time of sampling.
- Identify the percent passing the crusher closed-side setting.
- Identify the amount of recirculating load coming back to the crusher if operating in a closed circuit).
Output gradations are important, so be sure to conduct an assessment of the crusher conveyor belt cuts to determine:
- The actual crusher throughput (stph).
- The ratio of reduction (F80 divided by P80).
- The percent passing the crusher closed-side setting.
- The product shape being produced by the crusher.
Don’t neglect to perform an assessment of the screen’s performance. The screen is the cashbox of the plant. While the crusher produces a gradation, it is the screen that produces the product for the specification.
Ineffective screening of the crusher feed will have a detrimental effect on the crusher’s operation in terms of wasted horsepower, lower reduction ratio and increased wear.
To assess the screen’s performance:
- Take a belt cut of the screen feed conveyor belt.
- Take screen deck discharge belt cuts.
- Check the conveyor belts speeds (feet per minute).
- Measure the bed depth at the discharge tip of each screen deck.
- Check and record the screen speed.
- Check and record the screen stroke.
- Check and record the stroke angle.
- Make sure the snubbers are properly set and aligned.
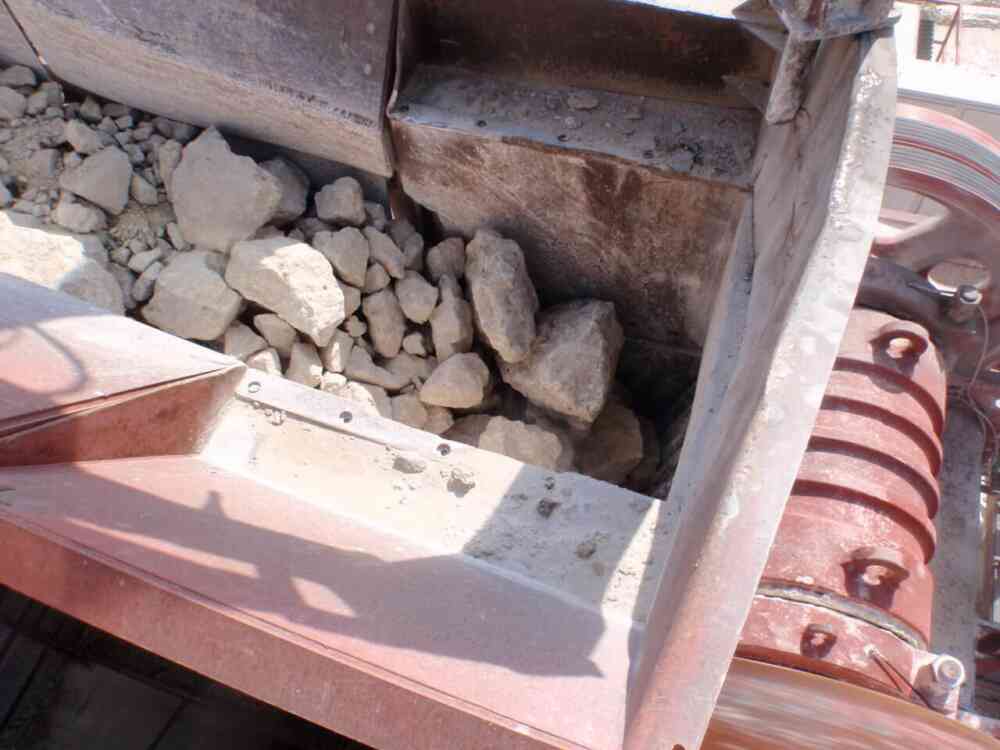
2. Forecast production needs
Once the circuit capabilities are established through the assessment process, it is necessary to set a production schedule.
Forecast your production needs by meeting with your sales team and customers to talk about trends in the marketplace — what customers are buying and what customers aren’t buying — to determine a production schedule. The production schedule will be a combination of the sales forecast and what your plant can actually produce.
Work with a complete management team to establish a realistic sales forecast, and review it regularly.

3. Maintain circuit performance
The key to maintaining the circuit’s production performance is establishing procedures to identify how each component is operating. Each piece of equipment has its own operating parameters.
Crushers
To maintain crusher performance:
- Understand the crusher design limits, i.e. volume, power, force.
- Keep a daily operator’s log sheet.
- Maintain a proper well-blended feed to the center of the crusher.
- Minimize feed segregation.
- Select the proper crusher liners.
- Change liners when you notice a 10% decrease in productivity.
- Maintain proper feed top size to the crusher.
- Adjust the crusher closed-side setting frequently.
- Maintain the proper crusher drive belt tension.
- Maintain clean crusher lubricating oil.
Screens
To maintain screen performance:
- Check and maintain proper screen media and stroke.
- Select the proper screen media.
- Inspect the media for wear or failure frequently.
- Inspect the tension of the screen media.
- Make certain that the screen is being fed correctly.
- Maintain adequate clearance around the screen body.
- Maintain proper drive belt tension.
- Lubricate the screen bearings per the manufacturer’s instruction.
- Check the spring condition.
- Check the snubber adjustment.
Conveyors
To maintain conveyor performance:
- Inspect conveyor idlers (carrying and return).
- Inspect conveyor pulleys (head, tail and gravity take-up).
- Inspect conveyor belt condition and tension.
- Inspect the belt splice.
- Check and maintain proper drive belt tension.
- Change the reducer oil per the manufacturer’s instruction.
- Lubricate the conveyor bearings per the manufacturer’s instruction.
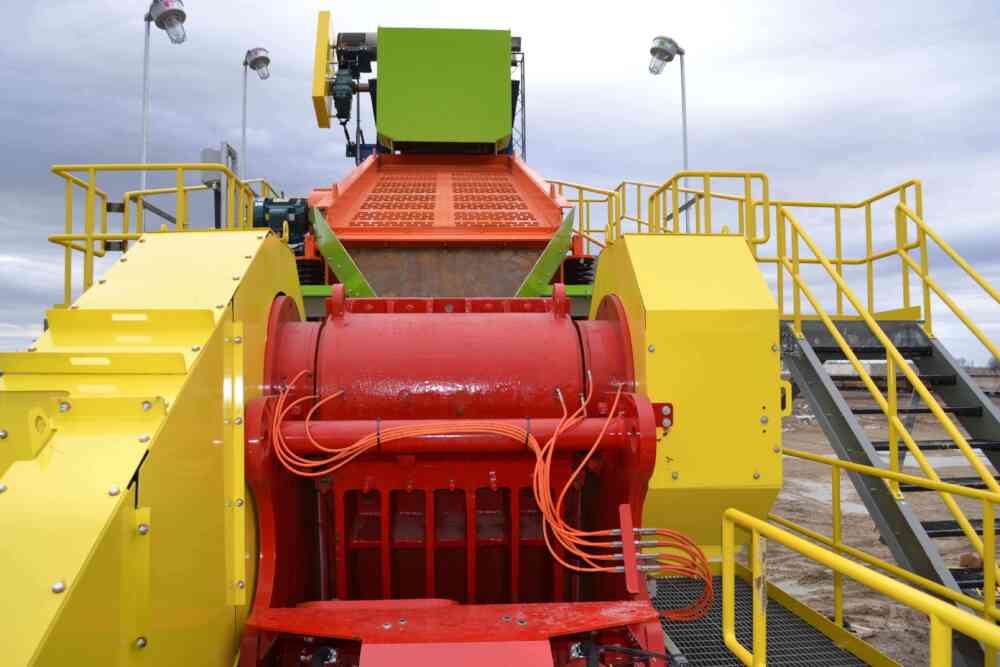
Prepare a preventative maintenance program
Scheduled maintenance is the only way to ensure that the circuit will continue to produce. Taking some time each shift, week, month, quarter, year, etc. to inspect components can prevent unexpected and often costly breakdowns.
Prepare a written preventative maintenance program (your manufacturer can provide recommendations for each piece of equipment) that includes specific dates when work will be completed and have it approved by the management team.
The most important part of a preventative maintenance program is sticking to it. Regardless of production requirements or if you think you can skip a day, preventative maintenance will ensure optimal operation of your equipment.
Maximize production levels
The most efficient way to maximize the production levels of the processing circuit is with an ongoing system. This system is simple, but it takes time.
First, you need to take time to assess the circuit in order to understand how your equipment is operating. This will help you to determine if you are producing what you want and how to adjust the circuit to make changes if you are not. It allows you to see what happens as you make changes and whether those changes have a positive effect on the plant. Documenting each step in the assessment process is key to realizing the benefits of your efforts.
Next, take time to put together a production scheduled based on forecasts in the marketplace. Knowing you need to produce so many tons of a certain product in a certain amount of time and factoring in downtime will tell you how many hours you need to operate to meet those goals. Monitor the forecast monthly or quarterly.
Finally, establish and stick to a preventative maintenance schedule to ensure optimal equipment operation.
Following these three steps leads to a much better operation. It will help you determine how to produce an extra 3 to 5 tons per hour, keep production in line with what sales is making, and make products customers want to buy today and tomorrow. This system is the only way to ensure that the circuit is producing the desired size products at the lowest cost per ton.