Frac Sand Plants
Frac Sand Plants are designed to remove silt/clay impurities, as well as size and dewater sand before drying, sizing and blending it into final products.
Applications

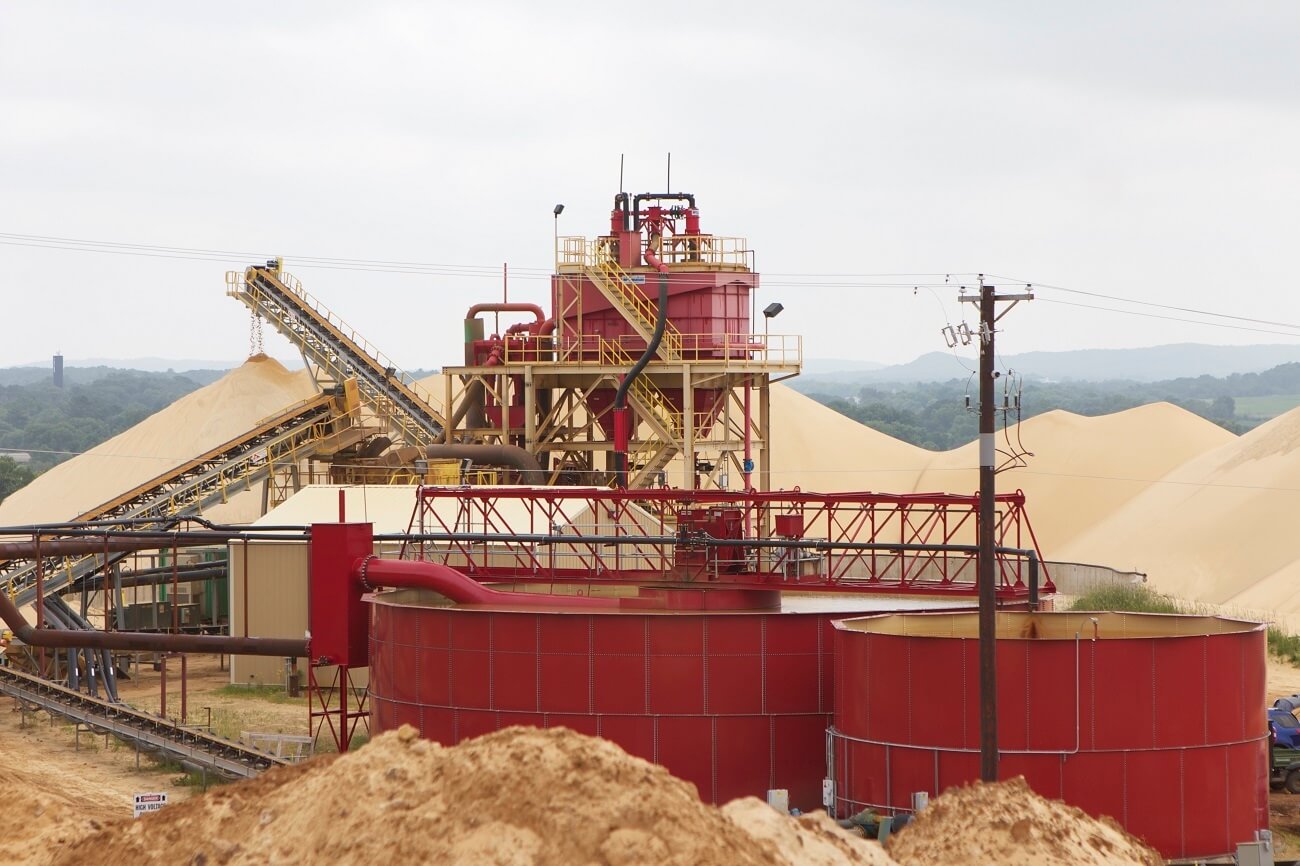
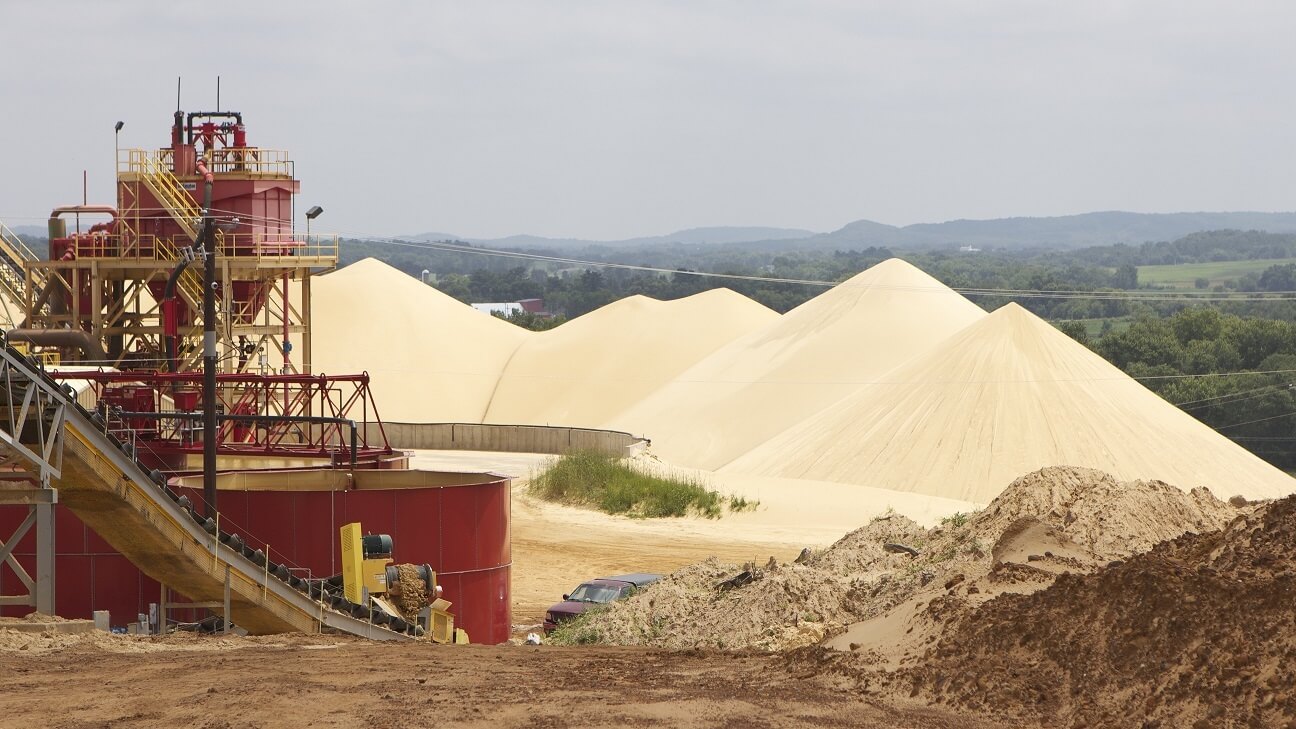
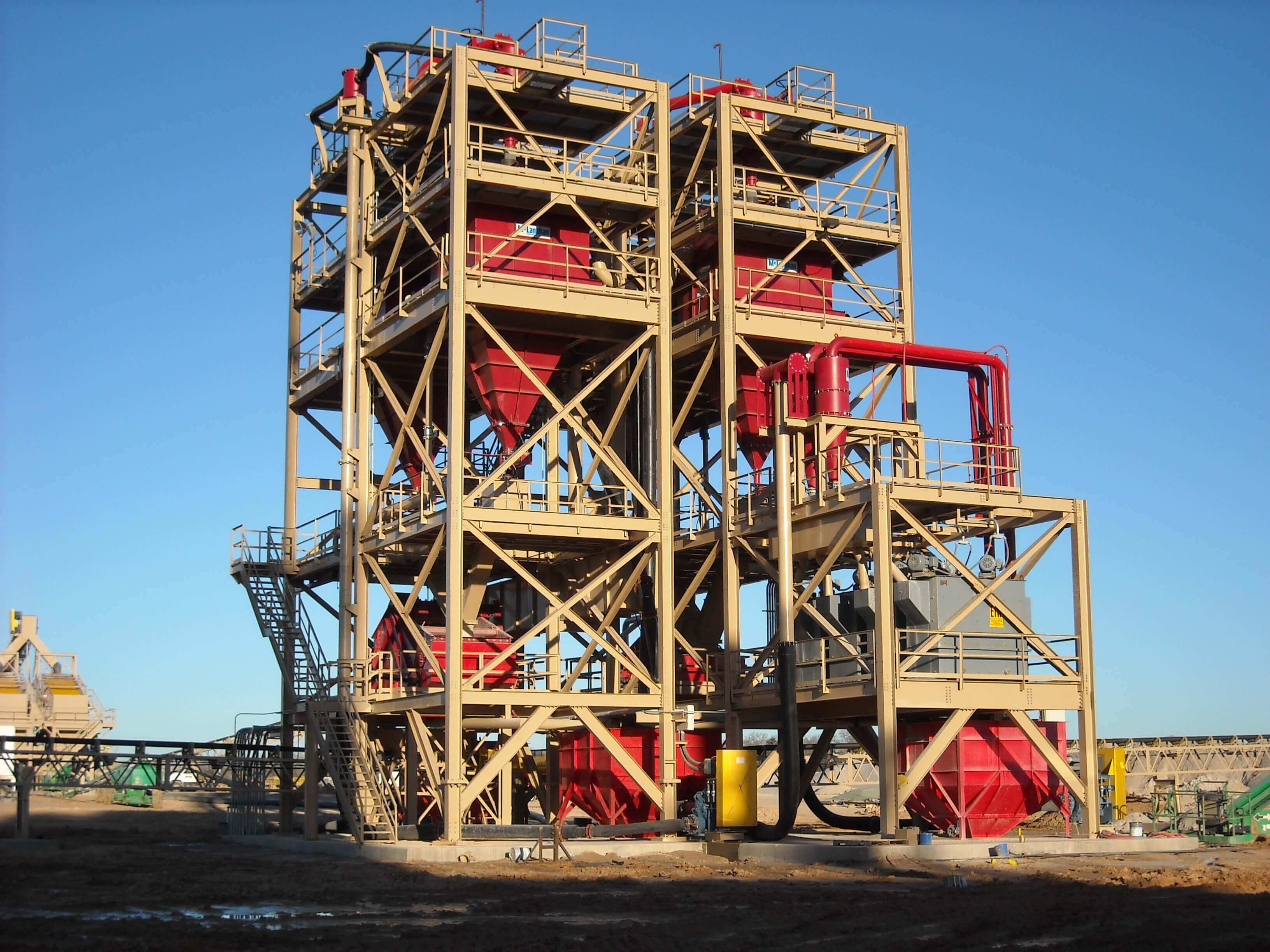
Frac Sand Plants are designed to remove silt/clay impurities, as well as size and dewater sand before drying, sizing and blending it into final products.
Applications
Jump To:
Frac Sand Plants can be engineered in many configurations, including high capacity multi-stage classification and long attritioning cycles, or the plants can be as simple as skid-based Cyclones and Dewatering Screens making a 140 mesh cut.
The final design of a plant will depend on the nature of the deposit and desired products. However, these decisions can also be influenced by downstream processing in the dry plant.
Before making the investment in a deposit or plant, it is necessary to test the deposit to see if it meets the American Petroleum Institute's (API) requirements for frac sand. The official standards can be found here.
Every sand deposit that will pass API testing still requires some form of processing to create fractions for drying and discrete sizing into the final frac sand products used in the field. The equipment is applied as appropriate in a complete system to benefit the yield from the deposit and the quality of the products being produced.
If your sand has been tested by an accredited lab and meets the API frac sand requirements, McLanahan can begin designing your plant immediately. If your sand has not yet been tested, our in-house laboratory can perform sieve analysis, as well as attrition and turbidity testing. For other API accredited test work, we can arrange for an accredited lab to perform the complete range of tests.
The various designs of plants may include the following processes featuring McLanahan designed and built equipment:
McLanahan is the leader in creating complete wet processing solutions to produce frac sands needed in the oil and gas well drilling industry. In-house process engineers take each deposit’s unique characteristics into account and work directly with customers to determine layout and equipment requirements.
A major benefit of working with McLanahan is our in-house designed and manufactured equipment, which includes Attrition Cells, Hydrosizers™, Centrifugal Pumps, Hydrocyclones and Separators™, Dewatering Screens, Fine Material Screw Washers, Thickeners and Filter Presses.
McLanahan’s process engineering team is regularly engaged by companies to audit competitor plants. Reviews like this provide insights based on our unique expertise, along with recommendations for process improvement. Often, the result of this is that any modifications and future plants are of McLanahan’s design and supply.
Frac sand is a form of proppant for the fracking process used in the oil and gas industry. The proppant’s basic function is to create and maintain the deep-underground passageways needed to harvest either natural gas or crude oil. The product can be in the form of ceramic beads, resin-coated sand and natural sand frac sand. Frac sand mining occurs in a variety of locations, and the differences in the deposits vary in gradation, clays and clay/silt content, and other physical characteristics. In order to manage these natural variations, it is necessary that a plant is designed with your site’s deposit in mind.
Requirements for frac sand can include:
McLanahan designs each of its Frac Sand Plants to meet the specific needs of each customer. Using field-proven McLanahan equipment, Frac Sand Plants can be designed for classifying, desliming, dewatering, pumping, scrubbing, sizing, tailings management and waste solids management. McLanahan Frac Sand Plants are engineered to make the critical separations required for frac sand. They produce the highest product yield at the lowest moisture.
There is not a simple answer to this question. What you need is the right plant. Our specialty is in using our in-house expertise and equipment range to create a plant that will help you meet your specification requirements and so that you have a single source contact. It may be that a multi-cut process is the answer; however, limits on available financing, permitting issues, environmental considerations and market changes will significantly influence the decisions.
Hydrosizers™ have an advantage of a smaller cross sectional area requirement per tph. This translates into a smaller footprint and fewer units required to process the same amount of throughput. The ability to make product specification changes without interrupting the process is an additional advantage, which allows more flexibility. Finally, when making a below 20 mesh cut, screens have much tighter feed condition requirements to ensure proper operation. With a screen, too much water in the feed will cause hydroplaning, while too little water will cause the bypass of material through the clumping of the material.
In general, all equipment has a range of operation, and the McLanahan team will work with site personnel to adjust the existing equipment to achieve the alternative requirements. McLanahan’s ability to provide the full solutions allows a better understanding of the process and allows for easier evaluation and modification to the application. New applications can be designed with flexibility for the product specification built into the plant.
McLanahan Frac Sand Plants are specifically engineered to meet each producer's needs based on the individual characteristics of the deposit.