Rotary Trommels
Rotary Trommel Screens utilize continuous tumbling and lifting actions to size and separate feed materials that include the municipal waste, recycling, industrial, aggregate and mining industries.
Applications
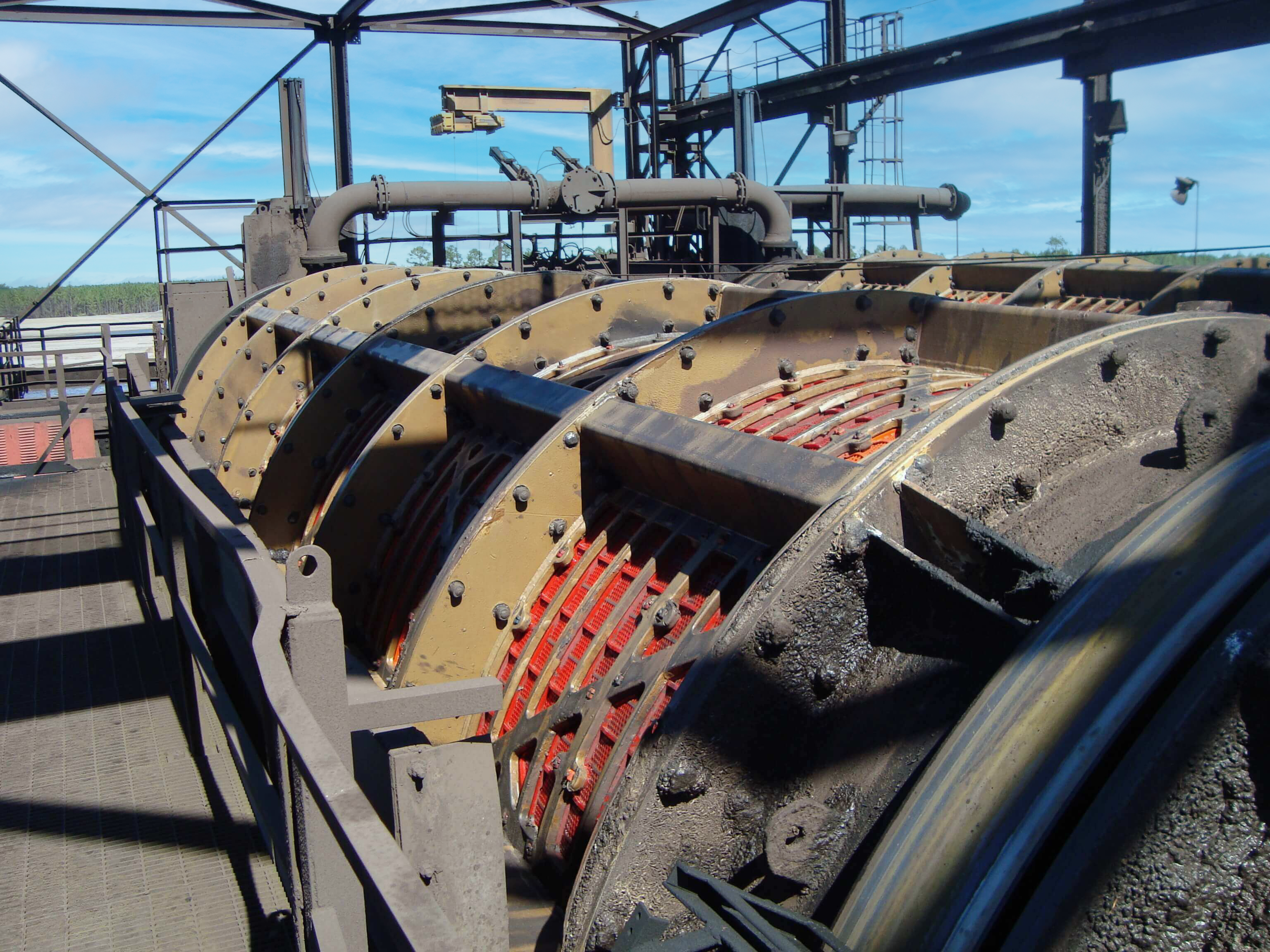
Rotary Trommel Screens utilize continuous tumbling and lifting actions to size and separate feed materials that include the municipal waste, recycling, industrial, aggregate and mining industries.
Applications
Jump To:
As the cylindrical drum of a Rotary Trommel Screen rotates, raw feed material is lifted on shelves until it nears the top of the drum. Material then falls, tumbling onto other material at the bottom of the drum. This action helps to break down softer fractions, as well as separate different types of materials. As the tumbling continues, smaller size fractions filter through holes in the screen plating, while larger material continues along the length of the cylinder to discharge at the end.
The tumbling action of the Rotary Trommel allows accurate sizing and separation that is beneficial for a variety of customers, including those looking to upgrade metallics after mass-burn solid waste incineration, to reclaim wood chips in sewage sludge composting, for accurate size separation of difficult-to-screen materials in municipal solids waste and resource recovery, and to separate and wash ores, rock and other fine materials
McLanahan manufacturing techniques guarantee that Rotary Trommel Screens are simple to operate. The design is also intended to be safer for operators. Specially designed safety features include sectionalized cylinder covers with inspection doors, an optional mast system to remove screen panels, optional inching drives, and a cylinder jacking and brake system for maintenance periods.
To serve many industries and applications, McLanahan Rotary Trommel Screens are offered with various types of screen media that have a variety of aperture sizes depending on the application requirement. For units that are larger than 10' (3m) in diameter, McLanahan performs a finite element analysis of a unit prior to manufacturing to ensure the optimal design strength.
Contact McLanahan or your nearest authorized local dealer not only for pricing but for discussions on suitability and use for your application.
You should know your feed material bulk density, the material particle size feed distribution, the tons per hour feed solids capacity, a process flow diagram showing equipment location of required unit in your processing plant, the separation or cut point(s) and the moisture content.
The type of screen media, protective safety covers and a full length spray bar are all options to consider.
Vibrating Screens, Wobbler Feeders, Vibrating Grizzly Feeders and Disc Screens can be considered.
The tumbling action of the Rotary Trommel allows accurate sizing and separation that is beneficial for a variety of customers.