Dewatering Screens
Dewatering Screens can be used to dewater -4 mesh (5 mm) particles of sand, coal, iron ore, salt, etc., as well as for limited efficiency fine sizing, washing and rinsing, desliming and organics screening.
Applications
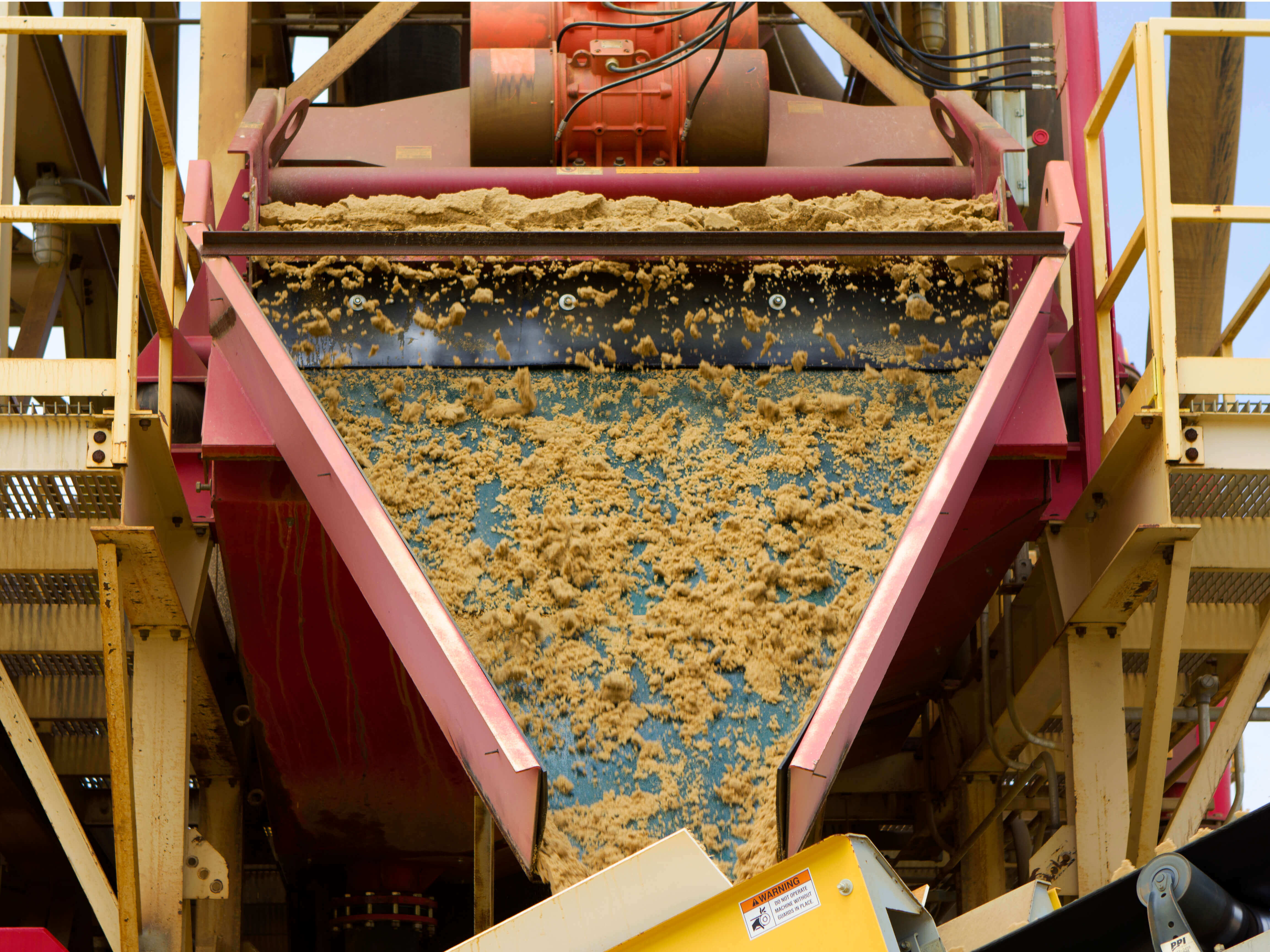
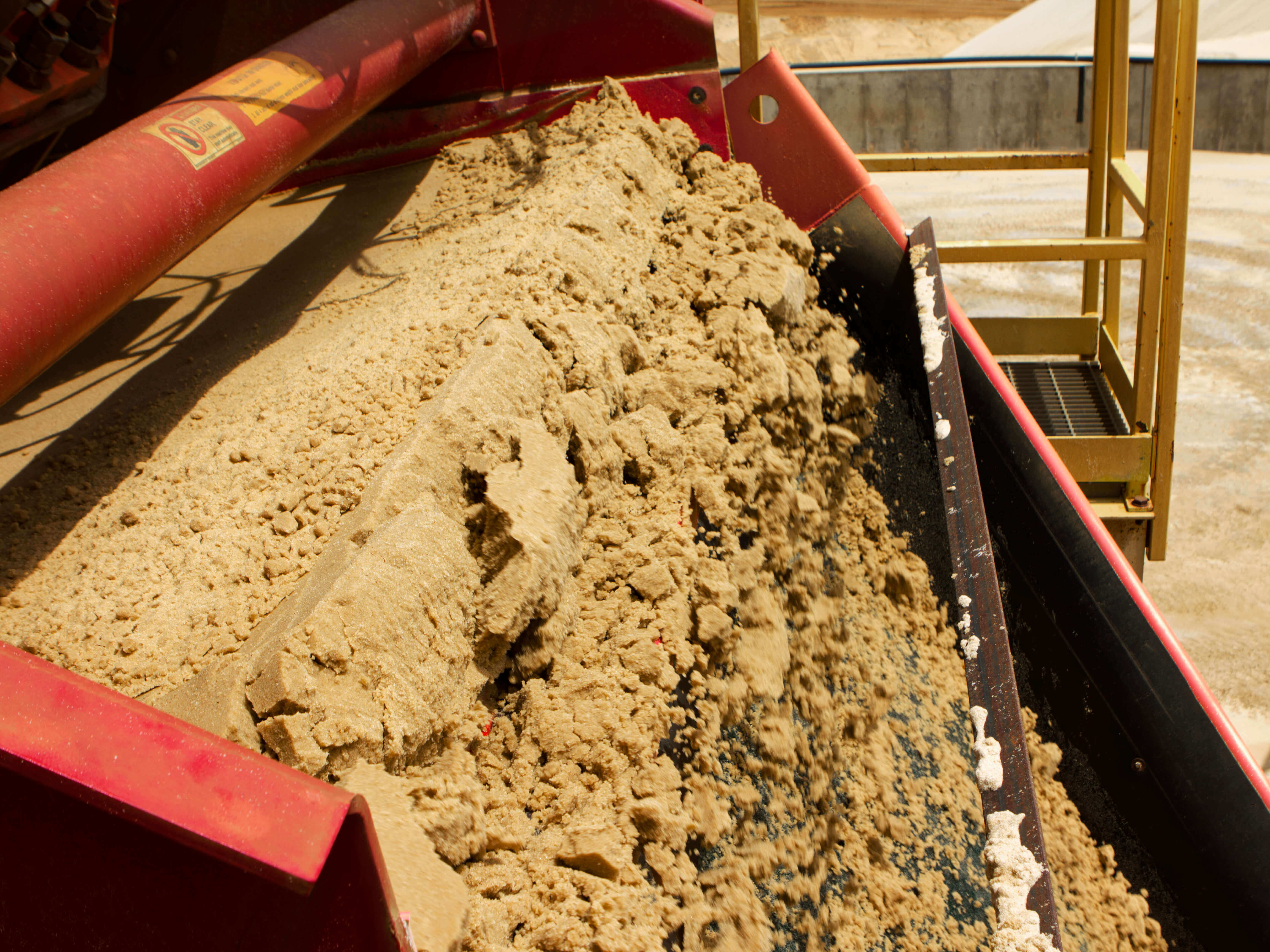
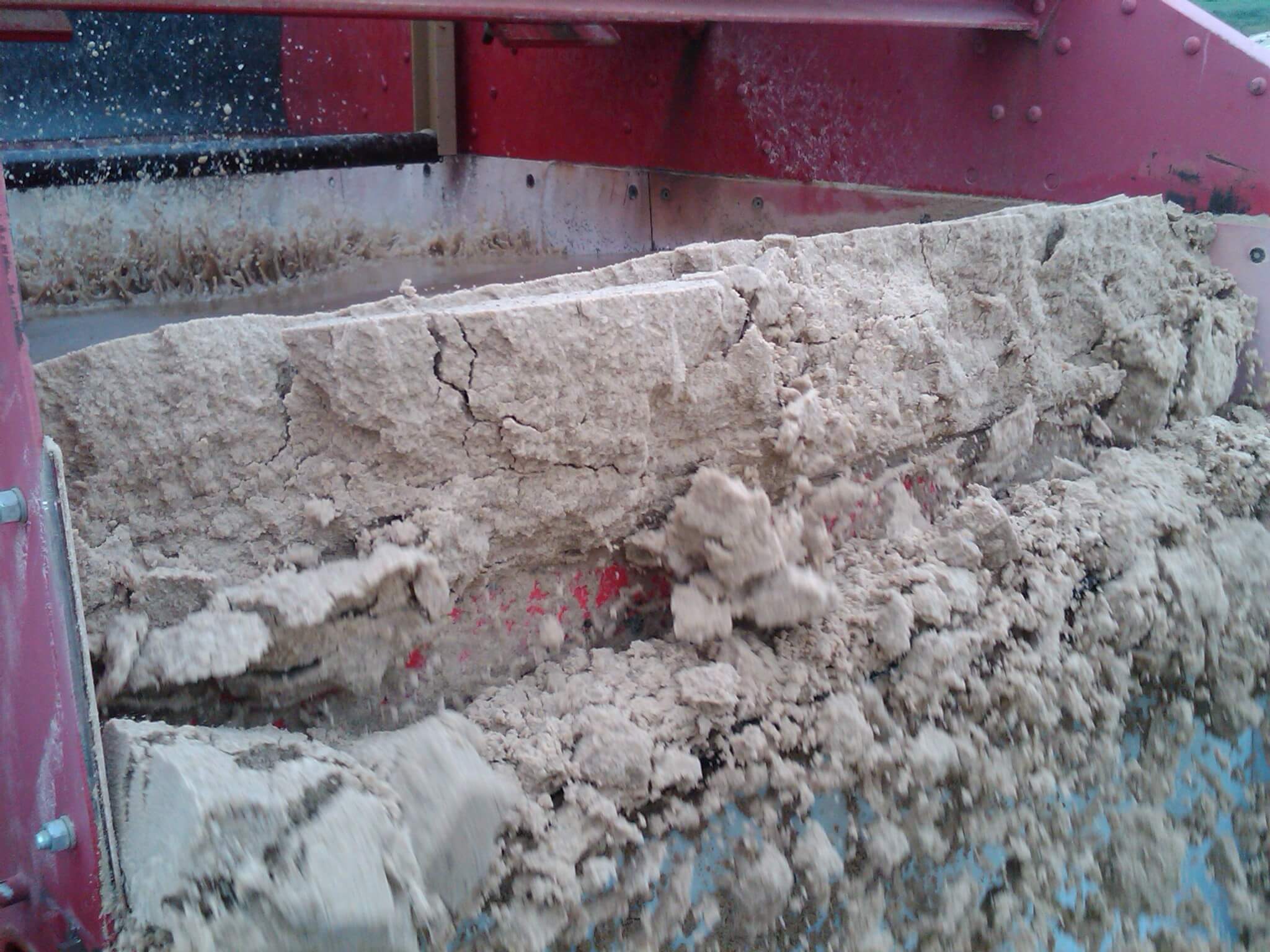
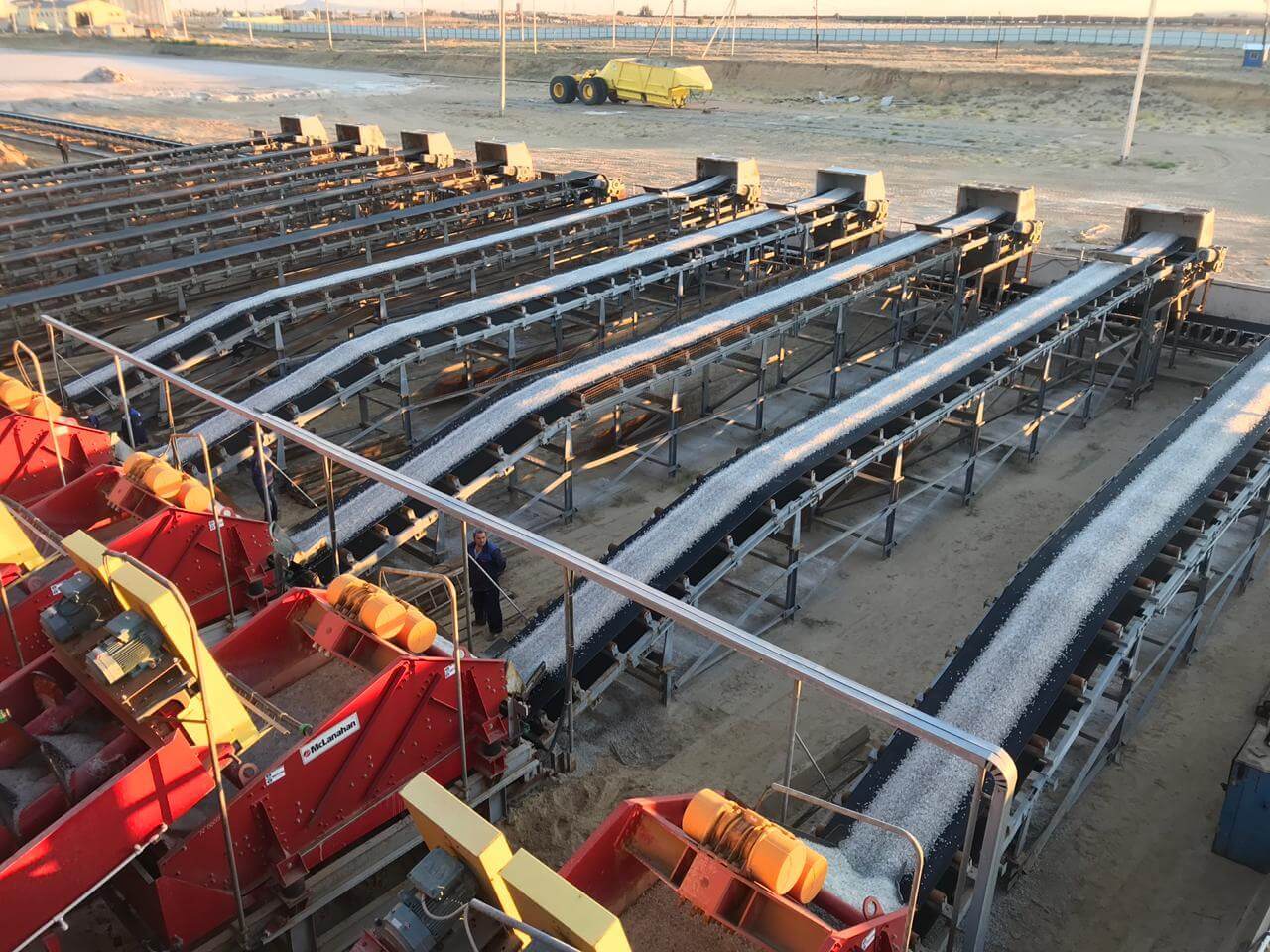
Dewatering Screens can be used to dewater -4 mesh (5 mm) particles of sand, coal, iron ore, salt, etc., as well as for limited efficiency fine sizing, washing and rinsing, desliming and organics screening.
Applications
Jump To:
Dewatering Screens have a wide variety of applications, including dewatering, desliming, degritting, rinsing, scrubbing, sizing and washing. They are designed to produce a consistent drip-free product and handle materials such as sand, gravel, crushed aggregates, frac sand, industrial sands, mineral sands, hard rock, precious metals ore, coal, iron ore, salt and other granular materials.
Surface moisture as low as 7% has been achieved with McLanahan Dewatering Screens; however, final moisture is dependent on surface area, surface morphology, and contact angle. Finer materials, such as those processed in fines recovery systems where the material is 100% passing 100 mesh (150 µm), will dewater to a drip-free consistency, which conveys and stacks, but may have a surface moisture content of more than 20%.
To dewater material effectively, slurry is fed onto a steep, downward inclined screen surface at the feed end of the Dewatering Screen to achieve rapid drainage. A pool of water begin forms in the valley as material builds up on the slightly upward inclined surface. Counter-rotating vibratory motors (or mechanical exciters on the largest of Dewatering Screens) create a linear motion at an angle to the screen surface that accelerates the solids upward and forward at 5 G. This, along with a generous stroke length, moves water through the countless openings between the particles to promote droplet formation.
The abrupt reversal of motion detaches water from the material, and the water droplets pass through the screen media. The solids are conveyed up the screen by this linear motion. The uphill slope of the screen, along with a discharge weir, creates a deep bed that acts as a filter medium, allowing retention of material much finer than the screen openings. A thick bed of material promotes fine retention while allowing the water to migrate through.
Where cleaner materials are required, cross dams and spray bars can be included to assist with the washing process, liberating fines that pass through the media. Using a dilute feed and additional spray water, these screens can effect some limited sizing. Dewatering Screens can be used for limited efficiency fine sizing at or above 10 mesh (2 mm) to create differential products, for stone washing and rinsing <2” (-50 mm) aggregates prior to loadout, desliming, and for trash/organics dewatering/screening.
McLanahan Dewatering Screens are based on the original Velco Dewatering Screens that were developed for use in mineral processing plants in the mid-1970s and are now the predominant dewatering device for granular materials. McLanahan enhanced this design using a crossbeam structure that makes the machine more robust and easier to maintain. McLanahan Dewatering Screens are designed for minimal maintenance. The bolt-together design allows for component replacement without cutting or welding. They require little operator training when installed and produce minimal noise.
Another improvement from the original design, McLanahan engineered its screen media for heavy-duty applications. This media features longitudinal stringers for full-length support. Tight tolerance, full-length urethane-to-urethane engagement virtually eliminates the entry of the process material at screen section interfaces, preventing troublesome wear points that can occur when using pin-and-sleeve and multi-point supported media.
McLanahan pioneered the use of longitudinal dividers to allow as many as three products to be dewatered on one screen. Many applications feature a two-stream process, but McLanahan Dewatering Screens allow up to one fine stream and two coarse streams to be kept separate or blended to create specialty products.
When compared with the typical Fine Material Screw Washer, the final product will generally be at least 10% drier with a McLanahan Dewatering Screen. Because of the wide range of equipment within McLanahan, the Dewatering Screen can be combined to complement other process equipment, such as Screw Washers, Hydrocyclones and Separators™. Certain types of washing processes (e.g. double wash) can benefit from a Screw Washer as a primary washing device supplemented by the Dewatering Screen for a drier product.
McLanahan's UltraDRY is a skid-mounted Dewatering Screen designed to fit under any brand of sand screw to improve final product dryness. It can also be installed on an inclined orientation with the use of spacer blocks to dewater underflow from a Hydrocyclone or Separator ™ to a drip-free consistency that is stackable, conveyable and ready for immediate sale. The compact, modular design makes it quick and easy to set up and move from site to site as needs change.
Some applications have experienced a moisture content as low as 7% with McLanahan Dewatering Screens, but final moisture content is dependent on both surface moisture and inherent moisture. When reporting moisture by weight (kg water/kg pulp), the specific gravity of the solids also plays a factor, with higher specific gravity materials showing lower moisture contents. If you remove all the water from the gaps between the particles, the only water left is that which is adsorbed as a thin film on the outside surface or as inherent moisture within the material itself (some brown coals can contain up to 20% inherent moisture). Therefore, the finer the materials being handled and the more irregular the surface, the higher the moisture content. Certain materials are also more hydrophobic or hydrophilic, which also affects the residual water. It is also important to understand that a Dewatering Screen’s action is critical to creating droplet formation on the underside of the bed of material. This combination of amplitude and frequency was studied by the University of Karlsruhe, which developed recommendations for this action.
In the early days of Dewatering Screens, urethane pin and sleeve design media was common. Since then, parallel developments occurred, rated capacities increased (doubling in some cases) and more robust media designs came about. Today, pin and sleeve style designs are perfectly adequate and appropriate for sizing screen applications; however, with the heavy loads and aggressive action on Dewatering Screens, few media manufacturers can match the mechanical integrity required for the application. McLanahan spent a long time researching and working on designs to match the need and the result is a longitudinal rail style system with urethane-to-urethane connections between the media and the stringers -- this type of interface doesn’t fail. The frequency of replacement of media in Dewatering Screens is such that no manufacturer or representative is going to lose much downstream revenue, but the end user always benefits from a better system.
Several factors need to be taken into consideration when designing a support structure for a Dewatering Screen, including forces, natural frequencies and multiple unit installations. McLanahan can provide design criteria and assistance; call our offices for support or contact us now. As a quick guide, Dewatering Screens should never be underestimated in their ability to shake a structure with their mass and the 900 rpm and 10 mm amplitude. Multiple Dewatering Screen installations can be a challenge with harmonics; occasionally a beat will be experienced. In some cases, vibration transference through the ground can be experienced in other structures. Good design practices include placing columns directly under the support points and substantial foundations to provide mass. Always allow 3” (75 mm) of clearance to other components in the direction of action (longitudinal to the screen) so no impact occurs when the vibratory motors or exciters go out of phase during shut down. Electric cables should always be supported/suspended from above directly to the junction box and never draped over vibrating components. McLanahan’s Dewatering Screen motors come with sealed junction boxes with long extended cables to connect into the electrical circuit.
McLanahan’s personnel pioneered the use of deck-dividers to allow two or even three products to be dewatered at one time. Producing a fine product on one side and a coarse product on the other with the facility to blend is part of the standard offering from McLanahan. Process engineers will assist with the application to ensure all factors are considered. Extensive out-of-balance loading (one or more of the products not being fed for long periods of time) can decrease the lifespan of the equipment.
The smallest aperture on a Dewatering Screen is typically 50 mesh (0.3 mm), so you will expect to see some of that size fraction and finer in the underflow of the screen. Not all of that fraction will pass through due to the very nature of caking style screens; fines are captured in the bed formed on top of the media. The usable fraction that does pass through the screen can be handled in several ways. The easiest is to recycle back to the device feeding the screen. In cases of greater flows, a dedicated scavenger circuit could be used.
McLanahan Dewatering Screens produce a consistent, drip-free product with as low as 7% moisture content.